Luận án Nghiên cứu ảnh hưởng của một số yếu tố đến tuổi thọ của răng cắt trên tang máy khấu dùng trong khai thác than hầm lò vùng Quảng Ninh
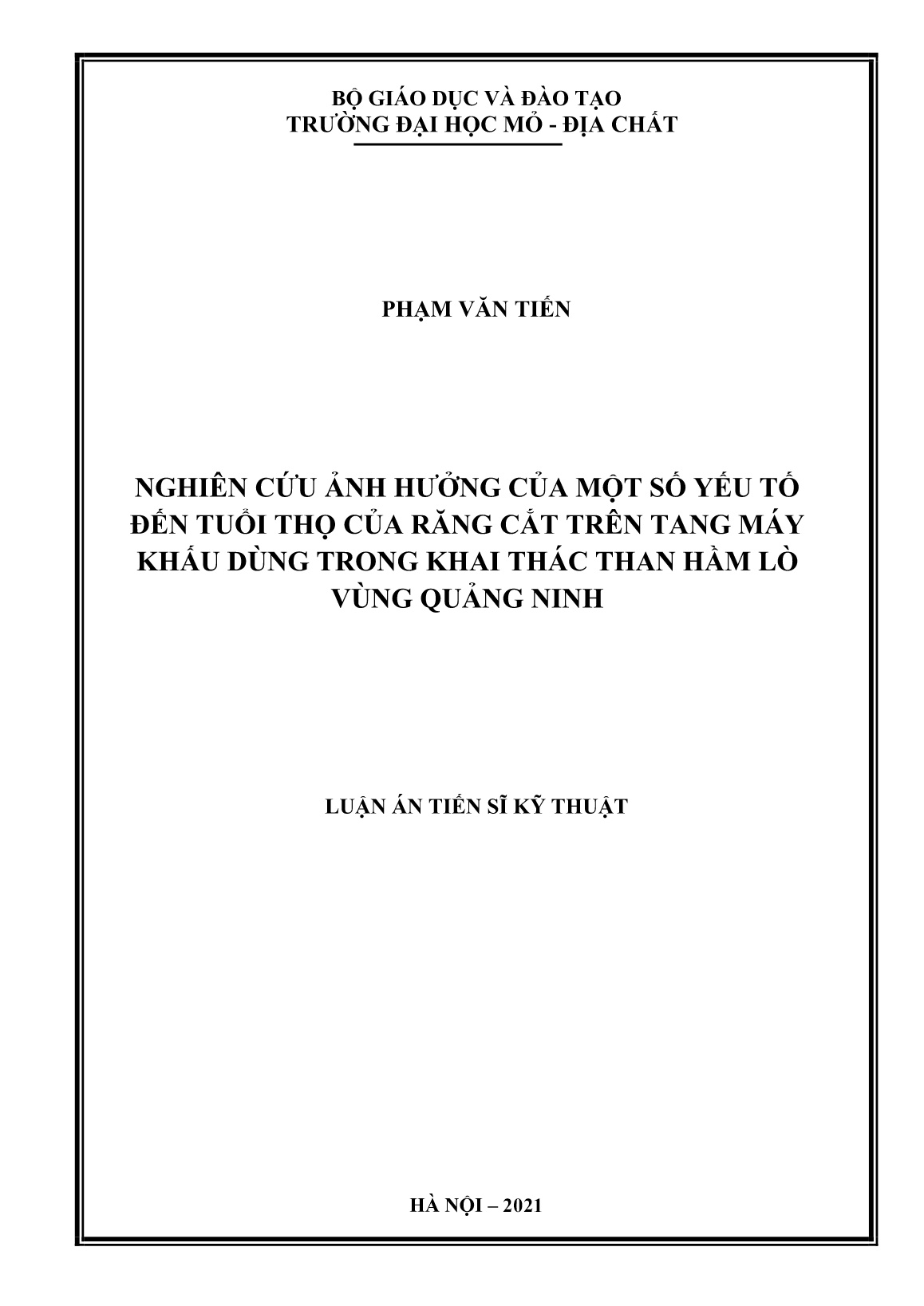
Trang 1
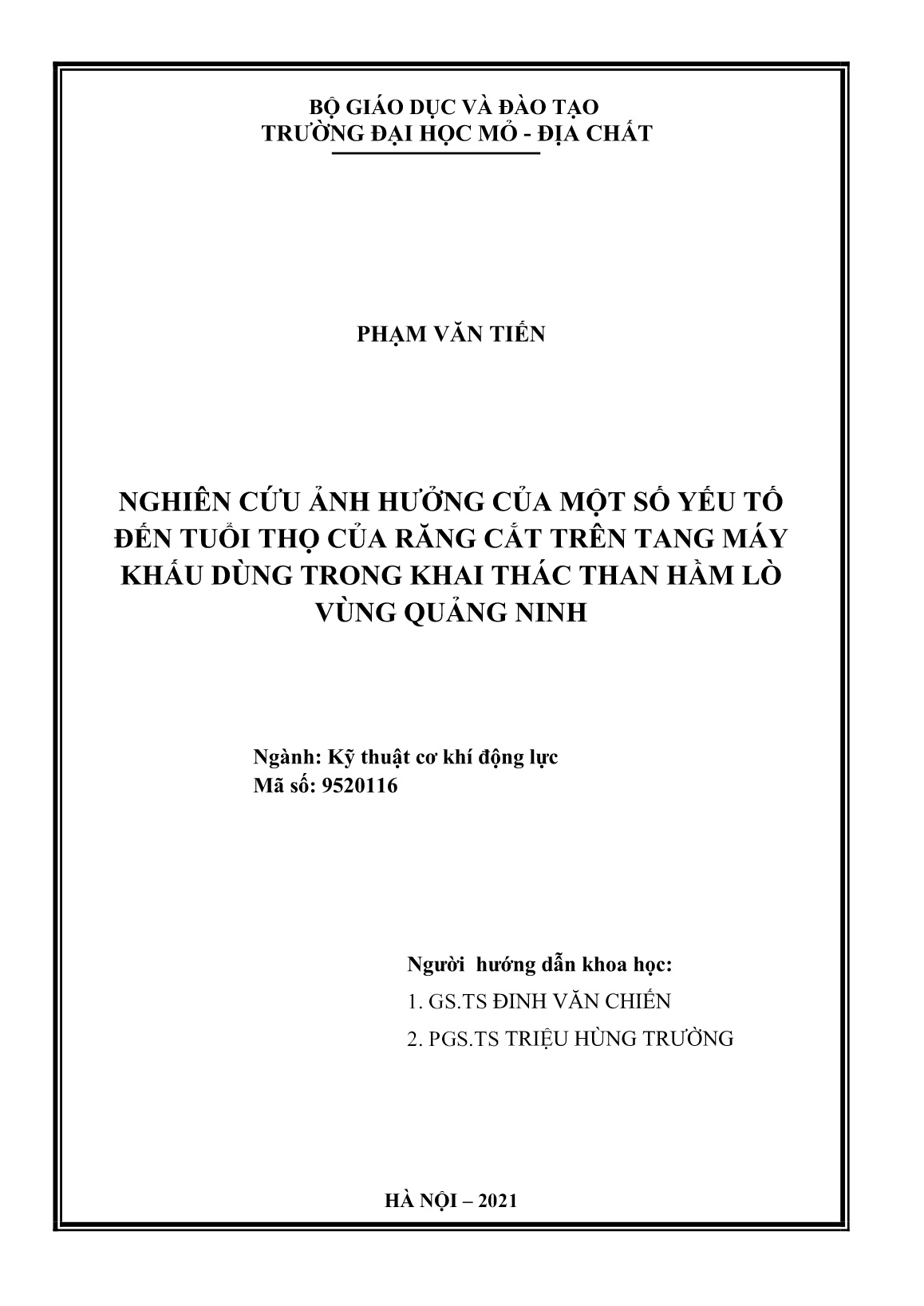
Trang 2
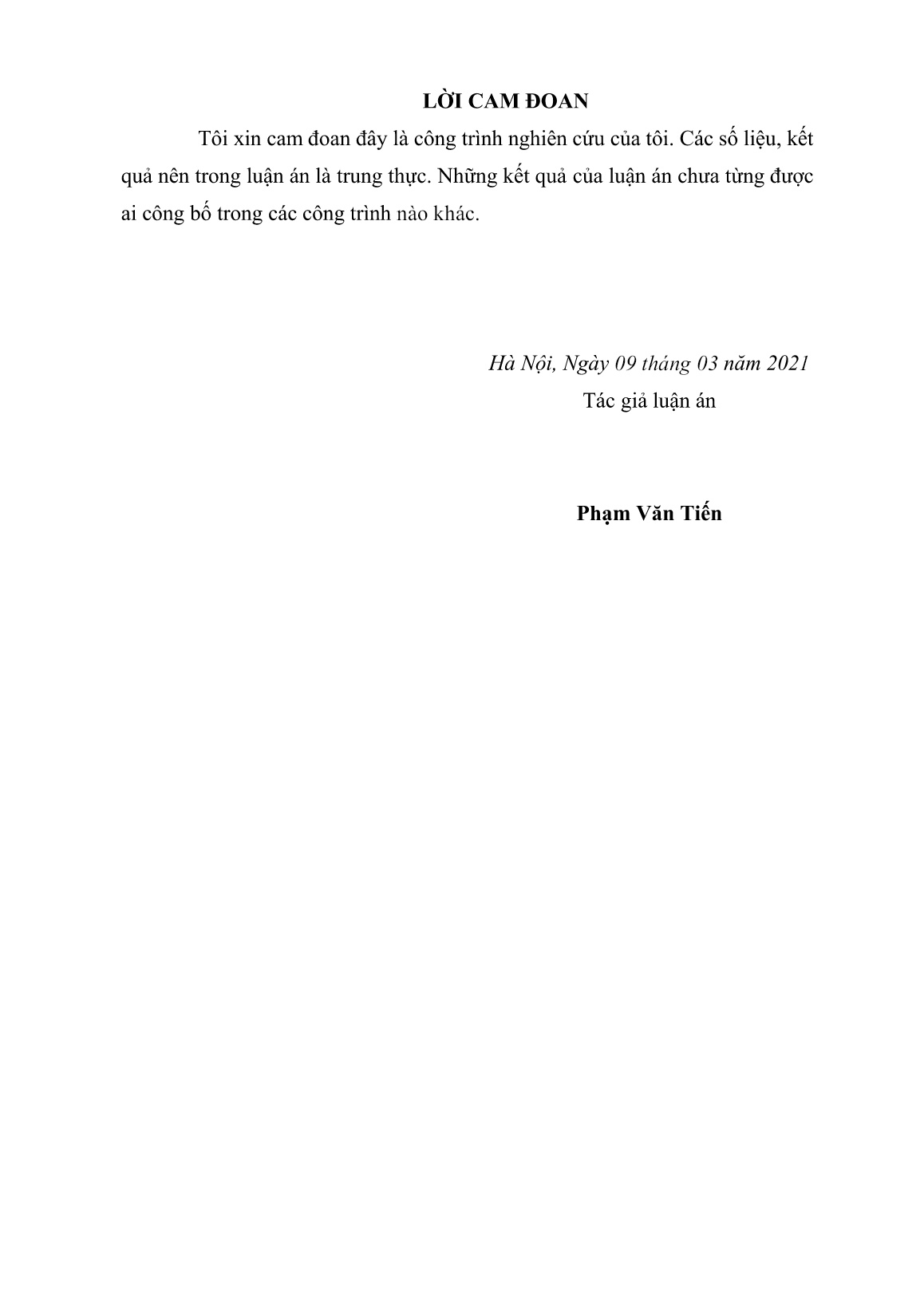
Trang 3
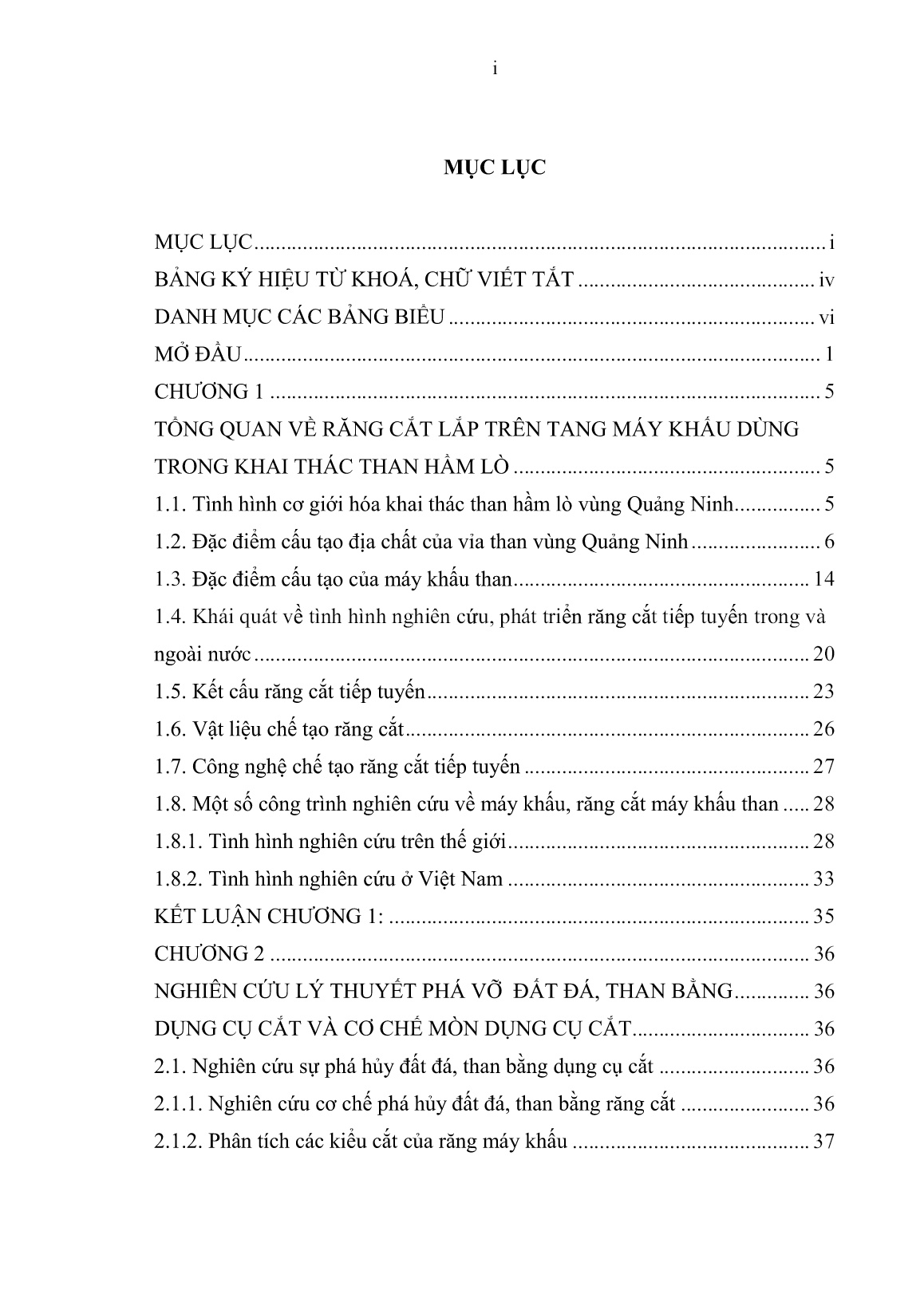
Trang 4
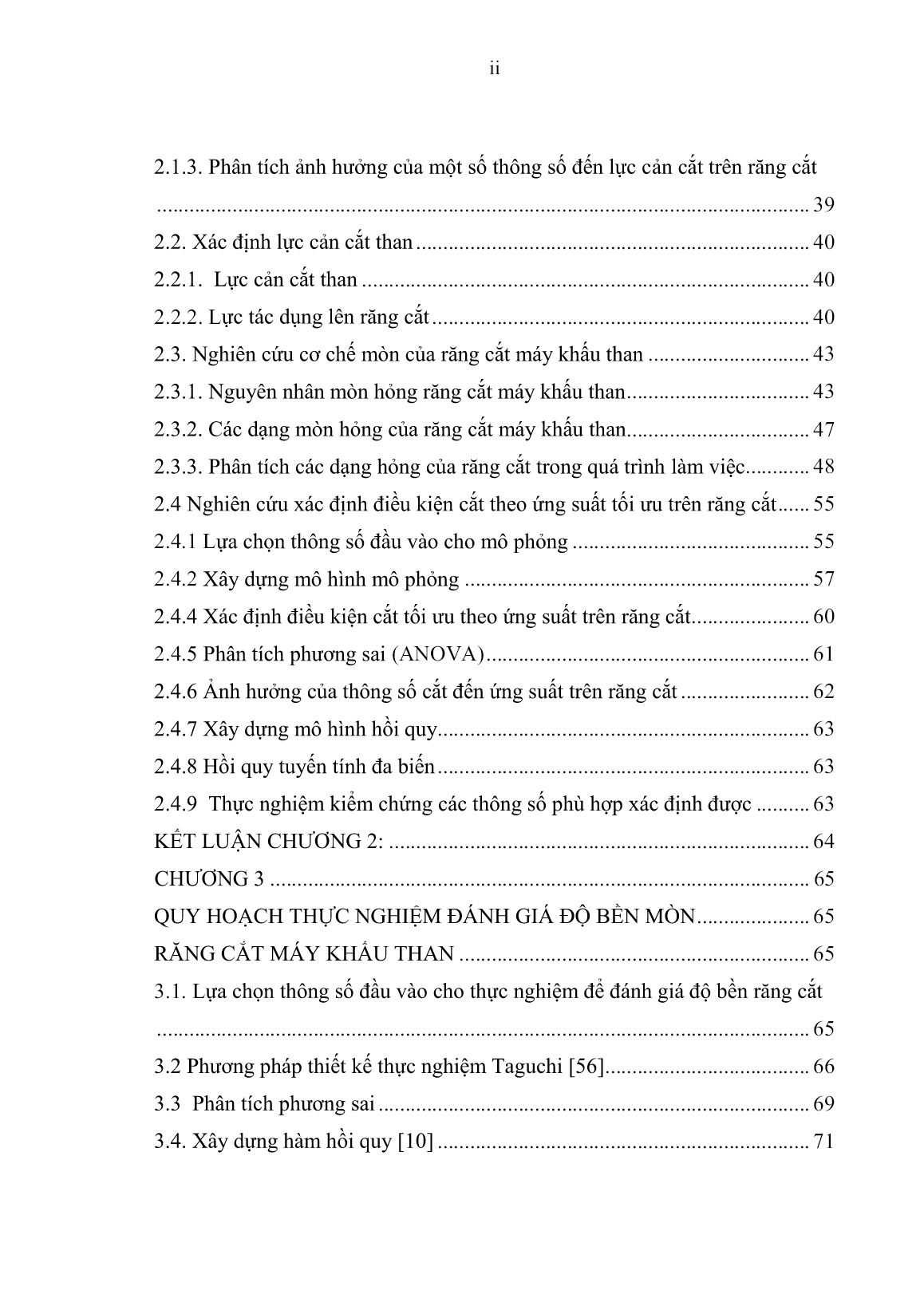
Trang 5
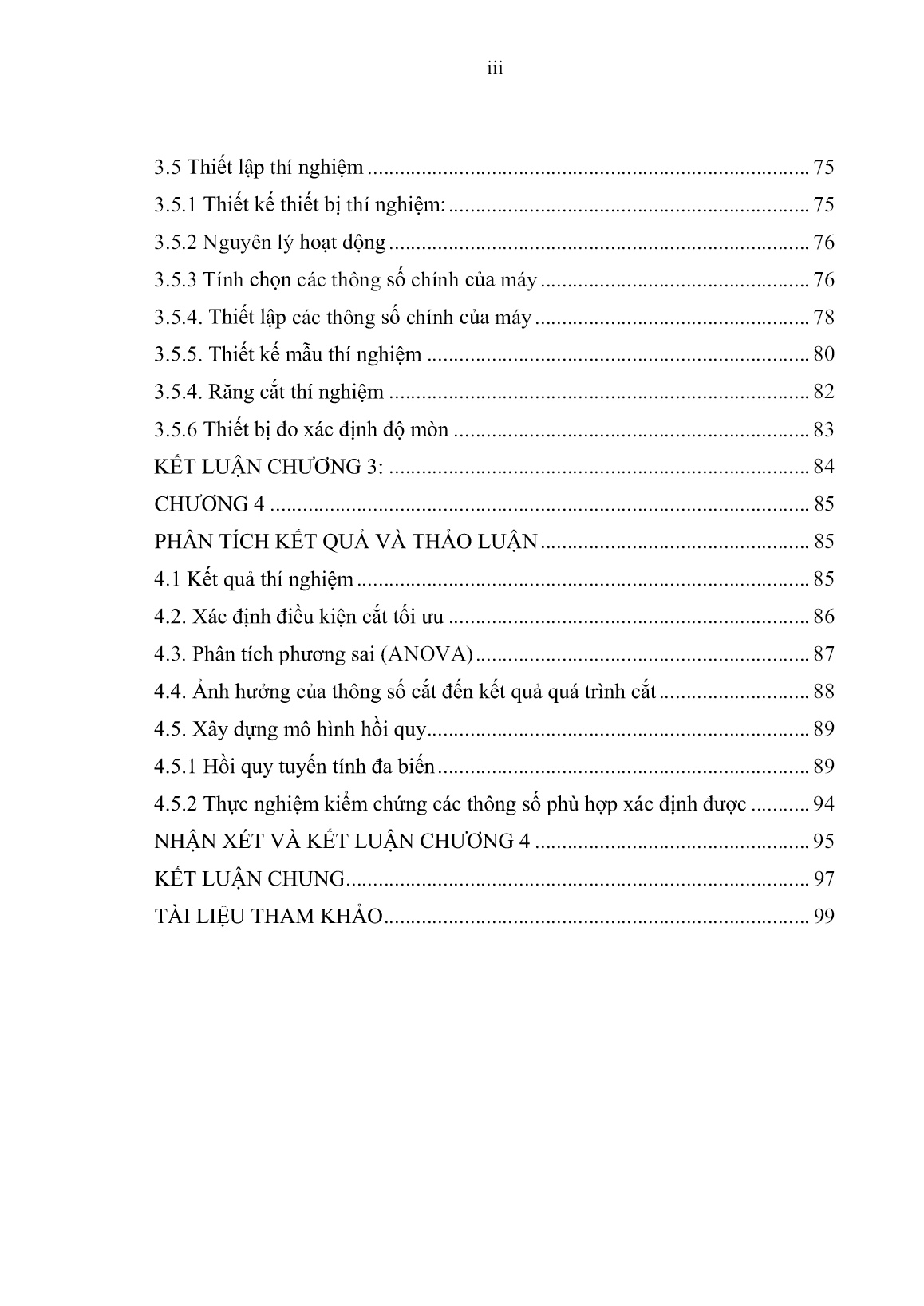
Trang 6
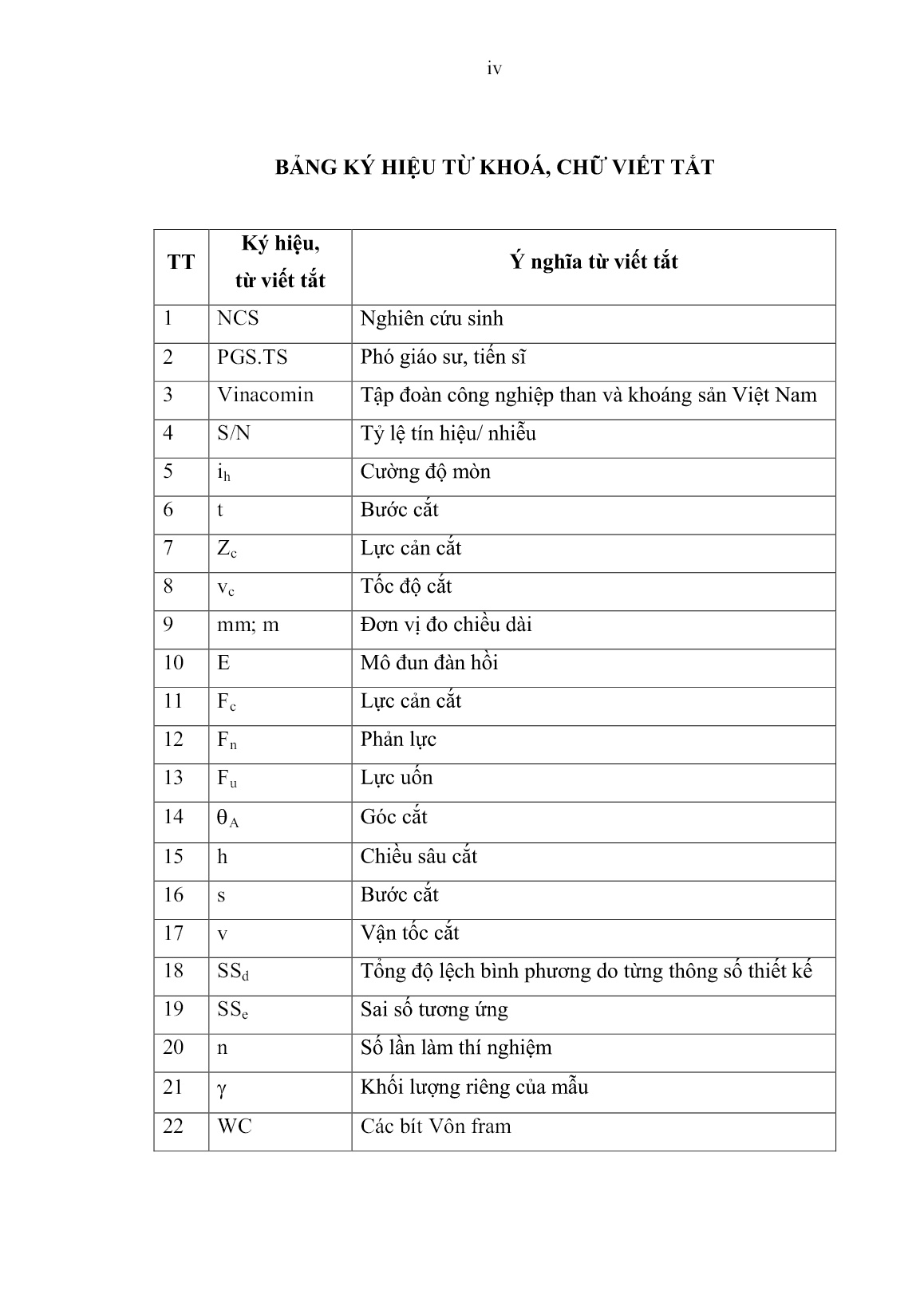
Trang 7
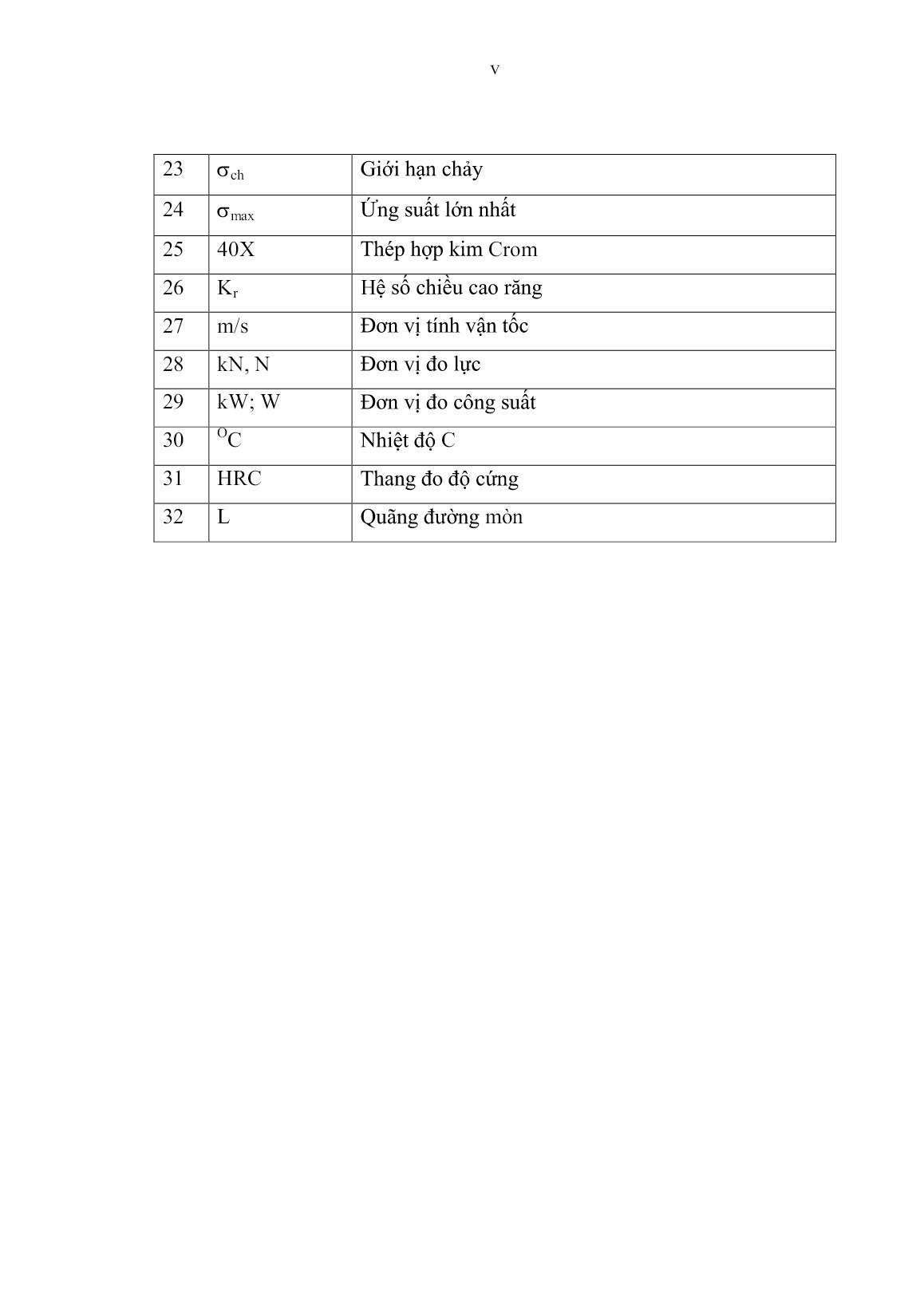
Trang 8
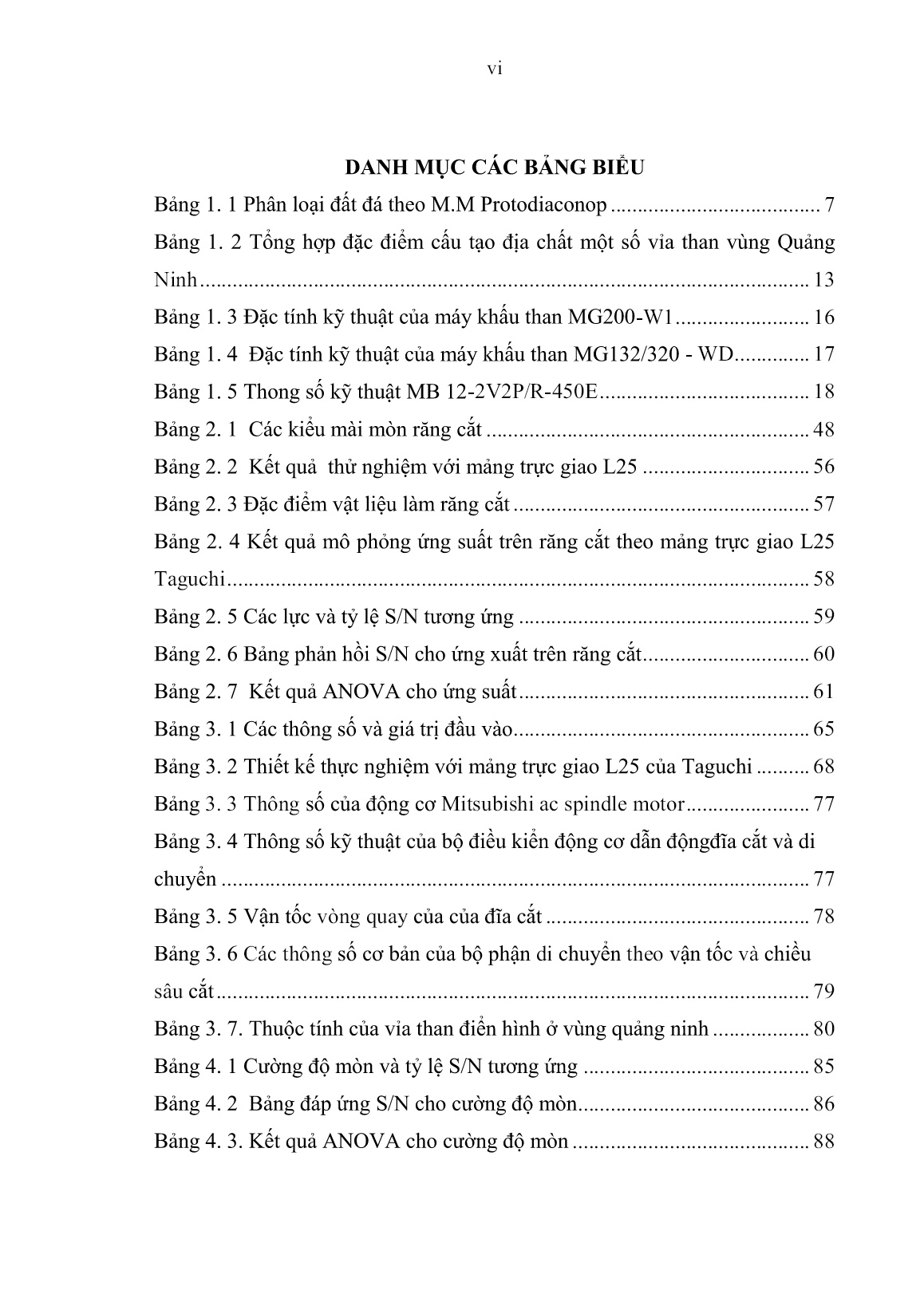
Trang 9
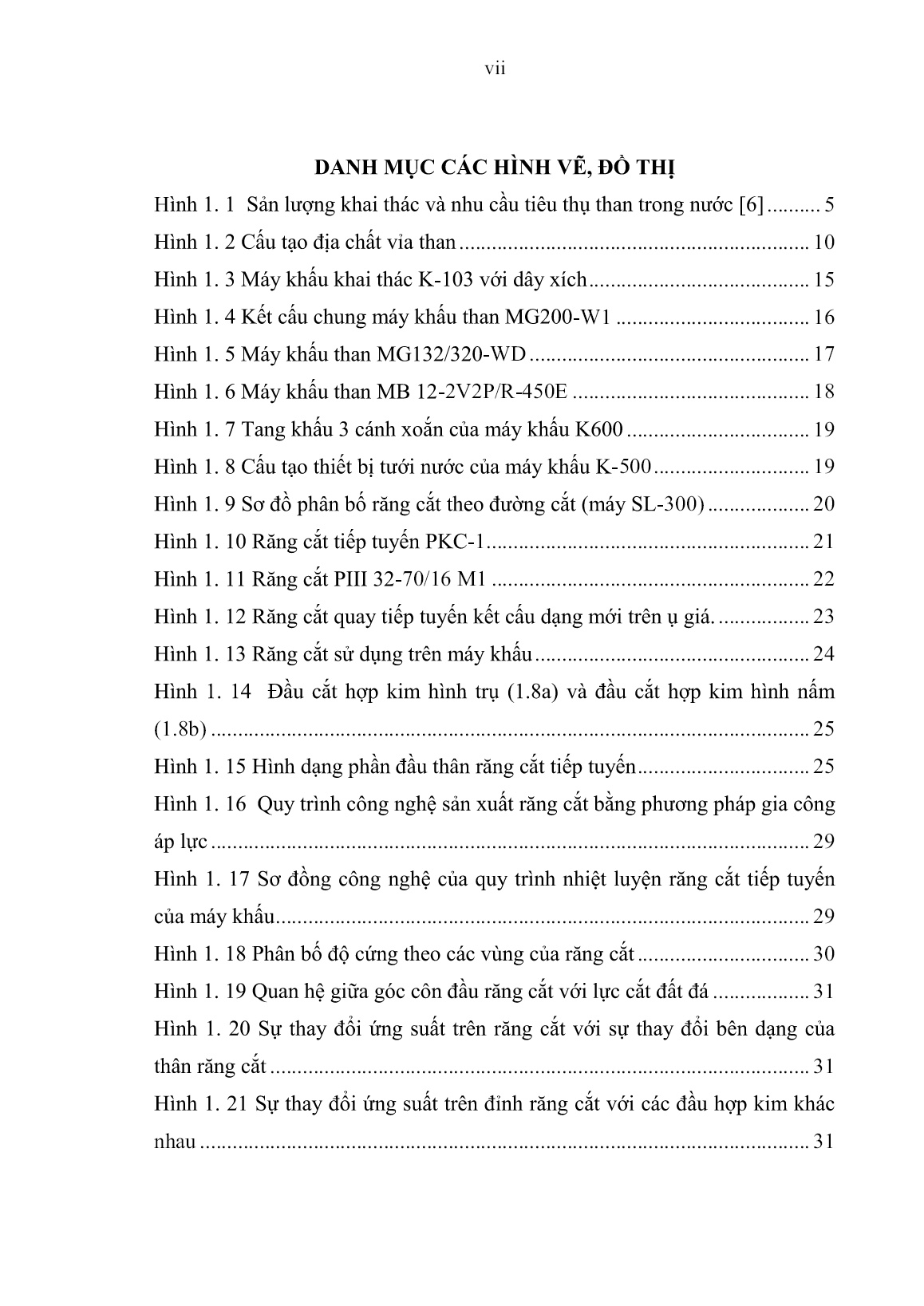
Trang 10
Tải về để xem bản đầy đủ
Bạn đang xem 10 trang mẫu của tài liệu "Luận án Nghiên cứu ảnh hưởng của một số yếu tố đến tuổi thọ của răng cắt trên tang máy khấu dùng trong khai thác than hầm lò vùng Quảng Ninh", để tải tài liệu gốc về máy hãy click vào nút Download ở trên.
Tóm tắt nội dung tài liệu: Luận án Nghiên cứu ảnh hưởng của một số yếu tố đến tuổi thọ của răng cắt trên tang máy khấu dùng trong khai thác than hầm lò vùng Quảng Ninh
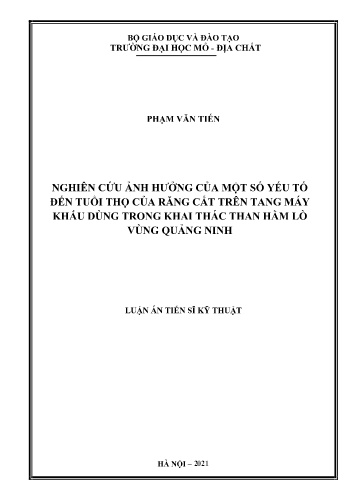
i khoáng sản và do đó giảm lực ấn sâu Py. Theo mức độ mòn của răng cắt, trên đầu răng tạo thành diện tích tiếp xúc mặt đầu (hình 2.1) và làm tăng lực ấn sâu. Nhƣ vậy, lực ấn sâu răng cắt không phụ thuộc vào việc có vận tốc đẩy răng vn (hình 2.1) hay không có vận tốc đẩy răng vn, (vn = 0). Mức độ đàn hồi của khoáng sản ở trƣớc răng cắt giảm xuống, khi các cục khoáng sản vỡ ra, và cùng với điều này áp lực khoáng sản lên mặt sau của răng cắt giảm, nghĩa là lực Py giảm. Lực cắt Px là tổng các lực xuất hiện trên mặt trƣớc của răng cắt và lực ma sát của răng với than (Py). 2.1.2. Phân tích các kiểu cắt của răng máy khấu Theo lý thuyết mài mòn tốc độ mài mòn của răng cắt phụ thộc vào áp lực tiếp xúc của răng cắt với đất đá. Vì vậy xác định các thông số tối ƣu và nâng cao độ bền của dụng cụ cắt bằng lý thuyết và thực nghiệm là xác định lực nhỏ nhất trên răng cắt từ sự ảnh hƣởng của các yếu tố: hình dạng hình học răng cắt, kích thƣớc phoi cắt, chế độ cắt và tính chất cơ lý của than hay khoáng sản. Khi xác 38 định lực cắt bằng thực nghiệm, kết quả thƣờng không ổn định, nhiều lúc giá trị rất khác nhau, chủ yếu là do tính chất cơ học của than không đồng nhất. Thực nghiệm đã chứng tỏ rằng lực tác dụng lên răng cắt trong quá trình cắt phụ thuộc không chỉ vào tính chất cơ học của khoáng sản mà còn phụ thuộc vào giá trị và vị trí tƣơng hỗ của mặt thoáng [37, 38]. Ngƣời ta chia các kiểu cắt ra làm 5 loại [53]: Trong sự phụ thuộc từ kích thƣớc h và t và sự tƣơng quan giữ chúng còn từ vị trí mặt thoáng bổ trợ cho quá trình cắt đƣợc đƣa ra trong hình 2.10. Hình 2. 2. Các dạng cắt khoáng sản của răng cắt Cắt tự do (Hình 2.2-a): Phoi cắt có hai mặt thoáng nhƣng khoảng cách giữa 2 đƣờng cắt liên tiếp nhỏ hơn chiều rộng răng (t b), do đó lực cắt là nhỏ nhất. Cắt bán tự do (Hình 2.2-b): Sự tách than đƣợc thực hiện khi đã có bề mặt thoáng thứ 2 xuất hiện. Điều này xảy ra khi bƣớc cắt t b, khi t = b + (5÷6)h thì cắt bán tự do chuyển thành cắt trên bề mặt hở. Cắt trên bề mặt hở (Hình 2.2-c): răng cắt trên bề mặt của gƣơng lò với bƣớc cắt t b + (5÷6)h. Khi này phoi cắt nghiêng về cả hai phía. Cắt bán bao bọc (hình 2.2-d): một thành bên của răng cắt tham gia vào quá trình cắt còn phía bên kia là mặt thoáng, do đó các cục than tách ra tạo thành độ nghiêng, chiều rộng phoi cắt lớn hơn chiều rộng răng cắt. II II t h B h h B h y a, b, c, d, e, h SS SSS t II II II I I I b 39 Cắt bao bọc (hình 2.2-e): răng cắt đi một lớp khoáng sản (phoi cắt) có chiều dày h trong một rãnh sâu, do đó chiều rộng phoi cắt bằng chiều rộng răng cắt. Cắt nhƣ thế này cả hai răng cắt phụ của răng cắt đều tham gia vào quá trình cắt nên yêu cầu lực cắt là lớn nhất. Trong 5 trƣờng hợp trên trƣờng hợp thứ 2 là đƣợc sử dụng phổ biến nhất cho máy khấu than. Trƣờng hợp một tuy có lực cắt nhỏ nhất nhƣng chi phí năng lƣợng riêng lớn, kèm theo kích thƣớc phoi cắt nhỏ và sinh bụi lớn. 2.1.3. Phân tích ảnh hƣởng của một số thông số đến lực cản cắt trên răng cắt Khi thay đổi bƣớc cắt t từ t=b đến t = b + (5÷6)h trong khi chiều sâu h cố định thì lực cắt tăng lên và đạt đến giá trị hằng số nhƣ hình 2.3. Và Bƣớc cắt tối ƣu đƣợc xác định khi năng lƣợng riêng đạt giá trị nhỏ nhất ttu = b + (1÷1,4) h nhƣ hình 2.3 – b. Hình 2. 3. Ảnh hưởng của chiều sâu và bước cắt đến lực cắt (a) và năng lượng riêng (b) Theo tài liệu [28] thì khi tăng góc cắt α làm cho lực cắt cũng tăng (Hình 2.4) điều này đƣợc giải thích nhƣ sau: tăng góc cắt làm tăng diện tích tiếp xúc phía trƣớc của răng nghĩa là mở rộng lớp nén chặt phía trƣớc răng kết quả là t'3 t'2 t'1 t=b Hw3min Hw2min Hw1min h1=const h2=const h3=const Hw, kWh/m3 t3 t2 t1 Z1 Z2 Z3 Z, kN t, mmt, mm b,a, h3=const h2=const h1=const h1 h2 h3 t=b 40 làm tăng lực cắt. Tuy nhiên lực cắt phần lớn phụ thuộc vào độ kiên cố của đất đá. Hình 2. 4. Ảnh hưởng của góc cắt đến lực cắt 2.2. Xác định lực cản cắt than 2.2.1. Lực cản cắt than Lực cản của than tác dụng lên răng cắt là một đại lƣợng luôn luôn thay đổi vì cấu trúc của than tại các điểm trong vỉa không đồng nhất, do trong vỉa than có các vết nứt, tạp chất lẫn lộn ... Do đó, trong thực tế để tính toán lực cản cắt hiện nay đƣợc xác định bằng cách thực nghiệm còn công thức lý thuyết chỉ đƣợc dùng để tính toán sơ bộ và tham khảo. Theo công thức thực nghiệm lực cản cắt trung bình Ztb đƣợc xác định sơ bộ bằng lực cản cắt đon vị nhân với chiều sâu cắt [77, 93]: Ztb = A.h, N (2.1) trong đó: Ztb – Lực cản cắt trung bình, N; A Lực cản cắt đơn vị đƣợc xác định bằng thực nghiệm, h Chiều sâu cắt, mm. 2.2.2. Lực tác dụng lên răng cắt Trong quá trình cắt, răng cắt chịu tác dụng của lực cản cắt của than và có thể phân lực cản đó ra làm ba thành phần (hình 2.5). Z - Lực cản cắt tác dụng theo phƣơng quỹ đạo cắt tại điểm giữa của Z, kN , h1 h2 h3 50 60 70 80 90 100 110 120 o 41 răng cắt, Y - Lực cản tiến, tác dụng theo phƣơng di chuyển tịnh tiến của máy, X - Lực đẩy ngang (lực bên sƣờn). Lực cản theo hƣớng cắt Z để xác định công suất cắt, lực cản Y để xác định công suất di chuyển, lực cản X với răng cắt tiếp tuyến thƣờng nhỏ có thể bỏ qua. Lực cản tổng cộng lên răng sẽ là [99, 93]: Zo = Z + .Y, N (2.2) trong đó là hệ số ma sát giữa than với răng cắt Hình 2. 5. Lực tác dụng lên răng cắt 1- Than, 2- Răng cắt Các thành phần lực trên nói lên bản chất của chúng, việc xác định lực cản cắt theo công thức trên rất khó khăn. Trong thực tế, để xác định lực cản cắt dùng cách phân tích nhƣ sau: Tại một điểm trên mặt trƣớc của răng cắt chịu lực cản pháp tuyến N và lực ma sát .N. Hợp lực R của chúng có thể phân thành hai thành phần: R = Y1 + Zc , N (2.3) Trong đó: Zc – Lực cản cắt theo phƣơng tốc độ cắt Vc , N Y1 – Lực cản theo phƣơng di chuyển máy, N. Tùy theo góc trƣớc của răng cắt dƣơng hay âm mà lực Y1 có hƣớng ép răng cắt vào gƣơng hay đẩy ra. 42 Ngoài ra, còn cần thấy rằng khi mặt sau của răng bị mòn, trên phần diện tích mòn còn chịu lực đẩy pháp tuyến Y2 và lực ma sát .Y2 . Trên hai mặt bên của răng bị mòn, cũng chịu lực cản pháp tuyến và lực ma sát. Tuy nhiên, để đơn giản, lực cản cắt trung bình tác dụng lên một răng đƣợc xác định: .(0,35. 0,3) 1 . . . . . . . . cos tb tb tb t g a tb A b Z h t k k k k b h tg , N ; (2.5) Trong đó: A – Lực cản cắt đơn vị của than, A = 2410 -:- 3000 N/cm, chọn A = 2500 N/cm b – Chiều dày lƣỡi cắt của răng, b = 0,8 cm htb – Chiều dày cắt trung bình của răng cơ bản, biên góc, góc cm ttb – Chiều rộng phoi cắt trung bình của răng cơ bản, biên góc, góc, cm kt – Hệ số vết lộ gƣơng, kt = 1,1 -:- 1,25 chọn kt = 1,2 kg – Hệ số kể đến ảnh hƣởng của góc cắt, kg = 0,98 ka – Hệ số kể đến ảnh hƣởng sức đẩy áp lực mỏ, ka = 0,56 - Hệ số kể đến hình dạng cắt trƣớc của răng, = 0,92 - Góc lắp răng với phƣơng di chuyển của bộ phận công tác, Với răng cơ bản = 0 Với răng biên góc = 23 Với răng góc = 45 – Góc vỡ của than, theo [4] tb tb h h tg 023,0.45,0 ; (2.6) Với htb đƣợc tính theo đơn vị mét (m) Với răng cắt cơ bản: = 43 Với răng cắt gần biên: = Với răng góc: = Do đó: Lực cản cắt tác dụng lên răng cắt cơ bản: Ztb = 2500. = 1356 N Trƣờng hợp 2 với răng tiếp tuyến thì b = 0,4 cm. Lúc này thay vào công thức trên tính đƣợc Ztb = 1147 N Từ đây thấy rằng nếu tính tiếp cho các răng khác thì cũng thấy giảm lực cản. 2.3. Nghiên cứu cơ chế mòn của răng cắt máy khấu than Một số nghiên cứu của một số mỏ than của Nga chỉ ra rằng khi trong vỉa xuất hiện đất đá kẹp thì lƣợng tiêu thụ răng cắt tăng nhanh. Khi răng cắt làm việc trong vỉa than có độ dày 1,8m hệ số kiên cố của than f = 1÷1.5 có 21% cát kết có độ cứng f = 4÷5 thì lƣợng tiêu thụ răng cắt đã tăng lên hơn khoảng 90 lần so với điều kiên địa chất tƣơng tự không có đất đá kẹp [45]. Ở Việt nam tuy chƣa có một nghiên cứu hay báo cáo cụ thể nào nhƣng theo thống kê ở một số mỏ đã áp dụng máy khấu cũng nhận thấy rằng lƣợng tiêu thụ răng cắt tăng đột biến khi máy khấu làm việc với vỉa có đất đá kẹp [1]. 2.3.1. Nguyên nhân mòn hỏng răng cắt máy khấu than Điều kiện khí hậu môi trƣờng của nƣớc ta là điều kiện khí hậu nóng ẩm vì vậy tất cả các máy móc thiết bị cũng đều chịu tác động của điều kiện môi trƣờng đó (máy chịu sự ôxi hóa từ môi trƣờng). Mặt khác đối với các công việc trong ngành mỏ nói chung đều là những công việc nặng nhọc, đặc biệt là mỏ hầm lò có môi trƣờng khắc nghiệt (nhiệt độ cao, độ ẩm lớn, ...) các máy móc thiết bị khi làm việc trong mỏ cũng chịu những sự tác động của môi 44 trƣờng mỏ gây ra mòn hỏng cho chi tiết và thiết bị. Ngoài ra trong quá trình làm việc trong mỏ hầm lò máy móc thiết bị cũng chịu sự tác động của áp lực mỏ làm ảnh hƣởng đến quá trình làm việc của máy móc thiết bị. Những tác động của môi trƣờng cũng làm giảm năng suất của các thiết bị. Trong một cụm máy có nhiều loại chi tiết, điều kiện ma sát của từng loại cũng khác nhau. Các chi tiết khác nhau về vật liệu, gia công chế tạo... Vì vậy, trong quá trình làm việc các chi tiết của cụm máy có độ mòn không đồng đều. Khi cụm máy đƣa vào sửa chữa có những chi tiết có thể dùng lại đƣợc, có chi tiết phải sửa chữa Hƣ hỏng do chế tạo, hƣ hỏng do vận hành và hƣ hỏng do chất lƣợng vật liệu... Hƣ hỏng do vận hành là nguyên nhân chủ yếu gây nên các hƣ hỏng máy. Hƣ hỏng do vận hành đƣợc chia ra làm 3 nhóm chính: - Mòn cơ học là dạng mòn do các tác dụng cơ học. Đây là dạng hƣ hỏng do tiếp xúc, mài mòn do tróc dính, do sự phá huỷ các bề mặt liên quan đến sự hao mòn vật liệu. Các giai đoạn mài mòn đƣợc biểu thị nhƣ hình sau đây: - Mòn dƣới tác dụng của môi trƣờng. Mòn do dòng chất lỏng, dòng khí hoặc hoá chất. Mòn dạng này có thể do các chất trên hòa tan khuyếch tán hay thẩm thấu theo thời gian vào chi tiết máy; cũng có thể do tác dụng hoá học, do các tác dụng của áp lực có chu kỳ hoặc không chu kỳ tiếp xúc với chi tiết... Các dạng mòn trên đƣợc gọi là ăn mòn kim loại. Hình 2. 6. Sơ đồ các giai đoạn mài mòn cơ học I- Giai đoạn bắt đầu mài mòn (giai đoạn khi máy bắt đầu làm việc) II- Giai đoạn mài mòn đã bão hòa (giai đoạn xảy ra mài mòn khi máy 45 làm việc bình thường) III- Giai đoạn mài mòn phát triển nhanh (mài mòn do sự cố, mài mòn đã phát triển đến mức phải loại bỏ chi tiết) - Dạng thứ 3 là dạng kết hợp cả cơ học và ăn mòn vật liệu dƣới tác dụng của các môi trƣờng. Dạng mài mòn (mòn cơ học) thƣờng xuất hiện trên các bề mặt khô tiếp xúc có chuyển động tƣơng đối với nhau, đặc biệt các bề mặt lắp ghép quá chặt, ma sát lớn,...Mòn cơ học xuất hiện khi có chuyển động của kim loại trên kim loại hay có môi trƣờng các chất phi kim loại chuyển động trên nó. Trong thực tế ngƣời ta phân mòn cơ học ra các loại nhƣ sau [27]: + Sự phá huỷ bề mặt do tróc dính (tróc loại 1) Do ma sát hình thành các mối liên kết cục bộ, gây biến dạng và phá hỏng mối liên kết đó (quá tải cục bộ). Xuất hiện chủ yếu ở ma sát trƣợt, tốc độ dịch chuyển nhỏ, thiếu bôi trơn làm áp suất cục bộ tăng quá giới hạn chảy. + Sự phá huỷ bề mặt do tróc nhiệt (tróc loại 2 hay mài mòn nhiệt) Do ma sát nhiệt độ tăng đáng kể hình thành các mối liên kết cục bộ, gây biến dạng dẻo rồi phá hỏng mối liên kết ấy (quá tải nhiệt). Dạng này xuất hiện chủ yếu do chuyển dịch tƣơng đối lớn và áp lực riêng p tăng, cấu trúc kim loại xảy ra hiện tƣợng kết tinh lại, ram, tôi cục bộ. Tróc loại 2 còn tuỳ thuộc vào độ bền, tính dẫn nhiệt, độ cứng của vật liệu... + Sự phá huỷ do mỏi: đây là dạng mài mòn rỗ. Do tác động của ứng suất biến đổi chu kỳ, ứng suất tăng lên và lớn hơn giới hạn đàn hồi. Hiện tƣợng này xảy ra do mối liên kết ma sát không liên tục, nó xảy ra trong từng phần của của bề mặt tiếp xúc. Phá huỷ do mỏi thƣờng gặp ở những bề mặt có nứt tế vi, vết lõm sâu, độ bóng thấp hoặc không đồng đều. Dạng mòn này thƣờng xảy ra khi có ma sát lăn, trên bề mặt của ổ lăn và ổ trƣợt, trên bề mặt của bánh răng... + Phá huỷ bề mặt do xói mòn kim loại (Mòn do tác dụng của môi trƣờng các dòng chảy). Là sự phá huỷ các bề mặt do lực tác dụng va đập và lập lại 46 nhiều lần hoặc thời gian kéo dài, áp lực lớn của dòng chất lỏng, dòng khí, dòng chuyển động của bột mài, sự phóng điện hoặc chùm tia năng lƣợng...chúng làm cho quá trình mòn do ma sát phức tạp thêm. + Phá huỷ bề mặt do hiện tƣợng fretting. Quá trình fretting đƣợc đặc trƣng: - Bởi sự có mặt của các chuyển vị nhỏ (bắt đầu có trị số lớn hơn khoảng cách giữa các nguyên tử; - Bởi sự đặc tính động của tải trọng; - Bởi sự ô xy hoá trong không khí làm tạo ra các sản phẩm bị ăn mòn; - Một số nhà khoa học còn cho rằng quá trình fretting còn do tróc gây nên thể hiện rõ nhất ở những chỗ tiếp xúc. - Là hiện tƣợng phá huỷ bề mặt do tróc, gỉ do sự ôxy hoá động, xảy ra do tổng hợp của nhiều yếu tố: ma sát, áp lực, độ dịch chuyển bề Mặt mặt tiếp xúc nhỏ, nhất ở điều kiện vận tốc (v) lớn, áp lực cao (p), nhiệt độ (to) cao. Muốn giảm hiện tƣợng này ta cần giảm vận tốc, áp lực, nhiệt độ. Sự phá huỷ bề mặt do ăn mòn kim loại: Ăn mòn là sự phá huỷ kim loại do tƣơng tác hoá học, điện hoá hoặc sinh hoá của kim loại với môi trƣờng. Quá trình ăn mòn kèm theo sự ô xy hoá bề mặt kim loại để tạo thành hợp chất hoá học của kim loại (oxit, hydroxit, cacbonat...). Sự phá huỷ bề mặt do ăn mòn điện: Sự phá hỏng bề mặt do tác dụng phóng điện khi có dòng điện đi qua : cổ góp, chổi than, các cơ cấu đóng và ngắt điện,... Từ những điều kiện làm việc trong mỏ và nhũng nguyên nhân ta thấy rằng nguyên nhân chủ yếu gây mòn hỏng chi tiết máy và thiết bị mỏ là: - Do ma sát xuất hiện giữa các bề mặt có sự chuyển động tƣơng đối với nhau, làm bề mặt của các chi tiết bị mài mòn, dẫn đến làm giảm kích thƣớc 47 hình học của chi tiết và thay đổi khe hở lắp ghép ban đầu. Kích thƣớc hình học giảm, làm độ bền của các chi tiết giảm. - Do các điều kiện làm việc của máy nhƣ tải trọng, nhiệt độ, do điều chỉnh các thông số làm việc không phù hợp làm cho các chi tiết bị biến dạng, bị mỏi, dẫn đến hỏng đột ngột. Sự mòn hỏng này thƣờng mang tính quy luật, phần lớn do ý thức trách nhiệm, do trình độ kỹ thuật non kém của ngƣời sử dụng gây ra. - Do ảnh hƣởng của môi trƣờng, do thiết kế (vật liệu không đủ bền, kết cấu chƣa hợp lý gây tập trung ứng suất), do chế tạo (Phƣơng pháp gia công, phƣơng pháp lắp giáp...). Những yếu tố này cũng gây ảnh hƣởng không nhỏ đến quá trình mòn của chi tiết. 2.3.2. Các dạng mòn hỏng của răng cắt máy khấu than Răng cắt là bộ phận trực tiếp nhận mọi lực tác động từ than nên thƣờng rất nhanh hỏng (2.7). Răng cắt mòn hỏng nhanh ảnh hƣởng trực tiếp tới năng suất của máy do phải dừng lại thay răng, đồng thời tăng chi phí răng cắt cho một tấn than dẫn tới tăng giá thành khai thác. Các dạng mòn hỏng của răng cắt máy khấu than rất đa dạng và xuất phát từ nhiều nguyên nhân khác nhau, vì thế việc nghiên cứu các dạng mòn hỏng của răng sẽ là rất quan trọng và là cơ sở cho các công việc tếp theo. a, b, Hình 2. 7. Các dạng hỏng của răng cắt a, Hỏng do mài mòn b, Hỏng do quá tải 48 Bảng 2. 1 Các kiểu mài mòn răng cắt Các kiểu mài mòn răng cắt Các kiểu mài mòn răng cắt Răng cắt mới: Chốt cắt bằng hợp kim cứng đƣợc liên kết cứng với thân răng bằng thép. Phá hủy chốt cắt: Gãy do tính dòn của chốt cắt, do ứng suất cắt cao. Răng mài mòn: Mòn không đối xứng của đỉnh chốt cắt. Chốt cắt bị tuột khỏi thân răng: Toàn bộ vật liệu chốt cắt bị tuột khỏi thân răng. Mài mòn không đối xứng: Các răng cắt bị mài mòn ở một phía Răng bị mài mòn tƣơng đƣơng mà không hề có sự tuột chốt cắt. Mài mòn phần thân thép: Mài mòn của phần nón thép theo đƣờng kính là kết quả của sự chà xát Phá hủy trục thép của thân răng cắt: Răng cắt bị hƣ hỏng phần dƣới trục thép bên dƣới nón thép và bên trên ngàm đỡ 2.3.3. Phân tích các dạng hỏng của răng cắt trong quá trình làm việc 2.3.3.1. Phân tích cơ chế hỏng răng cắt do hiện tượng mài mòn Từ cơ chế phá hủy đất đá bằng răng cắt ta thấy rằng ứng suất tiếp xúc trên răng cắt sẽ giảm dần từ đỉnh của hợp kim cứng đến hết phần tiếp xúc của đất đá 49 đến răng cắt. Cùng sự phân tích cấu tạo và vật liệu làm răng cắt ta nhận thấy rằng với vật liệu đầu răng thƣờng làm bằng hợp kim cứng có độ cứng cao (≥ 70 HRC), vật liệu làm thân răng thƣờng làm 30XM, 40X, 40XM, ... có độ cứng đến 54 HRC thấp hơn nhiều so với đầu hợp kim cứng tuy nhiên áp suất tiếp xúc giữa nó với đất đá vẫn rất lớn. Nhƣ vậy dễ dàng nhận thấy vùng dễ tổn thƣơng nhất là vùng kim loại bao xung quanh hợp kim cứng. a, b, c, d, Hình 2. 8. Các dạng mòn hỏng của răng cắt Theo các kết quả nghiên cứu, răng cắt bị hỏng theo mài mòn sẽ có các hiện tƣợng sau: - Răng cắt làm việc với vỉa than không có đá kẹp f = 0.8÷1.5 lƣợng mòn răng cắt nhỏ, gần nhƣ đầu hợp kim cứng không bị mài mòn. Răng cắt chỉ bị mài mòn xung quanh đầu hợp kim cứng đến khi làm suy yếu liên kết giữa đầu hợp kim cứng và thân răng (hình 2.8-a) cuối cùng sẽ dẫn đến mất đầu hợp kim cứng, quá trình mòn diễn ra rất chậm. Lƣợng tiêu thụ răng cắt nhỏ chỉ 0.5÷2 răng/1000 tấn than; - Răng cắt làm việc với vỉa có độ kiên cố trung bình (than cùng đất đá kẹp có độ kiên cố f = 2÷5) qua quá trình sử dụng đầu hợp kim cứng bị mài mòn nhƣng lƣợng mòn nhỏ, tuy nhiên phần kim loại bao quanh đầu hợp kim bị mòn nhanh (hình 2.8-b) dẫn tới suy yếu liên kết của nó với đầu hợp kim và nhanh chóng mất đầu hợp kim cứng. Lƣợng tiêu thụ răng cắt từ 12÷50 răng/1.000 tấn than; - Răng cắt làm việc với vỉa có độ kiên cố cao (than cùng với đất đá kẹp f = 5÷10) quá trình sử dụng răng cắt bị mài mòn cả phần đỉnh răng và thân 50 răng (hình 2.8-c,d). Trong nghiên cứu của [46] đã chỉ ra rằng khi răng làm việc với đất đá có độ kiên cố cao (độ bền nén 120 MPa (tƣơng đƣơng f = 12) với vận tốc cắt v = 2.5 m/s, chiều sâu cắt h = 10 mm, bƣớc cắt t = 50 mm) nhiệt độ ở bề mặt tiếp xúc của răng và đất đá tăng lên nhanh chóng có thể đạt trên 1.100 o C [46] (xem hình 2.9) có thể làm tan chảy kim loại, ngoài ra còn xuất hiện hiện hiện tƣợng đánh lửa gây nguy hiểm đến điều kiện an toàn mỏ. Hình 2. 9. Biểu đồ tăng nhiệt trên bề mặt của răng cắt trong quá trình làm việc 2.3.3.2. Phân tích cơ chế hỏng răng theo điều kiện phá hủy Từ công thức (2.5) ta thấy rằng lực cắt tỉ lệ thuận với chiều sâu cắt trong một số trƣờng hợp gặp đất đá cứng lực cắt tăng đột ngột làm phá hủy răng cắt. Hiện tƣợng hỏng răng do quá tải thƣờng xuất hiện trong các trƣờng hợp răng bị lỗi khi chế tạo (khuyết tật trong khi gia công hoặc nhiệt luyện), tính toán lựa chọn răng cắt không phù hợp với điều kiện địa chất mỏ. Phổ biến hơn do kết hợp của quá trình mài mòn và tải trọng lớn khi gặp đất đá kẹp là nguyên nhân chính làm tăng nhanh quá trình hỏng răng cắt. Nếu một răng cắt bị hỏng răng cắt tiếp theo trên một đƣờng cắt sẽ phải cắt lớp đất đá có chiều dày lớn hơn nghĩa là lực cắt trên nó sẽ tăng đột biến gây quá tải và khiến nó bị hỏng nhanh hơn. Vì vậy việc xác định đƣợc các thông số nhƣ chiều cao tối đa của phần thò ra của đầu hợp kim và chiều sâu tối thiểu của đầu hợp kim nằm trong thân răng sẽ giúp nâng cao tuổi thọ của răng cắt trong quá trình làm việc. Ngoài ra từ cơ sở đó ta có thể dự đoán đƣợc tuổi thọ của răng cắt sau 51 quá trình làm việc. Lực cắt P và lực uốn N đƣợc xác định nhƣ sau cP Z Sin (2.9) cN Z Cos (2.10) Trong đó: Zc – Lực cắt tác dụng lên răng cắt đƣợc xác định theo công thức (2.5), kN; θ – Góc cắt, độ. Hình 2. 10 Sơ đồ phân bố tải trọng trên răng Hình 2. 11 Bểu đồ nội lực của răng cắt 52 Hình 2. 12 Biểu đồ nội lực trên mặt cắt ngang của răng cắt. Để đảm bảo điều kiện bền thì: Với điểm 1 (hình 2.12): ứng suất nén phải nhỏ hơn ứng suất nén cho phép 1 ;td n Với điểm 3 (hình 2.12): ứng suất ké
File đính kèm:
luan_an_nghien_cuu_anh_huong_cua_mot_so_yeu_to_den_tuoi_tho.pdf
Tom tat thong tin ve KL moi cua LATS-Pham Van Tien.pdf
Tom tat LATS T.Viet-Pham Van Tien.pdf
Tom tat LATS T.Anh-Pham Van Tien.pdf