Luận án Nghiên cứu quá trình cháy và phát thải ô nhiễm động cơ Hybrid Biogas-Xăng
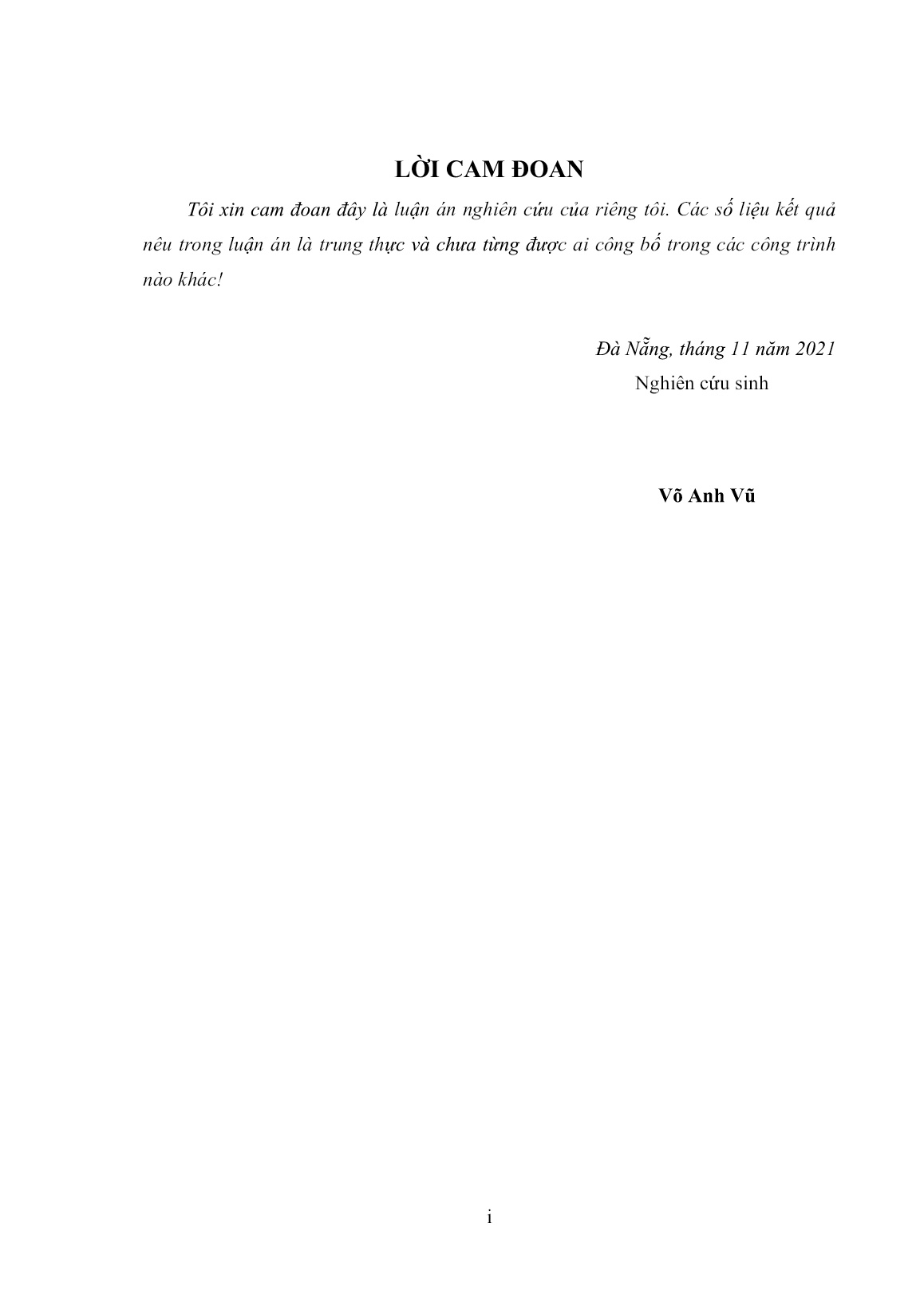
Trang 1
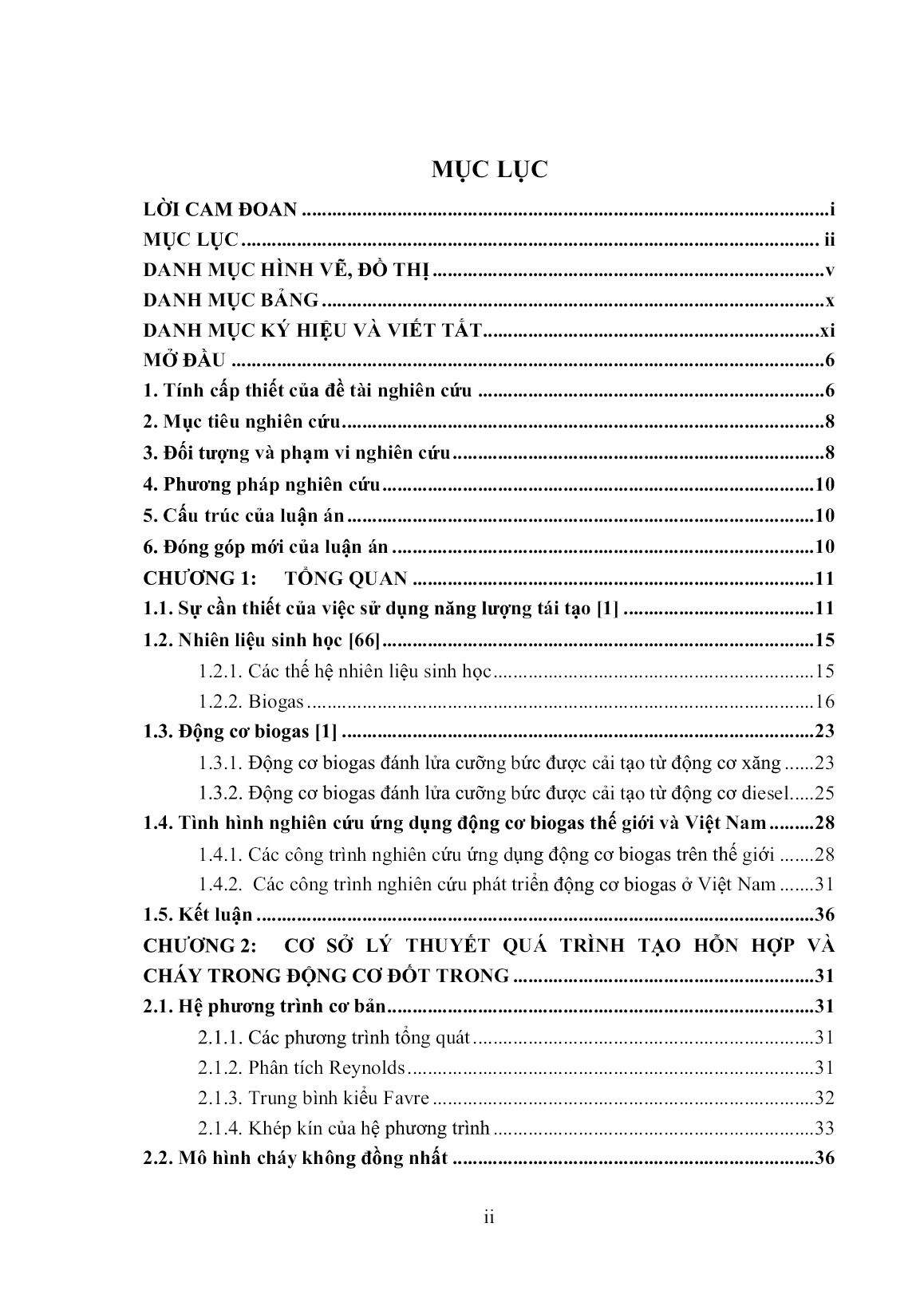
Trang 2
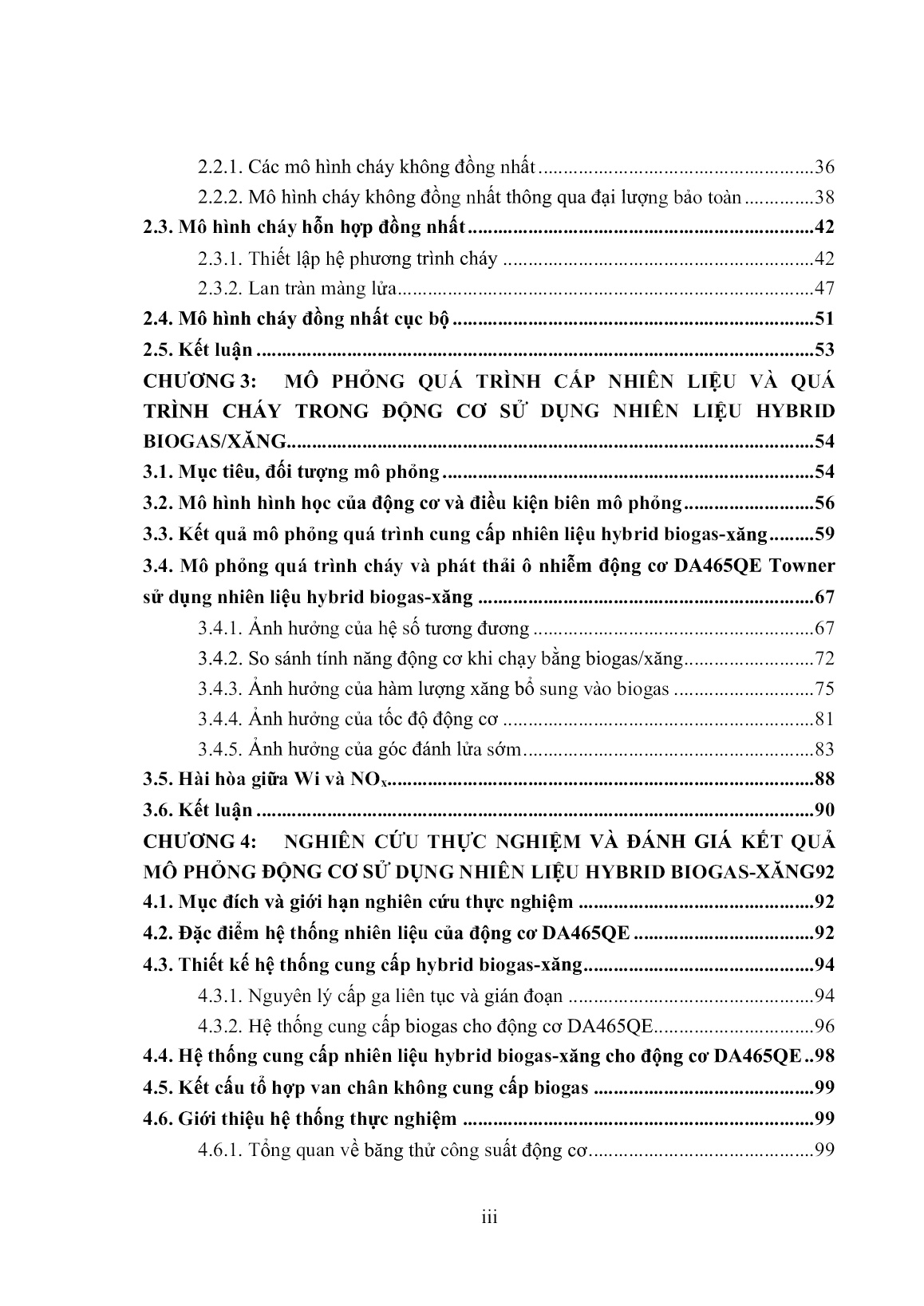
Trang 3
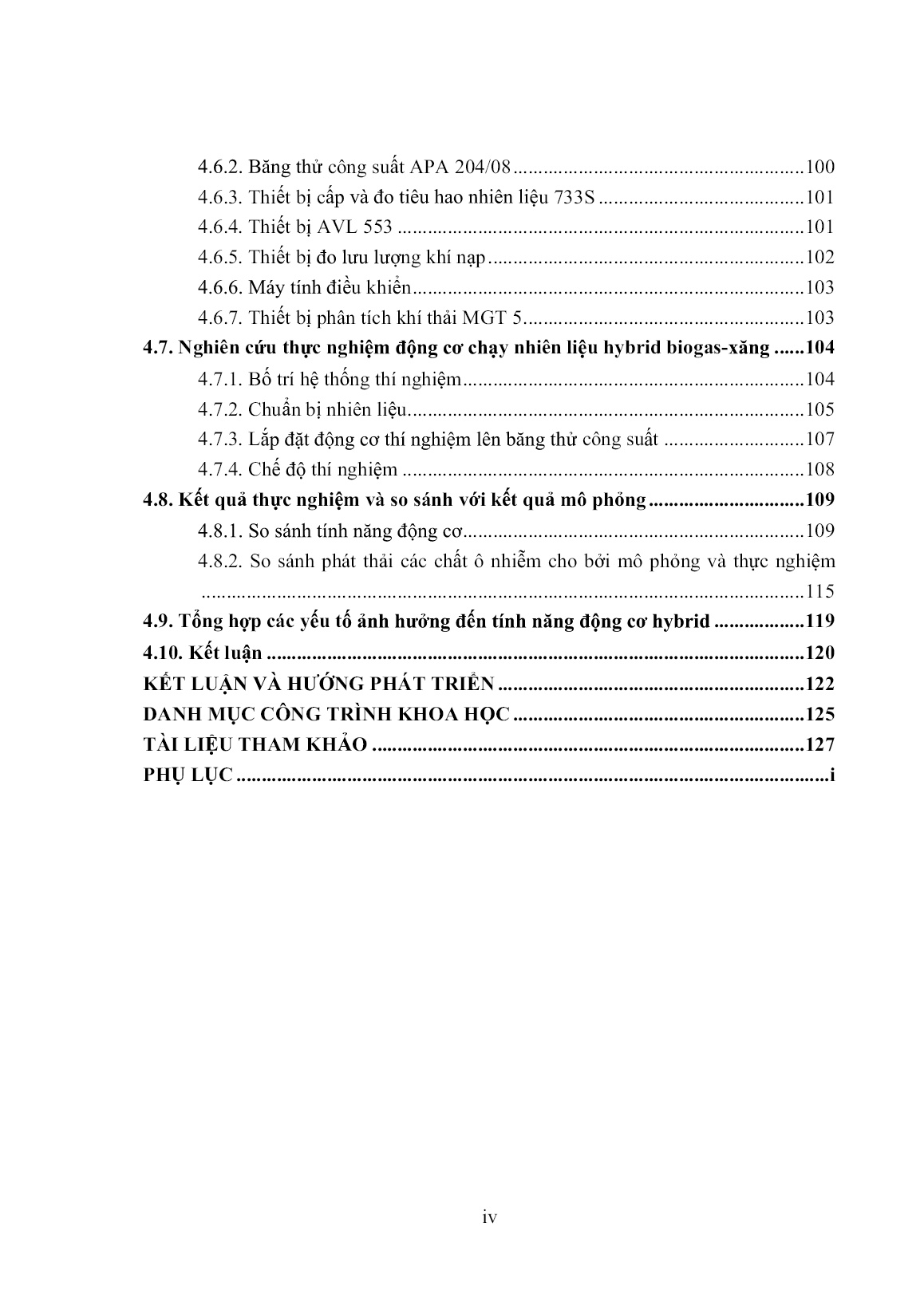
Trang 4
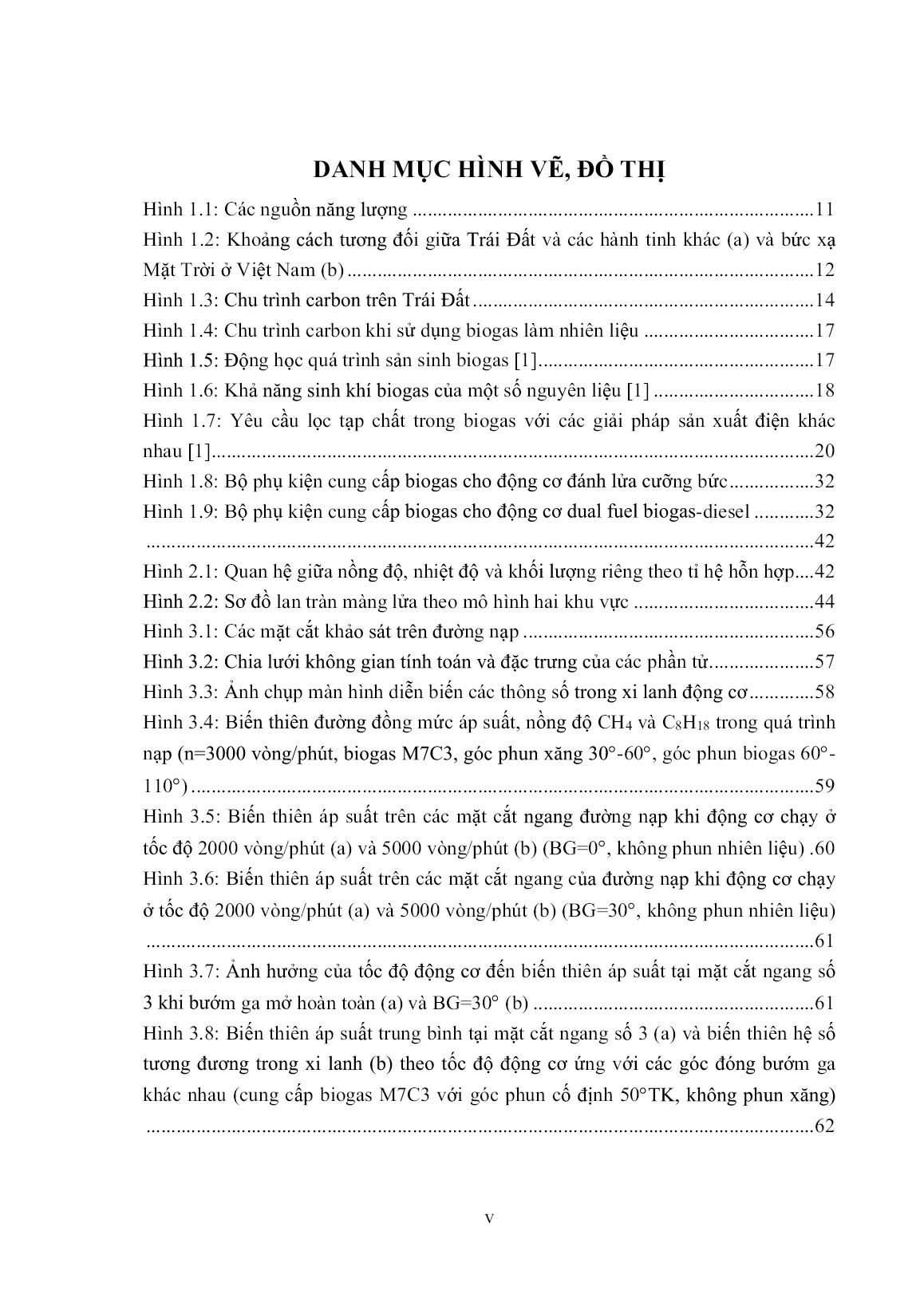
Trang 5
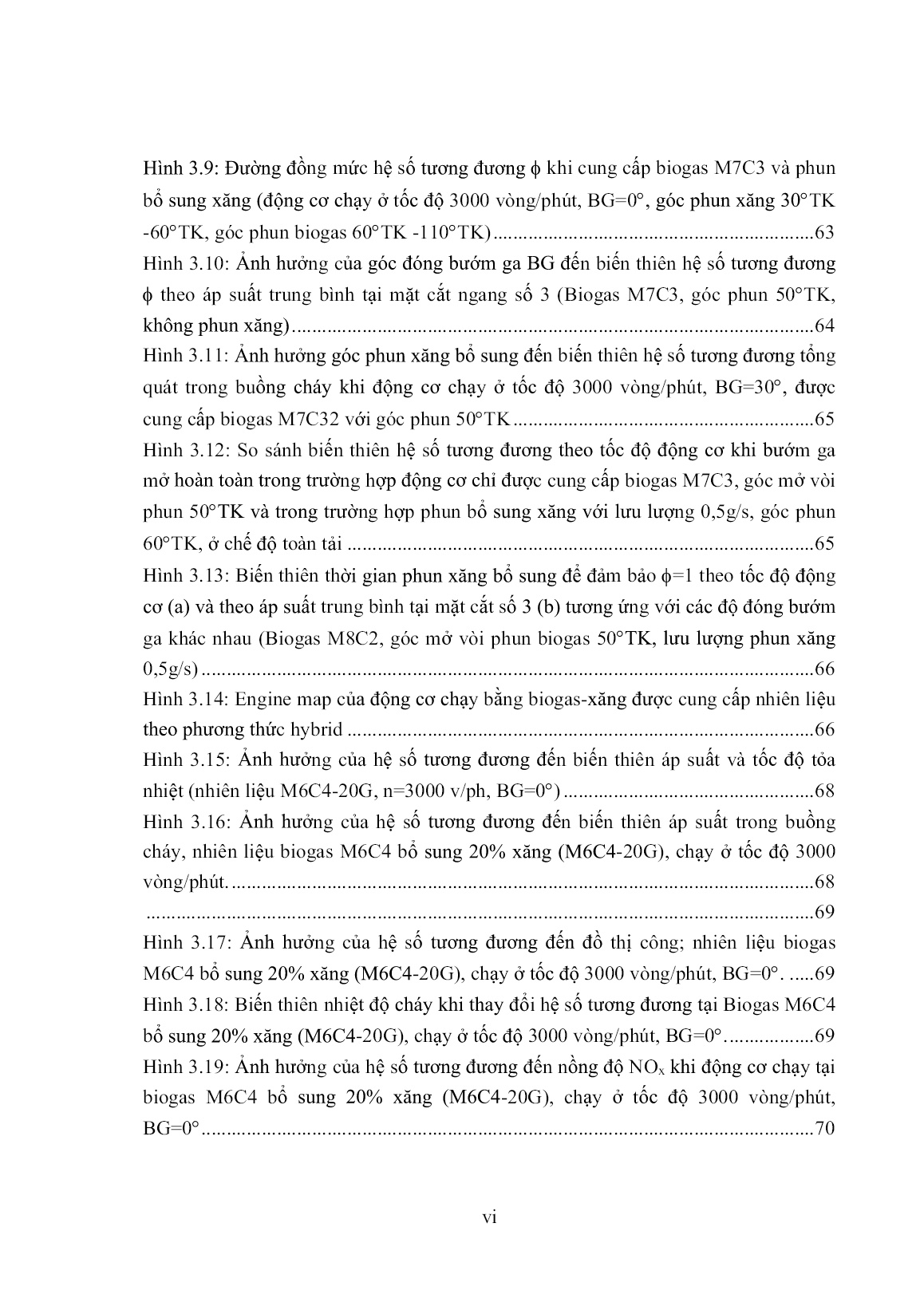
Trang 6
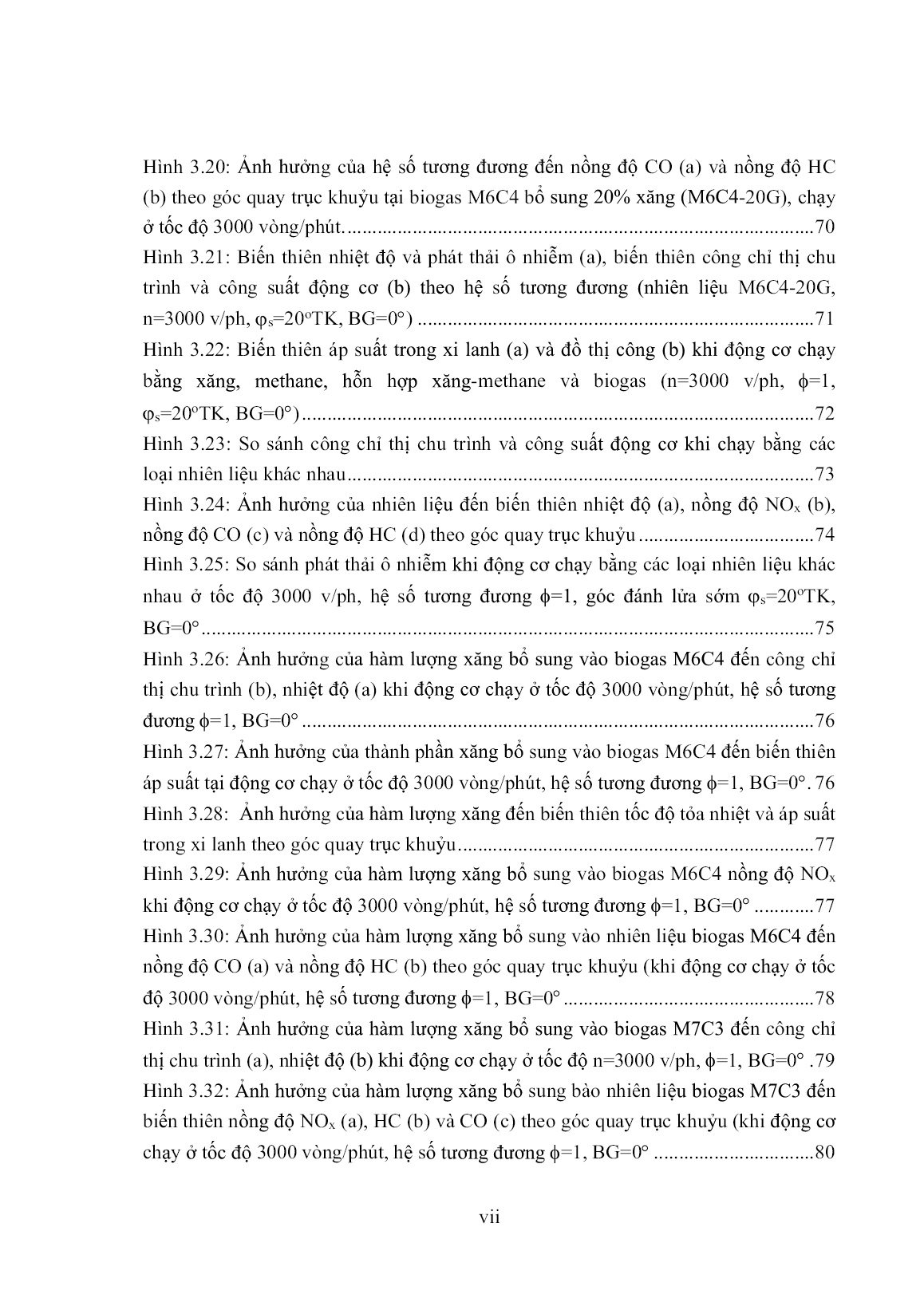
Trang 7
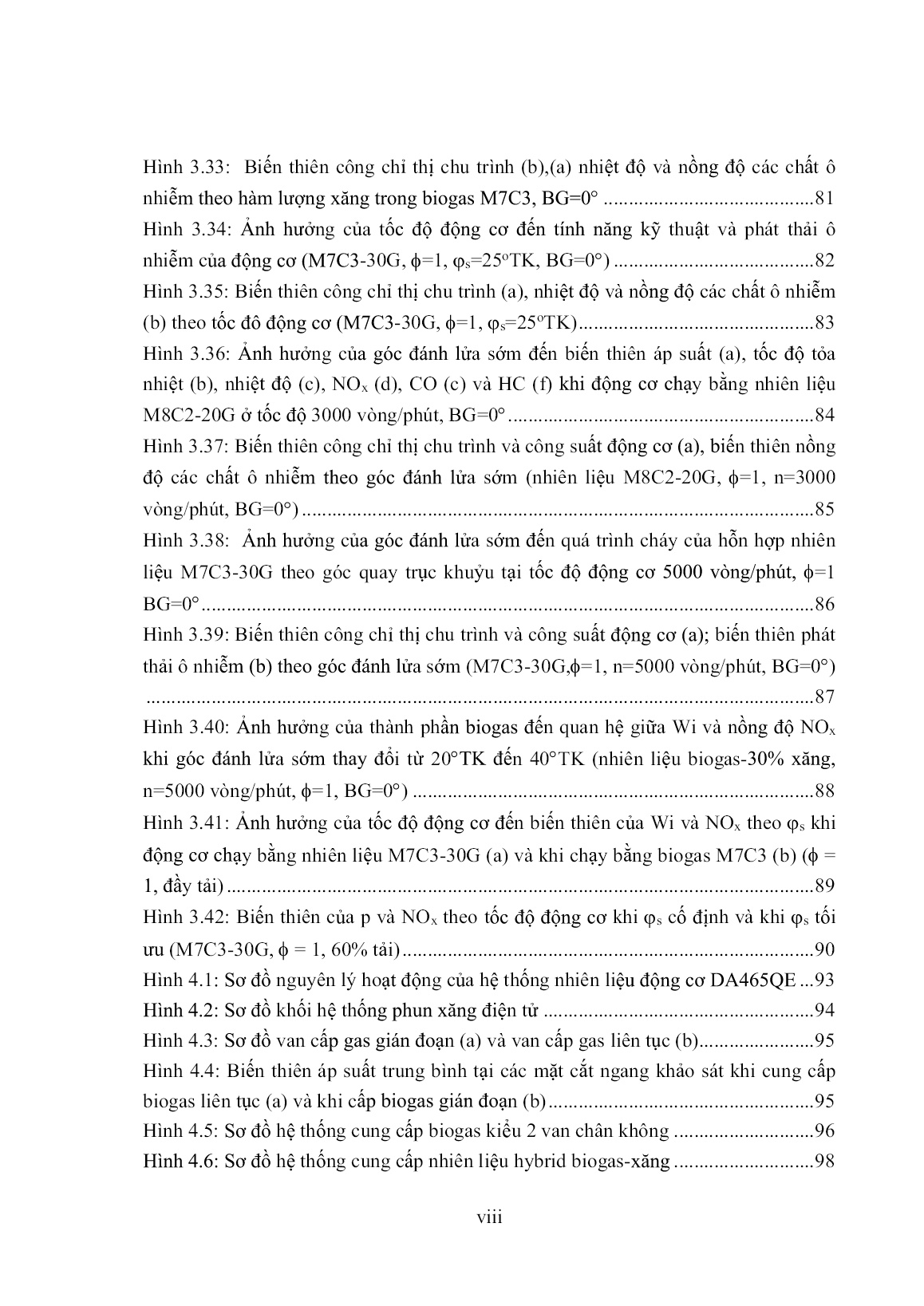
Trang 8
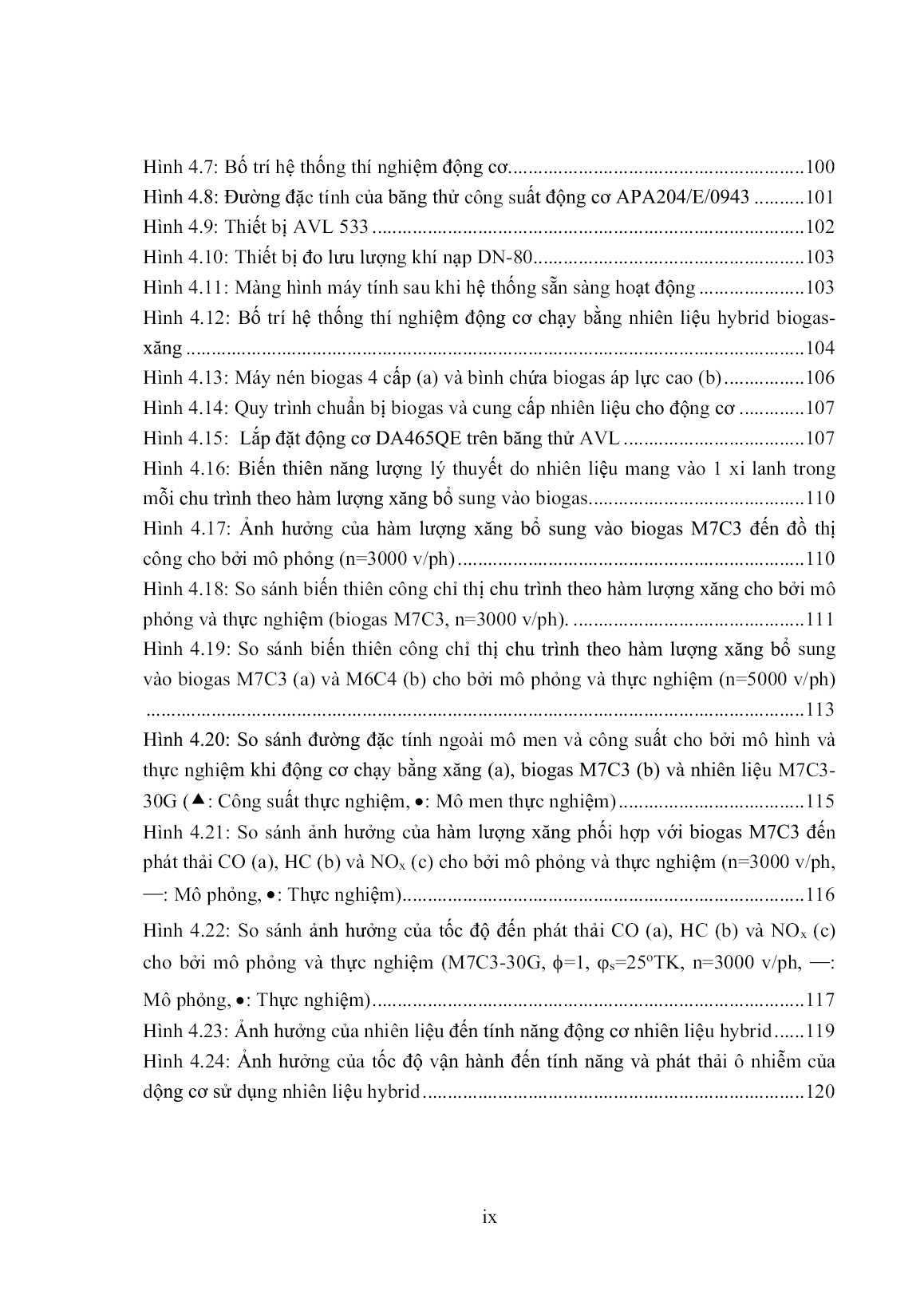
Trang 9
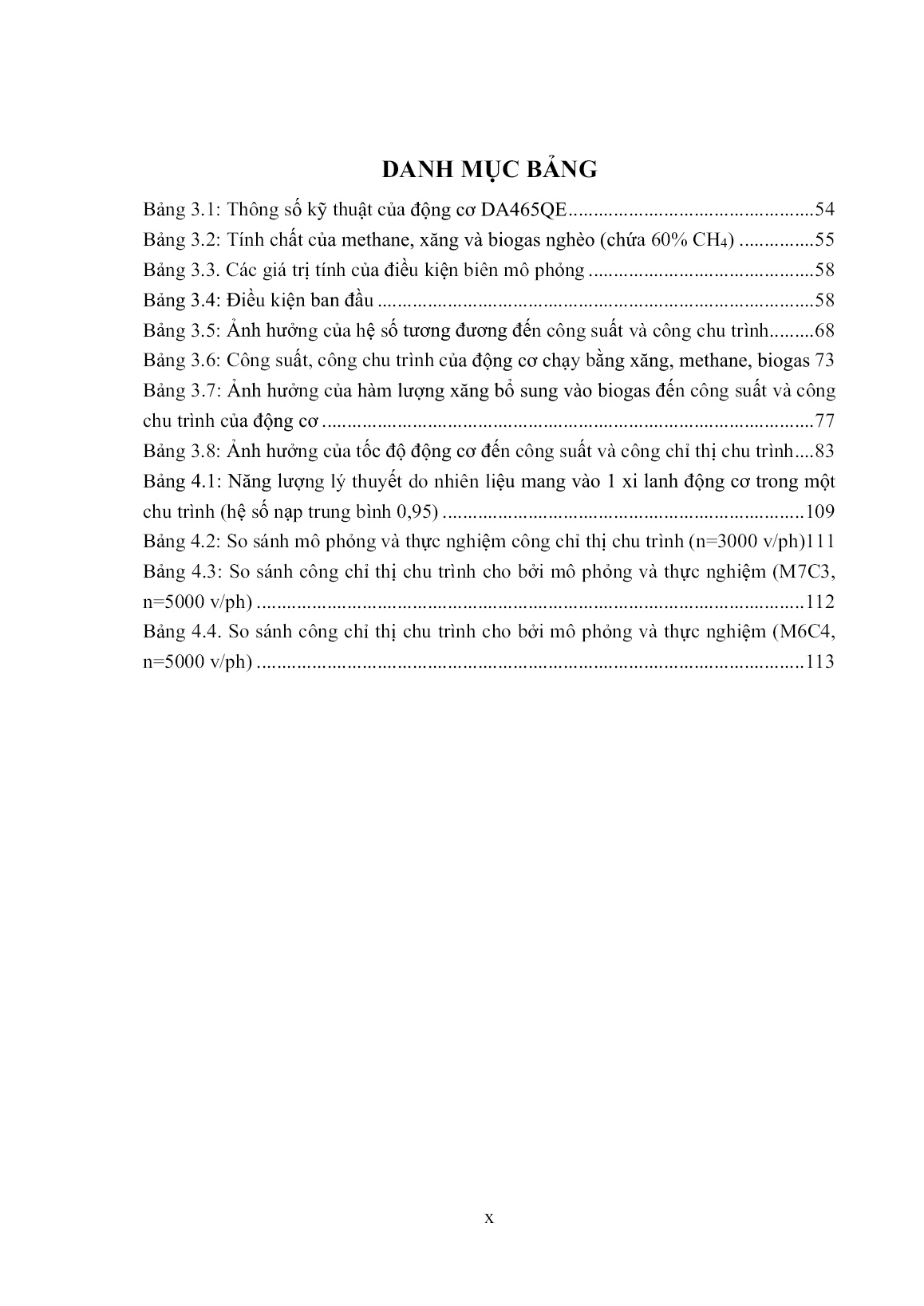
Trang 10
Tải về để xem bản đầy đủ
Bạn đang xem 10 trang mẫu của tài liệu "Luận án Nghiên cứu quá trình cháy và phát thải ô nhiễm động cơ Hybrid Biogas-Xăng", để tải tài liệu gốc về máy hãy click vào nút Download ở trên.
Tóm tắt nội dung tài liệu: Luận án Nghiên cứu quá trình cháy và phát thải ô nhiễm động cơ Hybrid Biogas-Xăng
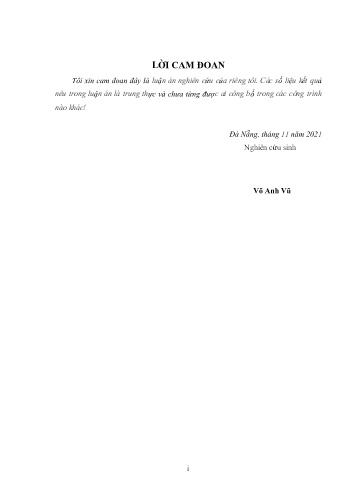
S t Sc + = + (2.75) Trong đó: c: giá trị trung bình của biến diễn tiến phản ứng; Sct = Chuẩn số Schmidt rối; Sc = Đại lượng nguồn diễn biến phản ứng (s-1). Biến diễn biến phản ứng được định nghĩa như sau: n i i 1 n i ,eq i 1 Y c Y = = = (2.76) Trong đó: n = Số lượng các chất trong sản phẩm; Yi = Nồng độ khối lượng của chất i trong sản phẩm; Yi,eq = Nồng độ khối lượng của chất i trong sản phẩm ở trạng thái cân bằng. Theo định nghĩa này thì: c = 0: hỗn hợp chưa cháy; c = 1: hỗn hợp đã cháy; c được định nghĩa như một giá trị điều kiện biên đối với tất cả dòng chảy vào hệ thống. Nó thường được đặc trưng bởi hai giá trị hoặc 0 (chưa cháy) hoặc 1 (cháy). Tốc độ trung bình của phản ứng được mô hình hóa như sau [59]. 𝜌𝑆𝑐 = 𝜌𝑢𝑆𝑡|𝛻𝑐| (2.77) Trong đó: u = khối lượng riêng của hỗn hợp chưa cháy; St = tốc độ màng lửa rối. 2.3.2. Lan tràn màng lửa 48 2.3.2.1. Tốc độ lan tràn màng lửa Buồng cháy động cơ giả định có hình dạng bất kỳ được đặc trưng bởi không gian kín có thể tích Vo (hình 2.2). Gọi Vb là thể tích hỗn hợp khí cháy, thể tích khí chưa cháy được xác định theo biểu thức sau: u o bV V V= − (2.78) Gọi u là khối lượng riêng của khí chưa cháy, ta có: ( )u o b um V V = − (2.79) Tốc độ tiêu thụ hỗn hợp mới: u u b o b u dm d dV (V V ) dt dt dt = − − (2.80) Nếu gọi A là diện tích bề mặt màng lửa, Sn là tốc độ cháy cơ bản (vuông góc với bề mặt màng lửa), tốc độ tiêu thụ hỗn hợp được tính theo biểu thức: u u n dm A S dt = − (2.81) Từ (2.80) và (2.81), ta có: 1 b o b u n u dV V V d S A dt A dt − = − (2.82) Giả sử khí chưa cháy chịu nén đoạn nhiệt, uup C = (p: áp suất trong buồng cháy), tốc độ cháy cơ bản (2.82) có thể tính theo áp suất p: b o b n u dV V V1 1 dp S A dt A p dt − = − (2.83) Đại lượng thứ nhất bên phải của biểu thức (2.83) là tốc độ lan tràn màng lửa tuyệt đối Ss, đại lượng thứ hai là tốc độ dịch chuyển màng lửa do khí cháy giãn nở Sg, ta có: n s gs s s= − (2.84) Trong đó: b s dV1 S A dt = (2.85) o b g u V V 1 dp S A p dt − = (2.86) 49 Tốc độ cháy cơ bản Sn là thông số quan trọng trong tính toán quá trình cháy của hỗn hợp đồng nhất. 2.3.2.2. Các công thức thực nghiệm tốc độ cháy cơ bản Tốc độ cháy cơ bản phụ thuộc nhiệt độ và áp suất theo đề xuất của Meghalchi và Keck. 𝑆𝑛 = 𝑆𝑛,𝑟𝑒𝑓 ( 𝑇𝑢 𝑇𝑢,𝑟𝑒𝑓 ) 𝛾 ( 𝑝𝑢 𝑝𝑢,𝑟𝑒𝑓 ) 𝛽 (2.87) Trong phương trình 2.87, Tu và pu là nhiệt độ và áp suất của hỗn hợp khí chưa cháy trước màng lửa, Tu,ref = 298K và pu,ref = 1atm. Tốc độ màng lửa chảy tầng tham chiếu, Ul,ref được tính như sau: ( ) 2 ,ref 1 2 3C CnS C= + − (2.88) Trong đó là hệ số tương đương trước màng lửa; C1, C2 và C3 là những hằng số đặc trưng nhiên liệu. Các số mũ , được tính toán như sau: 2,18 0,8( 1) 0,16 0,22( 1) = − − = − + − (2.89) Tốc độ màng lửa chảy tầng Meghalchi-Keck được tính sẵn đối với hỗn hợp nhiên liệu-không khí của methane, methanol, propane, iso-octane và nhiên liệu indolene. R. Stone và A. Clarke [65] đã tiến hành thí nghiệm xác định tốc độ cháy chảy tầng của hỗn hợp nhiên liệu CH4 được làm bẩn bởi CO2 và không khí. Nếu gọi nhiệt độ và áp suất không thứ nguyên T=Tu/To và p=pu/po, trong đó Tu, pu là nhiệt độ và áp suất của hỗn hợp khí chưa cháy; To và po là nhiệt độ và áp suất ở điều kiện lập bảng thì tốc độ cháy chảy tầng của hỗn hợp methane không khí có thể được xác lập bởi biểu thức bán thực nghiệm sau: Sn=0,366 T1,42 p- 0,297 (m/s) (2.90) Theo Rallis và Garforth [65] mối quan hệ giữa tốc độ cháy chảy tầng của hỗn hợp methane/không khí ở điều kiện cháy hoàn toàn được biểu diễn bằng biểu thức: Sn= Sn,o T (2.91) Trong đó o nằm trong khoảng 1,37 và 2,33. 50 Mới đây Hill và Hung [65] đối với điều kiện cháy hoàn toàn tìm ra số mũ của T là 1,80. Iijima và Takedo [65] tìm ra biểu thức tổng quát sau: =1,60+0,22( - 1) (2.92) Sự phụ thuộc tốc độ cháy chảy tầng của hỗn hợp methane/không khí vào áp suất ở điều kiện cháy hoàn toàn được Andrew và Bradley [65] xác lập như sau: Sn= 43,3P-0,5(cm/s) (2.93) (với áp suất được tính theo bar) Số mũ của p thay đổi nhẹ theo các tác giả nghiên cứu hỗn hợp cháy methane/không khí. Rallis và Garforth [65] đề nghị = - 0,3 ở điều kiện áp suất 1 bar, trong khi đó Hill and Hung [65] đề nghị = - 0,299 đối với áp suất nằm trong khoảng 0.2 đến 1 bar. Iijima và Takedo [65] đề nghị biểu thức tổng quát sau: 𝑆𝑛 = 𝑆𝑛,𝑜𝑇 𝛼(1 + 𝛽𝑙𝑜𝑔10𝑝) (2.94) Trong đó = - 0,42-0,31( - 1). 2.3.2.3. Tốc độ màng lửa rối Vấn đề mấu chốt trong mô hình hóa quá trình cháy hỗn hợp hòa trộn trước là dự đoán tốc độ màng lửa rối St, vuông góc bề mặt màng lửa. Tốc độ màng lửa rối chịu ảnh hưởng bởi các yếu tố sau: - Tốc độ màng lửa cơ bản được xác định theo nồng độ nhiên liệu, nhiệt độ và các tính chất khuếch tán phân tử cũng như chi tiết về động hóa học; - Độ nhăn nheo bề mặt màng lửa khi xoáy rối lớn và bề dày màng lửa khi xoáy rối nhỏ. Trong FLUENT, tốc độ màng lửa rối được tính toán dựa vào mô hình về độ nhăn nheo cũng như bề dày màng lửa [59]: 𝑆𝑡 = 𝐴(𝑢 ′)3/4𝑆𝑛 1/2 𝛼−1/4𝑙𝑡 1/4 = 𝐴𝑢 ′( 𝜏𝑡 𝜏𝑐 ) 1/4 (2.95) Trong đó: A = Hằng số mô hình; u’ = Độ lệch bình phương tốc độ (m/s); Sn = Tốc độ đo cháy cơ bản (m/s); 51 =k/ cp = Hệ số truyền nhiệt phân tử (khuếch tán nhiệt) (m2/s); lt = Thang độ dài rối (m); t=lt/u’= Thang thời gian rối (s); 2/c lU = = Thang thời gian hóa học (s). Thang độ dài rối lt được tính từ biểu thức: 3 t D ( u') l C = (2.96) Trong đó là tốc độ tiêu tán động năng rối. Mô hình dựa vào giả định cân bằng rối kích thước nhỏ bên trong màng lửa chảy tầng, kết quả là trong biểu thức màng lửa chảy rối chỉ chứa thuần túy các thông số rối kích thước lớn. Theo [59] thì A=0,52; CD=0,37 phù hợp với phần lớn ngọn lửa hòa trộn trước. Mô hình đạt được độ chính xác cao khi xoáy rối nhỏ nhất của dòng chảy (kích thước Kolmogorov) nhỏ hơn độ dày của màng lửa. Đó gọi là vùng phản ứng mỏng được đặc trưng bởi chuẩn số Karlovitz, Ka, lớn hơn đơn vị. Ka được định nghĩa như sau: 2 2 l a n t v K t S = = (2.97) Trong đó: tl = Độ lớn thời gian đặc trưng của màng lửa; t = Độ lớn thời gian rối nhỏ nhất (Kolmogorov); 4/1)(v = = Tốc độ Kolmogorov; = Độ nhớt động học. 2.4. Mô hình cháy đồng nhất cục bộ Quá trình cháy đồng nhất cục bộ diễn ra trong hỗn hợp nhiên liệu-không khí có hệ số tương đương không đồng nhất hoàn toàn do quá trình hòa trộn không hoàn hảo. Mô hình này phù hợp với động cơ sử dụng nhiên liệu hybrid. Mô hình cháy đồng nhất cục bộ trong FLUENT là sự kết hợp đơn giản của mô hình cháy hỗn hợp không đồng nhất và mô hình cháy hỗn hợp đồng nhất. Biến số 52 diễn tiến phản ứng cháy hòa trộn trước c xác định vị trí màng lửa. Phía sau màng lửa (c=1), chứa hỗn hợp cháy và mô hình thành phần hỗn hợp trạng thái cân bằng hay của màng lửa mỏng được sử dụng. Phía trước màng lửa (c=0), thành phần khối lượng các chất, nhiệt độ và khối lượng riêng được tính toán theo thành phần hỗn hợp hòa trộn nhưng không cháy. Trong màng lửa (0 < c < 1), sự phối hợp tuyến tính giữa hỗn hợp cháy và hỗn hợp chưa cháy được sử dụng. Mô hình cháy hòa trộn trước cục bộ giải phương trình chuyển đối với biến diễn tiến phản ứng trung bình c (để xác định vị trí màng lửa), cũng như thành phần hỗn hợp trung bình f và độ lệch bình phương của f , 2f ' . Phía trước màng lửa (c=0), nhiên liệu và chất oxy hóa được hòa trộn với nhau nhưng không cháy và phía sau màng lửa (c=1), hỗn hợp cháy. Các đại lượng trung bình theo trọng số khối lượng riêng (như thành phần các chất và nhiệt độ), ký hiệu là , được tính từ hàm số mật độ xác suất (pdf) của f và c như sau: 1 1 0 0 ( f ,c )p( f ,c )dfdc = (2.98) Với giả thiết màng lửa mỏng, chỉ tồn tại các chất tham gia phản ứng và sản phẩm cháy, các đại lượng trung bình được tính như sau: 1 1 b u 0 0 c ( f )p( f )df (1 c ) ( f )p( f )df = + − (2.99) Trong đó b và u theo thứ tự chỉ chất cháy và chưa cháy. Các đại lượng cháy, b là hàm số của thành phần hỗn hợp và được tính toán bằng cách hòa trộn một khối lượng f nhiên liệu và một khối lượng (1-f) của chất oxy hóa và cho phép hỗn hợp cân bằng. Khi xét hỗn hợp không đoạn nhiệt hoặc/và màng lửa mỏng chảy tầng, b cũng là hàm số của enthalpy hoặc sức căng nhưng điều này không làm thay đổi biểu thức cơ bản. Các đại lượng chưa cháy, u , được tính toán tương tự bằng cách hòa trộn một khối lượng f nhiên liệu với (1-f) chất oxy hóa nhưng không xảy ra phản ứng. Cũng như mô hình không hòa trộn trước, các tính toán hóa học và tích phân pdf đối với hỗn hợp khí cháy được tiến hành trong FLUENT và bảng dữ liệu được 53 xác lập. Dao động rối đối với hỗn hợp khí chưa cháy được bỏ qua, vì vậy các đại lượng chưa cháy trung bình u chỉ là những hàm số của f . Khối lượng riêng của hỗn hợp khí chưa cháy, nhiệt độ, nhiệt dung riêng và khuếch tán nhiệt được xấp xỉ bằng đa thức bậc ba của f theo phương pháp bình phương cực tiểu. 3 n u n n 0 c f = = (2.100) Vì các đại lượng chưa cháy biến thiên đều và chậm theo f nên những đa thức này thường đảm bảo được độ chính xác. 2.5. Kết luận Cháy rối là một quá trình rất phức tạp. Do môi trường rối xảy ra phản ứng hóa học nên các phần tử thay đổi từ nhiên liệu và chất oxy hóa ban đầu thành sản phẩm cháy thông qua hàng loạt các phản ứng hóa học. Để đơn giản hóa bài toán phản ứng trong môi trường chảy rối, các nhà khoa học đã đưa ra các mô hình cháy phù hợp với sự tương tác giữa nhiên liệu và chất oxy hóa. Hai mô hình cơ bản, đó là cháy của hỗn hợp không đồng nhất và cháy của hỗn hợp đồng nhất. Đối với động cơ sử dụng nhiên liệu hybrid thì mô hình cháy hỗn hợp đồng nhất cục bộ phù hợp với bản chất của quá trình cung cấp nhiên liệu. Mô hình cháy đồng nhất cục bộ là mô hình trung gian giữa cháy hỗn hợp không đồng nhất và cháy của hỗn hợp đồng nhất. Quá trình cháy được biểu diễn thông qua hai đại lượng bảo toàn, đó là thành phần hỗn hợp f và diễn tiến quá trình cháy c. Vị trí màng lửa và các thông số đặc trưng của quá trình cháy có thể được xác định thông qua hai thông số này. Trong tính toán quá trình cháy nhiên liệu hybrid biogas-xăng trình bày ở chương sau chúng tôi sử dụng mô hình cháy hỗn hợp đồng nhất cục bộ. 54 CHƯƠNG 3: MÔ PHỎNG QUÁ TRÌNH CẤP NHIÊN LIỆU VÀ QUÁ TRÌNH CHÁY TRONG ĐỘNG CƠ SỬ DỤNG NHIÊN LIỆU HYBRID BIOGAS/XĂNG 3.1. Mục tiêu, đối tượng mô phỏng Tính toán mô phỏng quá trình cung cấp nhiên liệu và quá trình cháy để định hướng việc cải tạo động cơ và nghiên cứu thực nghiệm. Mô phỏng được thực hiện trên động cơ DA465QE khi sử dụng nhiên liệu hybrid biogas-xăng. Động cơ DA465QE lắp trên xe tải nhẹ Thaco Towner 750kg. Đây là sản phẩm được sản xuất và lắp ráp trên dây chuyền hiện đại của Nhà máy ô tô Chu Lai-Trường Hải. Động cơ có đường kính xi lanh 65,5 mm; hành trình piston 72 mm; đạt công suất 35 kW ở tốc độ 5000 vg/ph và mô men 72 Nm ở tốc độ 3500 vg/ph khi chạy bằng xăng. Thông số kỹ thuật của xe được trình bày ở bảng 3.1. Bảng 3.1: Thông số kỹ thuật của động cơ DA465QE Tên thông số Ký hiệu Thứ nguyên Giá trị Công suất có ích Ne Kw 35 Tỷ số nén - 9 Tốc độ định mức n vòng/ phút 5000 Đường kính xi lanh D mm 65,5 Hành trình piston S mm 72 Chiều dài thanh truyền L mm 112 Mô men xoắn cực đại/ tốc độ quay - - 72Nm/3500vg/ph Số xi lanh i - 4 Số kỳ - 4 Động cơ DA465QE là loại động cơ phun xăng điều khiển điện tử, 4 xi lanh thẳng hàng, làm mát cưỡng bức. So với đường đặc tính của băng thử công suất APA thì đường đặc tính của động cơ DA465QE hoàn toàn nằm trong phạm vi làm việc của băng thử. 55 Định hướng nghiên cứu của luận án này là sử dụng biogas nghèo để giảm sự lệ thuộc vào hệ thống lọc nhiên liệu. Biogas thông thường chứa khoảng 60% - 80% Mê tan (M6C4, M7C3, M8C2), phụ thuộc nguyên liệu đầu vào. Với biogas chưa qua lọc thì công suất động cơ giảm khoảng 30-40%. Điều này có nghĩa là công suất động cơ chỉ còn khoảng 60% - 70% công suất cực đại so với khi chạy bằng xăng. Trong thực tế phần lớn thời gian ô tô vận hành tải thấp và trung bình. Vì vậy, phần lớn thời gian ô tô có thể chạy bằng biogas. Khi cần gia tốc, vượt chướng ngại, lên dốc thì hệ thống cung cấp xăng sẽ hỗ trợ giúp gia tăng công suất động cơ để cân bằng với công suất cản. Luận án tập trung nghiên cứu mô phỏng tại tốc độ 3000 vòng/phút và 5000 vòng/phút vì đây là phạm vi vận hành thường xuyên của ô tô tải nhẹ Towner. Biogas chứa thành phần chính là CH4 và tạp chất CO2. Thông thường thành phần CH4 dao động từ 60% đến 80%. Do có tạp chất CO2 nên tốc độ cháy của biogas thấp nhưng chỉ số octane cao, giúp hạn chế hiện tượng cháy kích nổ. Mặt khác, nhiệt trị của biogas nghèo thấp nên công suất của động cơ giảm. Xăng RON95 thương mại, có nhiệt trị cao, được sử dụng để cung cấp bổ sung vào động cơ khi cần phát công suất lớn. Bảng 3.2 so sánh các tính chất của methane, xăng và biogas nghèo (có thành phần CH4 khoảng 60%). Chúng ta thấy nhiệt trị của biogas nghèo chỉ 17 MJ/kg so với 43 MJ/kg đối với xăng. Tốc độ lan tràn màn lửa chỉ bằng khoảng 2/3 so với xăng nhưng chỉ số octane của biogas 130 cao hơn nhiều so với 95 của xăng thương mại. Bảng 3.2: Tính chất của methane, xăng và biogas nghèo (chứa 60% CH4) Tính chất Methane Xăng Biogas nghèo Công thức CH4 C8 H18 CH4+CO2 Khối lượng phân tử 16 114 - Chỉ số octane 120 95 130 Nhiệt độ tự cháy (C) 540 257 650 Tỉ số A/F lý thuyết (kg không khí/kg nhiên liệu) 17,16 14,7 5,8 Nhiệt trị thấp (MJ/kg) 47,3 43 17 Tốc độ lan tràn màn lửa chảy tầng (m/s) 0,4 0,33 0,25 Tỉ lệ phân tử C/H 0,25 0,44 - 56 3.2. Mô hình hình học của động cơ và điều kiện biên mô phỏng Để động cơ có thể chạy được bằng biogas-xăng, đường nạp động cơ được bổ sung thêm một họng venturi và vòi phun biogas. Mô hình không gian tính toán bao gồm xi lanh có thể tích thay đổi theo sự vận động của piston, buồng cháy và đường nạp vào xi lanh khảo sát. Đường nạp và buồng cháy tại ĐCT (vị trí góc quay =0oTK) thể hiện trên hình 3.1. Mô phỏng được thực hiện nhờ phần mềm ANSYS FLUENT. Hình 3.1: Các mặt cắt khảo sát trên đường nạp Việc thiết lập mô hình tính toán được thực hiện qua các bước sau: • Thiết kế không gian tính toán trên cơ sở kích thước động cơ và bổ sung thêm bộ tạo hỗn hợp. Thiết kế được thực hiện nhờ phần mềm Solidwork. • Chia không gian tính toán thành 3 thể tích chính: xi lanh, buồng cháy và đường nạp. Xi lanh và buồng cháy được ngăn cách bởi piston; buồng cháy và đường nạp được ngăn cách bằng xú páp nạp. • Thiết lập các van cung cấp nhiên liệu bằng cách chia vòi phun thành hai phần: phần trước van và phần sau van. Mặt ngăn cách các thể tích này được định dạng interior (khi van mở) và wall (khi van đóng). 57 • Chia lưới không gian tính toán: áp dụng phương pháp chia lưới tự động trong Ansys workbench để chia lưới các thể tích khác nhau trong không gian tính toán (hình 3.2). • Cài đặt các thông số động cơ, xác định không gian biến dạng của xi lanh và mặt di chuyển của piston trong menu Dynamic mesh. • Thiết lập thời điểm đóng, mở xú páp nạp; thời điểm đóng, mở của van cấp biogas trong menu Event của Dynamic mesh. • Lựa chọn mô hình chảy rối k- tiêu chuẩn. • Thiết lập thông số các dòng cung cấp nhiên liệu biogas và xăng. • Tính bảng nhiệt động học pdf. • Thiết lập điều kiện biên gồm: áp suất, nhiệt độ, thành phần nhiên liệu đi vào cửa nạp và đi vào các vòi phun. • Khai báo thành phần, nhiệt độ, áp suất khí sót. • Xác lập chế độ hiển thị kết quả tính toán. Hình 3.2: Chia lưới không gian tính toán và đặc trưng của các phần tử 58 Bảng 3.3. Các giá trị tính của điều kiện biên mô phỏng Thông số Đơn vị Giá trị Tốc độ động cơ (n) vg/ph 2000; 3000; 4000; 5000; 6000 7000. Thành phần biogas % mol M6C4; M7C3; M8C2; M100 Hàm lượng xăng bổ sung vào biogas % mol G0; G5; G10; G15; G20; G30; G100 Góc mở bướm ga (BG) () 0; 30; 45; 60 Trong quá trình tính toán, chúng ta thay đổi tốc độ động cơ, thành phần nhiên liệu, áp suất nhiên liệu, phương thức cung cấp nhiên liệu, vị trí bướm ga (Bảng 3.3) ... Kết quả thể hiện gồm biến thiên tốc độ dòng khí, áp suất, thành phần hỗn hợp, hệ số tương đương Các kết quả được ghi lại dưới dạng file số liệu để xử lý tiếp bằng Excel. Hình 3.3: Ảnh chụp màn hình diễn biến các thông số trong xi lanh động cơ Biến thiên các thông số của quá trình cung cấp nhiên liệu được thể hiện trên các mặt cắt: - Mặt cắt dọc xy chứa trục xi lanh và trục đường nạp; - Mặt cắt zy chứa trục xi lanh. Các mặt cắt ngang đường nạp S1, S2, S3, S4, S5 được xác lập tại các vị trí có thay đổi tiết diện như hình 3.1. Hình 3.3 là ảnh chụp màn hình diễn biến các thông số trong xi lanh động cơ của một trường hợp tính toán tiêu biểu. 59 Trong chu trình nhiệt động của động cơ, khí nạp được hút vào từ đường nạp theo điều kiện khí trời, khí sót còn lại trong buồng cháy là kết quả của chu trình trước đó. Thành phần, nhiệt độ, áp suất khí nạp, khí sót, biogas được thể hiện bảng 3.4. Bảng 3.4: Điều kiện ban đầu mol/mol O2 N2 CO2 H2O C8H18 CH4 Nhiệt độ (K) Áp suất dư (Pa) Khí nạp 0,21 0,79 0 0 0 0 300-375 0 Khí sót 0 0,77 0,14 0,09 0 0 550-700 1000 Biogas 0 0 0,2-0,4 0 0 0,6-0,8 310 2000-5000 3.3. Kết quả mô phỏng quá trình cung cấp nhiên liệu hybrid biogas-xăng (a) (b) Hình 3.4: Biến thiên đường đồng mức áp suất, nồng độ CH4 và C8H18 trong quá trình nạp (n=3000 vòng/phút, biogas M7C3, góc phun xăng 30-60, góc phun biogas 60- 110) 60 Hình 3.4a giới thiệu các đường đồng mức áp suất tĩnh trên đường nạp. Chúng ta thấy trong suốt kỳ nạp, độ chân không trên đường nạp lớn nhất xuất hiện ngay tại họng venturi và lan về phía hạ lưu. Mặt cắt số 3 là vùng có độ chân không lớn nhất. Về cuối quá trình nạp, khi xú páp nạp bắt đầu đóng lại thì áp suất vùng gần xú páp tăng. Đây là do quán tính của dòng khí. Hình 3.4b biểu diễn đường đồng mức nồng độ nhiên liệu CH4 và C8H18. Biogas được phun bằng hai vòi phun đối xứng bố trí ngay tại họng venturi. Thời điểm mở vòi phun là 60TK và đóng vòi phun tại 110TK. Vòi phun xăng mở tại 30TK và đóng tại 60TK. Sau khi nhiên liệu thoát ra khỏi các vòi phun chúng bị dòng khí kéo theo vào xi lanh. Do tia phun xăng là tia 2 pha nên sau khi phun, các hạt nhiên liệu bốc hơi mới hòa trộn với không khí. Do thời gian phun ngắn và vòi phun được bố trí gần xú páp nạp nên nhiên liệu xăng nhanh chóng được hút vào xi lanh. Trong khi đó CH4 trong biogas có sự chậm trễ nhất định. Cuối quá trình nạp, sau khi xú páp nạp đã đóng, trên đường nạp vẫn còn một tỉ lệ đáng kể CH4 chưa kịp hút hết vào xi lanh. (a) (b) Hình 3.5: Biến thiên áp suất trên các mặt cắt ngang đường nạp khi động cơ chạy ở tốc độ 2000 vòng/phút (a) và 5000 vòng/phút (b) (BG=0, không phun nhiên liệu) Hình 3.5a và hình 3.5b cho thấy độ chân không tại tiết diện S3 lớn nhất trong số các mặt cắt ngang khảo sát. Khi tốc độ tăng thì độ chân không tăng theo, đồng thời biên dạng đường cong áp suất mở rộng. Độ chân không cực đại tại mặt cắt 3 khi động 61 cơ chạy ở tốc độ 5000 vòng/phút gấp 3 lần độ chân không cực đại tại mặt cắt này khi động cơ chạy ở tốc độ 2000 vòng/phút. (a) (b) Hình 3.6: Biến thiên áp suất trên các mặt cắt ngang của đường nạp khi động cơ chạy ở tốc độ 2000 vòng/phút (a) và 5000 vòng/phút (b) (BG=30, không phun nhiên liệu) Hình 3.6a và hình 3.6b giới thiệu áp suất tại mặt cắt số 3 khi động cơ chạy ở các tốc độ khác nhau ở chế độ toàn tải và ở chế độ tải cục bộ (BG=30). Chúng ta thấy các đường cong không thay đổi nhiều khi thay đổi tải động cơ tuy nhiên giá trị tuyệt đối của áp suất thay đổi đáng kể. Trung bình độ chân không giảm 20% khi bướm ga đóng 30 so với khi mở hoàn toàn. (a) (b) Hình
File đính kèm:
luan_an_nghien_cuu_qua_trinh_chay_va_phat_thai_o_nhiem_dong.pdf
0.Phụ lục Bìa luận án-VoAnhVu.pdf
2. Tóm tắt tiếng việt-VoAnhVu.pdf
3. Toám tắt tiếng Anh-VoAnhVu.pdf
4. Thông tin đóng góp mới tiếng việt-VoAnhVu.pdf
5. Thông tin đóng góp mới tiếng anh-VoAnhVu.pdf
6. Trích yếu luận án tiếng việt-VoAnhVu.pdf
7. Trích yếu luận án tiếng anh-VoAnhVu.pdf