Luận án Nghiên cứu công nghệ chế tạo vật liệu compozit nền al-ti cốt hạt Al₂O₃ in-situ
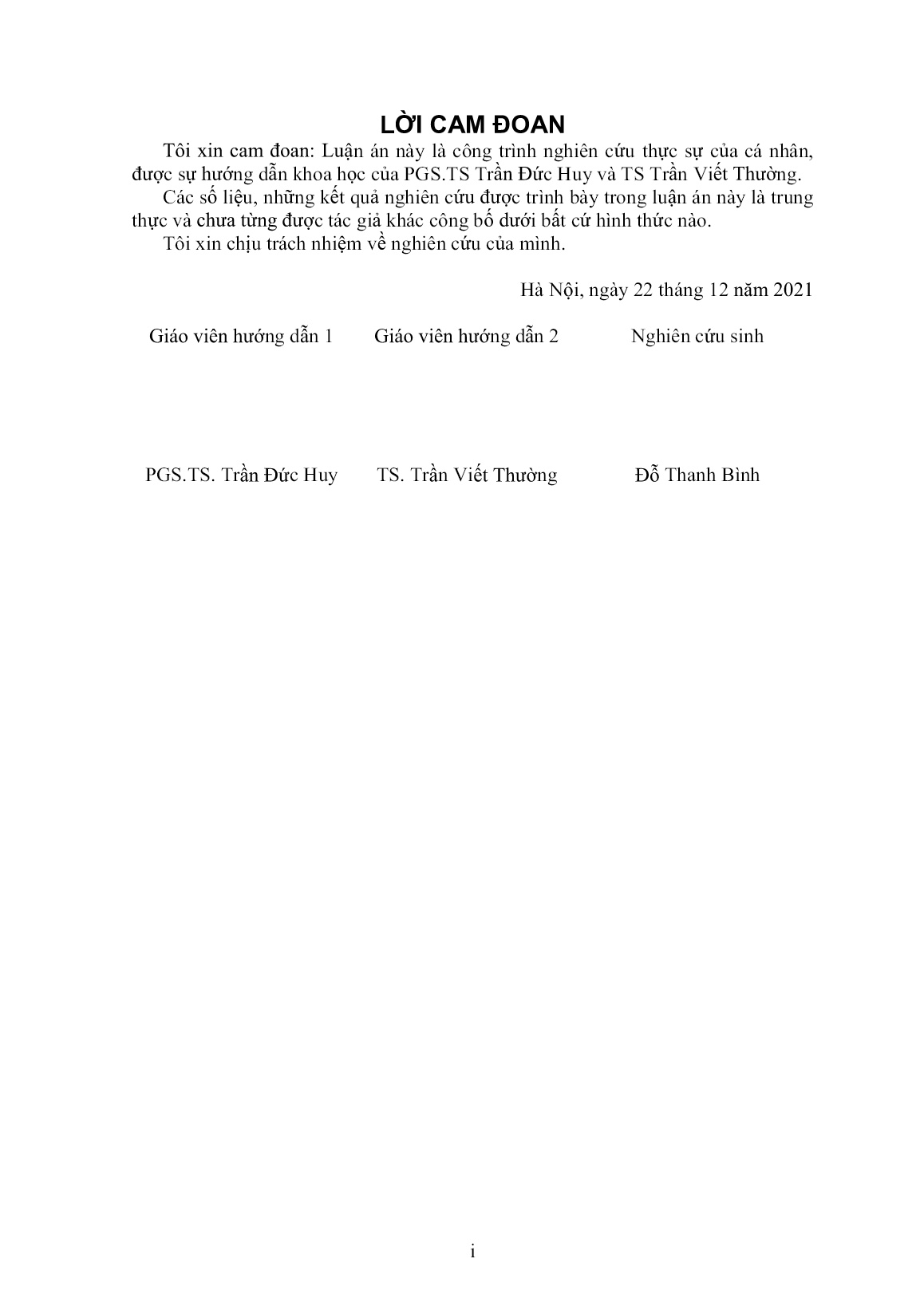
Trang 1
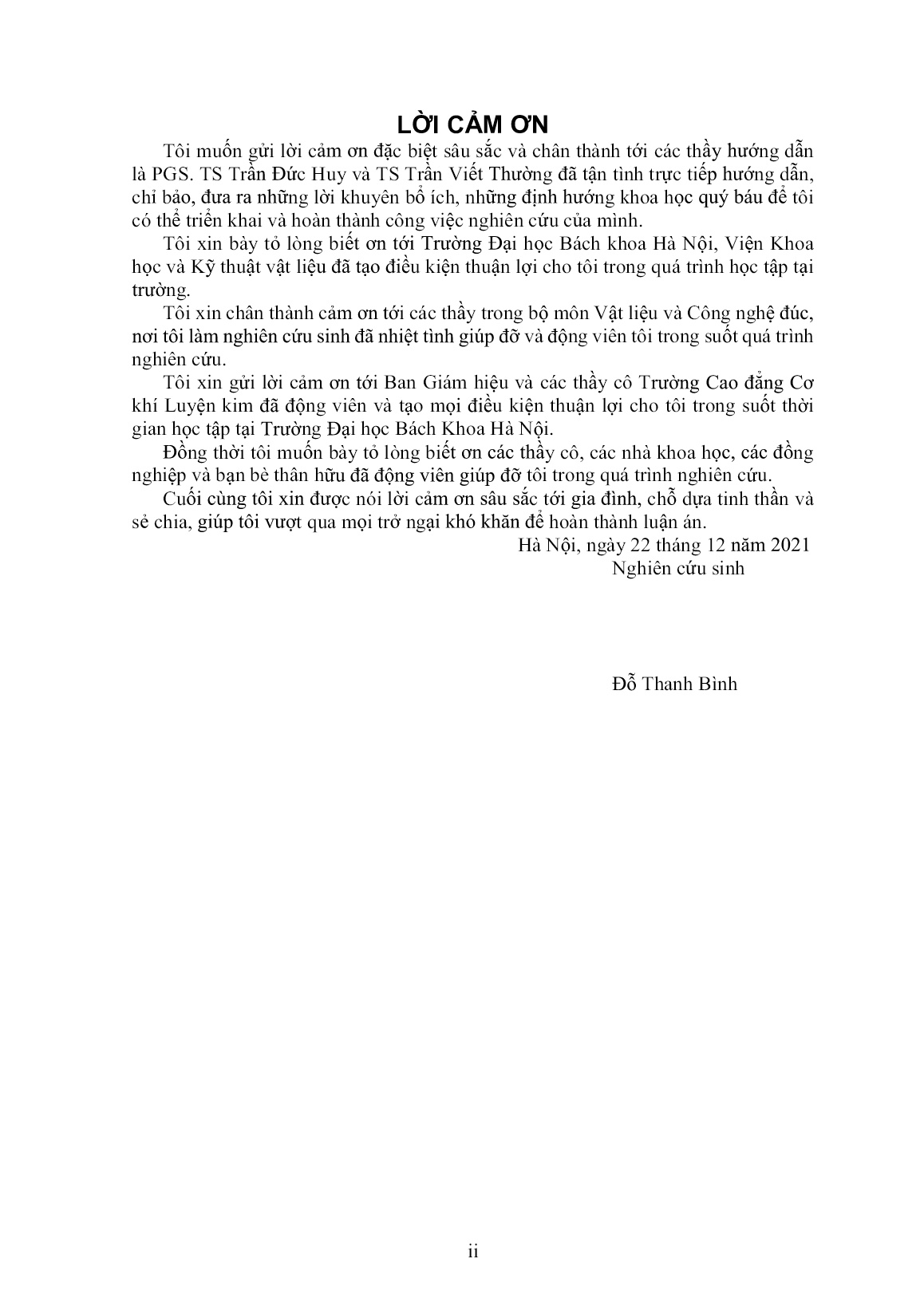
Trang 2
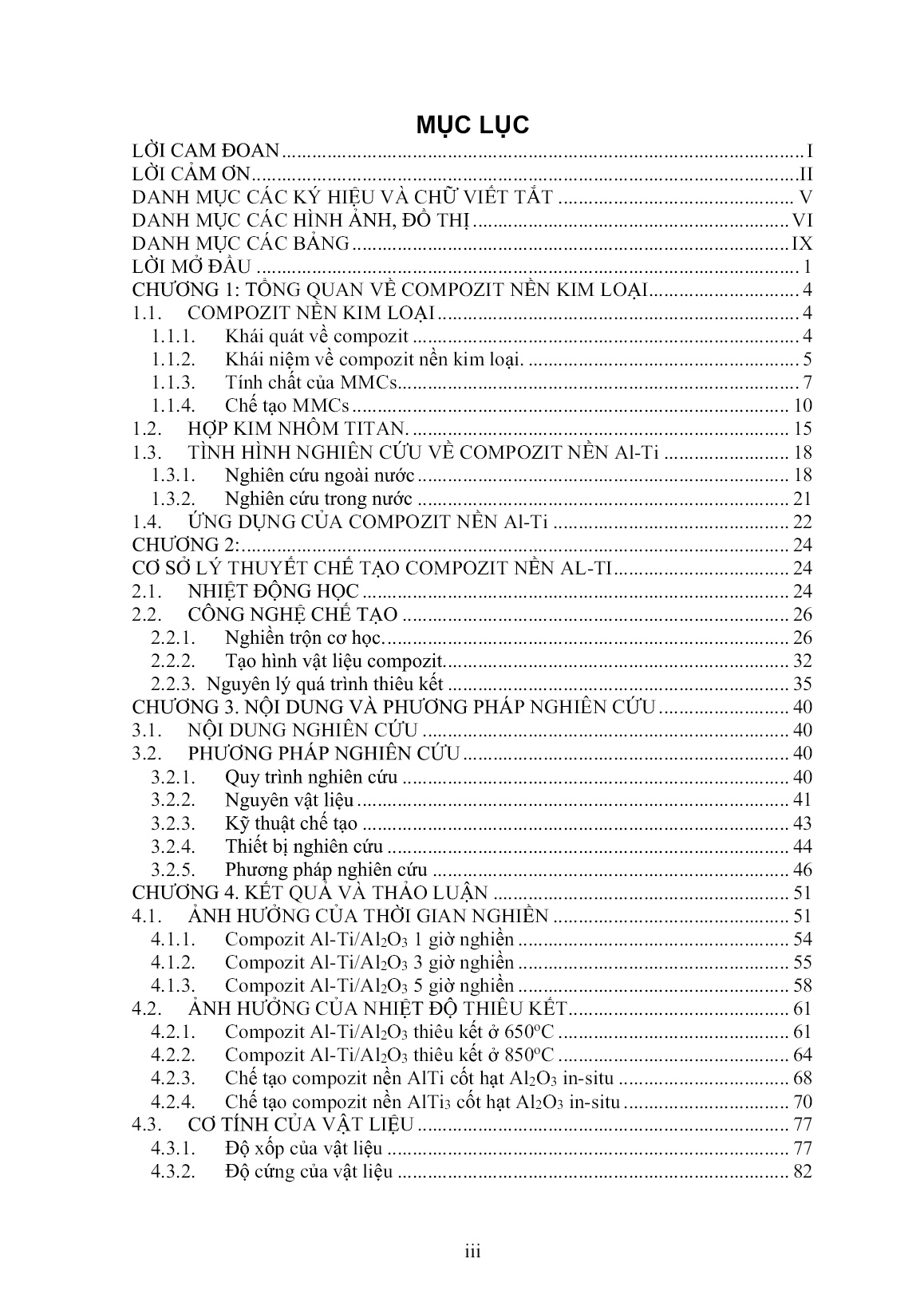
Trang 3
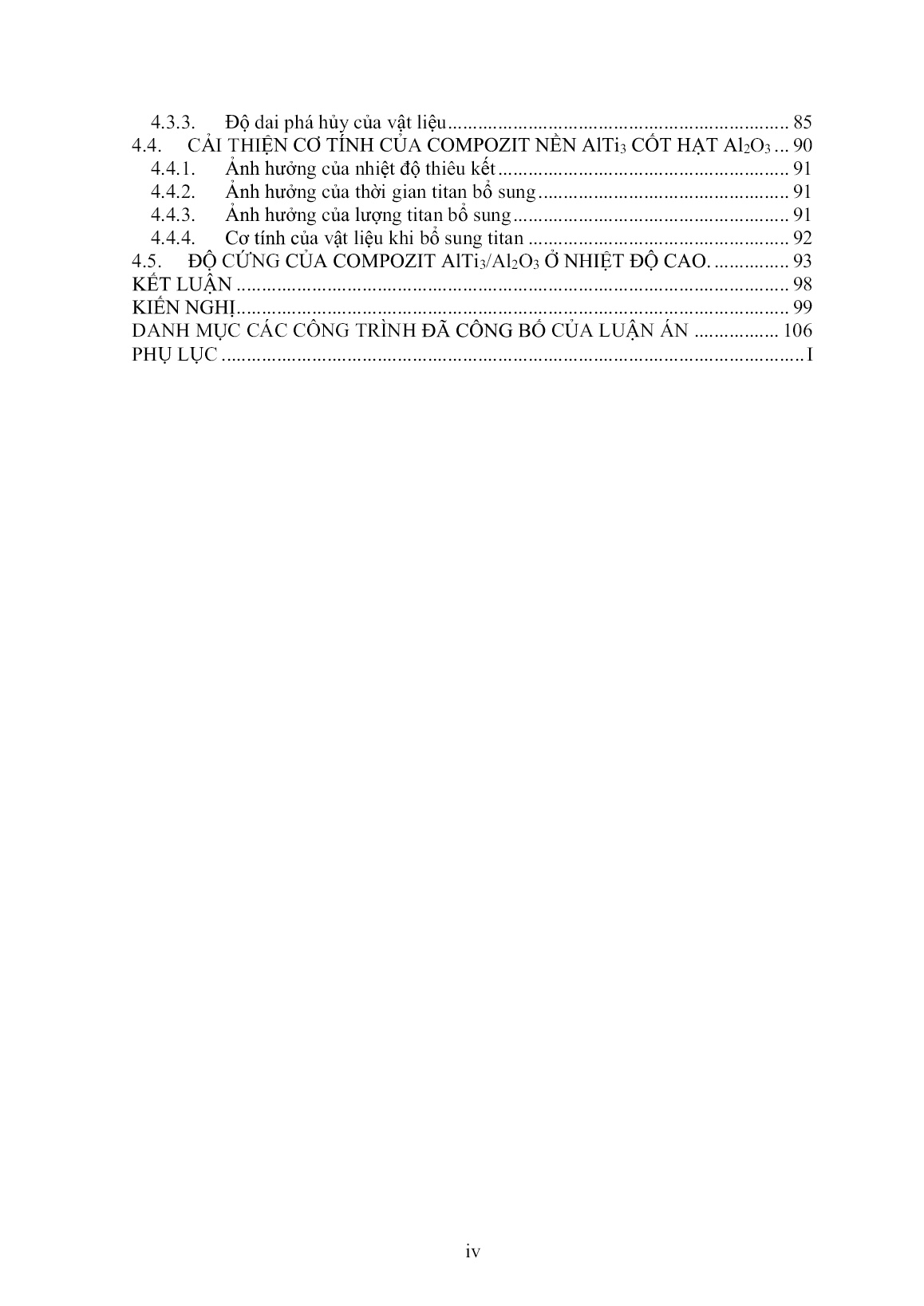
Trang 4
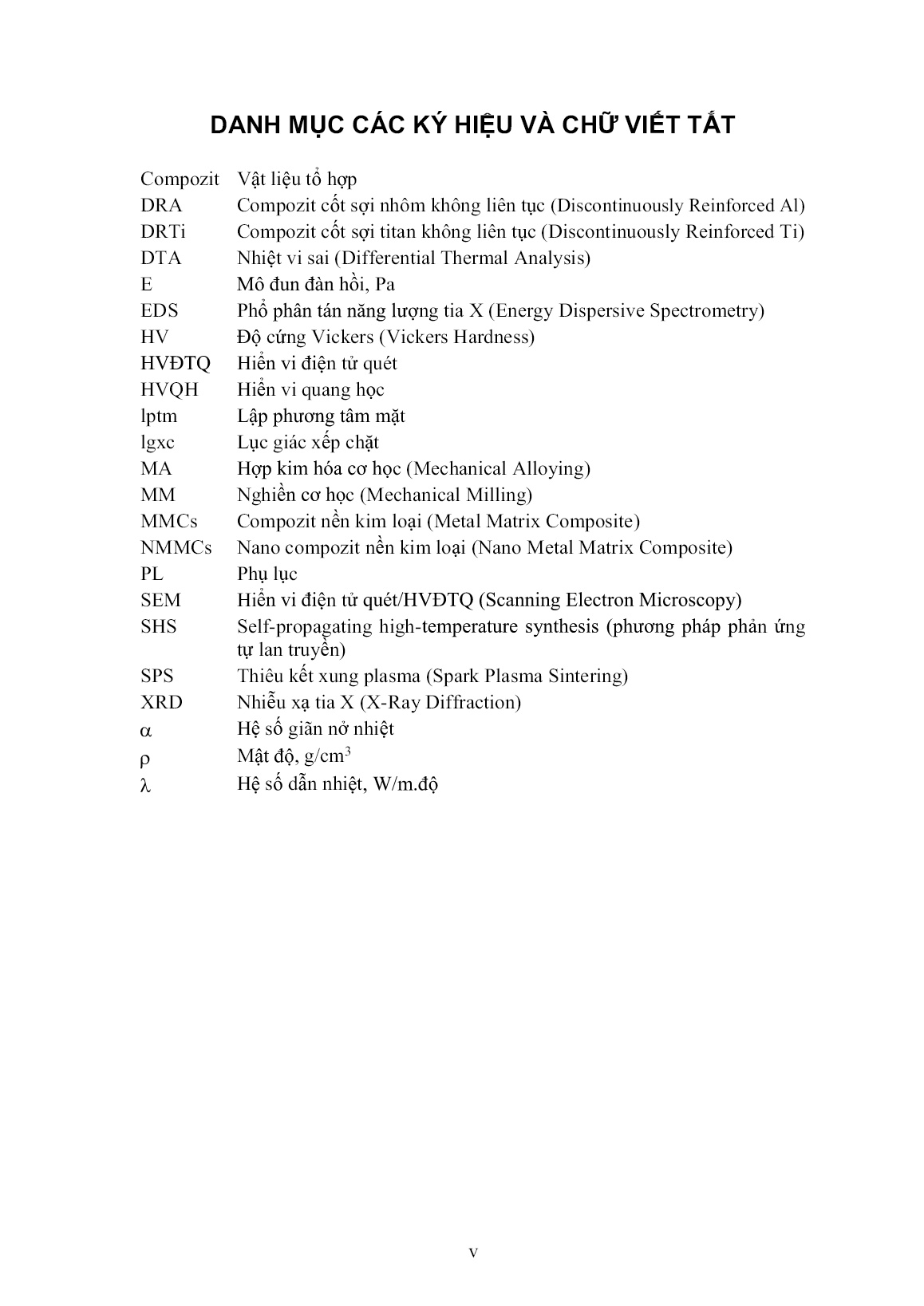
Trang 5
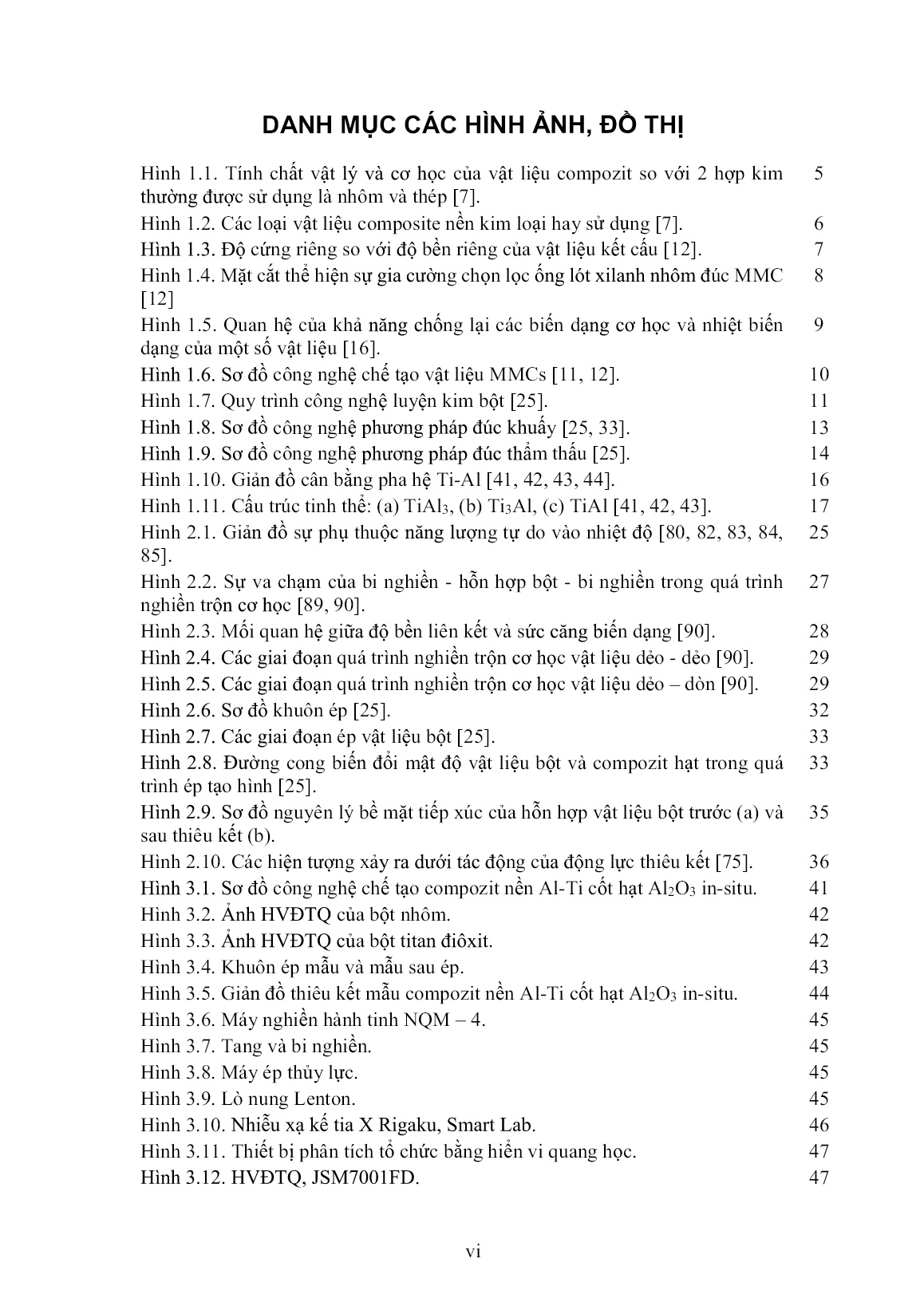
Trang 6
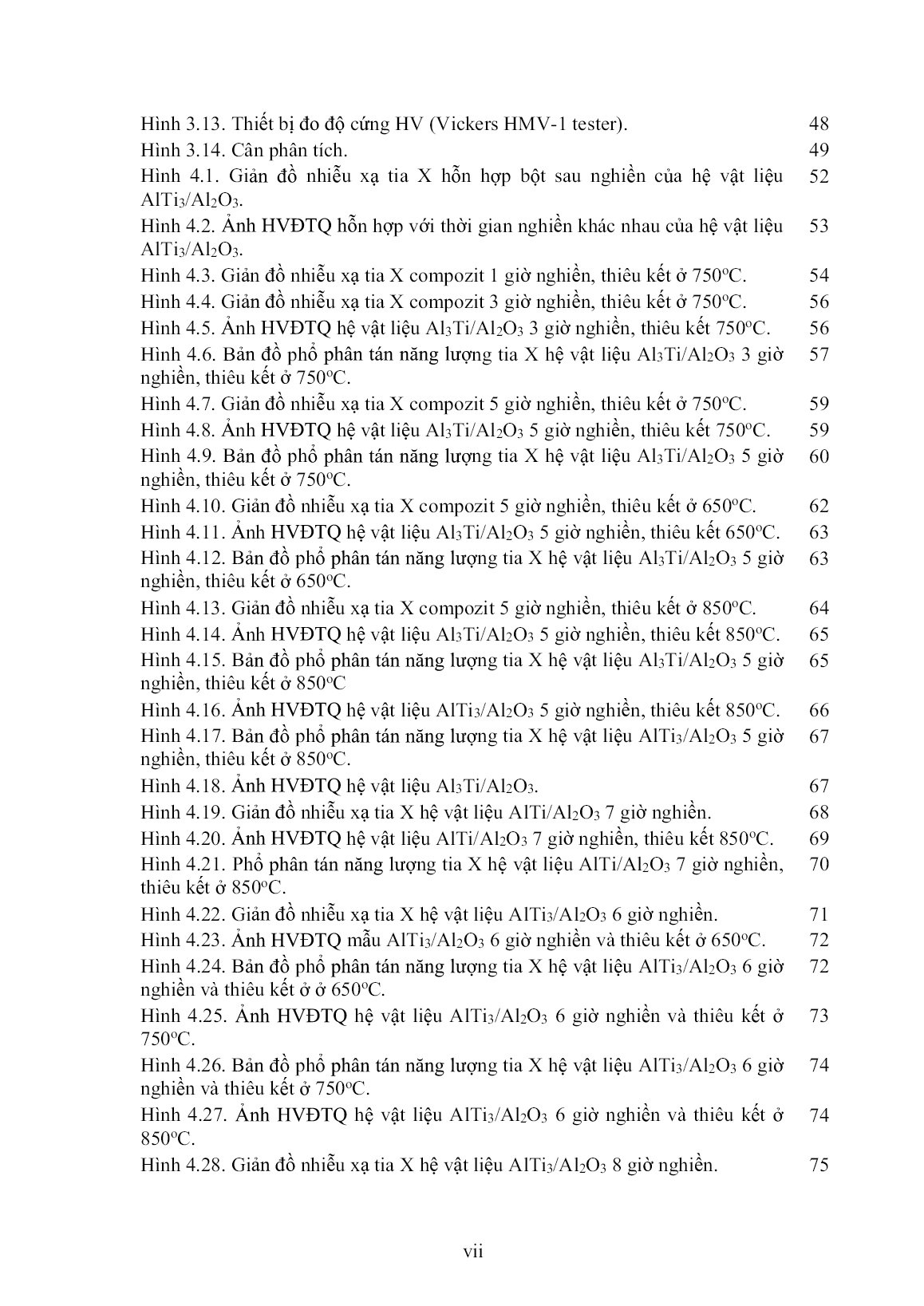
Trang 7
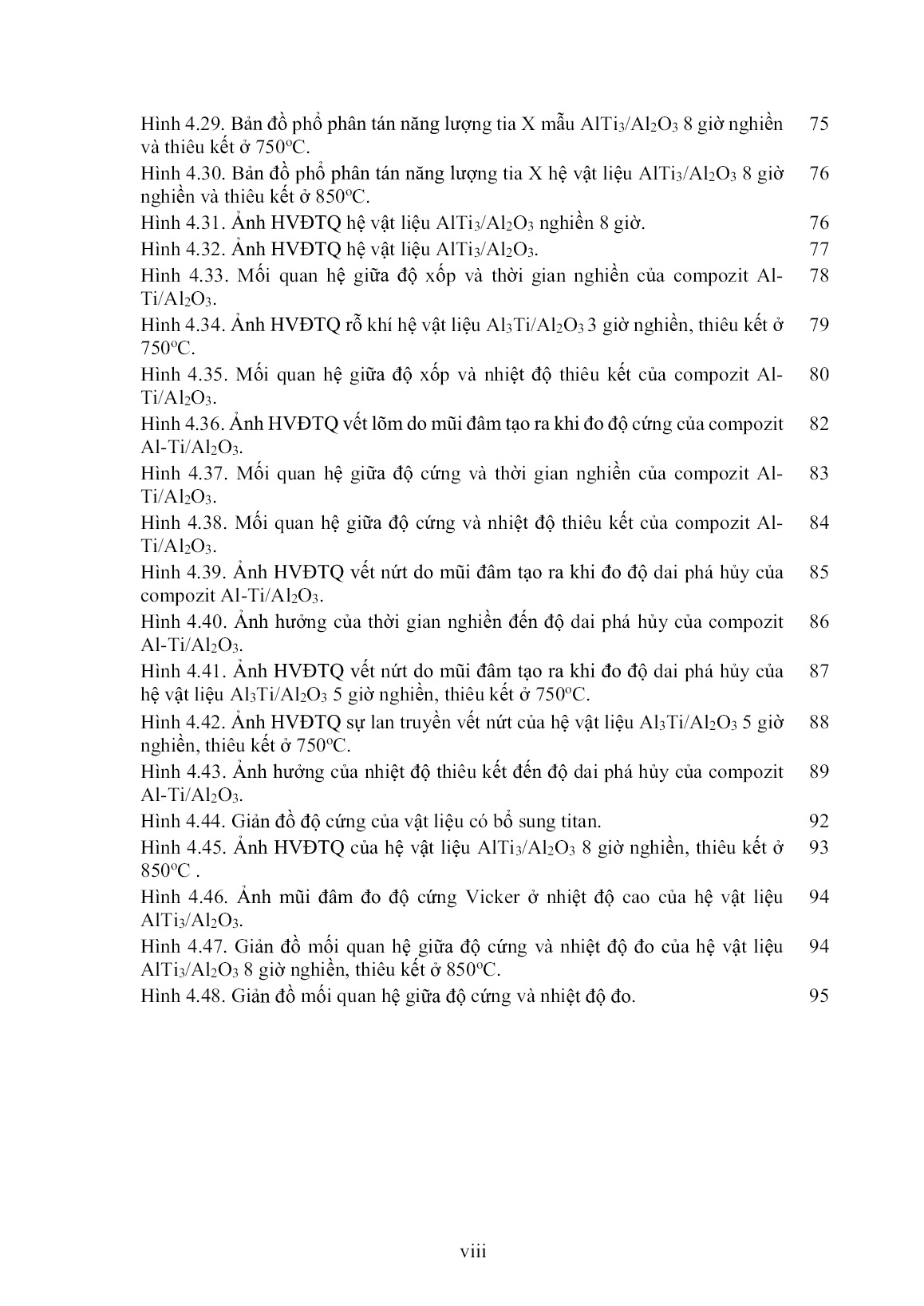
Trang 8
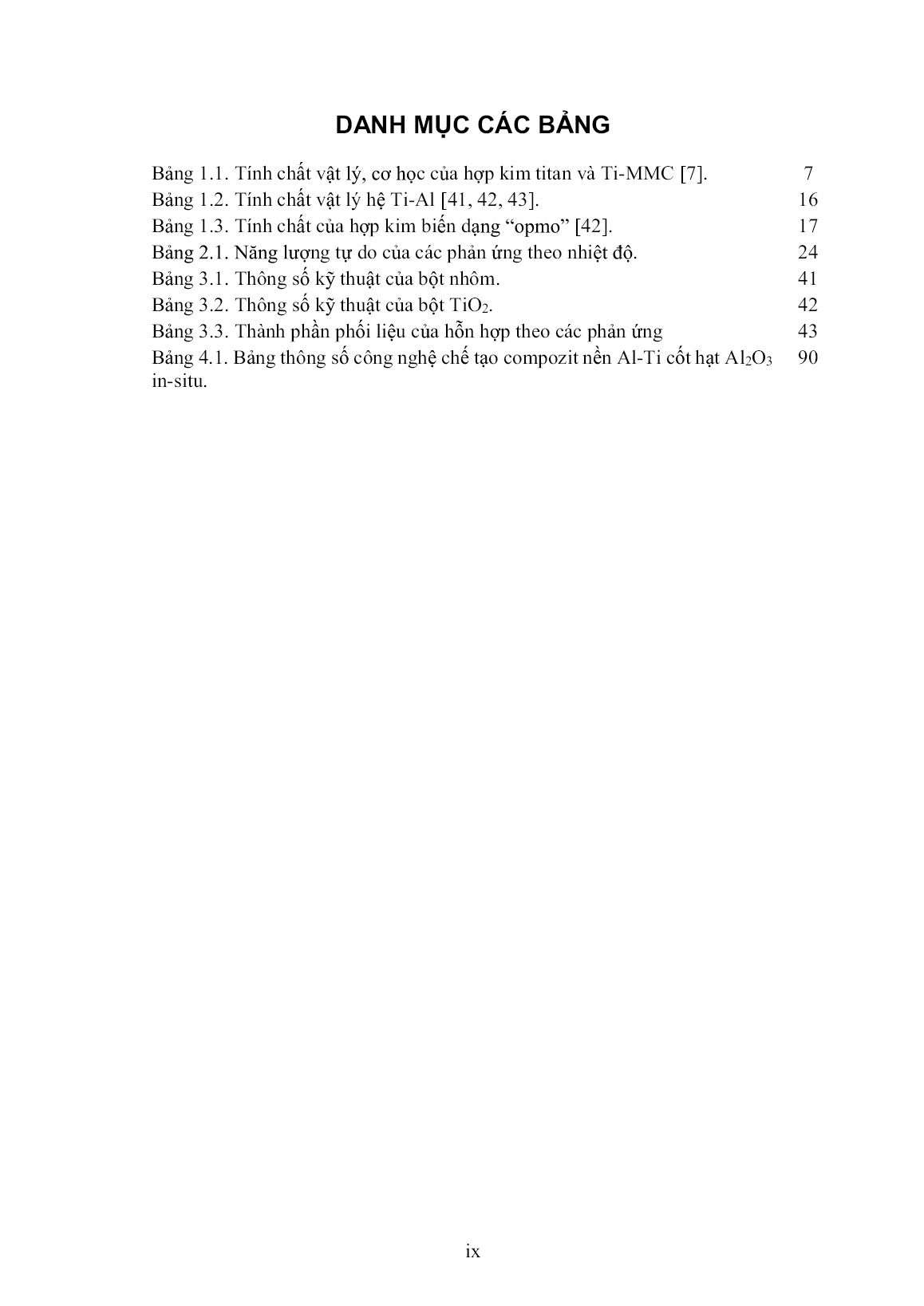
Trang 9
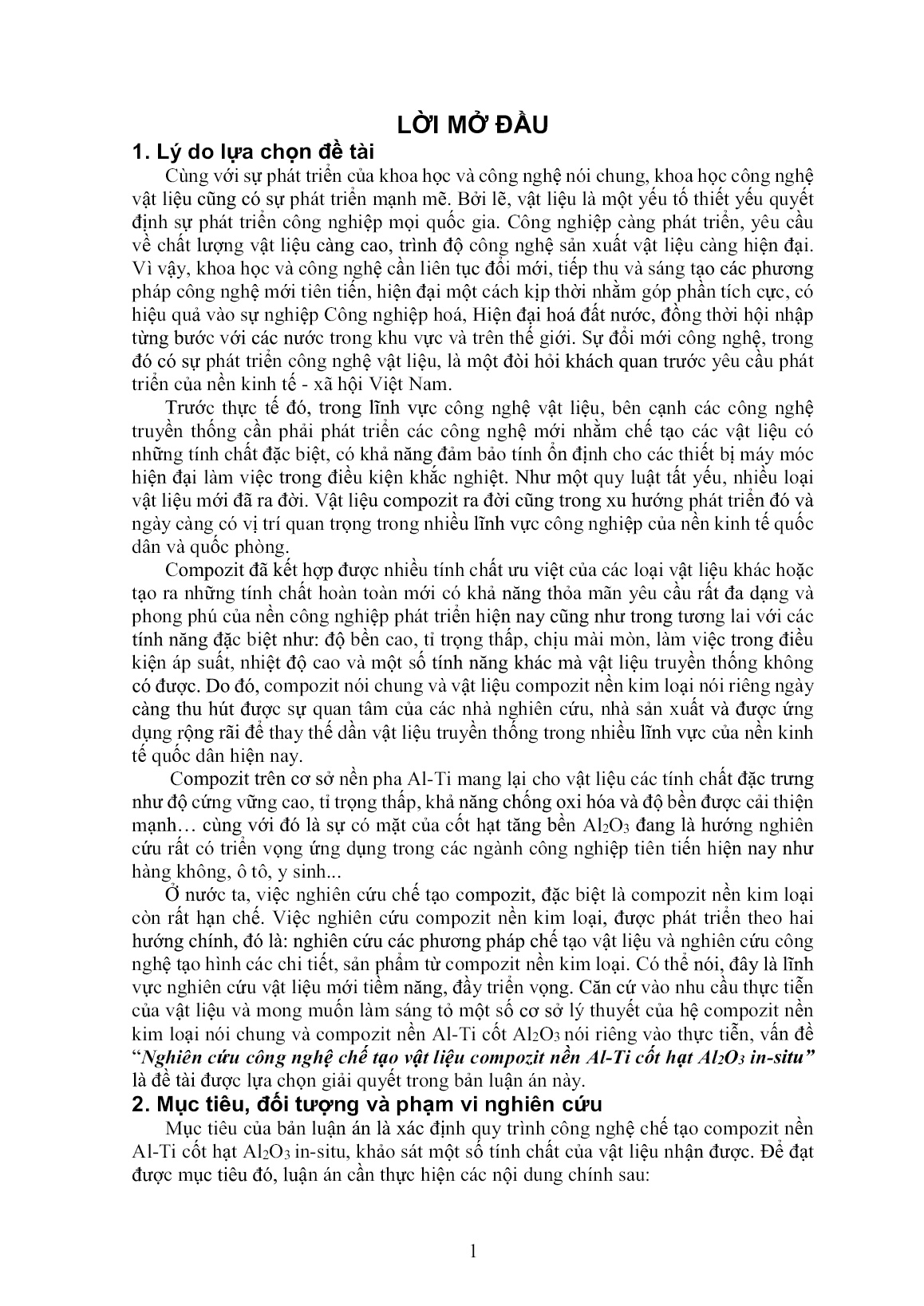
Trang 10
Tải về để xem bản đầy đủ
Bạn đang xem 10 trang mẫu của tài liệu "Luận án Nghiên cứu công nghệ chế tạo vật liệu compozit nền al-ti cốt hạt Al₂O₃ in-situ", để tải tài liệu gốc về máy hãy click vào nút Download ở trên.
Tóm tắt nội dung tài liệu: Luận án Nghiên cứu công nghệ chế tạo vật liệu compozit nền al-ti cốt hạt Al₂O₃ in-situ
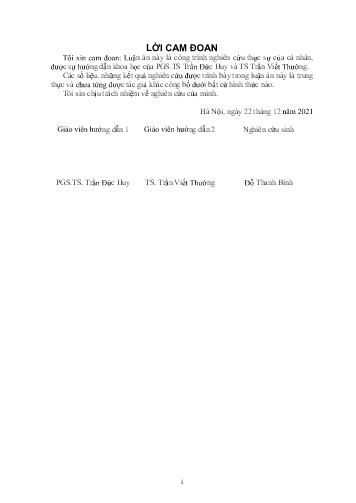
biên hạt có quá trình phát triển hạt. Quá trình co ngót bao gồm sự liên kết các hạt rắn hay tạo thành miền tiếp xúc, tiếp theo là sự cô lập lỗ xốp từ các lỗ xốp mở cho đến khi tạo vật liệu đặc. Cơ chế co ngót là cơ chế phức tạp liên quan đến tất cả các giai đoạn: hóa hơi ngưng tụ, khuếch tán bề mặt, khuếch tán biên hạt, khuếch tán thể tích, chảy nhớt, biến dạng dẻo. Mỗi quá trình chuyển khối đều thể hiện sự phụ thuộc vào kích thước hạt bột, kích thước tinh thể và khuyết tật. Trong đó kích thước hạt ảnh hưởng lớn nhất đến khuếch tán biên hạt và khuếch tán bề mặt. Trong giai đoạn đầu, khuếch tán bề mặt là đáng kể khi hiện tượng chính là sự phát triển miền tiếp xúc. Đối với các hạt nano, với diện tích và độ cong bề mặt lớn, khuếch tán bề mặt xảy ra rất nhanh ở ngay giai đoạn đầu quá trình thiêu kết. Đối với bột thông thường, khuếch tán bề mặt không dẫn đến quá trình co ngót mà chỉ dẫn đến sự mở rộng miền tiếp xúc giữa các hạt bột. Nhưng đối với hạt nano, sự tăng cường khuếch tán bề mặt cùng với việc tăng co ngót có thể xảy ra ở nhiệt độ thấp và với tốc độ rất nhanh. Sự kết tinh lại khác thường và sự thô đại hóa hạt không đồng thời với sự co ngót cũng có thể xảy ra ở nhiệt độ thấp. Điều đó không thể giải thích bằng khuếch tán bề mặt. Tốc độ nung nhiệt chậm làm mật độ cao một cách ngạc nhiên. Trong một số trường hợp khác không thấy sự ảnh hưởng nào của tốc độ nâng nhiệt đến sự co ngót và kết tinh lại. Tỷ lệ khuếch tán bề mặt và thể tích cũng không rõ ràng. Khuếch tán biên hạt trong thiêu kết hạt nano tất nhiên cũng lớn hơn nhiều so với bình thường. Thiêu kết kim loại hay ceramic kích thước nano đều bắt đầu từ nhiệt độ (0,2 ÷ 0,4) Tnc, như sắt thiêu kết ở nhiệt độ 900oK với kích thước 2000 nm nhưng lại thiêu kết ở 393K khi kích thước 30nm. Có nhiều cách tính nhiệt độ thiêu kết theo kích thước hạt. Đối với hạt có kích thước nhỏ hơn 100nm Alymos đã phát triển mối quan hệ thực nghiệm giữa nhiệt độ thiêu kết và kích thước hạt bằng biểu thức [94]: 𝑙𝑛𝑇𝑠 = 𝑙 𝑑 (2.20) Biểu thức này phù hợp với nhiều bột kim loại Herring đưa ra biểu thức quan hệ của thời gian thiêu kết và kích thước hạt như sau [95]: 𝑡1 𝑡2 = ( 𝑑1 𝑑2 ) 𝑛 (2.21) Chỉ số n=3 nếu cơ chế thiêu kết là chuyển khối và n=4 khi cơ chế thiêu kết chính là khuếch tán biên hạt. Từ biểu thức Arrhenius biểu diễn mối quan hệ của nhiệt độ thiêu kết vào kích thước hạt có thể được viết dưới dạng sau [94]: 𝑛. 𝑙𝑛 ( 𝑑1 𝑑2 ) = 𝑄 𝑅 . ( 1 𝑇1 − 1 𝑇2 ) (2.22) Trong đó: Q là năng lượng hoạt hóa của quá trình chiếm ưu thế d1, d2 là kích thước hạt bột ở thời điểm nhiệt độ đạt T1 và T2 Vật liệu nano thiêu kết phụ thuộc hoàn toàn vào đặc tính bề mặt, thậm chí là yếu tố quyết định đến quá trình. Nó không chỉ ảnh hưởng đến tính chất hạt bột, đến hành vi thiêu kết mà còn ảnh hưởng đến tính chất của sản phẩm tạo thành. Bột nano có hoạt tính bề mặt lớn và rất dễ bị nhiễm bẩn. Sự nhiễm bẩn bột phụ thuộc rất nhiều vào điều kiện sản xuất và chế tạo bột. Môi trường thiêu kết cũng là một yếu tố quan trọng gây nên sự nhiễm bẩn bột. 39 Bước đầu tiên của quá trình xít chặt là sự ép nguội ở nhiệt độ phòng. Kết quả thiêu kết cuối cùng thường được quyết định bởi cấu trúc tươi của vật ép. Lượng điểm tiếp xúc ban đầu, lỗ xốp nhỏ trong mẫu ép mật độ lớn, sự phân bổ lỗ xốp đồng đều làm tăng mật độ thiêu kết. Hạt nano dễ thiêu kết hơn vật liệu thông thường. Thời gian thiêu kết có thể ngắn hơn và nhiệt độ thiêu kết cũng thấp hơn. Sự trượt và sắp xếp lại hạt bị ngăn cản mạnh nhờ có lực ma sát lớn giữa các hạt bột. Lực này được tạo thành từ các hiện tượng cơ, lý, tĩnh điện, Van des walls và hấp phụ bề mặt càng trở nên đáng kể khi kích thước hạt giảm. Ma sát cơ học trở nên đáng kể do số lượng lớn các điểm tiếp xúc giữa các hạt. Biên hạt không bình thường tạo điều kiện cho sự sát nhập hạt. Do vậy, sự sắp xếp lại hạt bị ngăn trở và mật độ tươi thấp như trong trường hợp hạt bột thông thường. Khi sự trượt giữa các hạt bột được thuận lợi, mật độ tươi đạt được giá trị cao. Điều đó có thể đạt được nếu sử dụng chất bôi trơn hoặc mạ phủ bề mặt bột. Kết luận chương 2: 1. Đã xác định được điều kiện nhiệt động học của phản ứng chế tạo compozit nền Al-Ti cốt hạt Al2O3 từ bột nhôm và bột titan điôxit. Các phản ứng đều có thể xảy ra và thứ tự ưu tiên như sau trước hết là hệ vật liệu Al3Ti/Al2O3, tiếp đó lần lượt là các hệ vật liệu AlTi/Al2O3 và khó xảy ra hơn là AlTi3/Al2O3. 2. Compozit nền Al-Ti cốt hạt Al2O3 in-situ được chế tạo theo phương pháp luyện kim bột thông qua quá trình nghiền ép thiêu kết. 40 Chương 3. NỘI DUNG VÀ PHƯƠNG PHÁP NGHIÊN CỨU Trong các chương trước, đã trình bày về công nghệ chế tạo, tổ chức, tính chất và khả năng ứng dụng của compozit nền kim loại trong thực tế. Ảnh hưởng của cốt hạt nano tới cơ tính của vật liệu cũng được đề cập đến. Trong chương này sẽ giới thiệu nội dung và phương pháp nghiên cứu, quy trình chế tạo compozit nền Al-Ti cốt hạt Al2O3 in-situ. 3.1. NỘI DUNG NGHIÊN CỨU Nâng cao cơ tính của compozit nền Al-Ti bằng cách tạo ra cốt hạt gốm Al2O3 có cấu trúc cỡ nanomét là mục tiêu của luận án này. Mối quan hệ giữa nền Al-Ti với cốt hạt Al2O3, tính khả thiêu của hỗn hợp và khả năng tăng cơ tính của vật liệu, ảnh hưởng của các yếu tố công nghệ đến sự thay đổi thành phần pha, tổ chức tế vi và cơ tính của compozit sẽ là nội dung nghiên cứu chủ yếu của luận án. Cụ thể là: - Nghiên cứu chế tạo compozit nền Al-Ti cốt hạt Al2O3 in-situ kích thước cỡ nanomét. - Nghiên cứu ảnh hưởng của các thông số công nghệ đến khả năng hình thành pha trong quá trình chế tạo compozit nền Al-Ti cốt hạt Al2O3 in-situ. - Nghiên cứu ảnh hưởng của các thông số công nghệ đến cơ tính của vật liệu. 3.2. PHƯƠNG PHÁP NGHIÊN CỨU 3.2.1. Quy trình nghiên cứu Compozit nền Al-Ti cốt hạt Al2O3 có thể chế tạo theo các công nghệ khác nhau như: ôxi hóa, hợp kim hóa, Nhìn chung, việc hợp kim hóa cơ học [48, 49, 51, 53, 56, 57] trong thời gian gần đây được quan tâm. Phương pháp đó đã và đang được dùng phổ biến để chế tạo compozit cốt hạt phân tán trong nền kim loại tạo ra các sản phẩm đạt được yêu cầu cần thiết về độ cứng, độ bền, độ dẫn nhiệt, độ chịu mài mòn, v.v Nhờ kết hợp quá trình nghiền cơ học, ép và thiêu kết để tổng hợp compozit nền Al-Ti cốt hạt Al2O3 in-situ, cốt hạt Al2O3 hình thành có kích thước nhỏ mịn, phân tán tương đối đồng đều trong nền Al-Ti. Trong luận án này, đã lựa chọn phương pháp gia công cơ - hóa để chế tạo compozit nền Al-Ti cốt hạt Al2O3 in-situ. Qui trình công nghệ được trình bày trên hình 3.1. Cối và bi nghiền được làm sạch, khối lượng bi nghiền đưa vào cối tính theo tỉ lệ 10/1 so với lượng bột nghiền. Cân hỗn hợp bột căn cứ theo phản ứng, hỗn hợp sau cân được đưa vào cối nghiền, cối nghiền được đậy chặt bằng nắp và gioăng silicon, các thao tác thực hiện trong Glove box bảo vệ bằng khí Argon. Tiến hành nghiền trong máy nghiền hành tinh NQM-4, tốc độ quay 300 v/ph, thời gian nghiền từ 1 ÷ 8 giờ. Hỗn hợp bột sau nghiền được đem đi ép trong cối ép bằng hợp kim có đường kính 16mm, ép với áp lực 100MPa. Mẫu sau ép, tiến hành thiêu kết trong lò Lenton có khí Argon bảo vệ, nhiệt độ thiêu từ 650 oC đến 850oC. Mẫu sau thiêu kết tiến hành phân tích thành phần pha, tổ chức tế vi và xác định cơ tính. 41 3.2.2. Nguyên vật liệu a. Bột Nhôm Bột nhôm thương mại có độ sạch trên 99% (xuất xứ Đức) với thông số kỹ thuật trình bày trên bảng 3.1. Bảng 3.1. Thông số kỹ thuật của bột nhôm Hình dạng và kích thước của bột nhôm được quan sát và phân tích trên hiển vi điện tử quét (HVĐTQ) hình 3.2. Bột nhôm có hình dạng là các lá nhôm, kích thước trung bình khoảng 40 µm. Thông số kỹ thuật M, g/mol Khối lượng, % As, Pb Fe As Al 28,96 ≥ 0.03 ≤ 1 ≤ 0.0005 Còn lại Al (Bột, Al 99 %) TiO 2 (Bột, TiO 2 99,5 %) Cân trong Glove box Khí Ar Cối, bi nghiền Bi/bột = 10/1 Nghiền v = 300 v/ph Thời gian nghiền (1 ÷ 8) giờ Bột sau nghiền Ép Thiêu kết Sản phẩm Áp lực ép 100MPa Khí Ar Cối ép Nhiệt độ thiêu (650 ÷ 850) oC Xác định tính chất của compozit nền Al-Ti cốt hạt Al2O3 Hình 3.1. Sơ đồ công nghệ chế tạo compozit nền Al-Ti cốt hạt Al2O3 in-situ 42 b. Bột Titan đioxit Bột titan đioxit thương mại có độ sạch khoảng 99,5% (xuất xứ Trung Quốc) với thông số kỹ thuật trình bày trên bảng 3.2. Bảng 3.2. Thông số kỹ thuật của bột TiO2 Hình dạng và kích thước của bột titan điôxit được quan sát và phân tích trên hiển vi điện tử quét (HVĐTQ) hình 3.3. Bột titan điôxit có hình dạng hạt kết khối, kích thước trung bình khoảng 0,2 µm. Thông số kỹ thuật pH Khối lượng, % Cl N SiO2 Mg K Ca Fe TiO2 ≤ 8,6 0,002 0,001 0,005 0,003 0,01 0,007 0,001 Còn lại Hình 3.2. Ảnh HVĐTQ của bột nhôm Hình 3.3. Ảnh HVĐTQ của bột titan điôxit 43 3.2.3. Kỹ thuật chế tạo a. Cân phối liệu Tổng khối lượng hỗn hợp bột cho mỗi lần nghiền là 100 g, tỉ lệ riêng phần của từng loại bột trong hỗn hợp bột ban đầu đã được tính toán sao cho tạo ra thành phần pha theo các phản ứng 2.1, 2.2, 2.3: 13Al + 3TiO2 3Al3Ti + 2Al2O3 (2.1) 7Al + 3TiO2 3AlTi + 2Al2O3 (2.2) 5Al + 3TiO2 AlTi3 + 2Al2O3 (2.3) Bảng 3.3. Thành phần phối liệu của hỗn hợp theo các phản ứng TT Phản ứng Khối lượng Al (g) Khối lượng TiO2 (g) Khối lượng hỗn hợp (g) 1 2.1 59,40 40,60 100 2 2.2 44,07 55,93 100 3 2.3 36,01 63,99 100 b. Chế độ nghiền Sau khi tính toán phối liệu, hỗn hợp 100 g vật liệu bột ban đầu được nạp vào buồng nghiền cùng với bi nghiền bằng thép hợp kim đã biến cứng. Quá trình nghiền được thực hiện trên máy nghiền hành tinh NQM-4 với chế độ nghiền như sau: - Tốc độ quay : 300 vòng/phút - Tỉ lệ (theo khối lượng) bi nghiền/ bột nghiền : 10/1 - Chế độ nghiền : 15 phút, nghỉ 30 phút - Thời gian nghiền : (1 8) giờ - Môi trường bảo vệ : Khí Argon c. Ép tạo hình mẫu Nhằm tạo cho vật liệu có hình dáng cần thiết và có sự gắn kết nhất định trước khi thiêu kết. Tiến hành ép với áp lực 100 MPa để tạo khối sơ bộ hỗn hợp bột sau nghiền hành tinh từ 1 ÷ 8 giờ. Áp lực ép tạo ra sự biến dạng dẻo của các hạt bột trên bề mặt tiếp xúc và sự liên kết giữa các hạt bột trên bề mặt này. Hình 3.4. Khuôn ép mẫu và mẫu sau ép 44 Với điều kiện thí nghiệm hiện có, đã chọn phương pháp ép nguội một chiều trong khuôn kín hình trụ bằng thép 9CrSi đã qua nhiệt luyện, đường kính trong 16 mm, để tạo hình các mẫu thí nghiệm. Đây là phương pháp ép đơn giản, mặt khác đường kính và chiều cao của mẫu không lớn (H/D < 1). Kết cấu, hình dạng khuôn ép và mẫu sau ép như hình 3.4. d. Thiêu kết Công đoạn thiêu kết được tiến hành trong môi trường khí bảo vệ với chế độ thiêu kết và nhiệt độ thiêu kết riêng [48, 53, 95]. Quá trình này giúp các cấu tử bột liên kết lại với nhau, đồng thời hoàn nguyên titan đioxit thu được Al2O3 và pha Al-Ti. Sau khi thiêu kết mẫu có được độ bền chắc nhất định. Chế độ thiêu kết được thực hiện theo quy trình nêu ở hình 3.5. Việc lựa chọn nhiệt độ thiêu kết dựa vào nhiệt độ của cấu tử có nhiệt độ nóng chảy thấp hơn và giản đồ pha Ti-Al và Ti-Al-O [42, 47, 51, 53, 81], đã lựa chọn khoảng nhiệt độ thiêu từ 650 850oC. 3.2.4. Thiết bị nghiên cứu a. Máy nghiền hành tinh Thiết bị sử dụng trong nghiên cứu là máy nghiền bi kiểu hành tinh (NQM-4, xuất xứ Trung Quốc) như ở hình 3.6. Thông số kỹ thuật: - Chế độ làm việc: 2 tang nghiền hoặc 4 tang nghiền - Chế độ nghiền: nghiền khô, nghiền ướt - Tốc độ quay: 0 ÷ 600 vòng/phút, có thể điều chỉnh - Kích cỡ hạt đầu vào: < 10 mm với vật liệu mềm, < 3 mm với vật liệu cứng - Cỡ hạt đầu ra: nhỏ nhất 0.1 µm. - Thời gian hoạt động liên tục: tối đa 72 giờ Bi nghiền: bi thép hợp kim đã biến cứng, đường kính 6mm, khối lượng 4g/viên. Tang nghiền sử dụng thép hợp kim, không gỉ. Gioăng cao su chịu nhiệt và một số thiết bị phụ trợ khác, hình 3.7. Nguội cùng với lò tTK, oC , phút Hình 3.5. Quy trình thiêu kết mẫu compozit nền Al-Ti cốt hạt Al2O3 in-situ 30 phút 45 b. Thiết bị ép Hỗn hợp vật liệu bột được nạp vào trong khuôn ép, sau đó thực hiện quá trình ép trên máy ép thủy lực (hình 3.8), để tạo ra áp lực 100 MPa đã xác định ở trên. Hình 3.6. Máy nghiền hành tinh NQM – 4 Hình 3.8. Máy ép thủy lực Hình 3.7. Tang và bi nghiền Hình 3.9. Lò nung Lenton 46 c. Thiết bị thiêu Quá trình thiêu kết được tiến hành trong ống gốm gia nhiệt trong lò Lenton (Model: EF11/8B – Anh) như hình 3.9, môi trường thiêu kết là khí Argon. Thông số kỹ thuật + Nhiệt độ tối đa: 1100 oC + Công suất tối đa: 1,8 kW + Độ sạch của khí Argon trên 99 % 3.2.5. Phương pháp nghiên cứu Trên cơ sở nghiên cứu tổng quan đã đề xuất nội dung nghiên cứu và thực nghiệm nhằm đạt mục tiêu đề tài. Khi tiến hành thực nghiệm đã lựa chọn các phương pháp phù hợp với điều kiện của phòng thí nghiệm, kết hợp với các phương pháp đánh giá hiện đại khác để đảm bảo độ tin cậy. a. Phân tích nhiễu xạ tia X Mục đích của phương pháp phân tích nhiễu xạ Rơnghen là xác định thành phần pha của compozit, so sánh tương đối hàm lượng pha, từ đó cho phép điều chỉnh quy trình công nghệ chế tạo và góp phần lý giải các kết quả. Trong luận án này phân tích nhiễu xạ tia X nhằm xác định thành phần pha nền Al-Ti, cốt hạt Al2O3 và các pha liên quan, dựa vào vị trí và cường độ pick nhiễu xạ trên giản đồ ghi được của các mẫu xử lý ở chế độ công nghệ khác nhau sau nghiền và thiêu kết. Các phép đo được thực hiện trên thiết bị Rigaku, Smart Lab tại Trường đại học Doshisha, Nhật Bản, Khoa Hóa, Trường Đại học Khoa học tự nhiên, Đại học Quốc gia Hà Nội (hình 3.10). b. Phương pháp hiển vi Kỹ thuật hiển vi quang học Các mẫu trước khi xem tổ chức tế vi phải được mài nhẵn và đánh bóng. Các mẫu nghiên cứu có bề mặt phẳng được mài trên máy Struers – Labopol 25 có lắp giấy ráp SiC (hình 3.11a). Tốc độ vòng quay tới 500 vòng/phút và được làm mát bằng nước. Mẫu được mài Hình 3.10. Nhiễu xạ kế tia X Rigaku, Smart Lab 47 lần lượt trên giấy ráp 80, 320, 400, 600, 800, 1000, 1200, 1500 và sau đó đánh bóng trên vải nỉ. Bề mặt đạt được sáng, không có vết xước và cuối cùng được đánh bóng bằng bột Al2O3 cỡ hạt 5 µm. Tổ chức tế vi được quan sát và chụp trên kính hiển vi quang học (HVQH) Leica 4000 (hình 3.11b) Kỹ thuật hiển vi điện tử quét Hiển vi điện tử quét (HVĐTQ) là một công cụ cho phép thu nhận các ảnh bề mặt mẫu với độ phân giải cao, hoạt động trên nguyên tắc ghi các tín hiệu điện tử phát xạ từ sâu trong khối, bên dưới bề mặt mẫu (cỡ vài µm) khi chùm điện tử tương tác với bề mặt mẫu cho phép phân tích thành phần nguyên tố. Kiểu ảnh chung nhất được tạo bởi các điện tử thứ cấp có năng lượng thấp (E < 50 eV). Trong luận án phương pháp HVĐTQ dùng để xác định tổ chức tế vi của compozit, kích thước hạt và thành phần nguyên tố của các mẫu nghiên cứu, cấu trúc của mẫu xốp. Các nghiên cứu trong luận án được khảo sát trên kính HVĐTQ phát xạ trường FESEM Hitachi S-4800 (Model JSM-7600F) tại PTN Hiển vi điện tử và vi phân tích (BKEMMA) thuộc Viện Tiên tiến Khoa học và Công nghệ (AIST), Trường Đại học Bách Khoa Hà Nội và JSM7001FD tại Trường đại học Doshisha, Nhật Bản (hình 3.12). (a) (b) Hình 3.11. Thiết bị phân tích tổ chức bằng hiển vi quang học Hình 3.12. HVĐTQ, JSM7001FD 48 c. Thử cơ tính Đo độ cứng Vickers Phép đo cho các mẫu sau nghiền và thiêu kết tại phòng thí nghiệm Vật liệu học, Trường Đại học Bách khoa Hà Nội và Trường đại học Doshisha, Nhật Bản bằng máy đo độ cứng Vickers HMV-1 tester (Shimadzu), thử nghiệm với tải trọng 245,2 mN trong 15 s (hình 3.13). Độ dai phá hủy Nghiên cứu cho thấy có nhiều phương pháp xác định độ dai phá hủy khác nhau, trong luận án đo độ dai phá hủy được xác định theo độ dài vết nứt do mũi đâm từ phương pháp đo độ cứng Vickers, IF (indentation fracture) [96]. Mẫu sau mài và đánh bóng, tiến hành đo độ dai phá hủy bằng cách tạo vết nứt bởi vết đâm đo độ cứng Vickers với lực đâm được lựa chọn đủ lớn để tạo ra vết nứt có thể đo được của mẫu thử, lực đâm lớn hơn lực đo độ cứng mẫu và nhỏ hơn lực làm vỡ mẫu (nghiên cứu mẫu thử sử dụng lực đâm từ 98 đến 294 N). Vết nứt được tạo ra tại góc của mũi đâm, tiến hành đo chiều dài trung bình của vết nứt và đường chéo vết đâm. Độ dai phá hủy có mối liên hệ với lực đâm, kích thước trung bình vết nứt, môđun đàn hồi và độ cứng của vật liệu. Phương pháp này có đặc tính đo độ dai phá hủy “tế vi” và chỉ cần một lượng nhỏ vật liệu sử dụng khi đo. Độ dai có thể được cải thiện nếu thay đổi bản chất, đặc tính liên bề mặt và phân bố của các phần tử pha thứ hai nhằm khống chế sự lan truyền vết nứt từ phía trước đỉnh của nó. Độ dai khi đó gọi là độ dai nội tại, nó là thuộc tính của một tổ chức tế vi đặc thù và là dạng độ dai chủ yếu của nhóm vật liệu kim loại dẻo, ví dụ hợp kim, nhưng lại không hiệu quả đối với nhóm vật liệu giòn, ví dụ gốm. Loại vật liệu giòn cần có độ dai ngoại vi. Nó bao gồm các cơ chế (tế vi) tác động ở vùng phía sau đỉnh vết nứt nhằm giảm đáng kể động lực lan truyền đỉnh vết nứt (hiệu ứng che chắn đỉnh nứt) nhờ tạo ra các cầu nối giữa các bề mặt vết nứt, hoặc nhờ chuyển pha. Phá hủy thực tế là một sự cạnh tranh lẫn nhau giữa cơ chế (phá hủy) nội tại ở phía đỉnh vết nứt nhằm kích thích nứt lan truyền và cơ chế (che chắn) ngoại vi chủ yếu ở phía sau đỉnh vết nứt để cản trở nó. Độ dai phá hủy được tính theo công thức sau: 𝐾𝐼𝐶 = 0,026 𝐸1/2.𝑃1/2.𝑎 𝑐3/2 (3.4) Trong đó: KIC: Độ dai phá hủy (Pa.m1/2) E: Môđun đàn hồi (Pa) Mô đun đàn hồi E [97]: E=ΦP.EP+(1-ΦP)EM (3.5) E: mô đun đàn hổi của compozit (Pa) Hình 3.13. Thiết bị đo độ cứng Hv (Vickers HMV-1 tester) 49 Ep: Mô đun đàn hồi của cốt hạt (Pa) EM: Mô đun đàn hồi của nền (Pa) p: % thể tích hạt. P: Lực đâm (N) a: Độ dài đường chéo vết đâm (m) c: Chiều dài trung bình của vết nứt (m) Thí nghiệm được thực hiện tại phòng thí nghiệm Vật liệu học, Trường Đại học Bách khoa Hà Nội và Trường đại học Doshisha, Nhật Bản bằng máy đo độ cứng Vickers HMV-1 tester (Shimadzu) (hình 3.13). d. Phương pháp đo độ xốp Độ xốp là một thông số quan trọng đối với các sản phẩm bột. Nó cho phép gián tiếp đánh giá các tính chất khác như độ bền, độ cứng và tổ chức tế vi của sản phẩm. Độ xốp là tỉ lệ giữa tổng các lỗ hổng trong vật liệu với tổng thể tích toàn phần vật liệu đó. Để xác định được độ xốp (hay còn gọi là mật độ) của vật liệu đã áp dụng định luật Ác-si-mét và theo tiêu chuẩn TCVN 8189:2009 [98]. Độ xốp của mẫu compozit nền Al-Ti cốt hạt Al2O3 in-situ được xác định bằng cách lấy mẫu (được bôi một lớp glyxerin để tránh cho nước thấm vào bên trong mẫu vật liệu) đo độ xốp. Dùng cân đo tỉ trọng xác định độ xốp thể hiện trên hình 3.14. Tỷ trọng của mẫu được xác định theo công thức sau: m m V G γ (3.6) Trong đó: Gm- trọng lượng mẫu; Vm- thể tích mẫu. Vm = VH2O = GH2O γH2O = GH2O (3.7) Trong đó: VH2O - thể tích của nước bị chiếm chỗ; GH2O- trọng lượng của nước; γH2O- tỷ trọng của nước (γH2O ≈ 1g/cm 3). Giả sử: GKK là trọng lượng của mẫu khi cân trong không khí; GH2O là trọng lượng của mẫu khi cân trong nước. Ta có, tỷ trọng của mẫu vật liệu xốp được xác định như sau: γX = GKK. γH2O GKK − GH2O , g cm3⁄ (3.8) Sau khi xác định được tỷ trọng của mẫu vật liệu xốp, sẽ xác định được độ xốp tương đối của mẫu thông qua công thức: Hình 3.14. Cân phân tích 50 %100. γ γγ θ T XT (3.9) Trong đó: γT- tỷ trọng của mẫu vật liệu theo phối liệu có các cấu tử thành phần, g/cm 3; γT = [(vol.%Al). Al + (vol.%TiO2). ρTiO2] X- tỷ trọng của mẫu vật liệu xốp, g/cm3. Kết luận chương 3: 1. Đã lựa chọn được quy trình công nghệ và thiết bị thực nghiệm, phân tích kiểm tra, đánh giá tính chất của vật liệu phù hợp để nghiên cứu chế tạo compozit nền Al- Ti cốt hạt Al2O3 in-situ. 2. Đã lựa ch
File đính kèm:
luan_an_nghien_cuu_cong_nghe_che_tao_vat_lieu_compozit_nen_a.pdf
1. Bìa luận án.pdf
2. Bìa tóm tắt luận án.pdf
2. Tóm tắt luận án.pdf
3. Thông tin đưa lên mạng - tiếng Anh.pdf
4. Thông tin đưa lên mạng - tiếng Việt.docx
4. Thông tin đưa lên mạng - tiếng Việt.pdf
5. Trích yếu luận án.docx
5. Trích yếu luận án.pdf