Luận án Nghiên cứu quá trình hình thành hỗn hợp và cháy HCCI trong buồng cháy thể tích không đổi
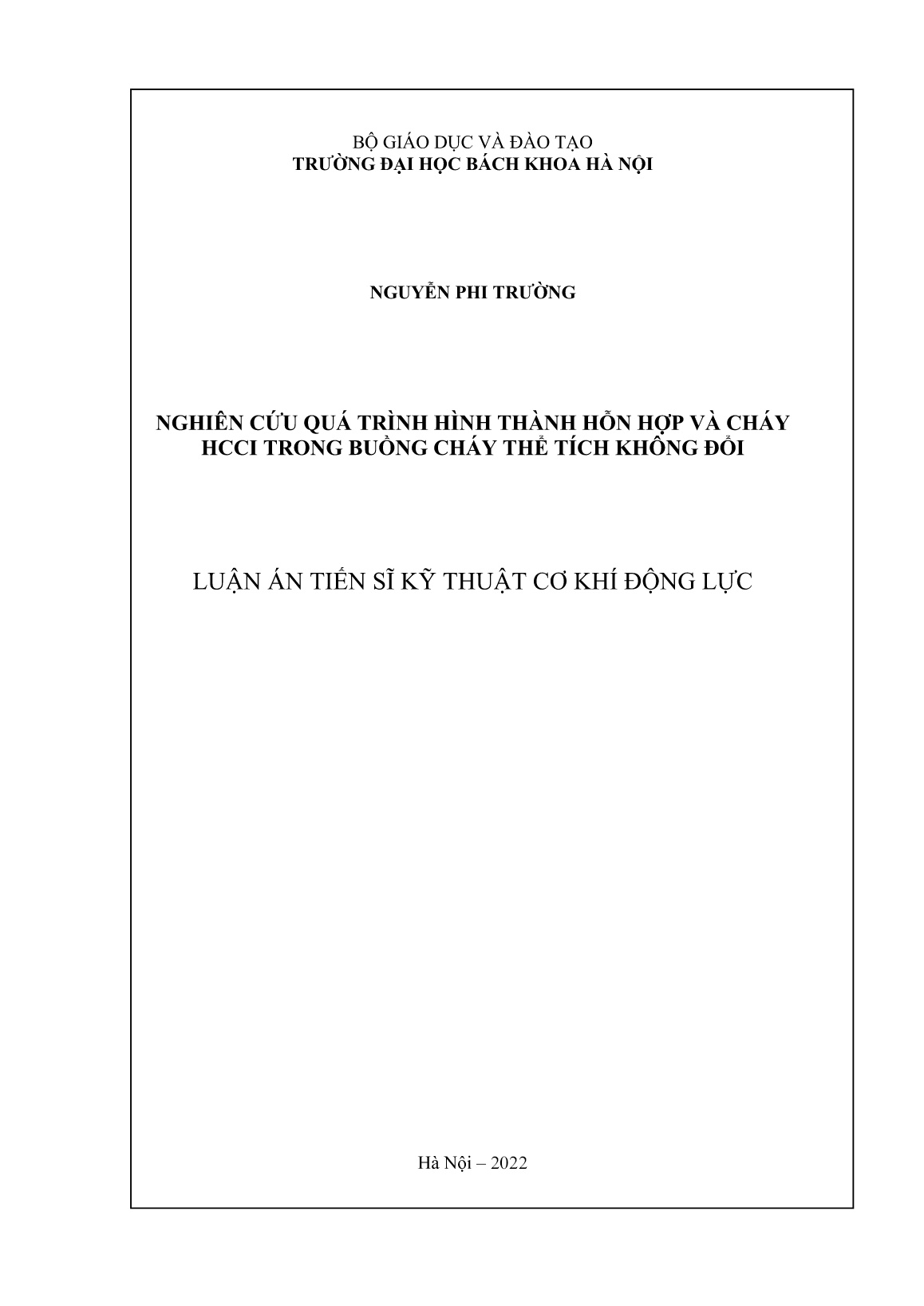
Trang 1
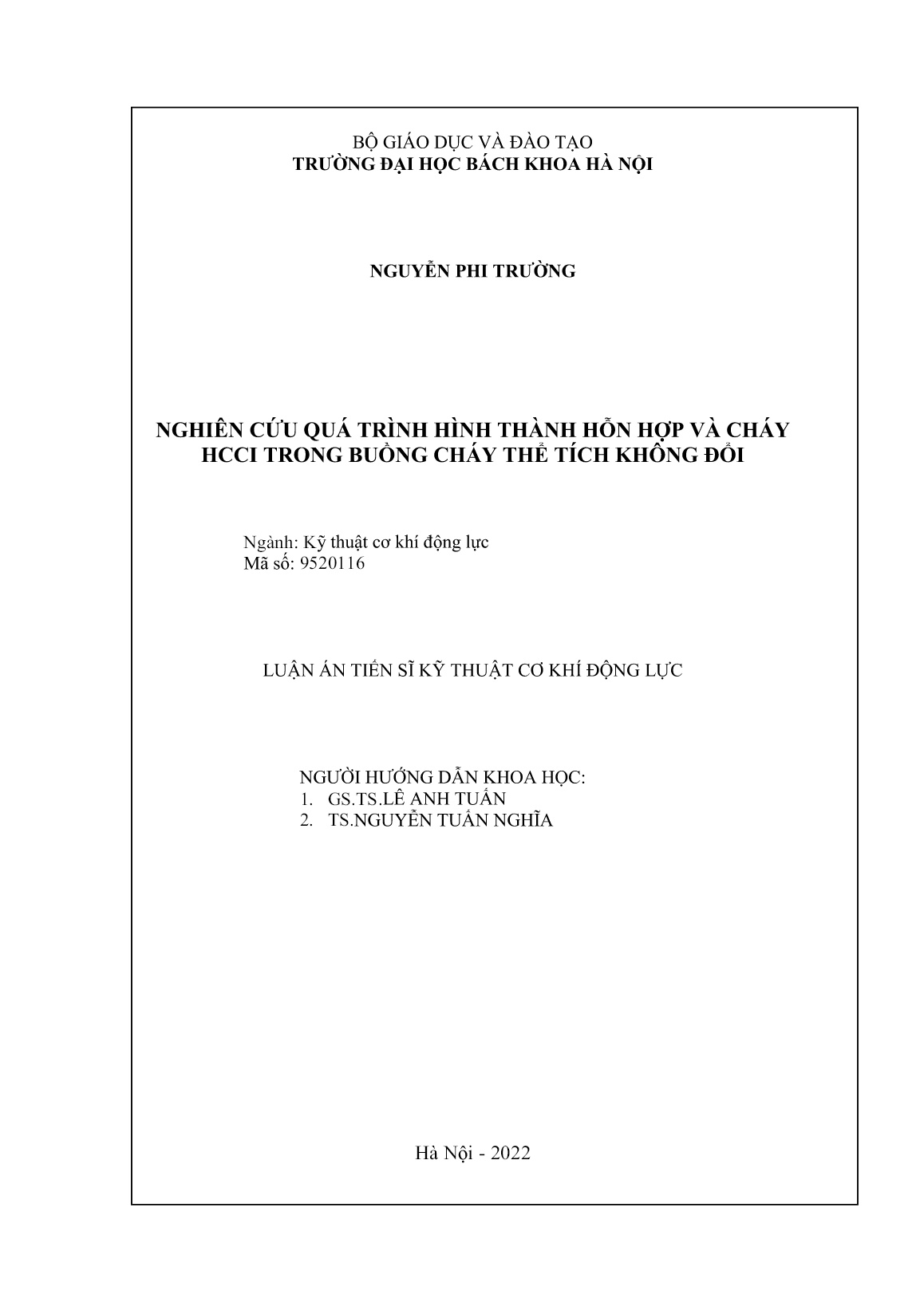
Trang 2
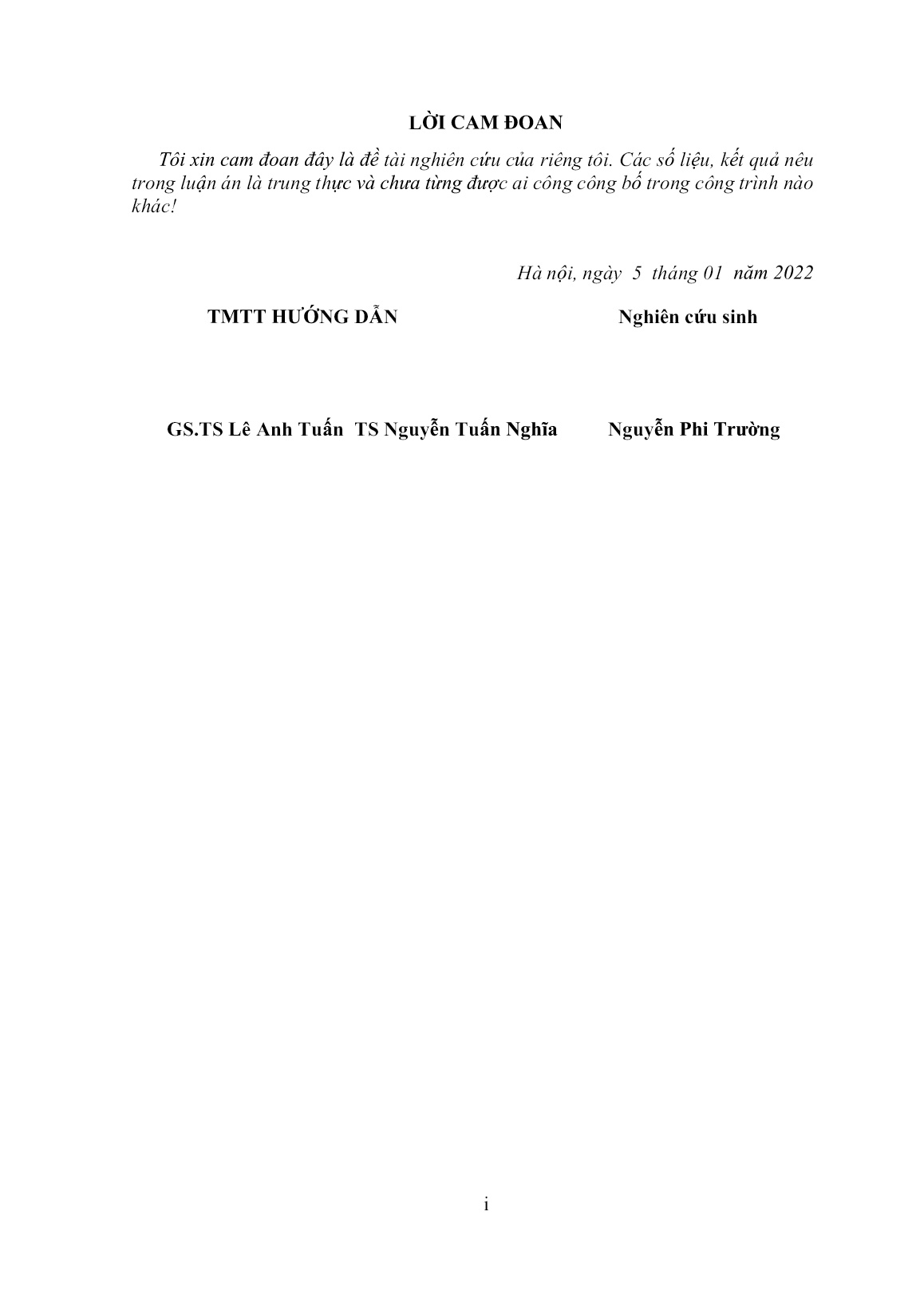
Trang 3
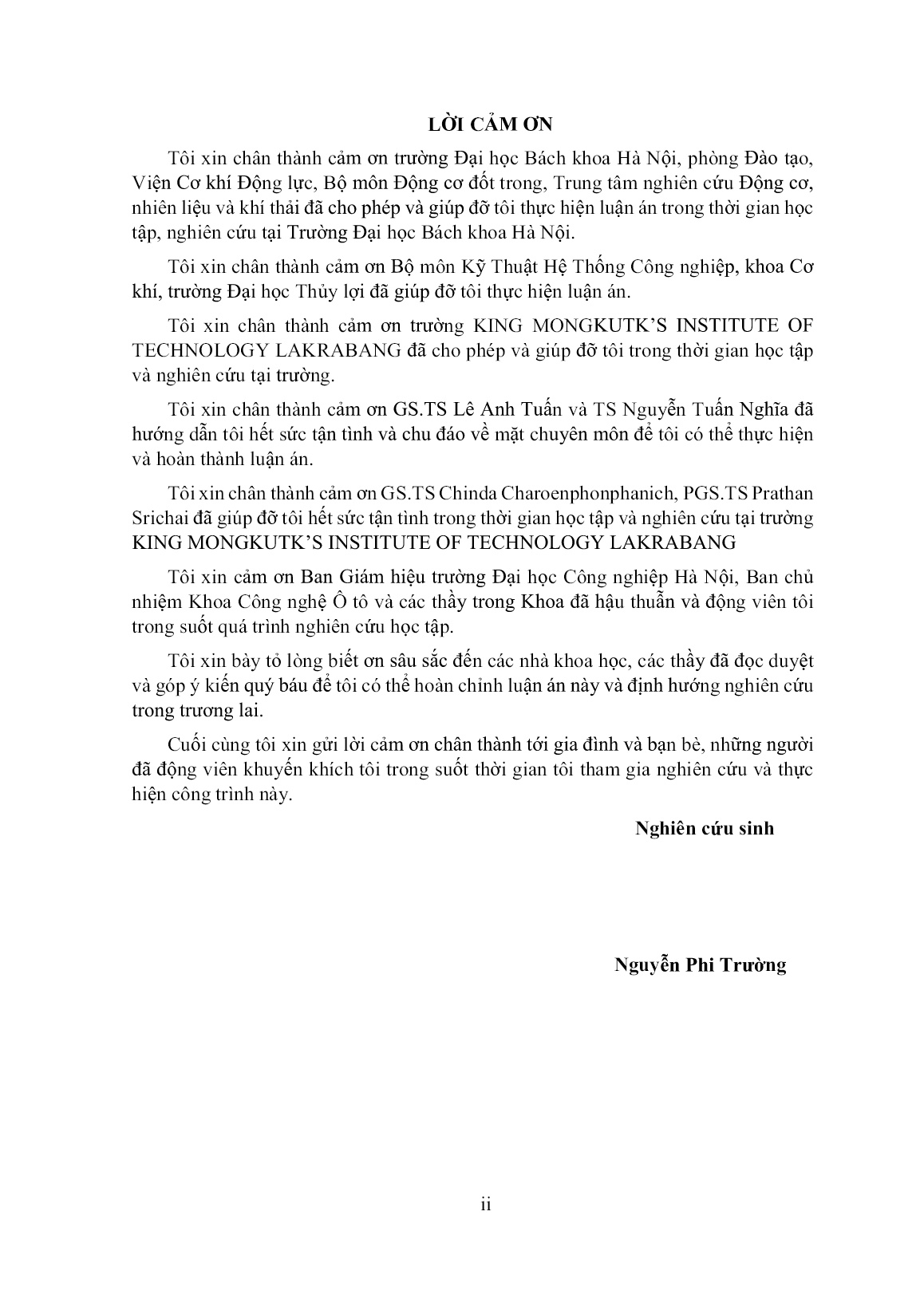
Trang 4
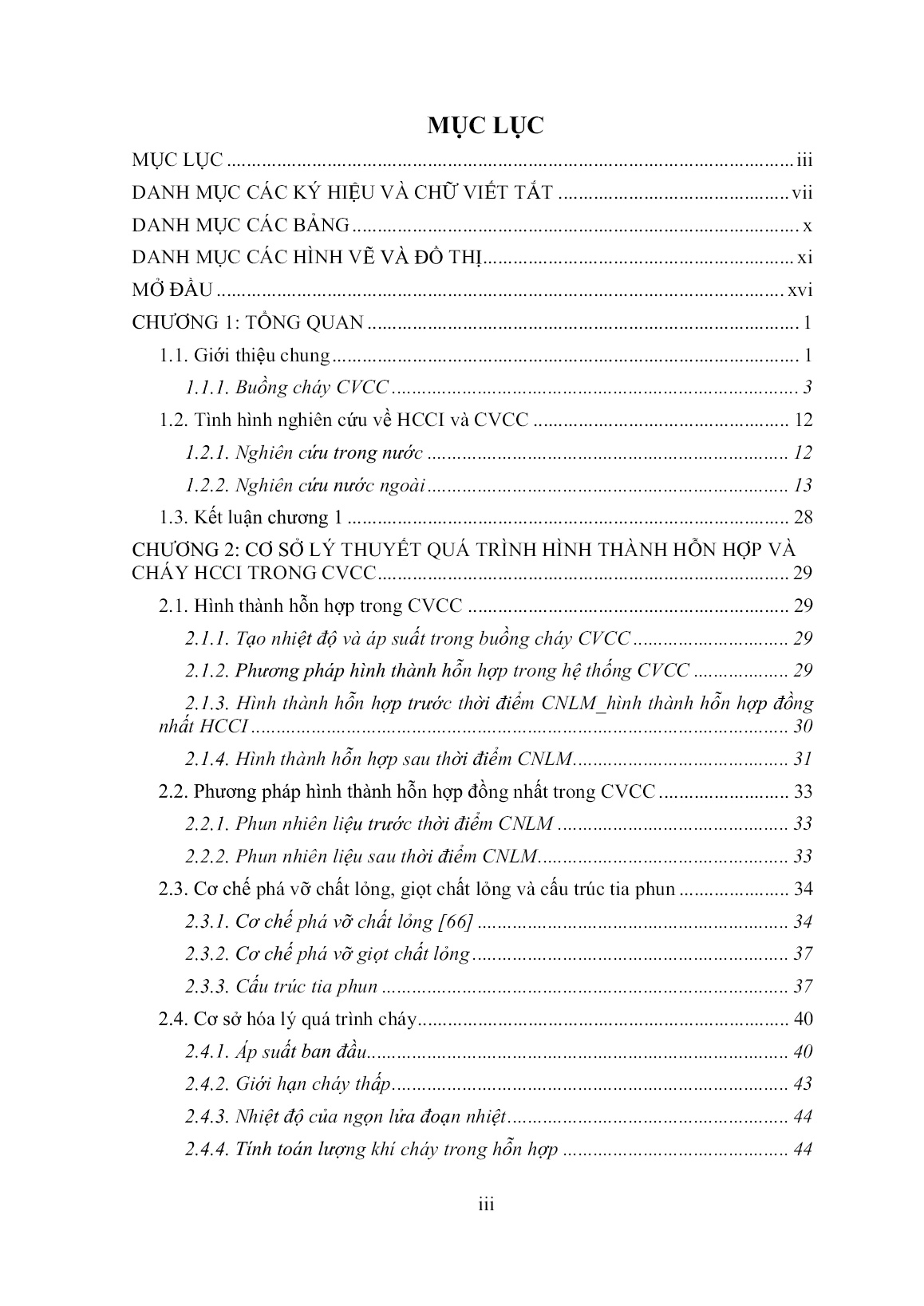
Trang 5
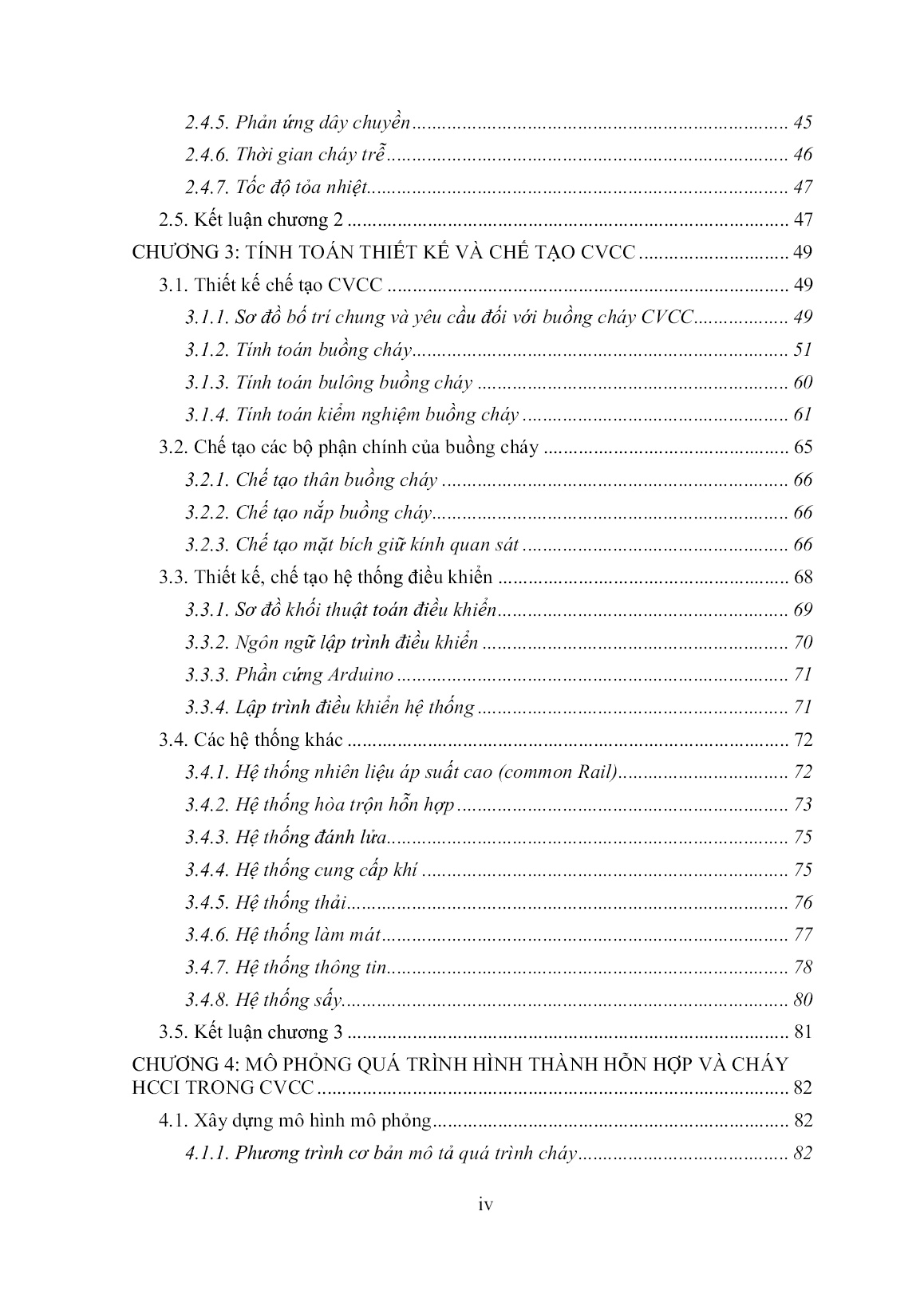
Trang 6
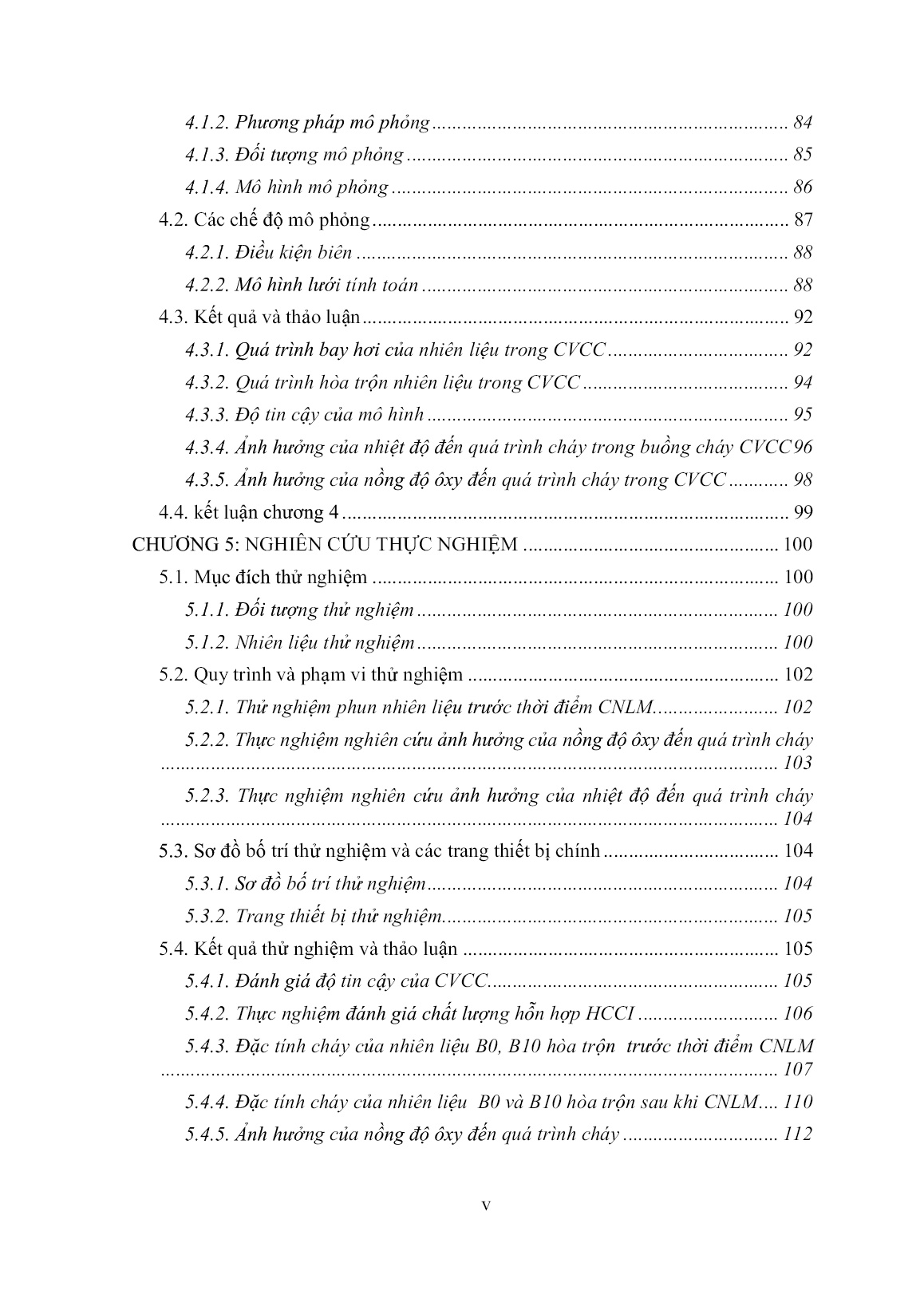
Trang 7
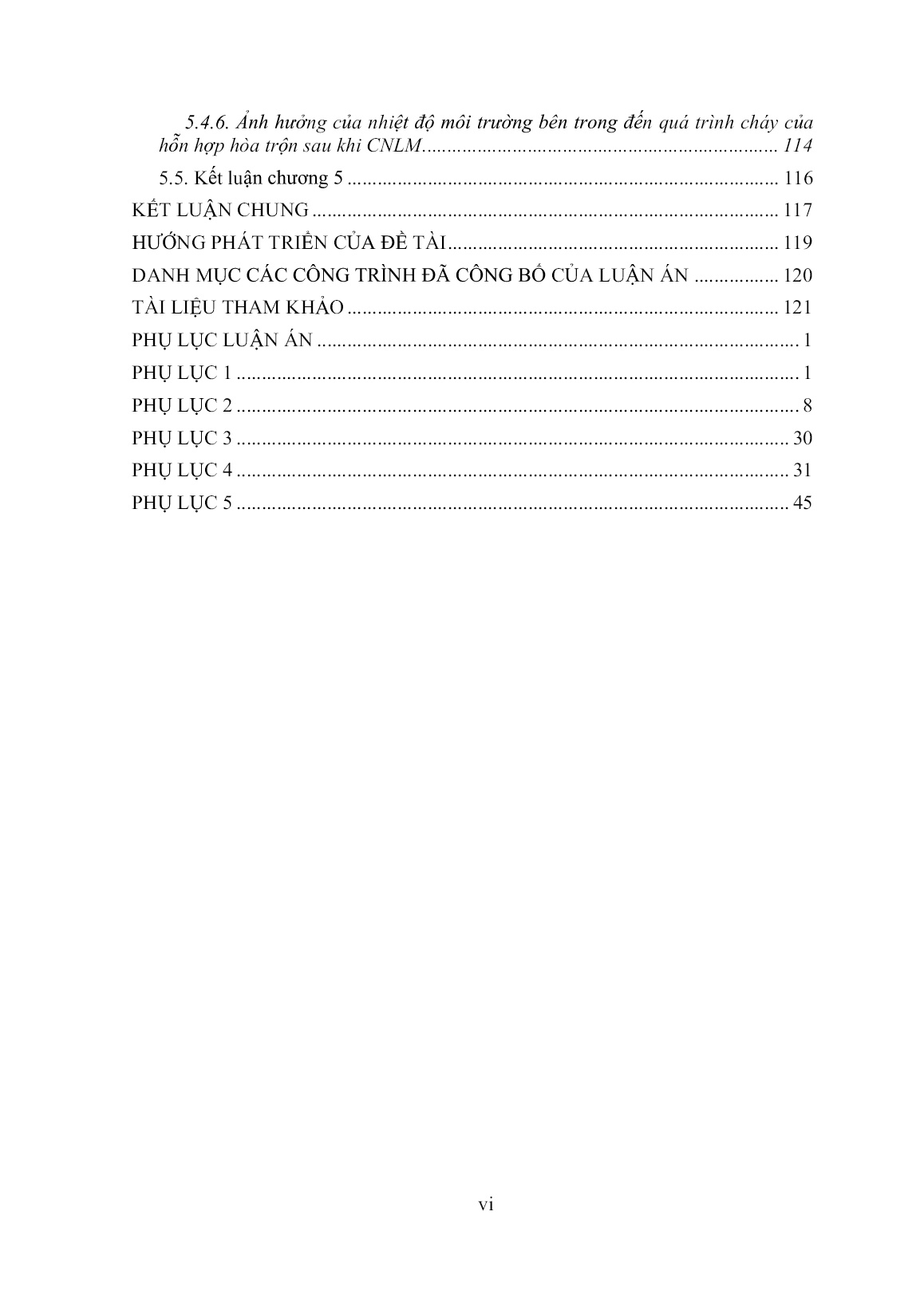
Trang 8

Trang 9
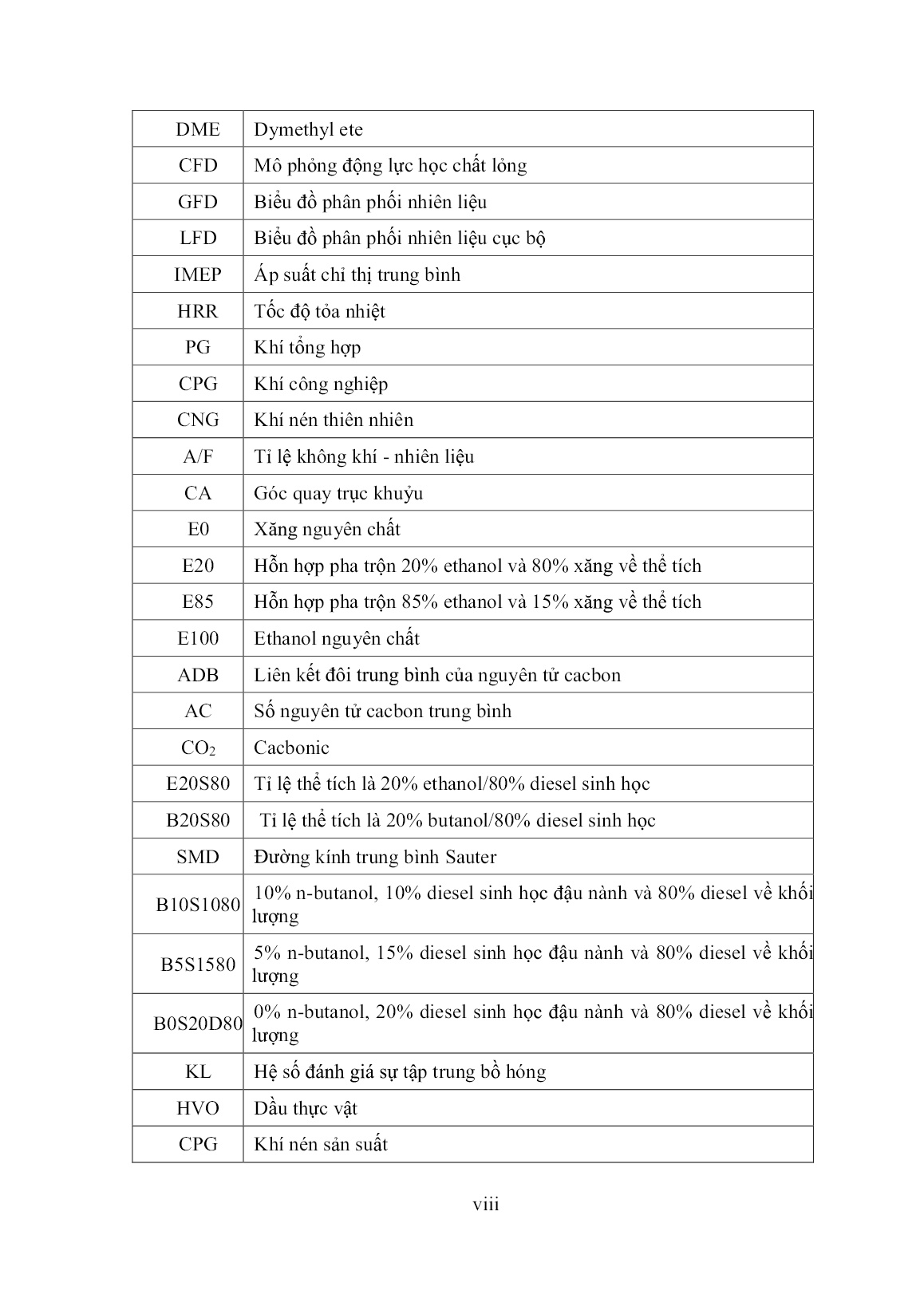
Trang 10
Tải về để xem bản đầy đủ
Bạn đang xem 10 trang mẫu của tài liệu "Luận án Nghiên cứu quá trình hình thành hỗn hợp và cháy HCCI trong buồng cháy thể tích không đổi", để tải tài liệu gốc về máy hãy click vào nút Download ở trên.
Tóm tắt nội dung tài liệu: Luận án Nghiên cứu quá trình hình thành hỗn hợp và cháy HCCI trong buồng cháy thể tích không đổi
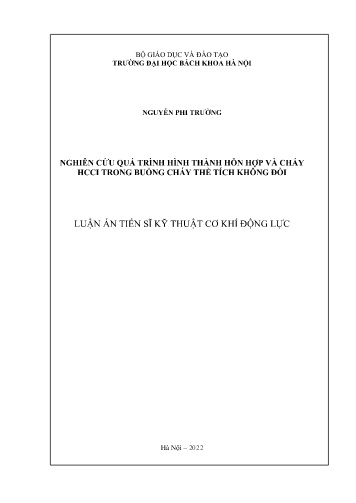
𝛥.𝑃𝑖𝑛𝑗 𝑝𝑎 ) 0.25 . ( 𝑡.𝑑𝑁 𝑡𝑎𝑛𝜃 ) 0.325 (3.3) 𝑅 = 2. 𝑋. 𝑡𝑎𝑛𝜃 (3.4) Trong đó X: chiều dài tia phun (m) Pinj: áp suất khác nhau giữa vòi phun và buồng cháy (N/m2) R: độ rộng tia phun (m) T: thời gian sau khi phun (s) C: hệ số dòng chảy DN: đường kính lỗ phun (m) ρa: mật độ khí (kg/m3) Bảng 3. 2. Điều kiện khí và đặc tính nhiên liệu sử dụng để tính toán chiều dài và góc tia phun [75] Nhiên liệu Ethanol Diesel Bio-diesel Khối lượng riêng nhiên liệu (ρf) (kg/m3) 785 848 881 Môi trường xung quanh Không khí Không khí Không khí Khối lượng riêng khí (ρa) (kg/m3) 18-32 18-32 18-32 53 Hệ số của vòi phun (Cd) 0.8 0.8 0.8 Áp suất phun (Pinj) (MPa) 150 150 150 Áp suất khí (Pg) (MPa) 4 4 4 Độ chênh lệch áp suất (dp) (MPa) 146 146 146 Thời gian phun (t) (ms) 2.5 2.5 2.5 Đường kính vòi phun (dn) (mm) 0.2 0.2 0.2 Hình 3. 3 cho thấy độ xuyên thấu và góc được tính theo biểu thức [74]. Kết quả cho thấy độ xuyên thấu tính toán và chiều rộng đầu phun đối với nhiên liệu thử nghiệm (Ethanol, diesel và diesel sinh học) giảm khi mật độ khí xung quanh tăng, trong khi góc phun cho kết quả ngược lại. Những kết quả này tương tự [76] và [15]. Sự khác biệt về đặc tính phun phụ thuộc vào mật độ nhiên liệu. Ethanol cho thấy sự thâm nhập phun dài nhất, tức là khoảng 79 mm, trong khi diesel sinh học cho thấy góc phun lớn nhất (17o) và chiều rộng đầu phun (25 mm) ở các điều kiện tính toán. Việc phun tối đa có thể có thể được rút ra như trong (Hình 3. 4). Hình 3. 3. Đặc tính của tia phun với nhiên liệu thử nghiệm [82] 54 Hình 3. 4. Kích thước lớn nhất đối với nhiên liệu thử nghiệm Thay số trong Bảng 3. 2 vào phương trình ta được: X là chiều dài tia phun (m) = 78 mm (diesel); = 77 mm (Ethanol); = 79 mm (bio diesel); R: độ rộng tia phun (m) = 26mm (diesel). Như vậy: Lựa chọn đường kính buồng cháy CVCC là 80 (mm), chiều rộng của buồng cháy lớn hơn 26 mm sẽ thỏa mãn điều kiện không bị hiện tượng sát vách. Với chiều rộng của buồng cháy như vậy sẽ không thể bố trí nhiều cụm chi tiết khác. Vì vậy, chiều rộng của buồng cháy sẽ được lựa chọn lớn hơn phù hợp bố trí các cụm chi tiết khác của buồng cháy cụ thể chọn sơ bộ chiều rộng bằng 90 (mm). Những đặc điểm phun này được sử dụng để chứng minh kích thước của buồng đốt hình tròn. Đường kính của buồng phụ thuộc vào độ xuyên thấu phun (chiều dài tia phun), trong khi chiều rộng buồng cháy phụ thuộc vào chiều rộng đầu tia phun. Đường kính và chiều rộng của buồng cháy phải bằng hoặc cao hơn chiều dài tia phun tối đa và chiều rộng đầu tia phun của nhiên liệu. Đối với chiều rộng của buồng cháy có thể lớn gấp đôi giá trị tối thiểu cần thiết để tránh nhiên liệu chạm vào tường, với chiều rộng ngoài việc phải lớn hơn kích thước tối thiểu nó còn phải bố trí nhiều thiết bị khác lên trên đó. Do đó, trong nghiên cứu này, đường kính và chiều rộng của buồng cháy hình tròn lần lượt là 80 (mm) và 90 (mm) như trong Hình 3. 5. Hình 3. 5. Hình chiếu bằng và chiếu cạnh của buồng cháy 55 3.1.2.2. Tính toán bề dày xylanh Độ dày tối ưu của buồng và cửa sổ được tính toán bằng lý thuyết và mô phỏng. Vật liệu được sử dụng cho buồng cháy CVCC và cửa sổ lần lượt là thép không gỉ S45C và thạch anh (Bảng 3. 3). Thép S45C được chọn làm vật liệu chế tạo CVCC vì đặc tính chống ăn mòn và có cường độ cao (Bảng 3. 4). Bảng 3. 3. Thông số của vật liệu làm kính quan sát Đặc tính Giá trị Đơn vị Khối lượng riêng 2210 Kg/m3 Mô đun đàn hồi 20oC 77,8 GPa Mô đun đàn hồi 50oC 82 GPa Mô đun đàn hồi 900oC 85 GPa Hệ số Poisson 0,17 Ứng suất nén tới hạn 343 MPa Độ cứng 5-7 Mhos Scale Bảng 3. 4. Thông số của vật liệu thép S45C Đặc tính Giá trị Đơn vị Độ bền kéo, giới hạn 569 MPa Khối lượng riêng 7700 Kg/m3 Hệ số Poisson 0,29 Mô đun đàn hồi 190,0 GPa Mô đun chống cắt 80,0 GPa Đối với cửa sổ quan sát, vật liệu thạch anh được chọn vì có cường độ rất cao và phạm vi truyền ánh sáng rộng. Hình dạng hình tròn tròn được lựa chọn cho CVCC. Với hình học này, nguyên lý của bình chịu áp lực thành dày được áp dụng [78]. Khi áp suất tác dụng lên bề mặt trong hình tròn thành dày, có ba loại ứng suất xảy ra trong vật liệu, đó là ứng suất Hoop hoặc ứng suất tiếp tuyến (σH), ứng suất dọc (σL) và ứng suất xuyên tâm (R), tuy nhiên ứng suất Hoop là ứng suất quan trọng nhất . Do đó, chỉ có ứng suất Hoop được sử dụng trong tính toán. Để tính toán độ dày cửa sổ, hai ứng suất được xem xét là ứng suất cắt và ứng suất uốn. Hệ số an toàn 12 được chọn cho buồng đốt và hệ số 15 cho cửa sổ thạch anh [78]. Tải trọng trên thành xylanh và cửa sổ được xác định là áp suất ở 80 bar. Trong xylanh khi có áp suất, bên trong vật liệu làm xylanh xuất hiện các ứng suất: ứng suất tiếp (H), ứng suất dài (L) và ứng suất hướng tâm (R) [78] như trên (Hình 3. 6). Tuy nhiên, trong tính toán chỉ quan tâm đến ứng suất tiếp. Ứng suất tiếp của thành xylanh được tính theo công thức 3.5 56 Hình 3. 6. Ứng suất bên trong thành xylanh [79] = 𝑃𝑐𝑦.(𝑏 2+𝑎2) (𝑏2−𝑎2) (3.5) Trong đó: : Ứng suất tiếp (MPa) Pcy: Áp lực tác dụng lên thành xylanh (MPa) a: Bán kính trong (m) b: Bán kính ngoài (m) Khí xung quanh tại TDC thu được bằng tính toán quá trình đa biến. Áp suất khí, nhiệt độ và mật độ tăng với tỉ số nén tăng. Áp suất, nhiệt độ và mật độ tại TDC lần lượt là 40-90 bar, 800-960 K và 18-32 kg/m3 đối với CR 16. Tăng tỉ số nén dẫn đến tăng áp suất, nhiệt độ và mật độ khí xung quanh tại TDC (Hình 3. 7). Thông số của vật liệu sử dụng và dữ liệu tính toán buồng cháy thể hiện trong Bảng 3. 5. Bảng 3. 5. Đặc tính vật liệu và dữ liệu tính toán bề dày thành buồng cháy Đặc tính vật liệu Thép S45C ứng suất tới hạn (Su) 343 MPa Tiêu chuẩn thiết kế Thiết kế ứng suất của vật liệu theo tải trọng động hoặc tải trọng va đập (σd) 𝑆𝑢 12 = 343 12 = 28,58 MPa Áp suất lớn nhất bên trong buồng cháy (Pcy) 8 MPa (80 bar) Bán kính ngoài buồng cháy (b, mm) Tính theo công thức 3.5 Bán kính trong buồng cháy (a, mm) 40 mm 57 Hình 3. 7. Điều kiện xung quanh TDC bởi quá trình đa biến tính toán với chỉ số đa biến (n=1,35) Từ dữ liệu đã cho, sử dụng phương trình (3.5) và Bảng 3. 5 tính được bán kính ngoài của hình tròn (b) là 57,64 mm. Tuy nhiên trên buồng cháy còn lắp ghép nhiều cụm chi tiết, thiết bị đo và ốc vít sẽ được liên kết với CVCC. Do đó, nghiên cứu lựa chọn sơ bộ độ dày thành 60 mm để cung cấp đủ độ bền cho CVCC. Sau khi tính toán ta có được kích thước sơ bộ của CVCC như trong Bảng 3. 6 Bảng 3. 6. Kích thước sơ bộ của CVCC Thông số Giá trị Đơn vị Đường kính ngoài 200 mm Đường kính trong 80 mm Chiều cao xylanh 90 mm 3.1.2.3. Tính toán kích thước kính quan sát Để tìm độ dày tối thiểu của thạch anh cho buồng cháy chịu tải 80 bar. Có bốn loại ứng suất liên quan: ứng suất pháp, ứng suất uốn, ứng suất cắt và ứng suất chống cắt của vật liệu. Bán kính của vùng quan sát được chọn là bán kính trong của buồng cháy. Đây là khu vực chịu tải trực tiếp. Bản vẽ kính kính thạch anh thể hiện trong (Hình 3. 8). 58 Hình 3. 8. Hình vẽ mặt cắt của kính thạch anh Độ dày kính thạch anh Để tìm độ dày thạch anh, hai ứng suất được xem xét, tức là ứng suất cắt và ứng suất uốn (Hình 3. 9). Ứng suất cắt và ứng suất uốn [80] có thể được tìm thấy từ phương trình sau. Ứng suất cắt 𝜏 = 𝑃𝑐𝑦.𝑎 2𝐿 (3.6) Ứng suất uốn 𝜎𝑏 = 𝑃𝑐𝑦.𝐴 4.𝐿2 (3.7) Trong đó: τ: Ứng suất cắt (MPa) 𝜎𝑏: Ứng suất uốn (MPa) a: Bán kính trong của kính (m) Pcy: Áp lực pháp tuyến lên bề mặt kính (MPa) như trong hình 3.10 A: Diện tích bề mặt (m2) chịu áp lực Pcy L: Bề dày kính (m) Hình 3. 9. Chiều dày và bề mặt kính quan sát Thông số vật liệu sử dụng làm kính quan sát được cho trong Bảng 3. 7. Bảng 3. 7. Thông số và dữ liệu tính toán cửa sổ quan sát Thuộc tính vật liệu Giá trị Thạch anh Độ bền uốn 94,3 MPa ứng suấn nén 1130 MPa 59 Độ bền kéo 49 MPa Tiêu chuẩn thiết kế Thiết kế ứng suất uốn của vật liệu với tải trọng động hoặc va đập (τd) 49 12 = 4,1 MPa Thiết kế ứng suất uốn của vật liệu với tải trọng động hoặc va đập (σBd) 0,35x1130 = 395,5 Thiết kế ứng suất pháp tuyến của vật liệu với tải trọng động hoặc va đập (τcd) 1130 15 = 75 MPa Thiết kế ứng suất chống uốn của vật liệu với tải trọng động hoặc va đập (τbd) 94,3 20 = 4,715 MPa Áp suất lớn nhất bên trong buồng cháy (Pcy) 8 MPa Bán kính trong của kính thạch anh (𝑎 = 𝐷𝑖 2 ) 47.5 mm Từ dữ liệu (Bảng 3. 7), độ dày thạch anh được tính toán. Sử dụng phương trình (3.6) để tìm độ dày của thạch anh để chống lại ứng suất cắt tính được độ dày tối thiểu của thạch anh là 33,9 mm. Để tìm độ dày của thạch anh để chống lại ứng suất uốn, phương trình (3.7) đưa ra độ dày tối thiểu cần thiết của thạch anh là 33,9 mm. Do đó, lựa chọn chiều dày sơ bộ của kính quan sát là 35 mm. Tính toán đường kính ngoài của kính quan sát Đường kính ngoài của kính quan sát có thể tính theo công thức sau: Ứng suất uốn 𝜎𝐵 = 𝑃𝑐𝑦𝑎 2 𝑏2−𝑎2 (3.8) Trong đó: 𝜎𝐵: Ứng suất uốn (MPa) b: Bán kính ngoài của kính quan sát (m) Từ công thức (3.8) ta tìm ra bán kính ngoài nhỏ nhất của kính quan sát là 48,10 mm. Lấy bán kính lớn hơn bán kính tối thiểu để tiện cho việc lắp ghép. Lựa chọn sơ bộ kích thước bằng 60 mm. Như vậy, sau khi tính toán về cơ bản đã xác định được kích thước của buồng cháy tương ứng với vật liệu S45C và tinh thể thạch anh (Bảng 3. 8) Bảng 3. 8. Thông số sơ bộ của buồng cháy Thông số Giá trị Đường kính ngoài 200 (mm) Đường kính trong 80 (mm) Chiều cao xylanh 90 (mm) 60 Vật liệu chế tạo S45C Áp suất tối đa 8 MPa Tính toán bulông buồng cháy Bulông lắp ghép giữa nắp buồng cháy với buồng cháy là chi tiết rất quan trọng vì vậy phải tính toán và lựa chọn đủ bền với hệ số an toàn k =1,3-1,5 Tính bu lông xiết chặt chịu lực dọc trục (Hình 3. 10). Hình 3. 10. Mối ghép bulông chịu lực dọc Sau khi xiết chặt, cho mối ghép chịu lực F, song song với đường tâm của bu lông Để mối ghép không bị phá hỏng, tức là trên mặt tiếp xúc giữa chúng còn áp suất, p>0 và bulông không bị hỏng σ < [σk]. Khi xiết mối ghép, lực xiết V làm các tấm ghép bị co lại một lượng là ΔS; đồng thời phản lực Ft làm thân bu lông bị dãn ra một lượng Δl, Δl = ΔS. Khi tác dụng lực F dọc trục, lực F được chia làm hai phần: + Phần F1 = χ.F, cộng thêm với lực Ft, làm bu lông dãn dài thêm một lượng. + Phần F2 = (1-χ).F, triệt tiêu bớt lực xiết V, làm các tấm ghép bớt co. χ được gọi là hệ số phân bố ngoại lực, giá trị của χ phụ thuộc vào độ cứng của thân bu lông và độ cứng của phần tấm ghép chịu tác dụng của lực xiết. Khi các tấm ghép bằng vật liệu thép hoặc gang, còn bu lông bằng thép có thể lấy χ = 0,2÷0,3. Như vậy, sau khi có lực dọc trục, lực tác dụng lên thân bu lông là Ft + χ.F, và lực ép lên các tấm ghép là V – (1-χ).F. + Điều kiện để các tấm ghép không bị tách hở là V – (1- χ).F > 0. + Ứng suất trong thân bu lông gồm hai phần, một phần do lực xiết, một phần do lực F1 gây nên: 𝜎 = 5,2.𝑉 𝜋.𝑑1 2 + 4.𝜒.𝐹 𝜋.𝑑1 2 ; Ft = V (3.9) Giả sử mối ghép không bị tách hở, ta tính được lực xiết cần thiết Vc. Vc > (1-χ).F; lấy Vc = K.(1-χ).F (3.10) Hệ số an toàn, có thể lấy K = 1,3 ÷ 1.5. 61 + Tính ứng suất trong thân bu lông: 𝜎 = 5,2.𝑉𝑐 𝜋.𝑑1 2 + 4.𝜒.𝐹 𝜋.𝑑1 2 (3.11) Lựa chọn: χ = 0,3; K = 1.5 với dường kính thân bulông d1 = 10 mm; áp suất trong buồng cháy p =80 bar (8000000 N/m2); đường kính buồng cháy D=80 mm. Thay số vào công thức (3.11) ta được ứng suất trong thân bu lông = 142,08 N/mm2 Như vậy: lựa chọn bulông có đường kính tiêu chuẩn 10 mm với ứng suất cho phép > 142.08 N/mm2 sẽ đảm bảo an toàn. Bu lông cường độ cao theo tiêu chuẩn DIN 931 (ren lửng) với bề mặt: ô xi đen, mạ điện phân, mạ kẽm nhúng nóng và nhuộm đen. Hình 3. 11 Ký hiệu trên bulông chịu lực cường độ cao. Thông số kỹ thuật Bu lông cường độ cao M10 (Bảng 3. 9) Bảng 3. 9. Thông số kỹ thuật bulông M10 cường độ cao d M10 Đường kính bulông tiêu chuẩn P 1,5 Bước ren k 7,5 Chiều dày của giác s 17 Chiều rộng của giác B, L>200 32 Chiều dài phần ren Hình 3. 11. Ký hiệu trên bulông Tính toán kiểm nghiệm buồng cháy Sử dụng phần mềm Ansys để mô phỏng tính bền với buồng cháy, và kính quan sát có kích thước sơ bộ và vật liệu chế tạo buồng cháy và kính quan sát như đã lựa chọn. 3.1.4.1. Kiểm nghiệm buồng cháy và kính quan sát Xây dựng mô hình CVCC là một hình tròn rỗng tròn với đường kính trong là 80 mm, đường kính ngoài 200 mm, chiều cao 80 mm, chiều dày 60 mm. Trên buồng cháy có lỗ để lắp vòi phun, quạt hòa trộn, bugi (Hình 3. 12). Kính quan sát được lựa chọn có kích thước đường kính 100 mm và chiều dày 35 mm. 62 Hình 3. 12. Mô hình CVCC, kính quan sát và nắp CVCC Điều kiện biên: Chia lưới mô hình, với kính quan sát, số lượng phần tử 508760, số nút 2089954, thân buồng cháy số lượng phần tử là 484098, số nút 679209, nắp buồng cháy số lượng phần tử 306578, số nút 437243 như trên hình (Hình 3. 13). Áp lực phân bố đều trên toàn bề mặt buồng cháy mặt kính quan sát và có giá trị không đổi 80 bar (8 MPa). Trong khi mô phỏng: vòi phun, quạt hòa trộn, bugi được liên kết chặt chẽ với thân CVCC bằng các bu lông chịu lực cao. Điều kiện mô phỏng được thể hiện trong Bảng 3. 10. Hình 3. 13. Mô hình chia lưới của buồng cháy, kính quan sát và nắp buồng cháy Bảng 3. 10. Điều kiện mô phỏng của buồng cháy Bộ phận của CVCC Áp suất (MPa) Nhiệt độ (0C) Thân buồng cháy 8 200; 400; 1000 Nắp kính quan sát 8 200; 400; 1000 Kính quan sát 8 200; 400; 1000 Kết quả mô phỏng: Hình 3. 14 và Hình 3. 15 chỉ ra rằng, khi tăng nhiệt độ của buồng cháy từ 2000C đến 10000C thì không ảnh hưởng đến các thông số ứng suất, chuyển vị và truyền nhiệt của buồng cháy. Điều này có thể được giải thích do vật liệu làm buồng cháy không ảnh hưởng đến mô đun đàn hồi và độ bền của vật liệu chế tạo buồng cháy. Ứng suất có xu hướng lớn dần từ ngoài vào phía trong buồng cháy và ứng suất, chuyển vị lớn nhất tập trung ở vị trí lắp ghép vòi phun và bugi. Ứng suất lớn nhất của buồng cháy khoảng 26,7 MPa. Với ứng suất này vật liệu làm buồng cháy đảm bảo đủ bền. Tổng chuyển vị của buồng cháy rất nhỏ 0.0000016 (m). chuyển vị tập trung ở những vị trí gia công để lắp ghép các chi tiết với nhau. Tuy nhiên không làm ảnh hưởng đến dung sai lắp ghép các chi tiết khác và khả năng làm việc của buồng cháy. 63 Hình 3. 14. Ứng suất, chuyển vị và truyền nhiệt của buồng cháy ở 4000C Hình 3. 15. Ứng suất, chuyển vị và truyền nhiệt của buồng cháy ở 10000C 64 Hình 3. 16. Ứng suất, chuyển vị và truyền nhiệt của kính quan sát ở 2000C Hình 3. 17. Ứng suất, chuyển vị và truyền nhiệt của kính quan sát ở 10000C 65 Hình 3. 18. Ảnh hưởng của nhiệt độ đến chuyển vị tương đương và truyền nhiệt đến kính quan sát Hình 3. 16; Hình 3. 17; Hình 3. 18 cho thấy, nhiệt độ không ảnh hưởng đến ứng suất mà chỉ ảnh hưởng đến chuyển vị tương đương và truyền nhiệt của kính quan sát. Chuyển vị và truyền nhiệt của kính quan sát thay đổi là do mô đun đàn hồi của vật liệu làm kính quan sát thay đổi theo nhiệt độ. Truyền nhiệt giảm đi khi tăng nhiệt độ của buồng cháy, điều này có thể được giải thích, khi tăng nhiệt độ thì độ chênh lệch nhiệt độ của hai bề mặt truyền nhiệt giảm dẫn đến truyền nhiệt giảm. Chuyển vị lớn nhất ở bề mặt tiếp xúc trực tiếp với áp suất cháy và giảm dần từ trong ra ngoài. Đối với truyền nhiệt thì xu hướng ngược lại với chuyển vị. Tức là, truyền nhiệt ở bề mặt bên ngoài của kính quan sát có giá trị lớn nhất và giảm dần vào phía trong, theo kết quả mô phỏng giá trị truyền nhiệt nhỏ nhất nằm ở tâm của kính và tiếp xúc trực tiếp với áp suất cháy. Ứng suất lớn nhất của kính quan sát tập trung ở bề mặt tiếp xúc trực tiếp với áp suất buồng cháy và có giá trị lớn nhất khoảng 112.9 MPa và nhỏ nhất ở mặt ngoài quan sát giá trị vào khoảng 57 MPa. Với giá trị ứng suất như vậy, vật liệu làm kính quan sát đảm bảo đủ bền trong quá trình làm việc với áp suất 8 MPa và nhiệt độ 10000C. Hình 3. 19. Ứng suất tương đương, chuyển vị và truyền nhiệt của nắp CVCC Hình 3. 19 là kết quả mô phỏng ứng suất, chuyển vị và truyền nhiệt của nắp buồng cháy. Giá trị ứng suất lớn nhất khi mô phỏng (160 MPa) vẫn đảm bảo an toàn tuyệt đối cho nắp buồng cháy, cũng giống như thân buồng cháy khi nghiên cứu, nhiệt độ không ảnh hưởng đến ứng suất, chuyển vị và truyền nhiệt của nắp buồng cháy (vật liệu chế tạo nắp buồng cháy giống như vật liệu chế tạo thân buồng cháy). Chuyển vị lớn nhất ở phần tiếp xúc với áp suất trong buồng cháy và giảm dần theo hướng từ trong ra ngoài. Ngược lại, truyền nhiệt lại có giá trị lớn nhất ở mặt ngoài và giá trị truyền nhiệt giảm dần theo hướng từ ngoài vào trong bề mặt tiếp xúc với áp suất cháy 8 MPa. 3.2. Chế tạo các bộ phận chính của buồng cháy 66 Thân buồng cháy, nắp buồng cháy và mặt bích là những chi tiết chính kết hợp với nhau tạo thành CVCC. Thân buồng cháy là chi tiết lớn nhất, nó chứa đựng các chi tiết khác của buồng cháy. Ngoài ra, nắp buồng cháy và mặt bích là hai chi tiết để giữ kính quan sát cố định trên thân buồng cháy. Dưới đây là quy trình gia công, chế tạo những chi tiết chính đó. Chế tạo thân buồng cháy Thân CVCC có dạng hình tròn rỗng. Trên thân buồng cháy có chứa nhiều chi tiết như: quạt hòa trộn, vòi phun nhiên liệu, đường khí nạp, thải, bugi, cảm biến áp suất và cảm biến nhiệt độ... Vì vậy, nó phải đảm bảo cứng vững và có độ chính xác cao (Hình 3. 20). Chế tạo nắp buồng cháy Nắp buồng cháy là chi tiết liên kết với mặt bích bên trong để giữ cố định kính quan sát. Ba chi tiết này lắp kín khít với thân của buồng cháy để tạo thành CVCC. Vì vậy, nắp buồng cháy phải gia công chính xác để có thể lắp giáp đảm bảo đúng kỹ thuật với các chi tiết còn lại (Hình 3. 21). Chế tạo mặt bích giữ kính quan sát Mặt bích có kích thước ngoài bằng với đường kính của nắp buồng cháy và đường kính trong bằng với đường kính của kính quan sát. Trong quá trình làm việc để tránh phá hỏng kính quan sát. Kích thước của mặt bích phải đảm bảo được gia công chính xác (Hình 3. 22). Quy trình công nghệ chế tạo thân CVCC, nắp CVCC và mặt bích giữ kính quan sát được trình bày cụ thể trong PHỤ LỤC 1. Hình 3. 20. Thân CVCC 67 Hình 3. 21. Nắp CVCC Hình 3. 22. Mặt bích giữ kính quan sát 68 Hình ảnh thực tế sau khi gia công các chi tiết chính của CVCC (Hình 3. 23) Hình 3. 23. Các chi tiết chính của buồng cháy sau khi gia công 3.3. Thiết kế, chế tạo hệ thống điều khiển Hệ thống điều khiển là sự kết hợp của hai phần mềm LabView và Arduino và thiết bị vi mạch điện tử Nano (Hình 3. 24). Đây là một hệ thống rất quan trọng của hệ thống CVCC. Hệ thống điều khiển có nhiệm vụ cung cấp lượng khí nạp chính xác vào buồng cháy, điều khiển thời gian hoạt động của quạt hòa trộn, thời gian và thời điểm đánh lửa cũng như thời gian phun. Cơ sở thiết kế và chế tạo hệ thống này được trình bày chi tiết trong phụ lục. Giao diện của hệ thống điều khiển như trên (Hình 3. 25). Hình 3. 24. Các bộ phận của hệ thống điều khiển CVCC 69 Hình 3. 25. Giao diện hệ thống điều khiển hoạt động của CVCC Sơ đồ khối thuật toán điều khiển Sơ đồ khối thuật toán điều khiển hệ thống CVCC như trên Hình 3. 26. Hình 3. 26. Sơ đồ thuật toán điều khiển hệ thống CVCC 70 Nhập thời gian cấp khí (A): nếu A > 0 mở van khí cấp cho buồng cháy, A ≤ 0 van khí đóng không cấp khí cho buồng cháy. Nhập thời gian chạy quạt hòa trộn (B): nếu B > 0 quạt hoạt động theo thời gian nhập vào, nếu B ≤ 0 quạt không hoạt động. Nhập thời gian phun nhiên liệu (D) và thời gian đánh lửa (C): nếu D > 0 và C > 0 thì hệ thống phun nhiên liệu và đánh lửa theo thời gian đã chọn. Ngược lại hệ thống không phun nhiên liệu và đánh lửa. Nhập thời điểm phun nhiên liệu và thời điểm đánh lửa: nếu thời B > 0 và C >
File đính kèm:
luan_an_nghien_cuu_qua_trinh_hinh_thanh_hon_hop_va_chay_hcci.pdf
Thông tin đưa lên Web_English.pdf
Thông tin đưa lên Web_Tiếng việt.pdf
Tom tat Luan an NCS Nguyen Phi Truong.pdf
Trich yeu Luan an.pdf