Luận án Nghiên cứu ảnh hưởng của lớp phủ bề mặt đến độ bền mỏi của chi tiết máy dạng trục
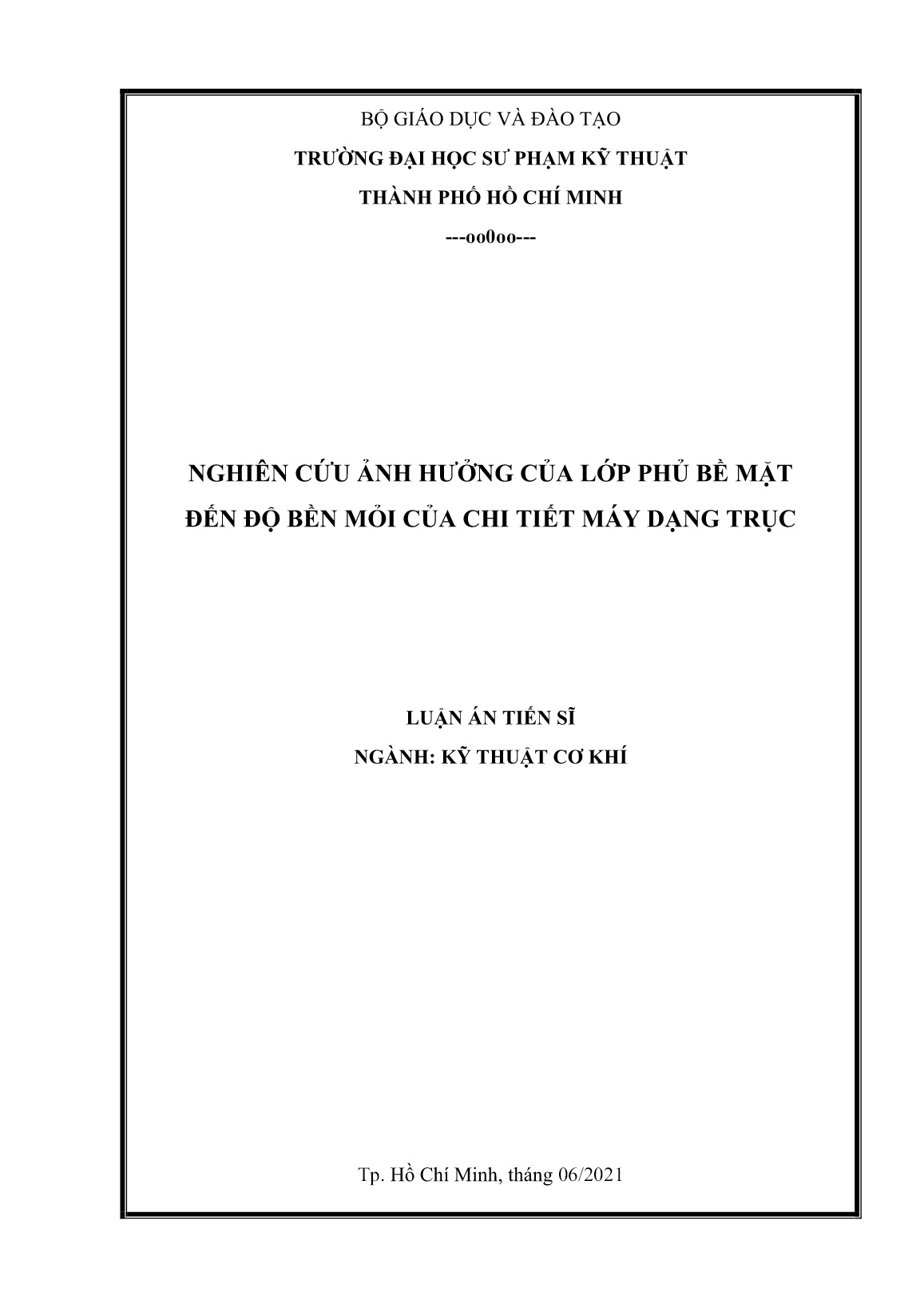
Trang 1
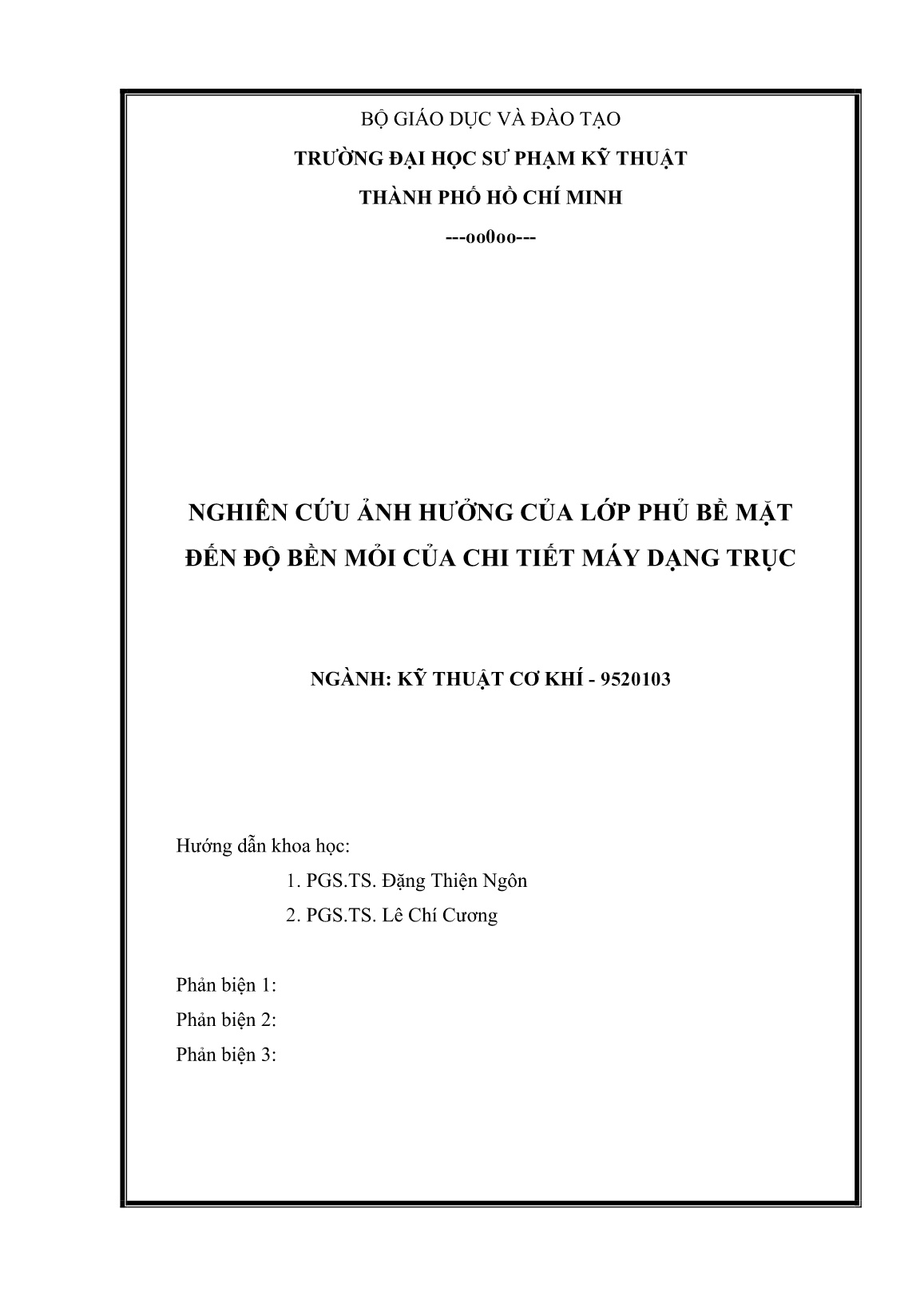
Trang 2

Trang 3
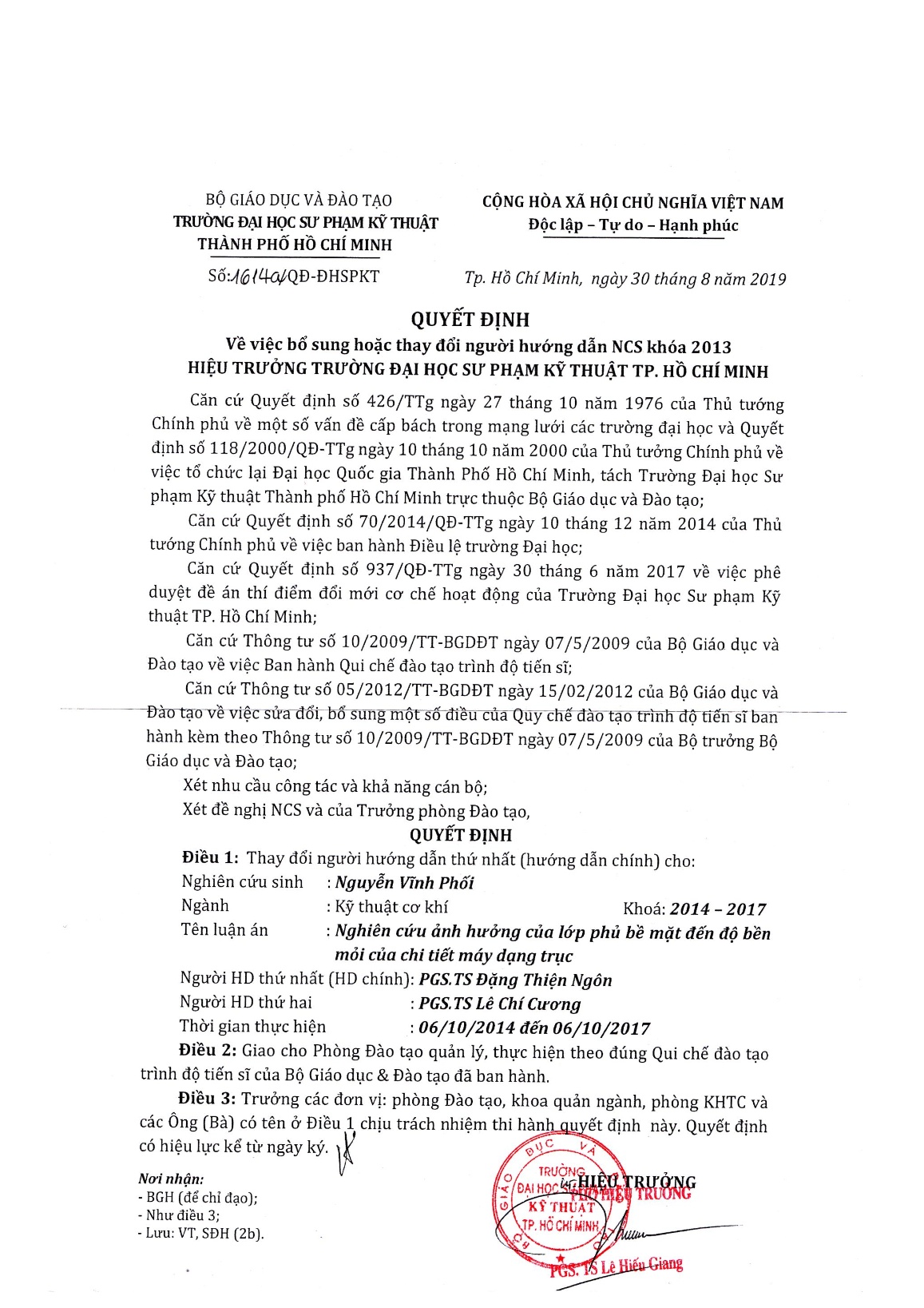
Trang 4
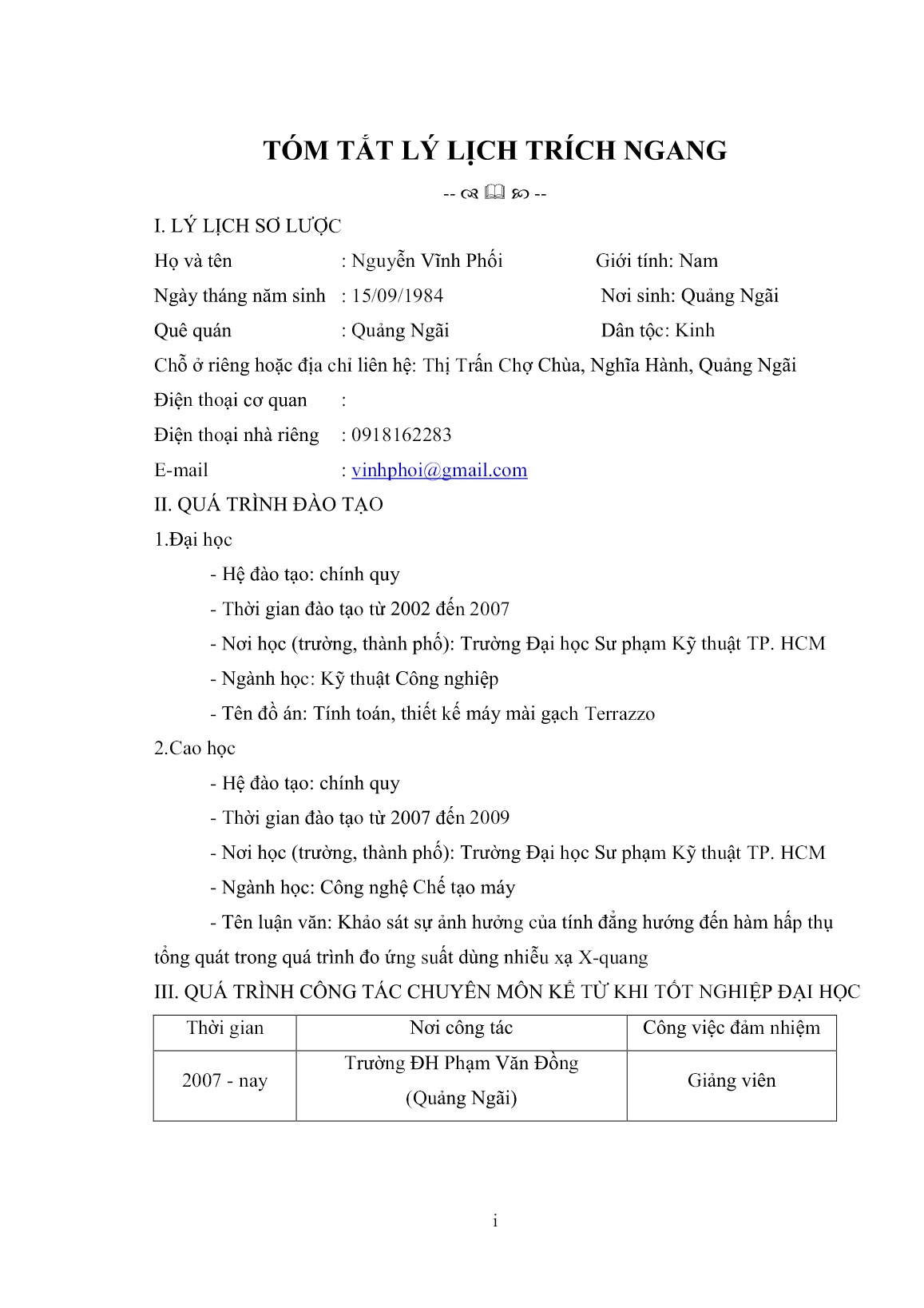
Trang 5
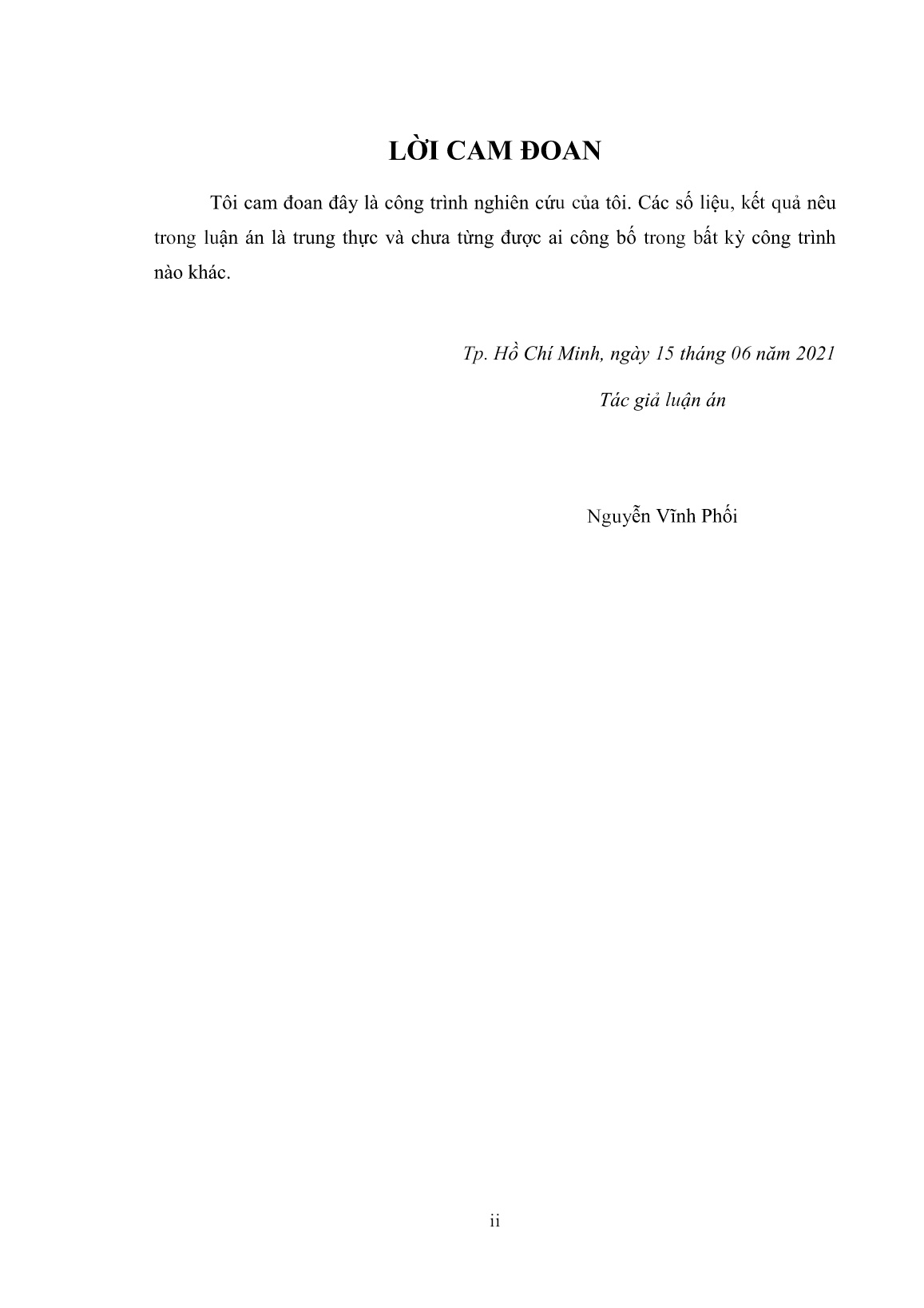
Trang 6
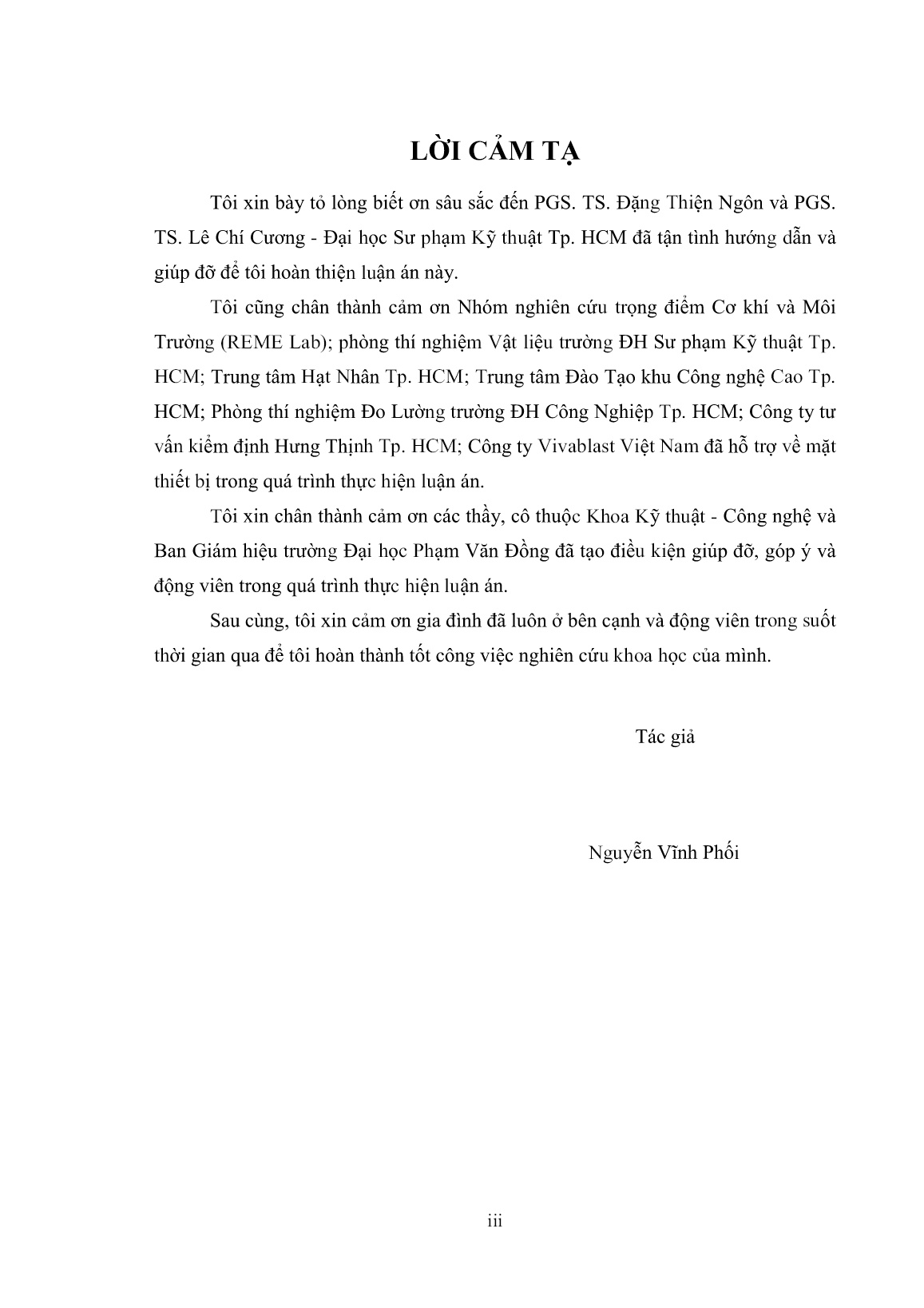
Trang 7
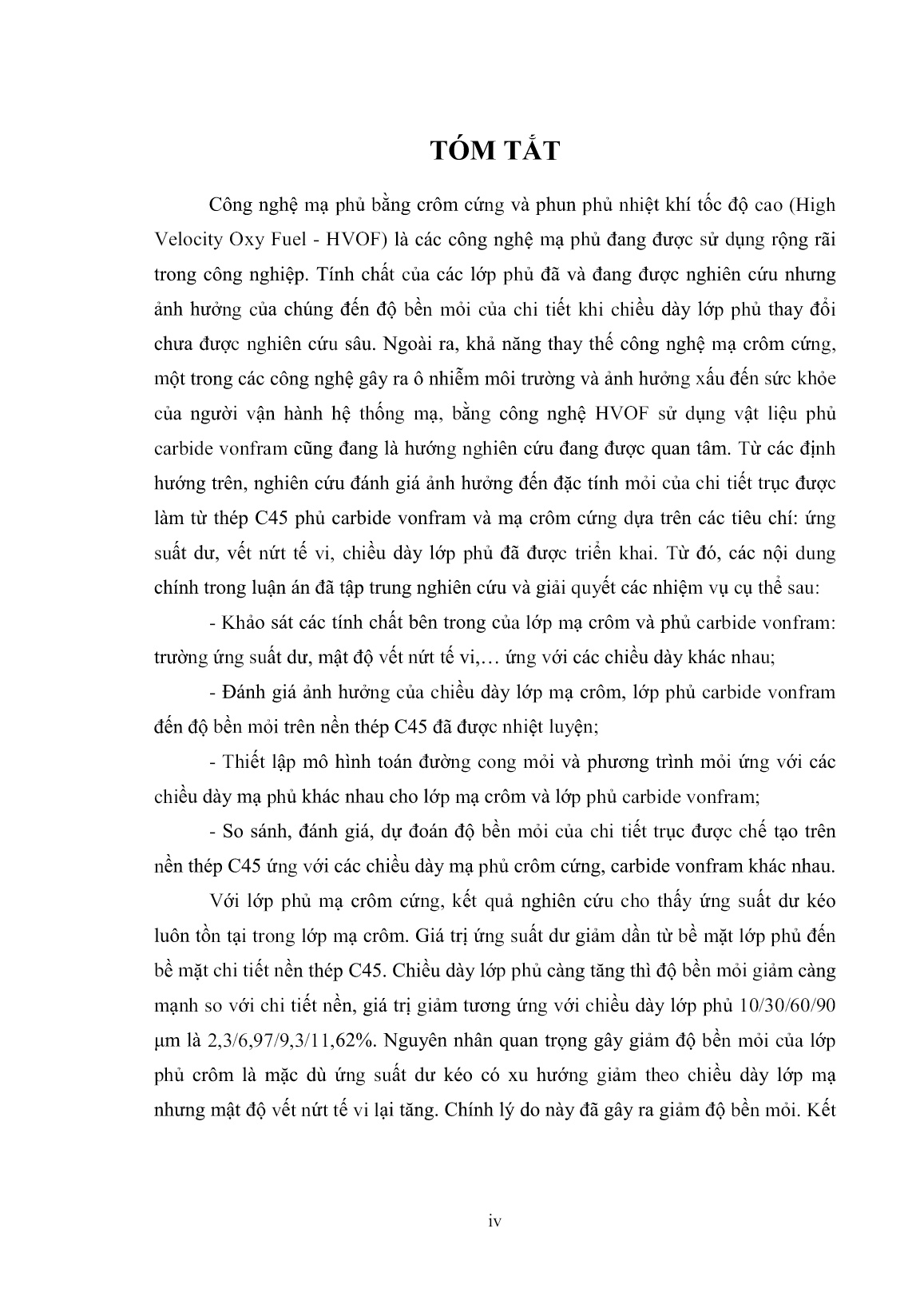
Trang 8
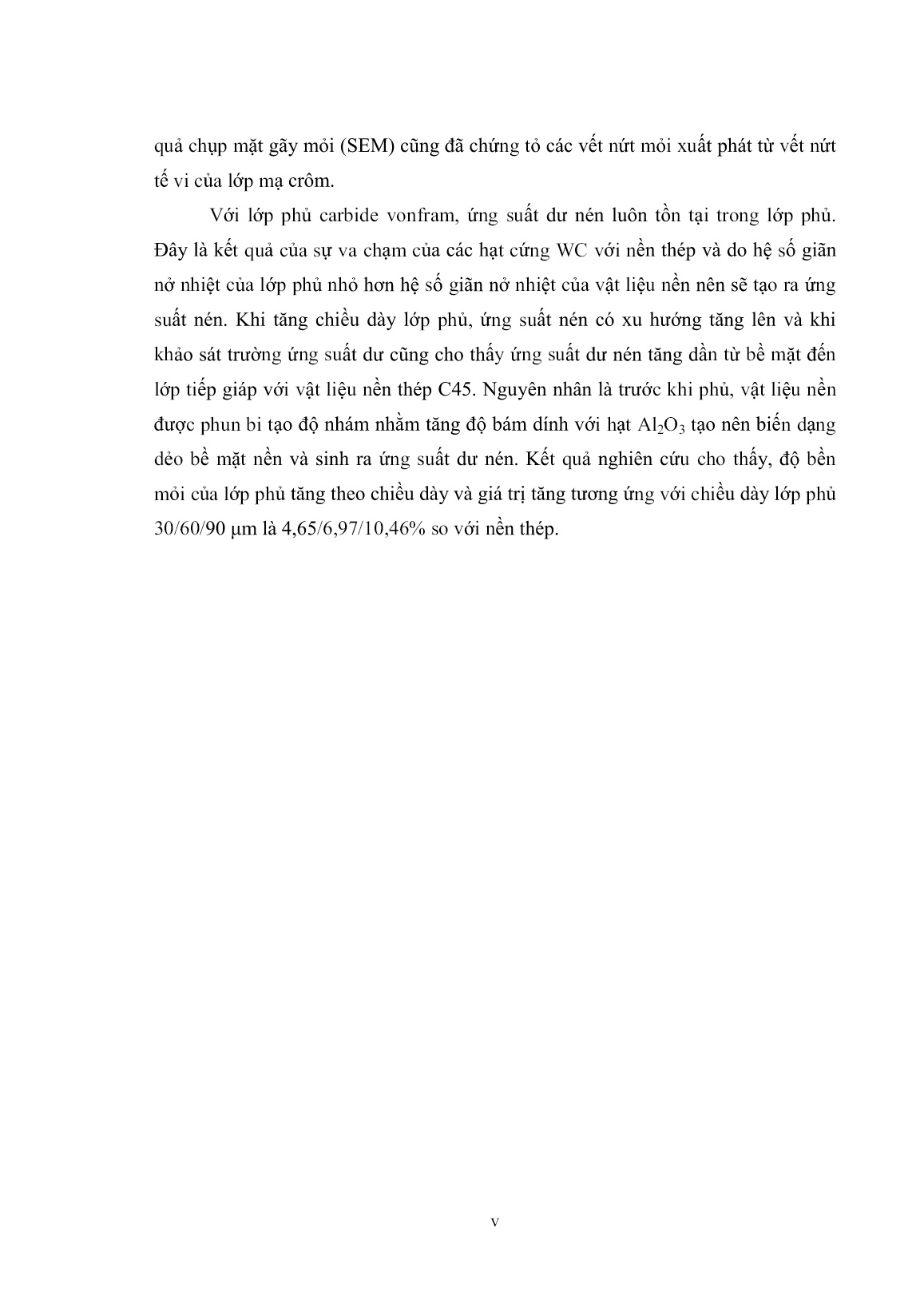
Trang 9
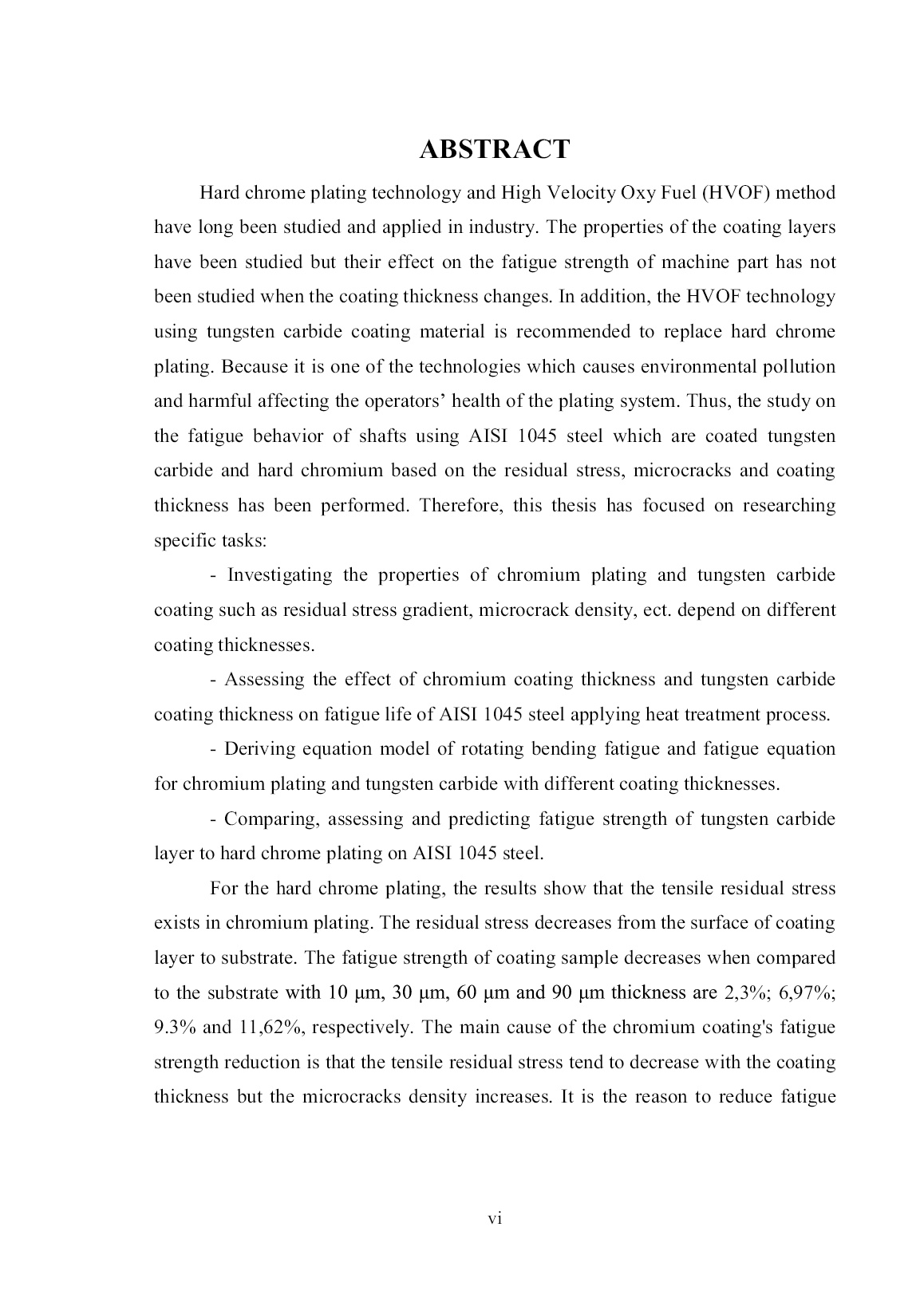
Trang 10
Tải về để xem bản đầy đủ
Bạn đang xem 10 trang mẫu của tài liệu "Luận án Nghiên cứu ảnh hưởng của lớp phủ bề mặt đến độ bền mỏi của chi tiết máy dạng trục", để tải tài liệu gốc về máy hãy click vào nút Download ở trên.
Tóm tắt nội dung tài liệu: Luận án Nghiên cứu ảnh hưởng của lớp phủ bề mặt đến độ bền mỏi của chi tiết máy dạng trục
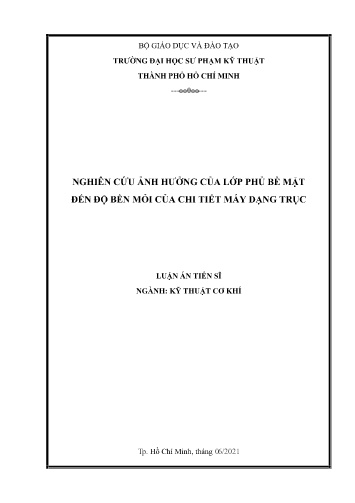
chảy của một lớp mỏng (°C); Ts : Nhiệt độ của vật liệu nền (°C). Hình 2.16. Ứng suất kéo do quá trình tôi b. Ứng suất do làm nguội Khi kết thúc quá trình lắng đọng hoặc trong quá trình phun bị gián đoạn sẽ sinh ra ứng suất như ở Hình 2.17. Hiện tượng này xảy ra chủ yếu do sự chênh lệch hệ số giãn nở nhiệt giữa kim loại nền và vật liệu lớp phủ. Nếu hệ số giãn nở nhiệt của lớp phủ lớn hơn hệ số giãn nở nhiệt của vật liệu nền (αc >αs) thì sẽ tạo ra ứng suất kéo bên trong lớp phủ [71, 72]. Điều này có thể làm giảm độ bám cũng như làm rạn nứt lớp phủ. Nếu các hệ số giãn nở cân bằng thì ứng suất sẽ không xảy ra. Còn nếu hệ số giãn nở nhiệt của lớp 57 phủ nhỏ hơn hệ số giãn nở nhiệt của vật liệu nền ( c< s) thì sẽ tạo ra ứng suất nén. Hình 2.17. Ứng suất nén trong quá trình phủ Ứng suất nén được tính theo công thức sau: SS CC SCRfC C tE tE TTE 21 )( (2.27) 2.5.2.3 Độ bám dính Sự bám dính của lớp phủ với vật liệu nền là một trong những yếu tố quan trọng được nhiều nhà khoa học nghiên cứu. Độ bám dính của lớp phủ bao gồm độ bền bám dính giữa lớp phủ với nền và giữa các phần tử bên trong lớp phủ. Trong đó, độ bám dính của lớp phủ với nền thường là yếu tố đựợc chú trọng bởi chúng thường khác nhau về vật liệu, trạng thái, tính chất vật lý, hóa học,... nên khó khăn hơn để tạo ra liên kết bền chặt. Các liên kết tạo thành lớp phủ chủ yếu là liên kết cơ học, chúng được quyết định bởi mức độ va đập của hạt phun đối với nền [73]. Nhiều nghiên cứu cho thấy nhiệt độ hạt phun và độ nhấp nhô (độ nhám) của bề mặt chi tiết phun là hai thông số tạo điều kiện để sự bám dính lớp phủ được tốt nhất. Khi động năng của hạt càng lớn, hạt phun bị nóng chảy cục bộ hoặc toàn phần khi va đập sẽ bị biến dạng mạnh hơn, tăng diện tích tiếp xúc và tăng bám dính cơ học cũng như lực hấp dẫn giữa các lớp nguyên tử hai kim loại. Đối với nhóm hạt phun không bị nóng chảy hoặc đã bị nguội, khi đến bề mặt chúng chỉ có sự bám dính hoàn toàn bằng lực cơ học. Tốc độ va đập càng cao, năng lượng chuyển thành nhiệt năng càng lớn, vật liệu phun dễ bị nóng chảy hoặc chuyển thành trạng thái dẻo, hạt dễ biến dạng và bám lên bề mặt chi tiết phun [74]. Đây chính là ưu điểm của phương pháp 58 phun HVOF bởi vận tốc hạt cao, điều này giải thích tại sao lớp phủ HVOF thường có độ bền bám dính lớn hơn các phương pháp phun thông dụng khác, kể cả trường hợp phun cùng vật liệu. Ngoài ra, theo nghiên cứu của tác giả D. Sen và các cộng sự [75] để đạt được độ bám dính tốt nhất giữa vật liệu phủ là WC-12Co và nền là thép cacbon trung bình thì độ nhám bề mặt chi tiết (sau phun hạt Al2O3) nền cần phải đạt 4 µm. 2.6 Nhiễu xạ tia X và ứng dụng đo ứng suất dư 2.6.1 Hiện tượng nhiễu xạ tia X Một số định nghĩa: - Phản xạ: tia tới bị phản xạ bởi một mặt phẳng; góc tới bằng góc phản xạ; năng lượng cũng như bước sóng không thay đổi. - Tán xạ: tia tới va chạm với một điểm vật chất nào đó; điểm vật chất này trở thành một nguồn bức xạ thứ cấp phát bức xạ (tia tán xạ) ra các hướng khác nhau. Tia tán và tia tới có năng lượng có thể bằng nhau (tán xạ đàn hồi) hoặc khác nhau (tán xạ không đàn hồi). - Giao thoa: là hiện tượng cộng hợp sóng. Có giao thoa tăng cường (các sóng tới cùng pha) và giao thoa triệt tiêu (các sóng tới ngược pha) - Nhiễu xạ: là sự giao thoa tăng cường của nhiều hơn một sóng tán xạ - Kết quả: thu được các đỉnh nhiễu xạ theo các phương mặt tinh thể xác định. Các đỉnh nhiễu xạ này có thể được ghi lại dưới dạng ảnh nhiễu trên phim hoặc được vẽ thành giản đồ nhiễu xạ. 2.6.2 Định luật Bragg và điều kiện nhiễu xạ Khi chiếu tia X có bước sóng (10-4 – 102 0 ) tương ứng với khoảng cách giữa các mặt phẳng nguyên tử vào vật rắn tinh thể sẽ xuất hiện các tia nhiễu xạ với cường độ và các phương khác nhau, các phương nhiễu xạ phụ thuộc vào bước sóng của bức xạ tới và bản chất của mẫu tinh thể. Định luật Bragg thiết lập mối quan hệ giữa bước sóng tia X và khoảng cách giữa các mặt nguyên tử (Hình 2.18). Các giả thuyết: Các mặt phẳng nguyên tử phản xạ các bức xạ tới phải độc lập, các tia tới phải tán xạ hoàn toàn. 59 Giả sử hai mặt phẳng nguyên tử song song A-A’ và B-B’ có cùng chỉ số Miller h,k,l và cách nhau bởi khoảng cách giữa hai mặt phẳng nguyên tử dhkl, chúng ta xem mặt tinh thể của tâm tán xạ nguyên tử là các mặt tinh thể và phản xạ giống như gương đối với tia X. Hình 2.18. Định luật Bragg [76] Giả sử hai tia 1 và 2 đơn sắc, song song và cùng pha với bước sóng λ chiếu vào hai mặt phẳng dưới góc θ. Hai tia này bị tán xạ bởi 2 nguyên tử P và Q và cho hai tia phản xạ 1’ và 2’ cũng tạo góc so với mặt phẳng ngang θ. Sự giao thoa của hai tia tán xạ xảy ra nếu thỏa mãn điều kiện sau: Hiệu quảng đường 1-Q-1’ và 2-P-2’, SQ + QT bằng số nguyên lần bước sóng. Tức là nλ = SQ + QT nλ = 2dhklsinθ (2.28) Trong đó n = 1, 2, 3... được gọi là bậc phản xạ. Phương trình (2.28) chính là định luật Bragg biểu thị mối quan hệ đơn giản giữa góc của tia nhiễu xạ với bước sóng tia X tới và khoảng cách giữa các mặt phẳng nguyên tử dhkl. Nếu định luật Bragg không được thoả mãn thì sự giao thoa thực chất sẽ không có vì cường độ nhiễu xạ thu được là rất nhỏ. Trong hầu hết các trường hợp, bậc phản xạ thứ nhất được sử dụng, n = 1, do 60 đó định luật Bragg được viết như sau : n = 2dhkl sin (2.29) Khi n > 1, các phản xạ được gọi là phản xạ bậc cao. Ta có thể viết phương trình (2.29) như sau : = 2(dhkl /n)sin (2.30) Trong đó dhkl /n là khoảng cách giữa các mặt ( nh nk nl ). Vì thế, có thể xem phản xạ bậc cao là phản xạ bậc nhất từ các mặt đặt tại khoảng cách bằng 1/n khoảng cách d. Bằng cách đặt d’ = d/n và thay vào phương trình (2.30) ta có thể viết định luật Bragg theo cách thông thường là : = 2d’ sin (2.31) hoặc = 2d sin (2.32) Khi chùm tia X có bước sóng đụng vào một tinh thể, chùm tia bị phản xạ không chỉ từ các nguyên tử bề mặt mà còn từ các nguyên tử ở phía dưới lớp bề mặt với một chiều sâu đáng kể. 2.6.3 Các yếu tố ảnh hưởng đến cường độ nhiễu xạ LPA Việc xác định chính xác vị trí đỉnh nhiễu xạ là điều kiện tiên quyết để xác định ứng suất dư, vì khi thực hiện nhiễu xạ ứng với một mặt phẳng nguyên tử hkl (mặt phản xạ) và một góc nhiễu xạ 2θ sẽ cho một đường nhiễu xạ nhất định và đỉnh nhiễu xạ là vị trí có cường độ I cực đại (Hình 2.19). Bằng cách chúng ta thực hiện nhiễu xạ cho vật mẫu (là vật nhiễu xạ ở trạng thái tự nhiên không tồn tại ứng suất) với thiết bị có cùng công suất, bước sóng chùm tia tới, mặt phẳng nhiễu xạ có chỉ số Miller h,k,l, và cùng góc nhiễu xạ 2θ sẽ thu được đường nhiễu xạ có đỉnh nhiễu xạ. Cùng với điều kiện như trên chúng ta thực hiện nhiễu xạ trên mẫu cần đo ứng suất và cũng thu được đường nhiễu xạ tương tự tuy nhiên đỉnh nhiễu xạ sẽ bị lệch đi ε = (d – d0)/d0 với d là khoảng cách của các mặt nhiễu xạ hkl của vật cần đo, d0 là khoảng cách của mặt nhiễu xạ của mẫu. Tuy nhiên cường độ nhiễu xạ còn phụ thuộc vào các yếu tố sau: hệ số hấp thụ (the absorption correction factor A), hệ số phân cực (the polarization factor P(2θ)) và hệ số Lorentz (the Lorentz factor L(2θ)). 61 Hình 2.19. Đỉnh nhiễu xạ có chỉ số Miller h,k,l, và góc nhiễu xạ 2θ [76] 2.6.4 Chiều sâu xuyên qua của tia X Độ suy giảm cường độ làm giới hạn chiều sâu xuyên qua của tia X. Chiều sâu xuyên qua của tia X phụ thuộc vào hệ số suy giảm của vật liệu và kích cỡ chùm tia trên mặt mẫu. Độ suy giảm của tia tới tương ứng với bề dày vật liệu mà nó xuyên qua. Lấy vi phân cường độ nhiễu xạ của một lớp mỏng cách bề mặt một khoảng “x” ta có: 0 1 1exp sin( ) sin( ) sin( ) D I ab dI x dx (2.33) Tổng cường độ nhiễu xạ giữa lớp này và lớp bề mặt là: 0 1 1 1 exp sin( ) sin( ) x D x o x D x dI G x dI (2.34) Khi 0 ta có: 2 1 exp( ) sin x x G (2.35) Công thức này cho thấy rằng ảnh hưởng của chiều sâu xuyên qua có thể được định nghĩa là bề dày mà nó góp phần cho 99% cường độ nhiễu xạ. 62 2.6.5 Tính ứng suất Trong phương pháp dùng nhiễu xạ để đo ứng suất, ứng suất không được đo một cách trực tiếp mà nó được đo thông qua giá trị biến dạng. 2.6.5.1 Xác định biến dạng Cho hệ tọa độ như (Hình 2.20), trong đó Si là hệ tọa độ gắn liền với mặt mẫu, trong đó S1,S2 nằm trên mặt mẫu, Li là hệ tọa độ thí nghiệm (hệ đo), có L3 vuông góc với họ mặt phẳng nguyên tử (hkl). L2 nằm trong mặt phẳng tạo bởi S1,S2, và làm với S2 một góc υ. Khi tính được khoảng cách ,d giữa các mặt phẳng (hkl) từ vị trí đỉnh nhiễu xạ, giá trị biến dạng dọc trục L3 là: , 0' 33 , 0 ( ) d d d (2.36) Trong đó: d0 là khoảng cách giữa các mặt mạng khi chưa có ứng suất. 1 S 2 S 3 S 1 L 3L ' 2 2 L S Maåu thöû ' 1S S Hình 2.20. Hệ tọa độ thí nghiệm và hệ tọa độ mẫu Dùng hệ thống ten xơ chuyển đổi tọa độ, phương trình (2.36) có thể viết: ' 33 3 3( ) k l kla a (2.37) Trong đó: 3 3,k la a : côsin chỉ phương của L3,Sk, và L3,Si 63 Với: cos cos sin cos sin sin cos 0 cos sin sin sin cos ika (2.38) Đây là ma trận chuyển đổi giữa hai hệ thống này Thay 3 3,k la a vào (2.37) ta được: 0' 2 2 2 2 2 11 12 22 0 2 33 13 23 ( ) cos sin sin 2 sin sin sin cos cos sin 2 sin sin 2 d d d (2.39) Đây là hàm căn bản của phương pháp nhiễu xạ dùng để xác định biến dạng. 2.6.5.2 Xác định mối liên hệ ứng suất – biến dạng Từ giá trị biến dạng đã xác định được, áp dụng định luật Hooke ta tính được ứng suất qua công thức sau [76]: ij ijkl klC (2.40) Trong đó: ijklC là ten xơ độ cứng đàn hồi hạng tư, đã được chuyển đến hệ tọa độ Si. Ứng suất trong hệ tọa độ nào cũng có thể được xác định bằng cách dùng luật chuyển đổi ten xơ hạng hai: ' mn mi nj ija a (2.41) Trong đó: mi nja a là côsin chỉ phương Ta nghịch đảo công thức (2.40), và được: ij ijkl klS (2.42) Trong đó: ijklS là ten xơ kết hợp đơn tinh thể hạng tư. Thay công thức (2.42) vào (2.39) ta sẽ tính được mối liên hệ giữa ứng suất và giá trị biến dạng. Vì mẫu đang xét là vật liệu đẳng hướng đàn hồi đồng nhất. Cho nên ta phải tính kết hợp đàn hồi thông qua các trục tinh thể với các trục được chuyển đổi ten xơ lần nữa dựa theo phương pháp Euler (Hình 2.21). 64 Hình 2.21. Trục tinh thể (Ci) và hướng của nó đối với hệ tọa độ mẫu (Si) cùng hệ trục đo(Li) ijkl im in ko lp mnopS a a a a S (2.43) Trong đó: - mnopS là ten xơ kết hợp được tính trong các trục tinh thể. - ko lpa a là côsin chỉ phương. Thay (2.43) vào (2.42) ta được: ij im in ko lp mnop kla a a a S (2.44) Từ (2.44) suy ra: 11 1 1 11 12, 22,, ... m n ko lp mnop kla a a a S (2.45) Tương tự, 12, 22, Thay công thức (2.45) vào (2.39) ta được công thức tính ứng suất theo định luật Hooke tổng quát: 2 1 11 22 33 1 ( ) 2 ij ij ijS S (2.46) Trong đó: - ij là delta Kronecker, bằng 1 nếu i=j; và bằng 0 nếu i j . - ij là ten xơ ứng suất. ( ,i j lấy từ 1 đến 3 ). C3 C2 C1 S2 S3 L3 S1 65 - ij là giá trị biến dạng theo phương ,i j - 1S E vaø 2 1 1 2 S E là hằng số đàn hồi tia X (XEC) của vật liệu đẳng hướng. - là hệ số Poison; và E là mô đun đàn hồi của vật liệu. - Nếu là vật liệu gần đẳng hướng thì nó phụ thuộc vào họ mặt phẳng nhiễu xạ hkl và pha vật liệu. Khi đó: 1 1 hklS S ; và 2 2 1 1 2 2 hklS S . Nếu thay các giá trị của i và j tương ứng là 1,2,3 vào công thức (2.46), ta có: 2 33 2 2212 2 11233 ' , sin)sin2sincos( 2 1 SL )( 2 1 3322111332 SS (2.47) 2sin)sincos( 2 1 23132 S Với 33 L là biến dạng theo phương đo L3 tương ứng với biến dạng theo phương , . Đây là công thức căn bản, là nền tảng tổng quát nhất của phương pháp nhiễu xạ dùng để xác định biến dạng. Là phương trình cơ bản liên hệ giữa ten xơ ứng suất và biến dạng áp dụng để tính toán đối với vật liệu đẳng hướng. 2.6.5.3 Nguyên lý đo ứng suất dùng nhiễu xạ tia X Ứng suất dư được xác định từ vị trí đỉnh của hình nhiễu xạ, khi xuất hiện ứng suất trong lớp bề mặt thì khoảng cách dhkl giữa các mặt nguyên tử sẽ thay đổi. Từ việc tính toán vị trí đỉnh nhiễu xạ ta có thể tính toán ứng suất thông qua biến dạng. Từ định luật Hooke biến dạng đàn hồi đẳng hướng qua biến đổi có thể xác định thông qua công thức sau: 2 33 2 2212 2 1133 ' , sin)sin2sincos( 1 E L 66 )( 1 33221133 EE (2.48) 2sin)sincos( 1 2313 E Từ công thức (2.48) ta có: )(sin 1 2211 2 0 0' , EEd dd (2.49) Trong đó 2 2 11 12 22cos sin 2 sin là ứng suất thành phần trong hệ mẫu Si ; Phương trình (2.49) có thể viết lại: 20 0 11 22 0 1 sin v v d d d d E E (2.50) Đây là phương trình thể hiện mối quan hệ dᴪ- sin 2ψ (Hình 2.22) có hệ số góc m là: 0 1 v m d E (2.51) Hình 2.22. Đồ thị d-Sin2ψ Từ phương trình trên ứng suất dư có thể xác định thông qua hệ số góc m là: 0 ( ) 1 m E d v (2.52) 67 Trong đó d0 là khoảng cách mặt tinh thể ở trạng thái không ứng suất, vì mẫu là vật liệu đẳng hướng nên d0 được tính như điểm không phụ thuộc vào ứng suất trên phương trình d-sin2ψ sau đây: 1 *2Sin (2.53) 68 Chƣơng 3 VẬT LIỆU - THIẾT BỊ VÀ PHƢƠNG PHÁP THÍ NGHIỆM 3.1 Vật liệu thí nghiệm 3.1.1 Vật liệu nền Thép C45 thuộc nhóm thép cacbon có hàm lượng cacbon từ 0,43 - 0,50% đảm bảo được các chỉ tiêu cơ tính tổng hợp như: độ bền, độ dẻo, độ dai, tính chịu lực, chịu uốn, chịu xoắn tốt. Với các tính chất này, thép C45 được sử dụng rộng rãi trong lĩnh vực cơ khí để chế tạo các chi tiết máy chịu mòn, chịu tải trọng tĩnh và va đập tương đối cao như trục, bánh răng,... Ngoài ra, trong quá trình chế tạo cơ khí, các chi tiết chế tạo từ thép C45 cũng có thể được xử lý nhiệt để đạt cơ tính tổng hợp cao nhất. Từ các cơ sở trên và thực tiễn chế tạo cơ khí tại Việt Nam, vật liệu thép (vật liệu nền) được lựa chọn cho việc chế tạo chi tiết mẫu để tiến hành các thí nghiệm để xác định độ bền mỏi là thép C45. Nguồn thép C45 sử dụng trong nghiên cứu được sản xuất tại công ty Feng Hsin Iron & Steel Co. Ltd (Đài Loan) theo tiêu chuẩn Nhật Bản. Để xác định các thành phần hoá học của nguồn thép C45 này, các mẫu kiểm tra thành phần hoá học đã được chế tạo (Hình 3.1) và phân tích bằng quang phổ tại phòng thí nghiệm Chiếu xạ (Sở Khoa học và Công nghệ Đồng Nai). Kết quả phân tích được trình bày ở Bảng 3.1. Hình 3.1. Mẫu kiểm tra thành phần vật liệu 69 Bảng 3.1. Thành phần các nguyên tố của mẫu thép C45 Nguyên tố C Si Mn P S Ni Cr Cu Thành phần (%) 0,46 0,21 0,64 0,021 0,007 0,04 0,09 0,16 Kết quả cho thấy mẫu thép C45 sử dụng có các thành phần hóa học nằm trong phạm vi thành phần hóa học của mác thép C45 [77]. 3.1.2 Vật liệu crôm cứng Crôm là nguyên tố có ký hiệu là Cr, số nguyên tử 24, loại điện giải (mạ điện) có màu trắng bạc, ánh xanh. Tùy theo điều kiện điện phân khi mạ điện, crôm có độ cứng rất cao (65-70 HRC). Ngoài độ cứng cao, crôm còn có các đặc điểm nổi bậc khác như là hệ số ma sát thấp (f = 0,12) nên rất bền mài mòn, khó thấm ướt, bám dính rất tốt với nhiều kim loại nền. Vì vậy, lớp mạ crôm được ứng dụng vào rất nhiều lĩnh vực để làm tăng độ cứng, tăng độ bền mài mòn, độ bền hóa học, phục hồi các chi tiết máy bị mài mòn... Tuy nhiên, lớp mạ crôm cũng có những nhược điểm là độ giòn cao, ứng suất dư lớn nên dễ bị rạn nứt [64, 78]. 3.1.3 Vật liệu carbide vonfram Đây là một loại bột phun phủ được sử dụng phổ biến trên thế giới với nhiều hãng sản xuất như Praxainr (Mỹ), Orelikon Metco (Thụy Sĩ), MEC (Ấn Độ). Tuỳ thuộc vào mục đích sử dụng như chế tạo mới hay phục hồi bề mặt chi tiết máy mà có thể sử dụng các phương pháp phun phủ và chọn loại bột cho thích hợp. Từ kết quả của các công trình đã nghiên cứu và tài liệu của hãng Orelikon Metco [59] cho thấy chất phủ bột carbide WC-10Co-4Cr (Woka 3652) có cơ tính rất tốt và được sử dụng rộng rãi nhờ pha carbide vonfram WC có độ cứng rất cao và chất kết dính coban giúp giảm sự mài mòn và chống ăn mòn rất tốt. So với vật liệu phủ WC-Co thì WC-10Co-4Cr có khả năng chống ăn mòn cao hơn vì có thành phần crôm nên là vật liệu đang được sử dụng để thay thế mạ crôm cứng. Trong thực tế, loại bột này rất phù hợp để áp dụng phun nhiệt cho chế tạo mới hay phục hồi các chi tiết dạng trục chịu mài mòn. Đã có nhiều công trình lựa chọn WC-10Co-4Cr cho phun phủ nhiệt để nghiên cứu nâng cao cơ tính của chi tiết, trong đó có độ bền mỏi [40-44, 46-48]. Từ các đặc điểm phân tích trên, bột carbide WC-10Co-4Cr đã được lựa 70 chọn làm chất phun phủ nhiệt để nghiên cứu đánh giá độ bền mỏi của chi tiết được phun phủ. Hình 3.2 giới thiệu tổ chức hạt của loại bột carbide WC-10Co-4Cr. Hình 3.2. Vật liệu WC-10Co-4Cr của hãng Orelikon Metco. Ltd. (Thụy sĩ) Bảng 3.2. Các thành phần nguyên tố của carbide vonfram Nguyên tố W Co Cr C (total) Fe (max) Thành phần (%) Balance 8,5-11,5 3,4-4,6 4,8-5,6 0,2 3.2 Thiết bị phục vụ thực nghiệm 3.2.1 Lò nung nhiệt Xử lý thớ, nhiệt luyện tôi và ram cho các chi tiết mẫu được thực hiện trên lò nung Thermal Electric Furnace (Nhật) tại phân xưởng cơ khí Công ty Đăng Tấn (Thủ Dầu Một, Bình Dương). Thông số cơ bản của lò nung: - Nhiệt độ buồng nung: 600 - 10900C - Kích thước buồng nung: Ø 600 x H 300 mm - Công suất: 19 kW, nguồn điện 3 pha 220 V 71 Hình 3.3. Lò nung Thermal Electric Furnace (Nhật) Để các chi tiết mẫu trong quá trình xử lý thớ, tôi không bị dính vào nhau do ảnh hưởng của nhiệt độ, một đồ gá hỗ trợ gá đặt các chi tiết mẫu đã được thiết kế và chế tạo (Hình 3.4). a) Đồ gá xử lý thớ b) Đồ gá tôi Hình 3.4. Đồ gá chi tiết mẫu khi xử lý nhiệt Buồng nhiệt Bộ phận điều khiển Thùng chứa dung dịch làm nguội 72 a) Quá trình xử lý thớ b) Quá trình tôi Hình 3.5. Quá trình nhiệt luyện Sau quá trình tôi thể hiện trên Hình 3.5b, quá trình ram được thực hiện trên thiết bị S-now Industrial Furnace (Trung Quốc) tại phân xưởng cơ khí Công ty Đăng Tấn. Các thông số cơ bản của thiết bị: - Nguồn điện: 3 pha 380 V - Kích thước buồng nung: 500x350x350 mm - Nhiệt độ lớn nhất: 6500C Hình 3.6. Lò ram S-now Industrial Furnace (Trung Quốc) 73 3.2.2 Máy quang phổ xác định thành phần vật liệu Thành phần của vật liệu được sử dụng để chế tạo chi tiết mẫu được phân tích, đánh giá bằng máy quang phổ GNR-F20 (Italia) tại Sở Khoa học và Công nghệ tỉnh Đồng Nai. Các thông số của máy quang phổ GNR-F20 (Hình 3.7): - Nguồn điện: 220 V - Công suất phóng (sparking): 3 kW - Công suất hồ quang (arc): 3 kW Hình 3.7. Máy quang phổ GNR-F20 (Italia) 3.2.3 Máy đo độ nhám Độ nhám của chi tiết mẫu được đo trên máy Mitutoyo SJ-301 (Nhật). Công việc đo kiểm được thực hiện tại phòng thí nghiệm đo lường trường đại học Công Nghiệp Tp. HCM. Máy có các thông số cơ bản như sau: - Màn hình: 14,5 cm - Phương pháp đo: cảm ứng - Bán kính trượt: 40 mm - Lực đo: 0,75 mN - Cổng giao tiếp: RS-232C - Tiêu chuẩn chịu mài mòn: EN ISO, VDA, ANSI, JIS - Bộ lọc kỹ thuật số: 2RC -75% 74 Hình 3.8. Máy đo độ nhám Mitutoyo SJ-301 3.2.4 Máy đo độ cứng HRC Độ cứng của chi tiết mẫu được đo trên máy Mitutoyo ATK-600 (Nhật) thuộc phòng thí nghiệm đo lường Trường Đại học Công Nghiệp Tp. HCM. Máy đo độ cứng Mitutoyo ATK-600 (Hình 3.9) có các thông số cơ bản như sau: - Mũi đâm kim cương và mũi đâm bi thép: 1/16" - Tải thử: 588,4 N / 980,7N / 1471N - Bàn gá: mặt phẳng hình tròn (ø64mm) - Chiều cao mẫu lớn nhất: 140 mm - Chiều sâu mẫu lớn nhất: 122 mm (từ tâm mũi đâm) Hình 3.9. Đo độ cứng trên máy Mitutoyo ATK-600 75 3.2.5 Máy đo độ cứng HV (Vicker) Độ cứng của lớp phủ được đo trên máy Meatall-HV5 (Trung Quốc) thuộc Trung tâm Kỹ thuật Tiêu chuẩn Đo lường Chấ
File đính kèm:
luan_an_nghien_cuu_anh_huong_cua_lop_phu_be_mat_den_do_ben_m.pdf
Trang thong tin LA tieng Viet_NVPhoi 31_08_2021.docx
Trang thong tin LA tieng Anh_NVPhoi 31_08_2021.docx
Tom tat luan an tieng Viet_NVPhoi 31_08_2021.pdf
Tom tat luan an tieng Anh_NVPhoi 31_08_2021.pdf