Luận án Nghiên cứu ảnh hưởng của nhiệt độ, tải trọng và thời gian đến tổ chức tế vi và cơ tính của ống thép chịu nhiệt hợp kim thấp
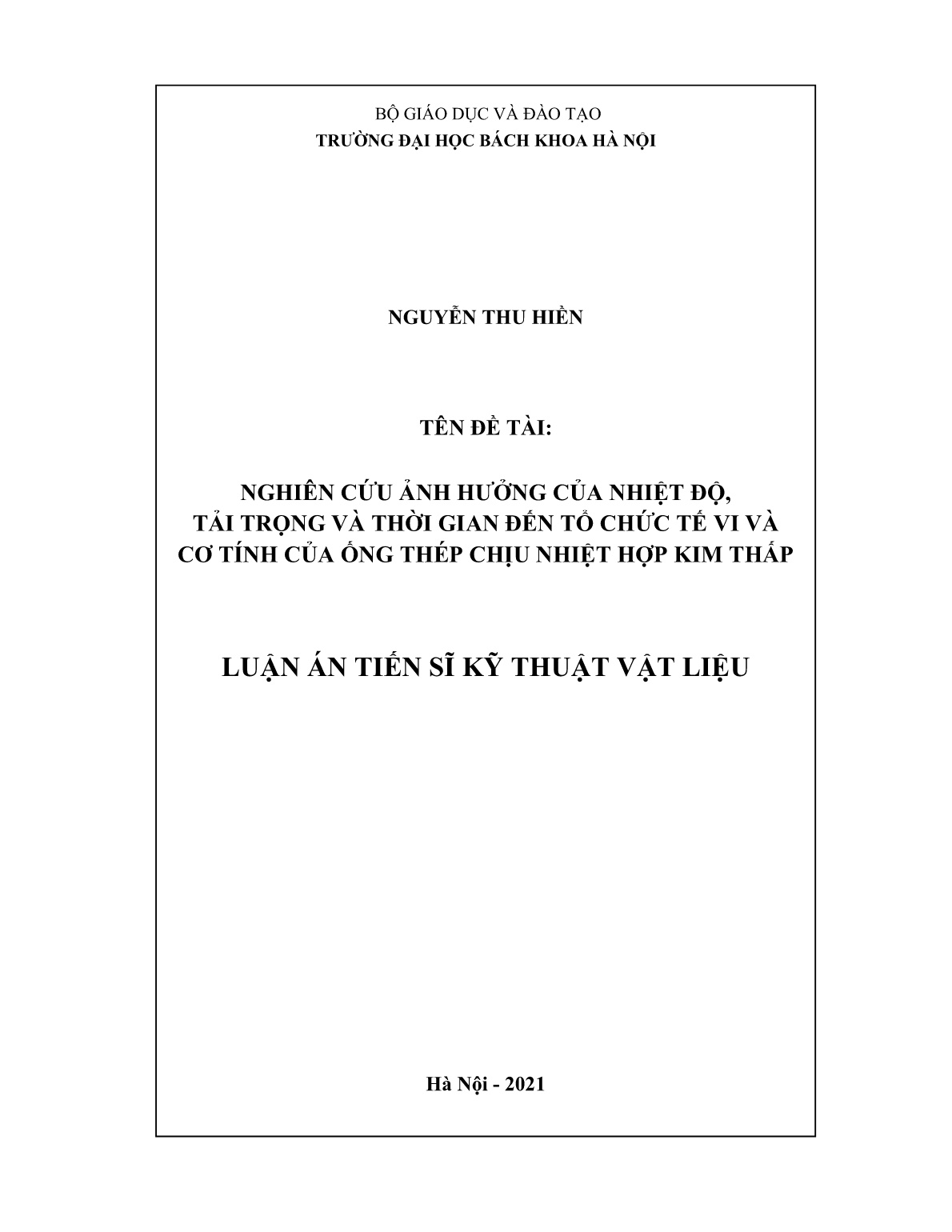
Trang 1
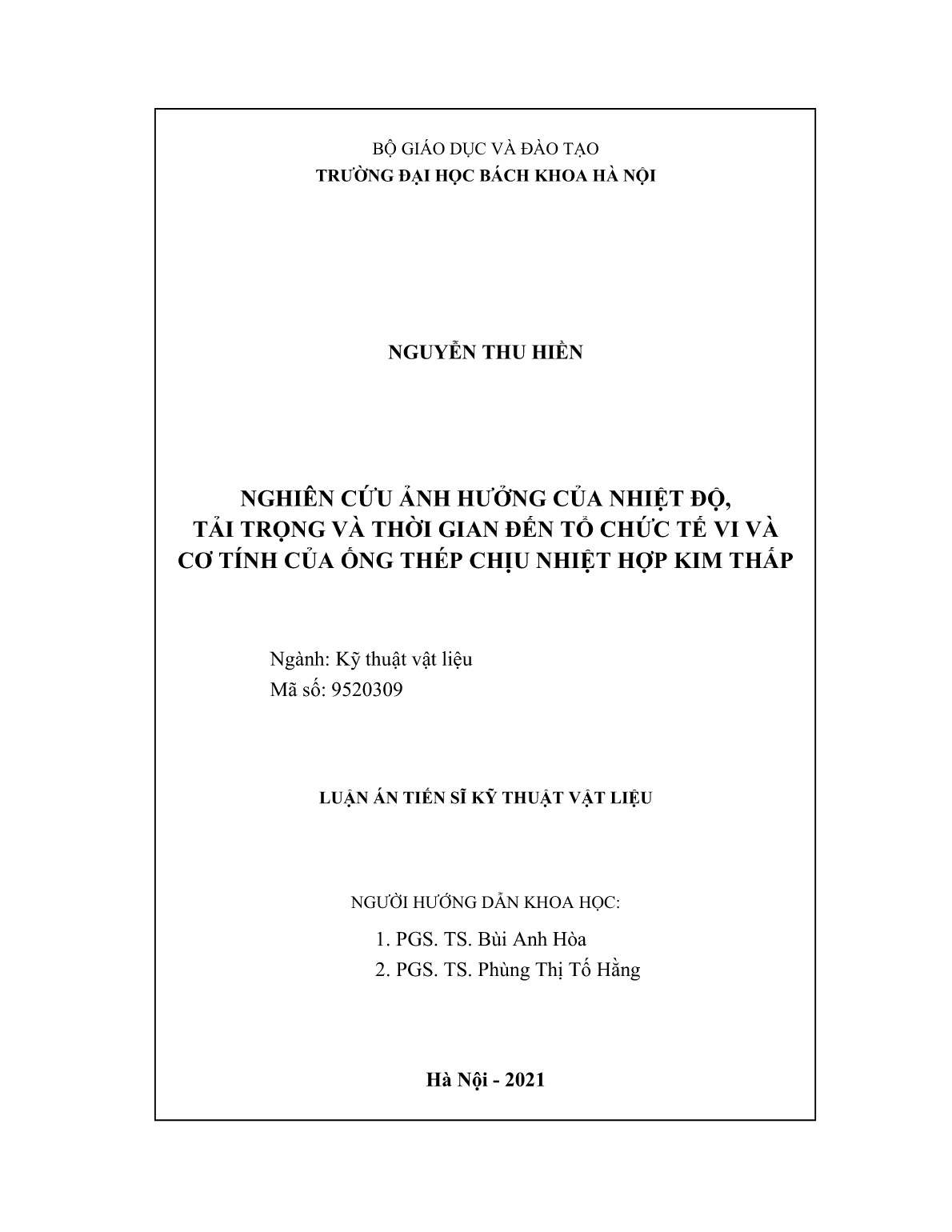
Trang 2
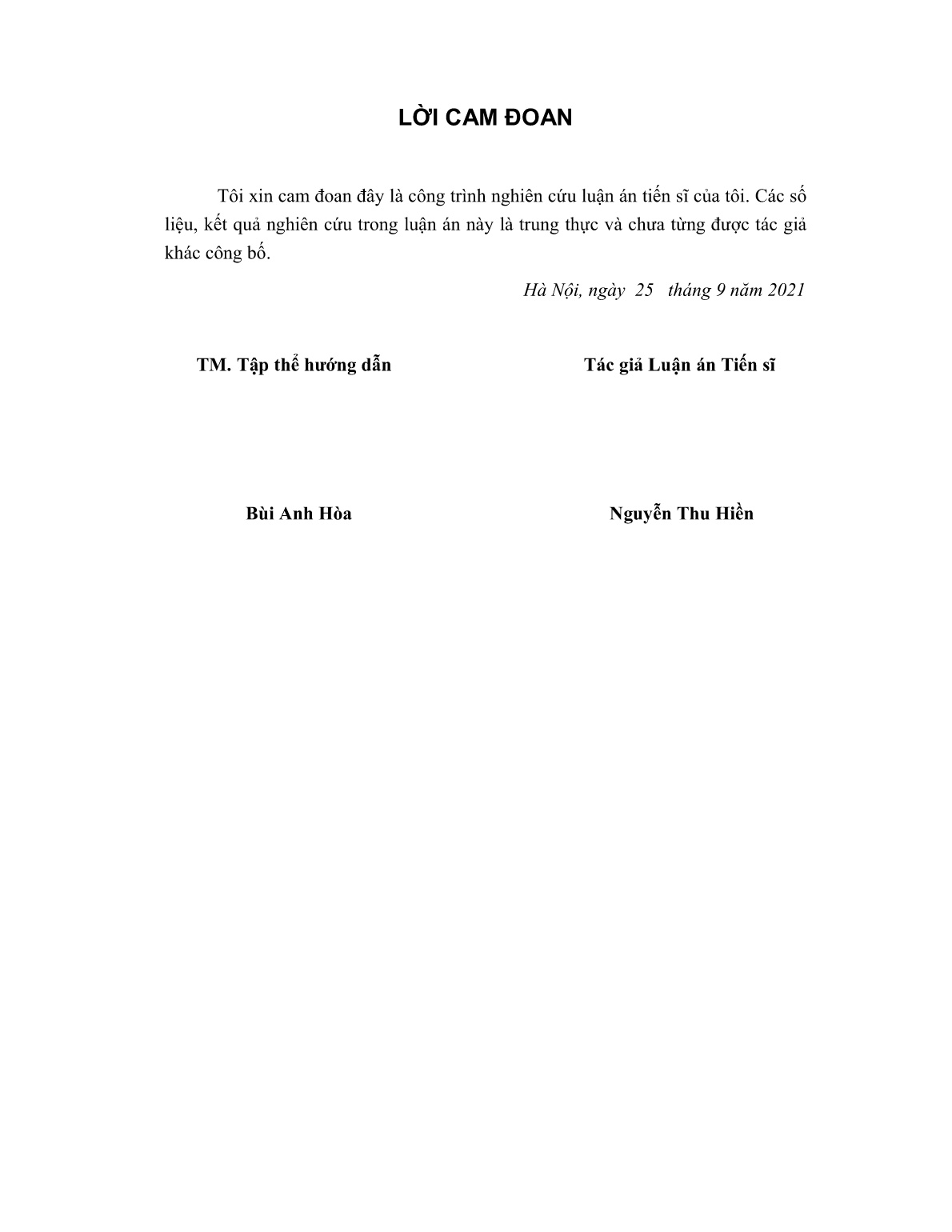
Trang 3
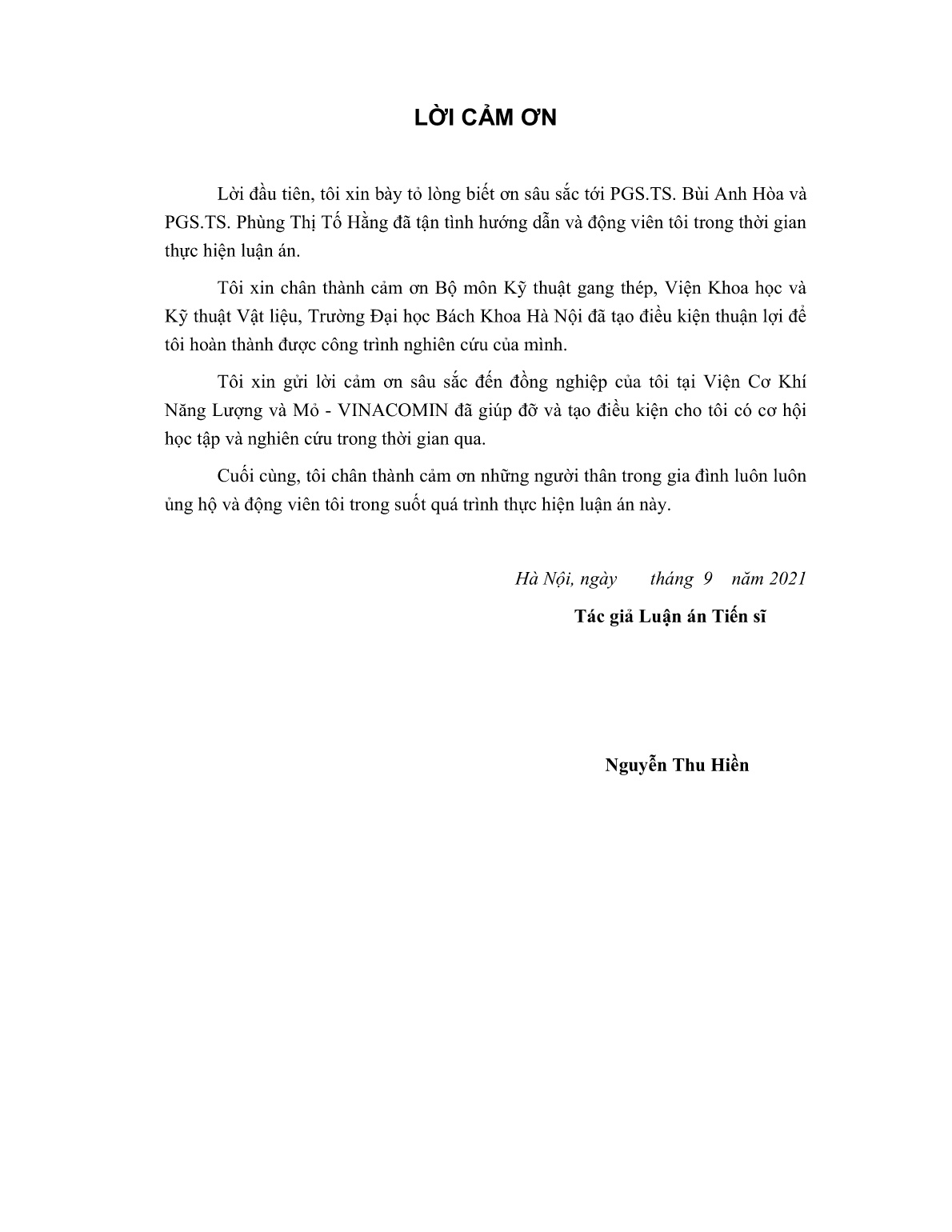
Trang 4

Trang 5
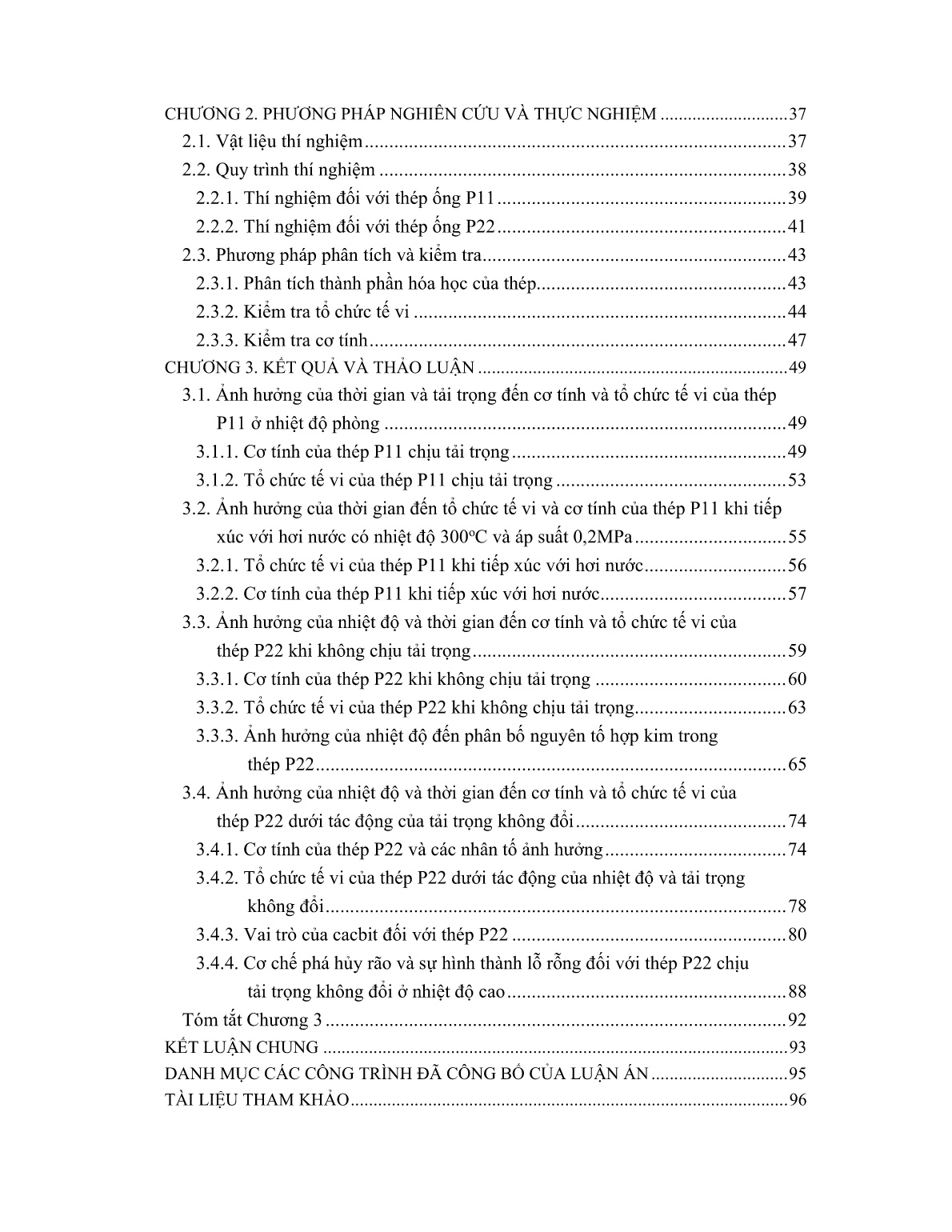
Trang 6
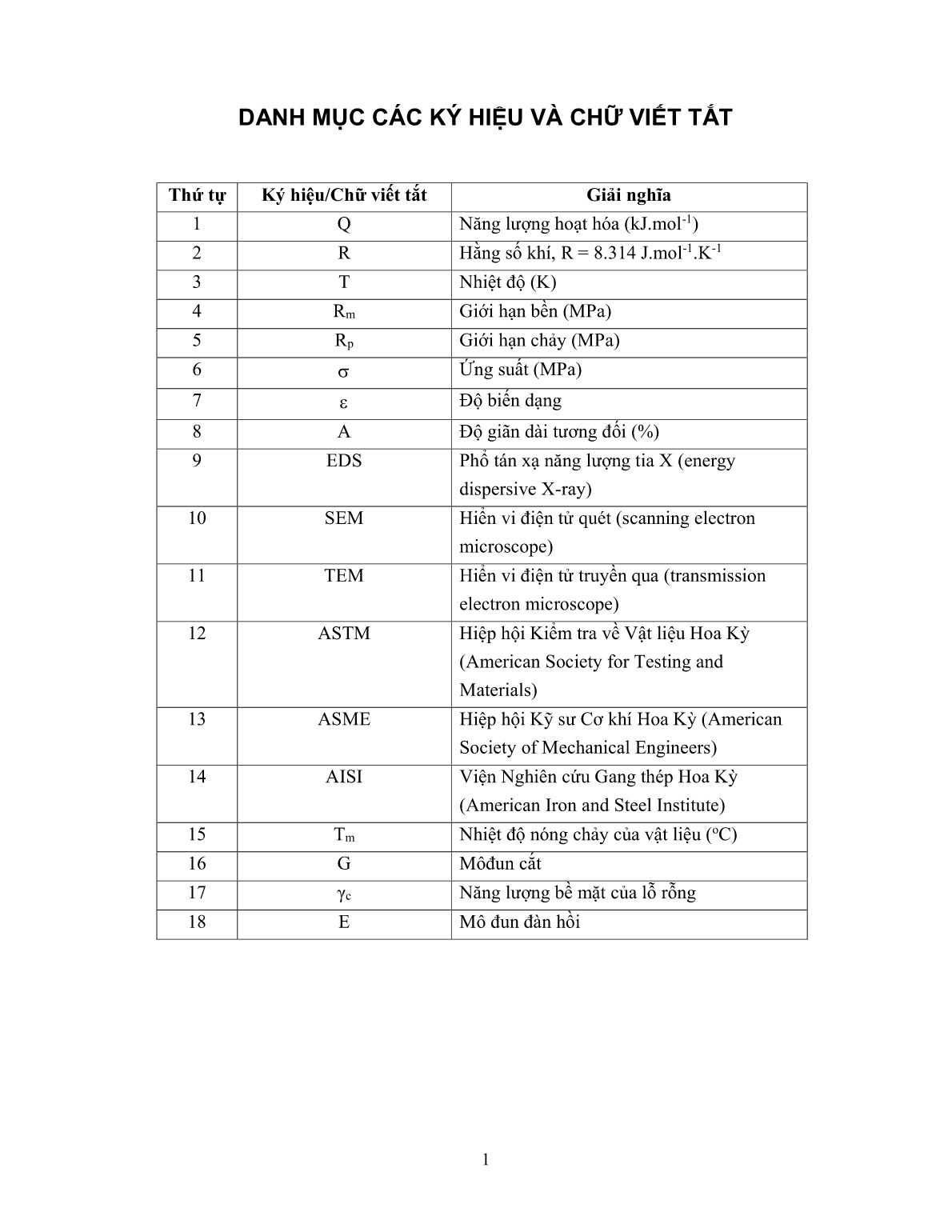
Trang 7
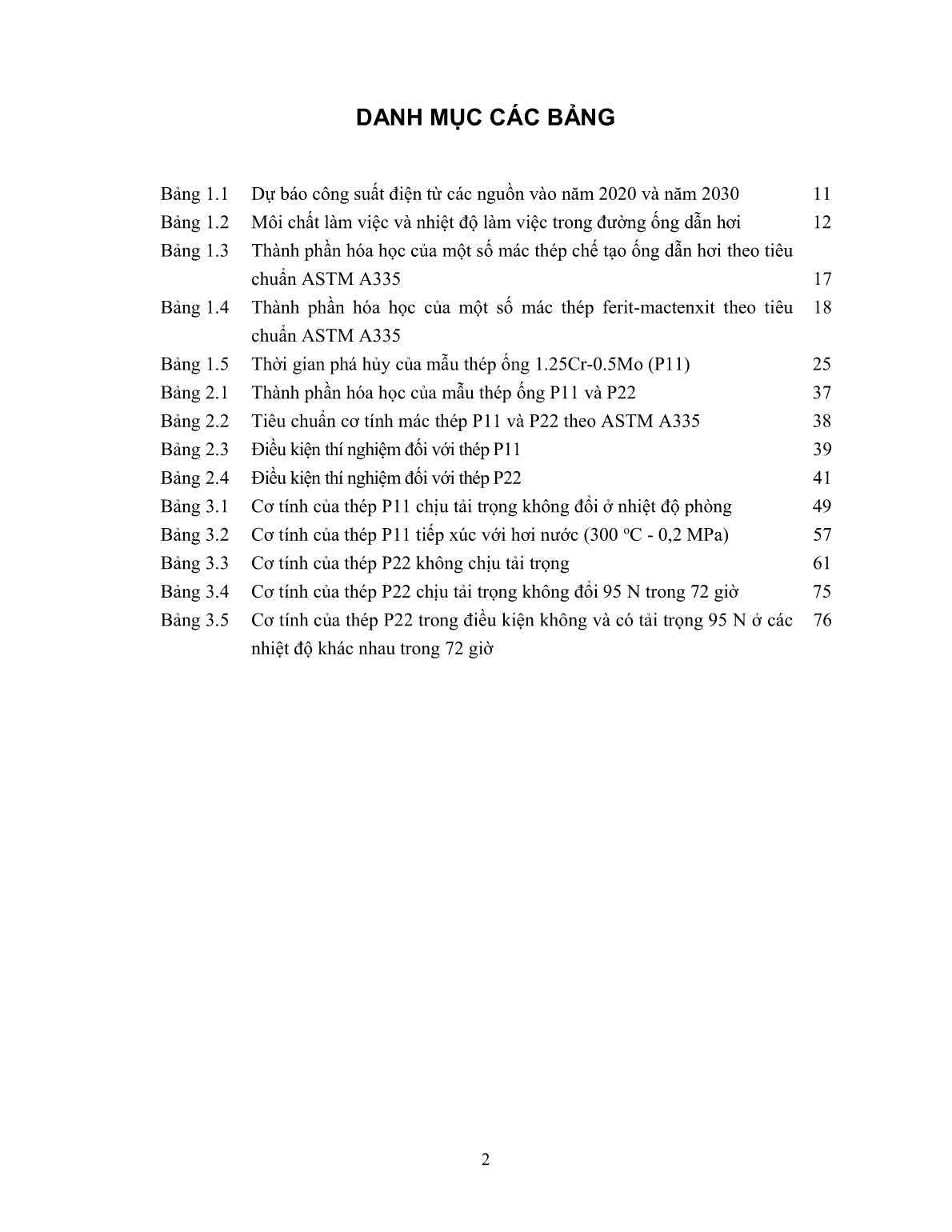
Trang 8
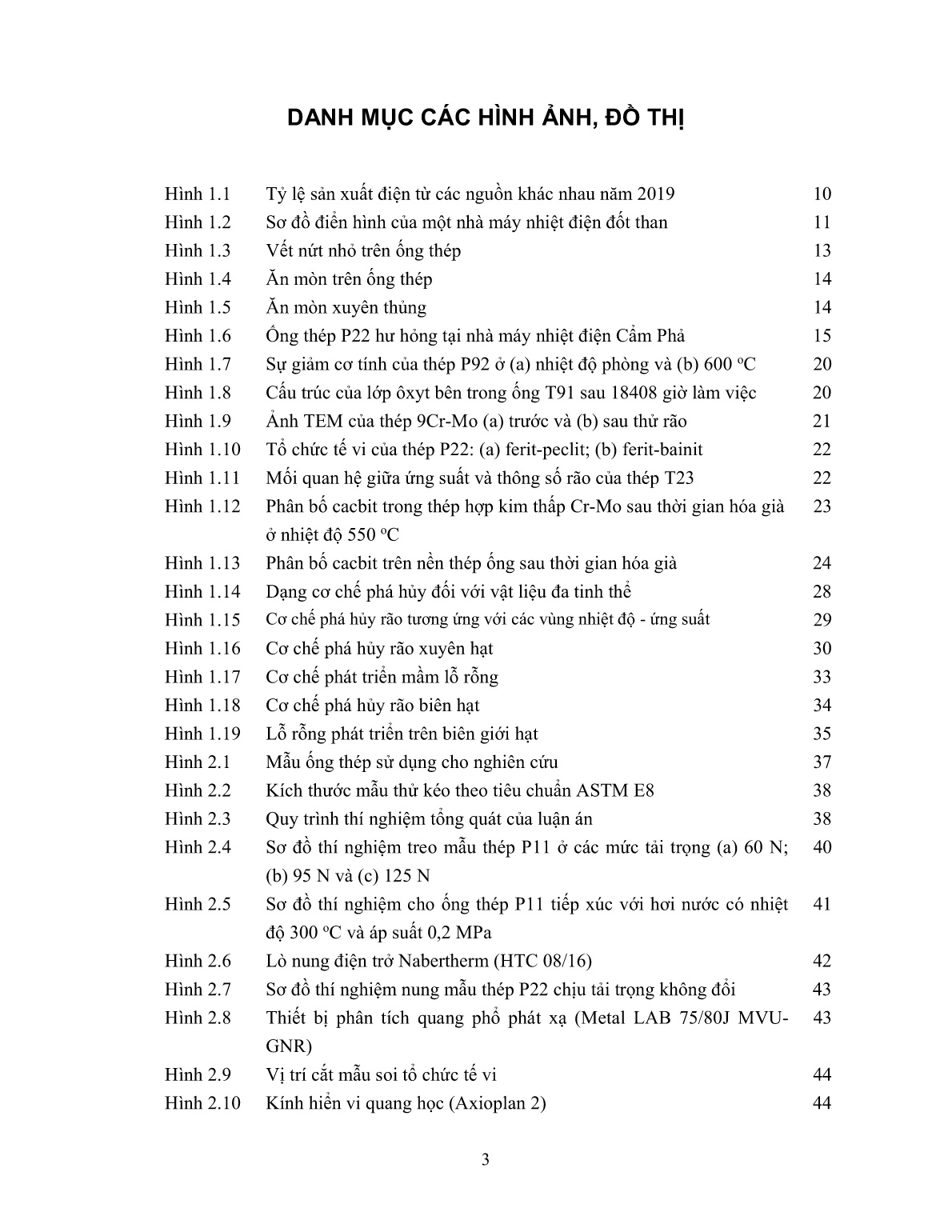
Trang 9
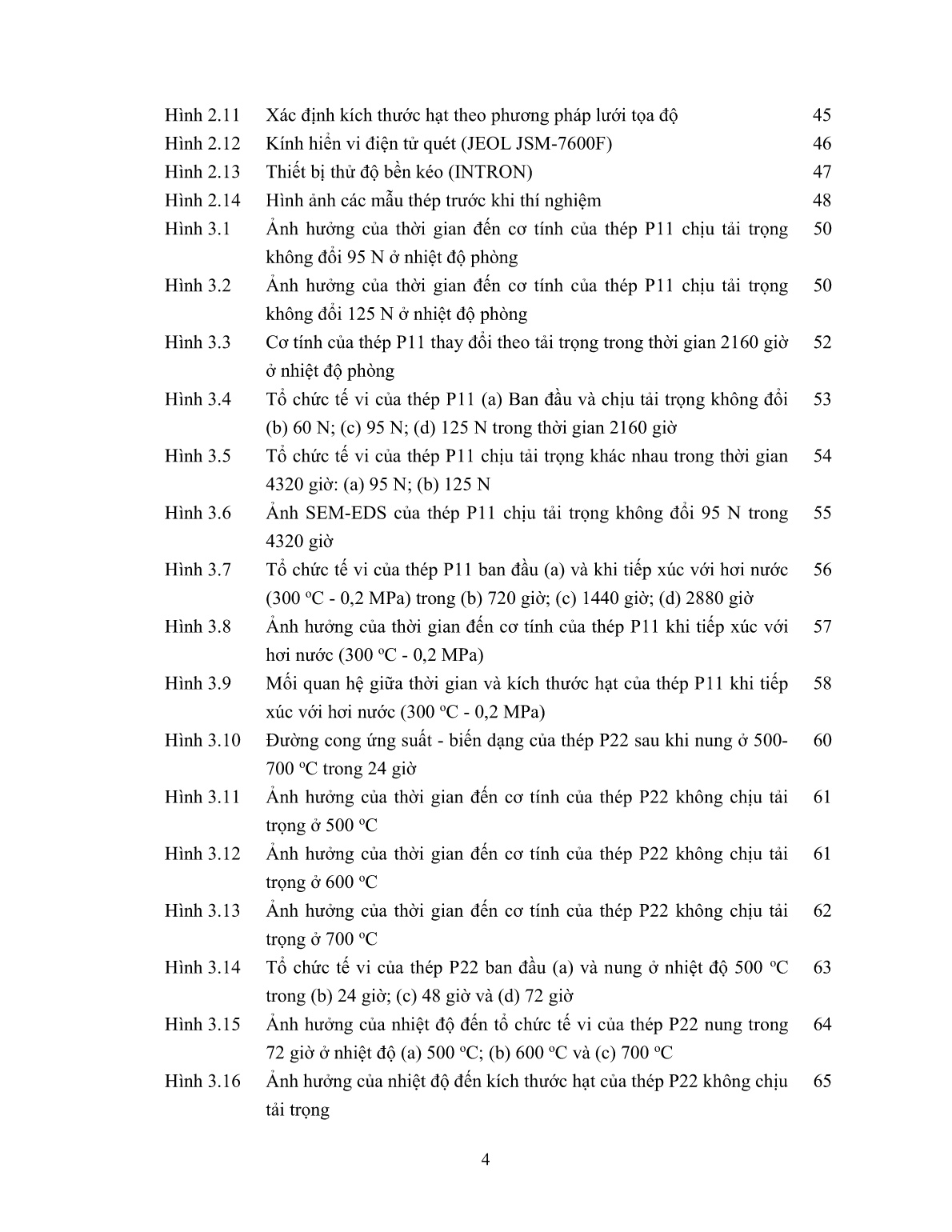
Trang 10
Tải về để xem bản đầy đủ
Bạn đang xem 10 trang mẫu của tài liệu "Luận án Nghiên cứu ảnh hưởng của nhiệt độ, tải trọng và thời gian đến tổ chức tế vi và cơ tính của ống thép chịu nhiệt hợp kim thấp", để tải tài liệu gốc về máy hãy click vào nút Download ở trên.
Tóm tắt nội dung tài liệu: Luận án Nghiên cứu ảnh hưởng của nhiệt độ, tải trọng và thời gian đến tổ chức tế vi và cơ tính của ống thép chịu nhiệt hợp kim thấp
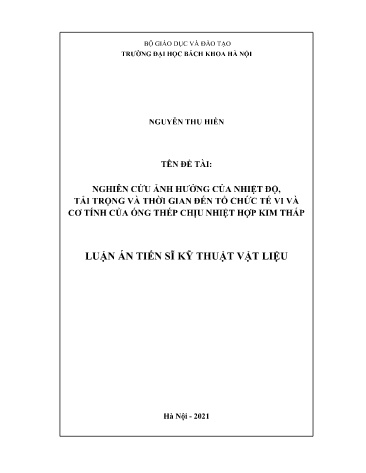
nh lệch trượt. Do đó, sự phát triển sẽ bị hạn chế bởi nguồn lệch sẵn có. Khi đó, lỗ rỗng phát triển có sự kiểm soát. 1.6.2.4. Nguyên nhân dẫn đến phá hủy 1) Phá hủy do biến dạng: Dưới tác dụng của ứng suất, sự phát triển lỗ rỗng sẽ đủ nhanh so với tốc độ rão, do đó, hạn chế tốc độ phát triển sẽ luôn chiếm ưu thế. Hạt thứ cấp được đánh giá có vai trò quan trọng trong việc kiểm soát tốc độ biến dạng rão trong vùng rão thứ ba, do đó, xác định được thời gian rão. Các hạt thứ cấp có thể hình thành bằng các quá trình xử lý nhiệt, cơ chế gây ra biến dạng dường như nhanh hơn. 2) Phá hủy do hoạt nhiệt gây ra: Phá hủy do nhiệt gây ra có thể xảy ra trong một số vật liệu bằng cách làm tăng kích thước phần thể tích không đổi của các hạt hoặc sự hòa tan của các hạt tiết ra mà tăng độ bền rão cho vật liệu. Hạt với kích thước lớn hơn là nguyên nhân dẫn đến tăng tỷ lệ rão trong quá trình biến dạng rão và dẫn đến phá hủy do rão trong vật liệu. 3) Phá hủy do môi trường gây ra: Đặc điểm phân biệt của phá hủy do môi trường gây ra là tỷ lệ hư hỏng tỷ lệ nghịch với kích thước của cấu tử. Loại phá hủy này có thể do quá trình ôxy hóa hoặc môi trường ăn mòn. Điều này dẫn đến vết nứt và tiếp xúc với vật liệu mới để ăn mòn thêm dẫn đến giảm thời gian của rão. 36 Tóm tắt Chương 1: Thép ống chịu nhiệt đã xuất hiện một số hư hỏng trong quá trình sử dụng tại các nhà máy nhiệt điện của Việt Nam. Thực tế cho thấy cần xem xét ảnh hưởng của thông số như áp suất, nhiệt độ và thời gian đến tính chất của các ống thép. Trên cơ sở đó, có thể tránh được sự cố gây nguy hiểm đến tính mạng con người và các hư hỏng của thiết bị, cũng như vận hành hiệu quả nhà máy điện hoặc chủ động có kế hoạch sửa chữa, thay thế kịp thời. Nghiên cứu về thép ống chịu nhiệt hợp kim thấp (P11 và P22) đã được tiến hành trên thế giới bằng phương pháp kiểm tra tổ chức tế vi và cơ tính của các ống thép sau một thời gian dài làm việc. Nguyên nhân gây ra sự suy giảm cơ tính của ống thép được cho là có liên quan đến cơ chế chảy rão của vật liệu được biểu hiện thông qua những biến đổi của tổ chức tế vi. Ở Việt Nam, vẫn chưa có nghiên cứu về hai mác thép này mặc dù được sử dụng với số lượng rất lớn trong các nhà máy nhiệt điện. Dựa trên thực tế nghiên cứu trong nước và trên thế giới chưa có nghiên cứu về thép P11 và P22 trong khoảng thời gian làm việc ban đầu, luận án tập trung nghiên cứu ảnh hưởng của các thông số như nhiệt độ, tải trọng và thời gian đến tổ chức tế vi và cơ tính của thép ống chưa sử dụng (mác P11 và P22). Đây có thể là khởi nguồn cho các sự cố xảy ra với thép ống trong quá trình làm việc lâu dài. 37 40 mm CHƯƠNG 2. PHƯƠNG PHÁP NGHIÊN CỨU VÀ THỰC NGHIỆM 2.1. Vật liệu thí nghiệm Ống thép P11 và P22 sử dụng trong nghiên cứu này được sản xuất theo công nghệ cán ống nóng không hàn (Seamless pipe), tiếp theo là ủ ở nhiệt độ 700-800 oC và làm nguội ngoài không khí. Hình 2.1 là ảnh ống thép dùng cho nghiên cứu. Đây là loại chưa qua sử dụng, được dùng để chế tạo các bộ phận ống dẫn hơi trong nhà máy nhiệt điện ở Việt Nam. Hai loại ống thép có kích thước như sau: - Đường kính trong: 30 mm; - Đường kính ngoài: 40 mm; - Chiều dày thành ống: 5 mm; Hình 2.1 Mẫu ống thép sử dụng cho nghiên cứu Thành phần hóa học của các mẫu thép ống được phân tích bằng máy quang phổ phát xạ và được cho trong bảng 2.1. Kết quả cho thấy thành phần hóa học của thép phù hợp tiêu chuẩn quy định đối với mác thép P11 và P22. Bảng 2.1 Thành phần hóa học của mẫu thép P11 và P22 Nguyên tố C Si Cr Mn Mo P S Mẫu thép P11 Thành phần (% k.l) 0,109 0,364 1,065 0,438 0,487 0,013 0,01 Mẫu thép P22 Thành phần (% k.l) 0,090 0,230 2,270 0,470 0,890 0,005 0,015 38 Tiêu chuẩn về cơ tính của thép ống P11 và P22 được cho trong bảng 2.2 theo ASTM A335. Thép đạt tiêu chuẩn sẽ được sử dụng chế tạo ống dẫn hơi trong các nhà máy nhiệt điện. Bảng 2.2 Tiêu chuẩn cơ tính mác thép P11 và P22 theo ASTM A335 Tiêu chuẩn cơ tính của thép P11 Rm (MPa) Rp (MPa) A (%) 415 205 30 Tiêu chuẩn cơ tính của thép P22 Rm (MPa) Rp (MPa) A (%) 415 205 30 2.2. Quy trình thí nghiệm Mẫu ống thép P11 và P22 được làm sạch các chất bẩn như các vết gỉ, bụi,... bằng giấy nhám. Sau đó, sử dụng máy cắt dây bằng tia lửa điện để chế tạo các mẫu thử kéo có chiều dày 1,5 mm theo tiêu chuẩn ASTM E8, như hình 2.2. Hình 2.2 Kích thước mẫu thử kéo theo tiêu chuẩn ASTM E8 (đơn vị: mm) Hình 2.3 Quy trình thí nghiệm tổng quát của luận án Đặt trong điều kiện thí nghiệm xác định Kiểm tra, đánh giá Kiểm tra cơ tính Soi tổ chức tế vi Mẫu thử kéo 39 Trong luận án này, quy trình thí nghiệm tổng quát được mô tả như trong hình 2.3. Trong nhà máy nhiệt điện, ống thép P11 hoặc P22 phải chịu tác động của áp suất lên thành ống tới 20 MPa ở nhiệt độ cao nhất đến 600 oC. Ở Việt Nam, ống dẫn hơi loại này được sử dụng trong điều kiện làm việc thay đổi ở nhiệt độ 300-500 oC với áp suất hơi thấp hơn các nhà máy điện trên thế giới. Đây chính là căn cứ để lựa chọn nhiệt độ và ứng suất cho các thí nghiệm trong luận án này. Ứng suất kéo được lựa chọn với 3 giá trị 6,45; 9,68 và 12,9 MPa. Với tiết diện ngang của mẫu thử cơ tính như trong hình 2.2, tương ứng với tải trọng đặt lên mẫu là 65, 95 và 125 N. Nhiệt độ thí nghiệm được chọn ở nhiệt độ phòng và ở nhiệt độ cao trong phạm vi 500-700 oC; ngoài ra, có một số thí nghiệm được thực hiện ở nhiệt độ 300-500 oC. Riêng đối với thí nghiệm sử dụng hơi nước, do hạn chế về mặt thiết bị nên cố định nhiệt độ là 300 oC và áp suất hơi nước là 0,2 MPa. Sau thời gian đặt mẫu trong các điều kiện (nhiệt độ, tải trọng) xác định, tiến hành các nghiên cứu tiếp theo như: kiểm tra cơ tính và soi tổ chức tế vi. 2.2.1. Thí nghiệm đối với thép ống P11 Đối với mẫu thép P11, tiến hành hai loại thí nghiệm nhằm nghiên cứu ảnh hưởng của các thông số: thời gian và tải trọng (ở điều kiện nhiệt độ phòng); và thời gian (ở điều kiện tiếp xúc với hơi nước có nhiệt độ 300 oC và áp suất 0,2 MPa) đến tổ chức tế vi và cơ tính của thép (bảng 2.3). Bảng 2.3 Điều kiện thí nghiệm đối với thép P11 Nhiệt độ (oC) Tải trọng (N) Thời gian (giờ) Chịu tải trọng không đổi ở nhiệt độ phòng 25 60 2160 95 4320 125 4320 Tiếp xúc với hơi nước ở nhiệt độ cao 300 0,2 MPa (Áp suất) 720 1440 2880 2.2.1.1. Nghiên cứu ảnh hưởng của thời gian và tải trọng ở nhiệt độ phòng Các mẫu thử kéo được treo ở nhiệt độ phòng như trong sơ đồ hình 2.4. Tải trọng được đặt lên mẫu lần lượt là 60, 95 và 125 N. Trong đó, thời gian treo mẫu tại mỗi tải trọng lần lượt là 2160 (tương đương 90 ngày) và 4320 giờ (tương đương 180 ngày). Sau thời gian xác định, dỡ bỏ tải trọng và chuẩn bị mẫu cho các nghiên cứu tiếp theo về kiểm tra cơ tính và soi tổ chức tế vi. 40 Hình 2.4 Sơ đồ thí nghiệm treo mẫu thép P11 ở các mức tải trọng (a) 60 N; (b) 95 N và (c) 125 N 2.2.1.2. Nghiên cứu ảnh hưởng của thời gian tiếp xúc với hơi nước có nhiệt độ và áp suất không thay đổi Trong thí nghiệm này, các ống thép P11 chưa qua sử dụng được lắp trực tiếp vào hệ thống dẫn hơi nước như trong hình 2.5. Hơi nước được sinh ra từ một nồi hơi và qua hệ thống ống dẫn để chạy qua đoạn ống thép P11. Nhiệt độ của hơi nước duy trì ở 300 oC và áp suất 0,2 MPa trong suốt thời gian thí nghiệm. Áp suất của hơi nước được đo bằng áp suất kế và nhiệt độ hơi nước được đo bằng nhiệt kế. Sau khoảng thời gian nhất định (720 giờ - tương đương 30 ngày, 1440 giờ - tương đương 60 ngày và 2880 giờ - tương đương 120 ngày), mẫu ống thép P11 được tháo ra và đem đi chuẩn bị mẫu thử cơ tính (như trong hình 2.2) và mẫu soi tổ chức tế vi. 41 Hình 2.5 Sơ đồ thí nghiệm cho ống thép P11 tiếp xúc với hơi nước có nhiệt độ 300 oC và áp suất 0,2 MPa 2.2.2. Thí nghiệm đối với thép ống P22 Đối với mẫu thép P22, tiến hành hai loại thí nghiệm nhằm nghiên cứu ảnh hưởng của nhiệt độ và thời gian đến tổ chức tế vi và cơ tính của thép khi không và có chịu tác động của tải trọng (bảng 2.4). Bảng 2.4 Điều kiện thí nghiệm đối với thép P22 Nhiệt độ (oC) Tải trọng (N) Thời gian (giờ) Không chịu tải trọng 500 0 24 600 48 700 72 Chịu tải trọng không đổi ở nhiệt độ cao 300 95 72 400 500 600 700 95 24 48 125 48 72 42 2.2.2.1. Nghiên cứu ảnh hưởng của nhiệt độ và thời gian khi thép không chịu tải trọng Hình 2.6 Lò nung điện trở Nabertherm (HTC 08/16) Các mẫu thử kéo được nung trong lò buồng điện trở (Nabertherm, HTC 08/16) - Hình 2.6. Để giảm hiện tượng ôxy hóa bề mặt, các mẫu thép được cho vào trong một khay đựng và phủ kín bằng ôxyt nhôm. Tốc độ nâng nhiệt được chọn là 10 oC/phút, giữ nhiệt ở các nhiệt độ khác nhau (500, 600 và 700 °C) - tương tự với nhiệt độ làm việc của thép ống dẫn hơi tại các nhà máy nhiệt điện. Sau thời gian giữ nhiệt là 24, 48 và 72 giờ, các mẫu thép được làm nguội cùng lò và chuẩn bị cho các nghiên cứu tiếp theo về kiểm tra cơ tính và soi tổ chức tế vi. 2.2.2.2. Nghiên cứu ảnh hưởng của nhiệt độ và thời gian khi thép chịu tải trọng không đổi Mẫu thử kéo được treo và nung trong lò điện trở kiểu ống đứng (Nabertherm), như trong hình 2.7. Tải trọng đặt lên mẫu thép lần lượt là 95 và 125 N. Tốc độ nâng nhiệt được chọn là 10 oC/phút, giữ nhiệt ở các nhiệt độ khác nhau (300, 400, 500, 600 và 700 °C) với thời gian 72 giờ. Ở nhiệt độ 700 oC, thời gian giữ nhiệt được thay đổi ở các mức 24, 48 và 72 giờ. Sau thời gian giữ nhiệt đã chọn, các mẫu thép được làm nguội cùng lò và bỏ tải trọng để chuẩn bị cho các nghiên cứu tiếp theo về kiểm tra cơ tính và soi tổ chức tế vi. 43 Hình 2.7 Sơ đồ thí nghiệm nung mẫu thép P22 chịu tải trọng không đổi 2.3. Phương pháp phân tích và kiểm tra 2.3.1. Phân tích thành phần hóa học của thép Hình 2.8 Thiết bị phân tích quang phổ phát xạ (Metal LAB 75/80J MVU-GNR) Thành phần hóa học của mẫu ống thép P11 và P22 được phân tích bằng thiết bị quang phổ phát xạ (Metal LAB 75/80J MVU-GNR) của Viện Cơ khí Năng lượng 44 và Mỏ - VINACOMIN (hình 2.8). Để đảm bảo độ chính xác, bề mặt mẫu thép được mài nhẵn bằng máy mài và làm sạch. Máy có độ chính xác cao, khả năng phân tích đến 10-4 % khối lượng các nguyên tố thường có trong thép như C, Mn, Si, Cr, S, P và một số nguyên tố khác. Sau khi hiệu chỉnh máy, thực hiện thao tác phân tích mẫu; kết quả phân tích là giá trị trung bình của 3 lần đo. 2.3.2. Kiểm tra tổ chức tế vi Để tiến hành soi tổ chức tế vi, các mẫu thép được cắt ở vị trí như trong hình 2.9. Sau đó, mài mẫu với giấy nhám với các cấp độ khác nhau. Cuối cùng là đánh bóng mẫu và tẩm thực bằng dung dịch có chứa 5 ml HCl, 1 gam axit picric, etanol 100 ml (95 %) hoặc metanol (95 %). Hình 2.9 Vị trí cắt mẫu soi tổ chức tế vi Hình 2.10 Kính hiển vi quang học (Axioplan 2) Vị trí quan sát tổ chức tế vi 45 Các mẫu thép sau khi trải qua các bước chuẩn bị mẫu, tiến hành kiểm tra tổ chức tế vi bằng kính hiển vi quang học (Axioplan 2) tại Viện Cơ khí Năng lượng và Mỏ - VINACOMIN (hình 2.10). Nguyên lý làm việc của kính hiển vi quang học là dựa vào nguyên lý phản xạ ánh sáng để quan sát hình ảnh tổ chức tế vi của mẫu nhờ một hệ thống các thấu kính (thị kính và vật kính) với độ phóng đại lên đến 1000 lần. Một kính hiển vi quang học có nhiều bộ phận như: nguồn sáng, giá đặt mẫu, vật kính (có thể là một thấu kính hoặc một hệ thấu kính, là bộ phận chính tạo nên sự phóng đại), thị kính và thiết bị ghi nhận hình ảnh. Hình 2.11 Xác định kích thước hạt theo phương pháp lưới tọa độ Từ ảnh chụp hiển vi quang học, tiến hành tính toán kích thước hạt theo phương pháp lưới tọa độ như mô tả trong hình 2.11. Theo đó, kẻ các đường thẳng (dọc và ngang) trên ảnh tổ chức tế vi sao cho cắt các biên giới hạt. Kích thước hạt trung bình được tính toán theo công thức 2.1. d = (2.1) Trong đó: d - Kích thước hạt trung bình (µm); L - Chiều dài thực tế của ảnh tổ chức tế vi (µm); D - Chiều rộng thực tế của ảnh tổ chức tế vi; m - Số hạt mà đường kẻ dọc đã cắt biên giới hạt; n - Số hạt mà đường kẻ ngang đã cắt biên giới hạt. 46 Phân bố cacbit trong mẫu thép được quan sát bằng thiết bị hiển bị điện tử quét (SEM) kết hợp vi phân tích thành phần bằng phổ nguyên tố (EDS). Nguyên lý của phương pháp này là dựa vào tán xạ của chùm điện tử quét trên bề mặt mẫu để tạo ra hình ảnh có độ phân giải cao của bề mặt mẫu. SEM có khả năng tạo hình ảnh hai chiều của bề mặt mẫu với độ phân giải cao, có thể quan sát tổ chức tế vi đến kích thước vài nanomet, cao hơn rất nhiều so với kính hiển vi quang học có độ phân giải tốt nhất chỉ vào khoảng vài trăm nanomet. Ảnh chụp SEM cho kết quả về hình thái các pha tồn tại với độ phân giải cao. Hình 2.12 là thiết bị SEM-EDS (JEOL JSM- 7600F) của Trung tâm Đánh giá hư hỏng vật liệu (COMFA) được sử dụng trong luận án này. Hình 2.12 Kính hiển vi điện tử quét (JEOL JSM-7600F) Phương pháp phổ nguyên tố EDS (Energy Dispersive X-ray Spectroscopy) là một kỹ thuật dùng để phân tích thành phần hóa học của vật rắn. EDS thường được kết hợp trong SEM hoặc TEM. Khi chùm điện tử có năng lượng lớn được chiếu vào vật rắn, nó sẽ đâm xuyên sâu vào nguyên tử vật rắn và tương tác với các lớp điện tử bên trong của nguyên tử. Tương tác này dẫn đến sự phát xạ các tia X thứ cấp. Năng lượng, bước sóng của các tia X thứ cấp phát ra là đặc trưng cho nguyên tử số (Z) của các nguyên tử có trong chất rắn. Việc ghi nhận phổ tia X thứ cấp phát ra từ vật rắn sẽ cho thông tin về các nguyên tố hóa học có mặt trong mẫu đồng thời cho các thông tin về hàm lượng các nguyên tố này. Phân tích phổ nguyên tố EDS giúp xác 47 định thành phần nguyên tố trong phạm vi nhỏ, từ đó có thể dự đoán sơ bộ về thành phần các pha có trong vật liệu. Thông qua kỹ thuật này, có thể nhận xét được sự thay đổi về tổ chức tế vi của thép P11 và P22 dưới ảnh hưởng của các thông số như nhiệt độ, ứng suất và thời gian. 2.3.3. Kiểm tra cơ tính Cơ tính của các mẫu thép được xác định thông qua phương pháp thử kéo trên thiết bị thử độ bền kéo (INTRON) của Viện vật liệu xây dựng (hình 2.13). Hình 2.13 Thiết bị thử độ bền kéo Hình 2.14 là các mẫu trước khi thử kéo. Phương pháp thử kéo được thực hiện bằng cách tác động lực kéo lên hai đầu mẫu thử cho đến khi phá hủy mẫu. Dựa trên sự thay đổi của kích thước mẫu thử khi tăng lực kéo sẽ vẽ được đường cong ứng suất - biến dạng; và xác định được các thông số cơ tính chủ yếu: - Giới hạn bền kéo (Rm, MPa) là ứng suất tương ứng với lực lớn nhất; - Giới hạn chảy (Rp, MPa) là ứng suất tại điểm chảy của vật liệu kim loại khi xuất hiện biến dạng dẻo mà lực thử không tăng; - Độ giãn dài (A, %) là tỷ lệ của mức tăng chiều dài so với chiều dài ban đầu của mẫu thử. 48 Hình 2.14 Hình ảnh các mẫu thép trước khi thí nghiệm 49 CHƯƠNG 3. KẾT QUẢ VÀ THẢO LUẬN 3.1. Ảnh hưởng của thời gian và tải trọng đến cơ tính và tổ chức tế vi của thép P11 ở nhiệt độ phòng 3.1.1. Cơ tính của thép P11 chịu tải trọng Bảng 3.1 là kết quả kiểm tra cơ tính của thép P11 chịu tải trọng khác nhau ở nhiệt độ phòng sau thời gian 2160 và 4320 giờ. Bảng 3.1 Cơ tính của thép P11 chịu tải trọng không đổi ở nhiệt độ phòng Điều kiện thí nghiệm Cơ tính Tải trọng (N) Thời gian (giờ) Rm (MPa) Rp (MPa) A (%) Mẫu ban đầu 481 325 32 60 2160 488 378 31 95 2160 553 380 33 125 2160 605 402 33 95 4320 456 335 33 125 4320 446 340 33 3.3.1.1. Ảnh hưởng của thời gian chịu ứng suất kéo Kết quả sự thay đổi cơ tính của thép P11 theo thời gian chịu tải trọng ở nhiệt độ phòng được cho trong hình 3.1 và 3.2. Có thể thấy rằng, cơ tính của thép thay đổi khi tăng tải trọng tác động lên thép hoặc kéo dài thời gian khi thép chịu tải trọng không đổi. Khi tăng thời gian giữ tải trọng, ban đầu giới hạn bền và giới hạn chảy của thép tăng lên, trong khi độ giãn dài gần như không thay đổi. Cụ thể, khi tải trọng được giữ trong 2160 giờ thì giới hạn bền tăng từ 481 lên 553 MPa, giới hạn chảy tăng từ 325 lên 380 MPa đối với mức tải trọng là 95 N (hình 3.1). Thời gian chịu tải trọng tăng lên thì giới hạn bền và giới hạn chảy giảm. Cụ thể, khi tăng thời gian chịu tải trọng lên 4320 giờ, giới hạn bền giảm từ 553 xuống còn 456 MPa; tương ứng với hai giai đoạn hóa bền và thải bền. Ở mức tải trọng lớn hơn (125 N), quy luật thay đổi của giới hạn bền và giới hạn chảy cũng tương tự (hình 3.2). Tuy nhiên, kết quả cho thấy mức độ tăng bền và thải bền của các mẫu thép có xu hướng rõ rệt hơn khi đặt tải trọng cao hơn. Với tải trọng là 125 N, mức độ tăng giới hạn bền là 123 MPa (lớn hơn so với 72 MPa khi đặt tải trọng là 95 N). 50 Hình 3.1 Ảnh hưởng của thời gian đến cơ tính của thép P11 chịu tải trọng không đổi 95 N ở nhiệt độ phòng Hình 3.2 Ảnh hưởng của thời gian đến cơ tính của thép P11 chịu tải trọng không đổi 125 N ở nhiệt độ phòng 51 Sự hóa bền và thải bền một mẫu thép khi chịu tải (ở nhiệt độ phòng) trong thời gian dài là tuân theo đúng quy luật và được giải thích về lý thuyết như sau [52]: biến dạng dẻo trong thép (vật liệu đa tinh thể) đầu tiên được xem xét biến dạng trong một hạt (coi là đơn tinh thể) nói chung gồm ba giai đoạn với các đặc điểm hóa bền khác nhau. Trong giai đoạn đầu tiên, khi ứng suất vượt qua giá trị tới hạn, các lệch chuyển động trên khắp mặt trượt sơ cấp cho đến khi gặp các cản trở (chẳng hạn tương tác giữa các lệch, pha thứ 2), cần bổ sung thêm ứng suất (hoặc tiếp tục duy trì ứng suất) để lệch tiếp tục trượt được, đó là hóa bền biến dạng. Do mức độ hóa bền nhỏ và trượt chủ yếu trên mặt sơ cấp nên giai đoạn này gọi là trượt đơn giản. Giai đoạn tiếp theo, gọi là trượt phức tạp, khi ứng suất đủ lớn, các hệ trượt thứ cấp có thể hoạt động được. Tương tác giữa các lệch thuộc hệ sơ cấp và thứ cấp sẽ tạo ra vô số cản trở chuyển động của lệch, tới mức hầu như lệch bị dừng lại bên chướng ngại và các nguồn lệch có nguy cơ ngừng phát, vì thế cần tiếp tục tăng (hay duy trì) ứng suất để nguồn hoạt động tạo biến dạng, làm cho hóa bền biến dạng tăng hàng chục lần so với giai đoạn đầu, tạo ra cấu trúc lệch kiểu ô lưới và tường ngăn là những búi lệch với mật độ rất cao. Ở giai đoạn cuối, hóa bền biến dạng vẫn tiếp tục nhưng tốc độ giảm, bắt đầu xảy ra thải bền khi các lệch trái dấu gặp nhau và hủy lẫn nhau, hoặc khi lệch vượt qua các cản trở (chủ yếu nhờ trượt ngang) làm cho chướng ngại trở thành đoạn lưới vuông góc với mặt trượt. Trong khi đó các lệch cùng dấu bắt đầu sắp xếp lại trật tự, làm cho các phần tinh thể kề nhau bị quay hoặc nghiêng với nhau. Các quá trình này làm cho cấu trục ô lệch hoàn thiện hơn (tường ngăn ô có thể giảm mật độ lệch và trật tự hơn, bên trong các ô nghèo lệch). Sự thải bền này được gọi là hồi phục động học. Trong đa tinh thể, các hạt (coi là các đơn tinh thể với biến dạng khi có lực tác dụng như đã nêu trên) có định hướng khác nhau và biên giới giữa chúng là các cản trở của chuyển động của lệch. Để lệch có thể trượt trong toàn bộ đa tinh tinh thể, cần nhiều hệ trượt hoạt động, do vậy, ngay từ đầu trượt phức tạp đã xảy ra trong đa tinh thể với ứng suất cao hơn nhiều so với trượt đơn gian trong đơn tinh thể cùng kiểu mạng. Biên hạt chính là nơi mà các lệch trượt bị dừng lại, tạo thành một tập hơn với số lượng đáng kể tạo ra một trường ứng suất bổ sung cùng với ngoại lực, đủ để kích thích tạo lệch trong các hạt lân cận hoạt động. Cứ như vậy, quá trình biến dạng dẻo được thực hiện từ hạt này qua hạt khác. Quá trình này sẽ trở nên khó khăn nếu kích thước hạt càng nhỏ. Như vậy, với các mẫu chịu tải trọng khác nhau, mức độ hóa bền khác nhau. Mức độ hóa bền càng mạnh khi ứng suất tác dụng càng lớn và kéo dài, tạo điều kiện cho việc phát sinh và tăng cường hoạt động của lệch, tương ứng với sự tăng cơ tính 52 của các mẫu thép. Đồng thời sự hủy lẫn nhau của các lệch trái dấu, sự sắp xếp lại chúng trong các ô lệch trong giai đoạn tiếp theo đã tạo nên sự thải bền làm giảm cơ tính của các mẫu
File đính kèm:
luan_an_nghien_cuu_anh_huong_cua_nhiet_do_tai_trong_va_thoi.pdf
THÔNG TIN TÍNH MỚI LUẬN ÁN TIẾN SĨ (TIẾNG ANH).pdf
THÔNG TIN TÍNH MỚI LUẬN ÁN TIẾN SĨ (TIẾNG VIỆT).pdf
TÓM TẮT LUẬN ÁN TIẾN SĨ.pdf
TRÍCH YẾU LATS.pdf