Luận án Nghiên cứu quá trình trích ly với sự hỗ trợ của màng ứng dụng thu hồi indium từ dung dịch thải của công nghiệp điện tử
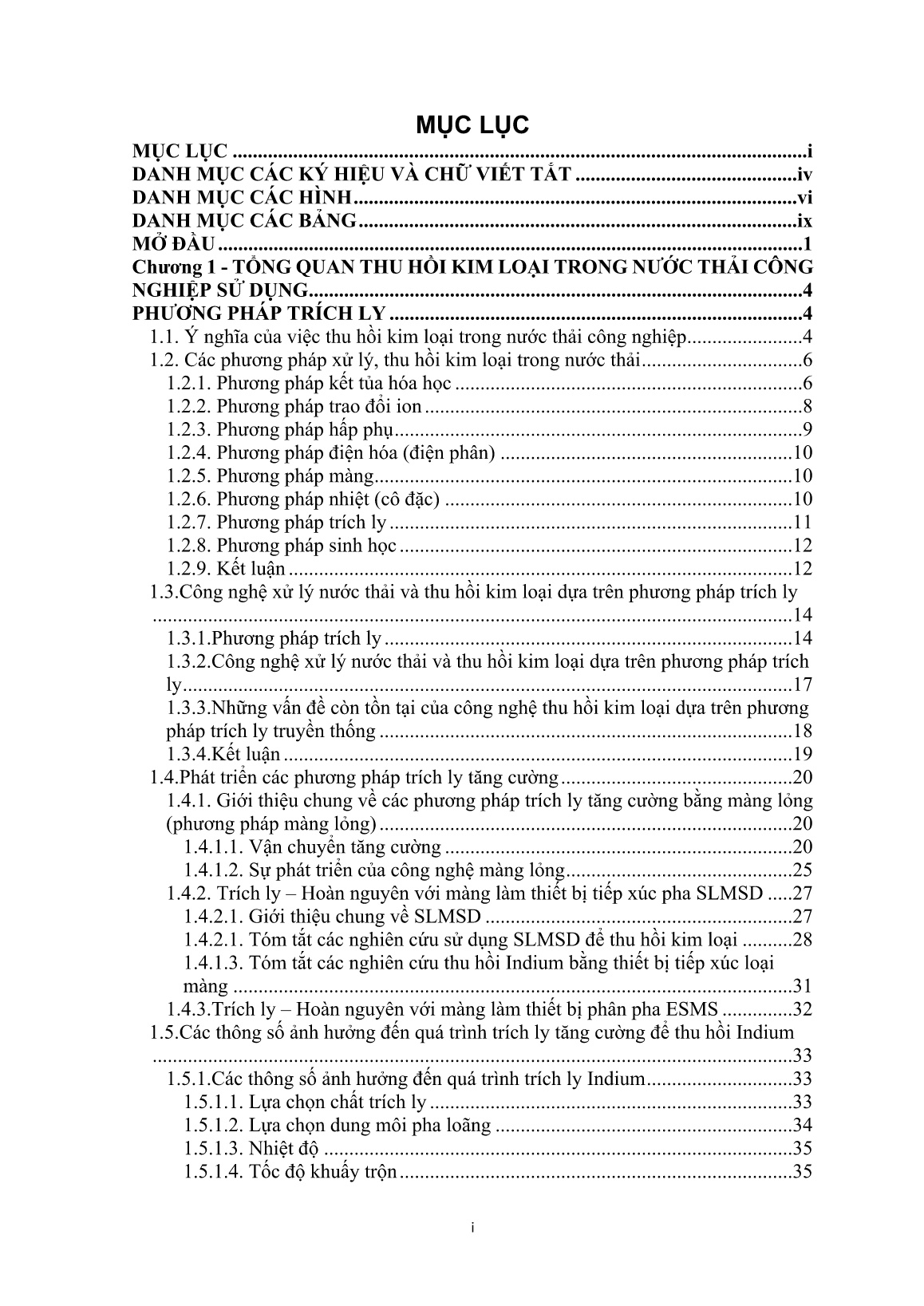
Trang 1
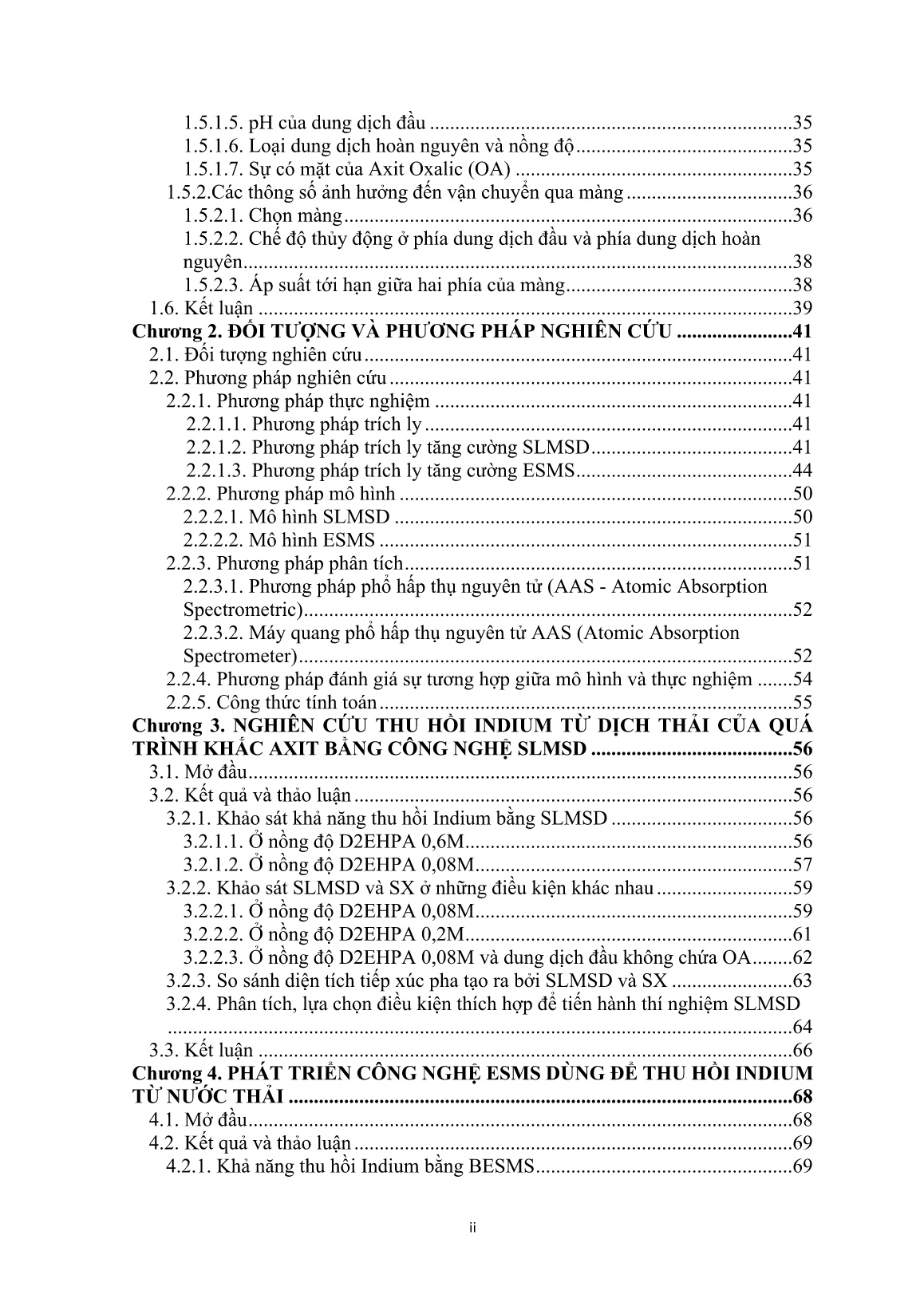
Trang 2
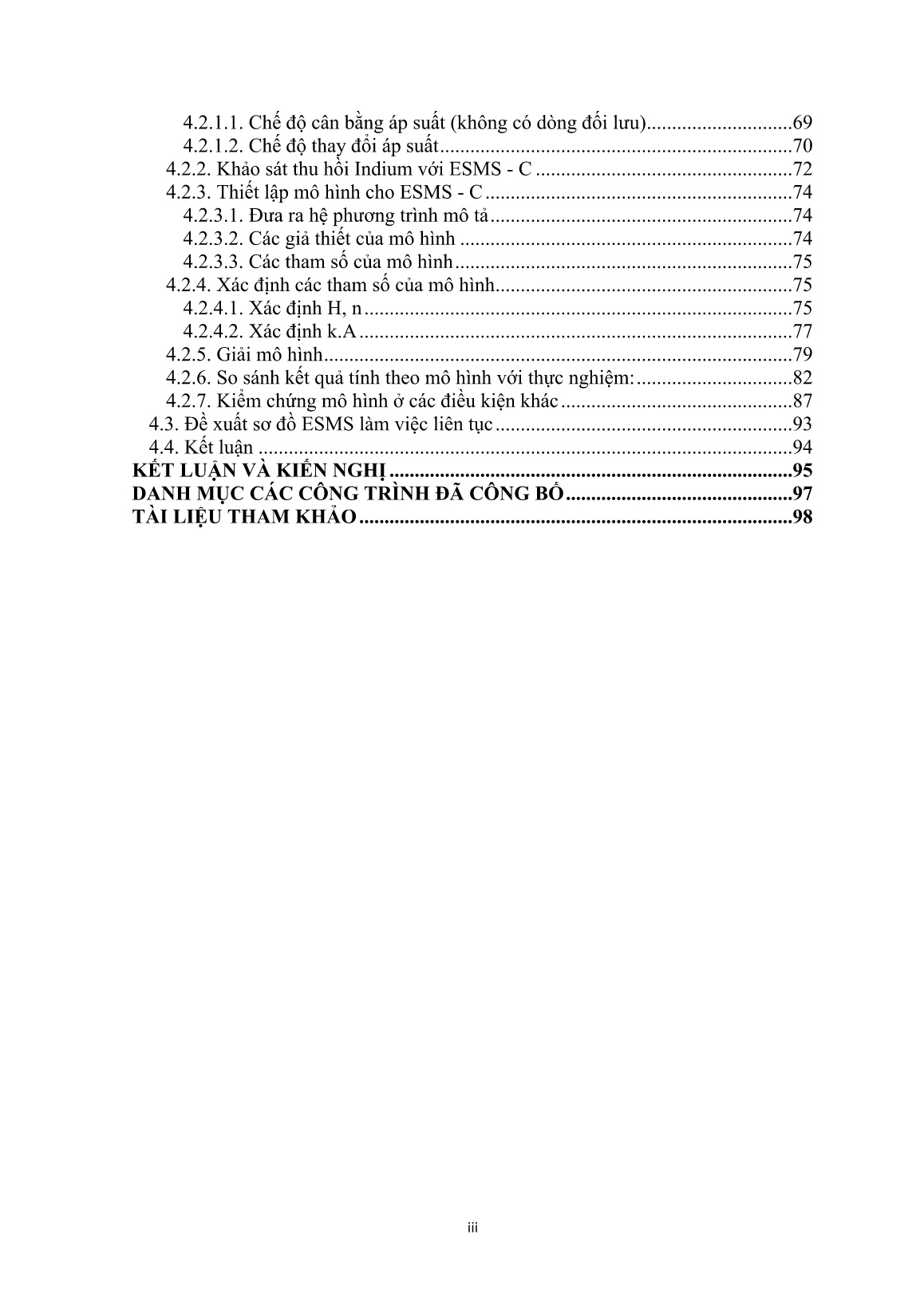
Trang 3
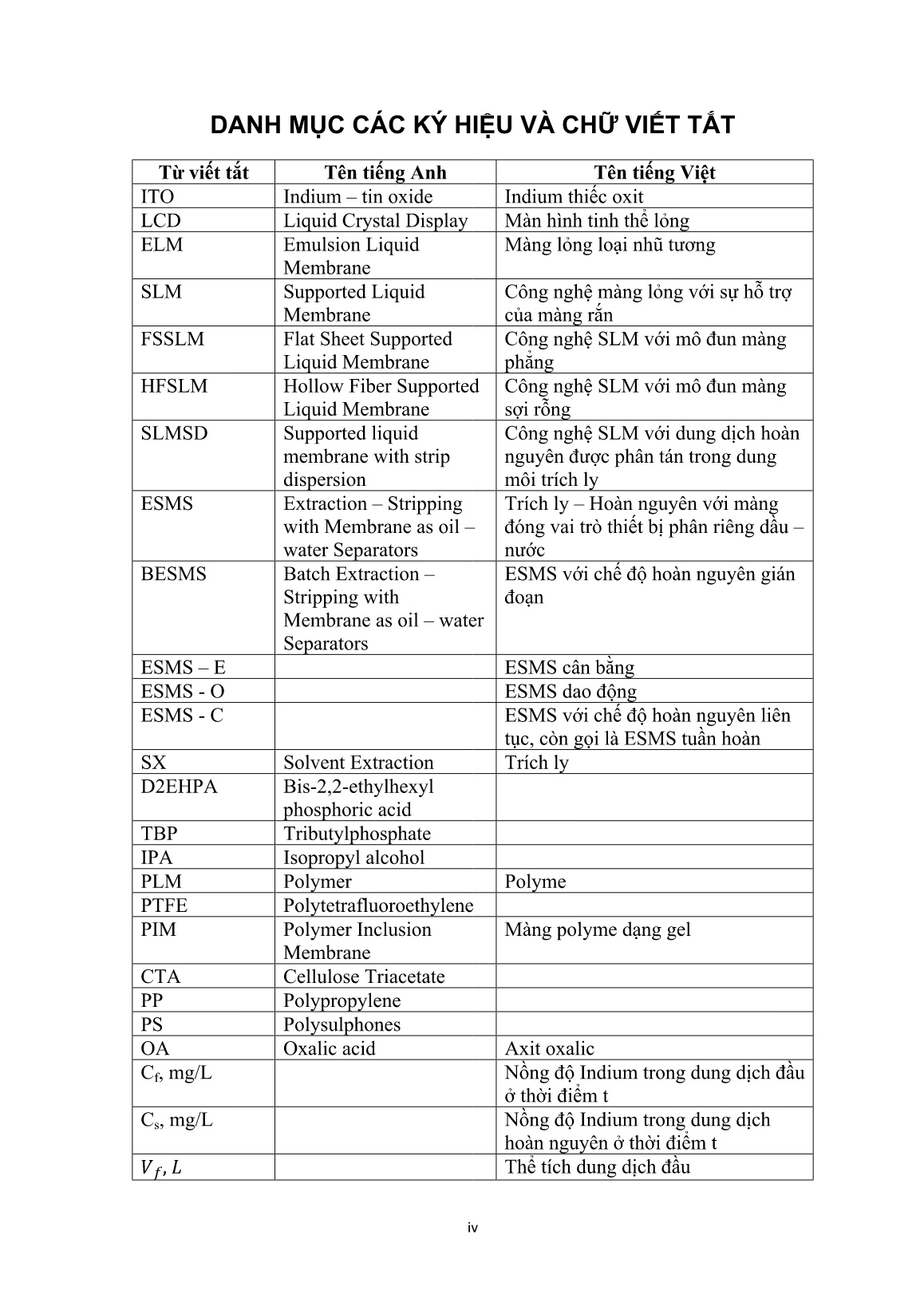
Trang 4
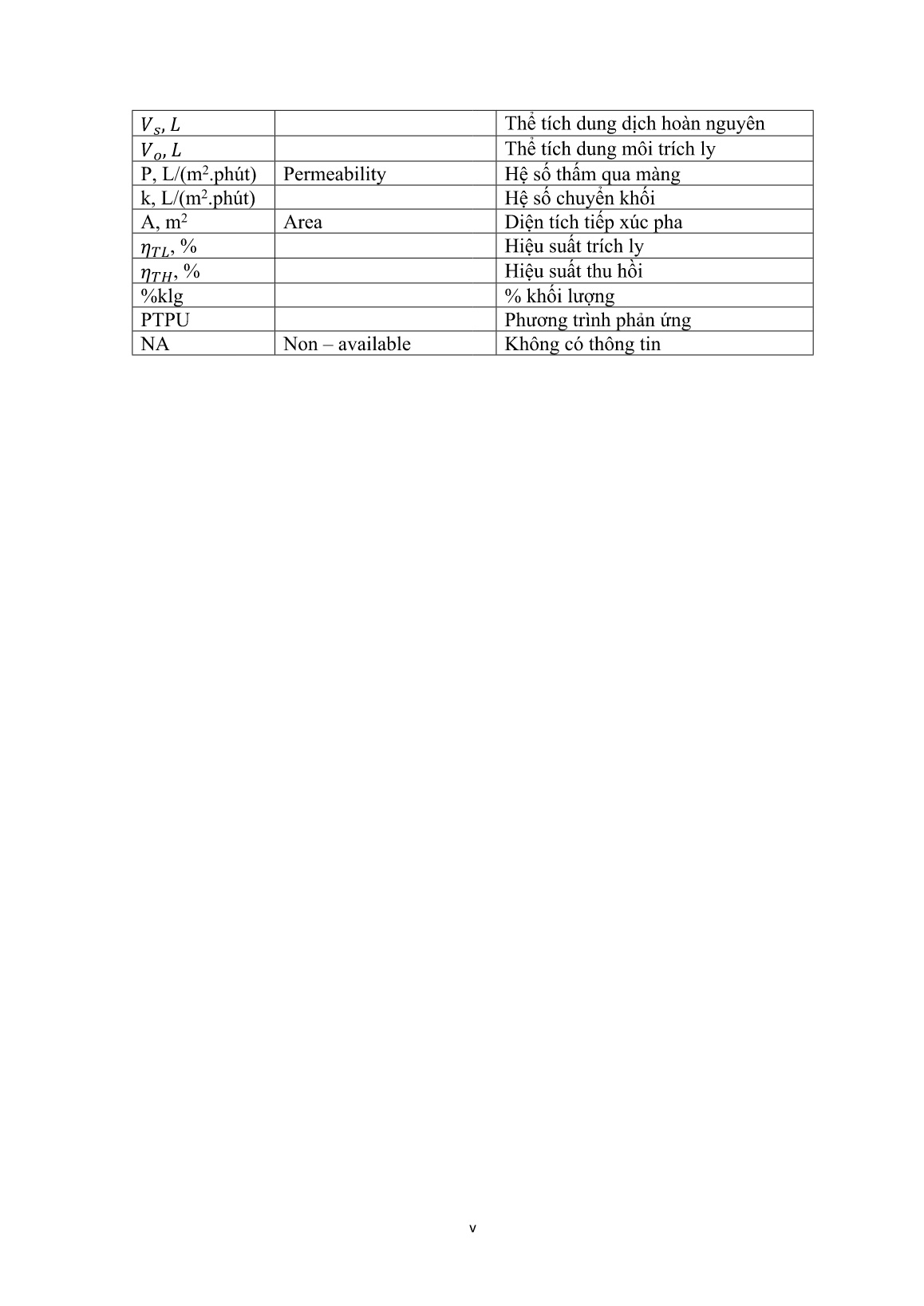
Trang 5
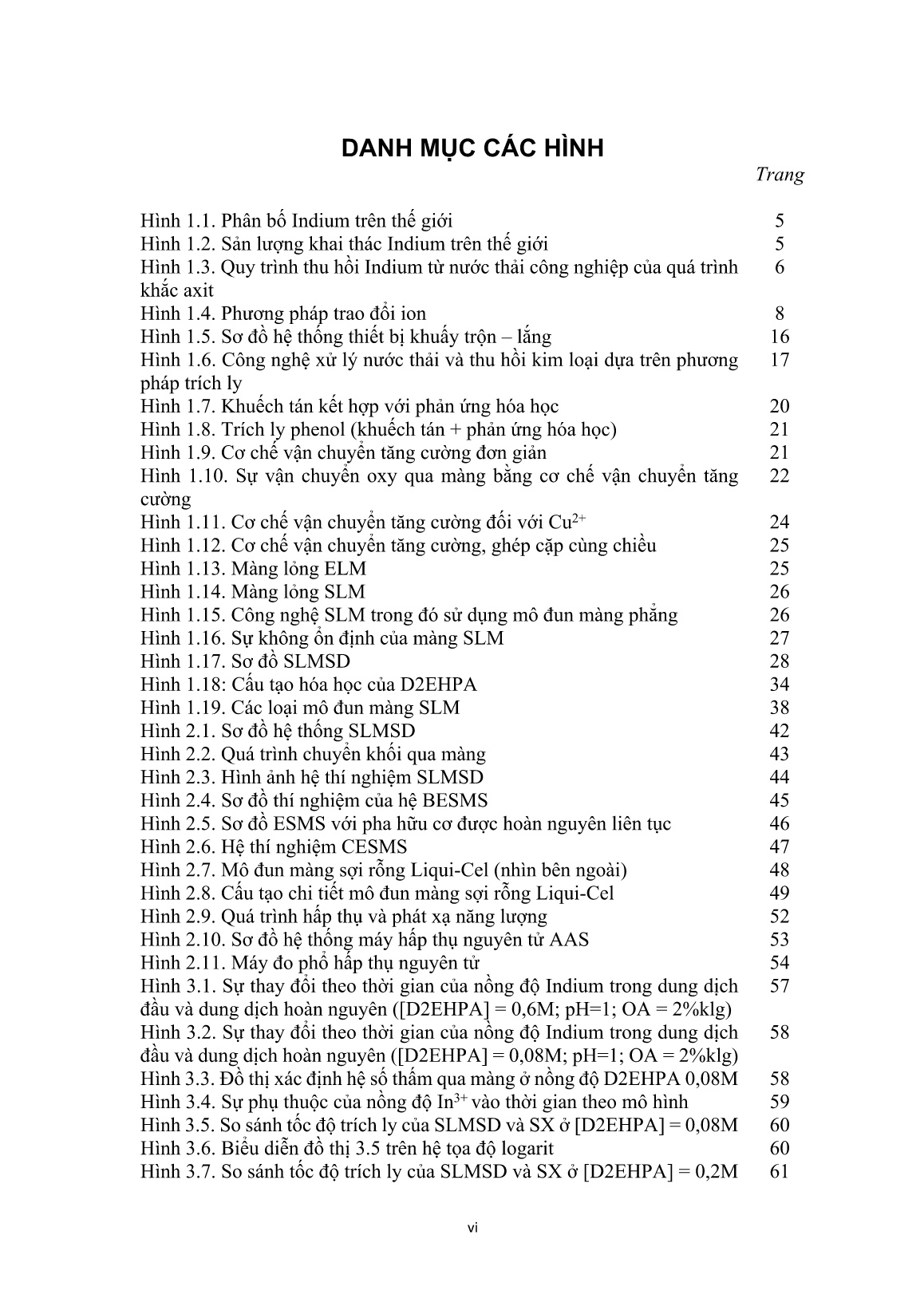
Trang 6
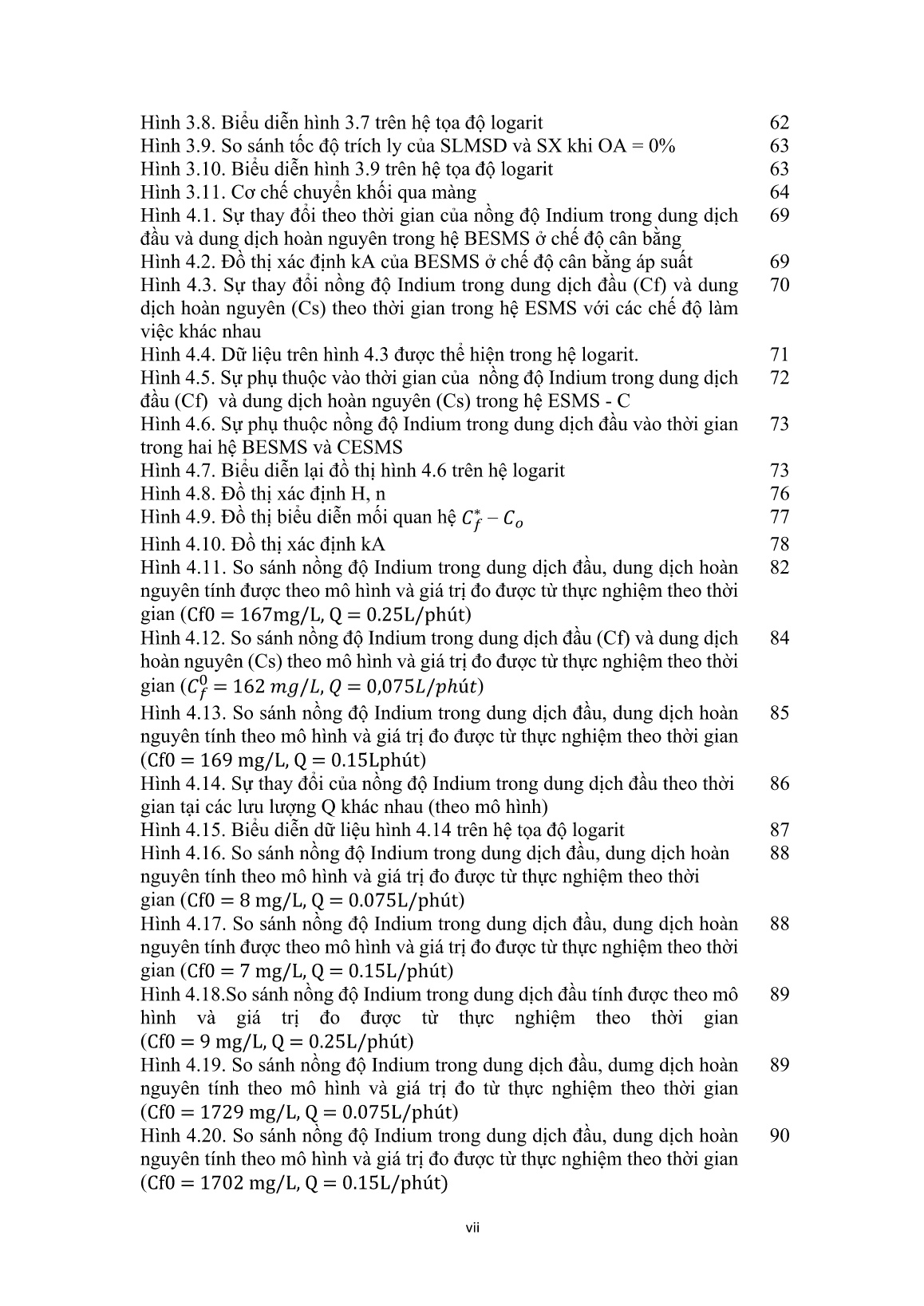
Trang 7
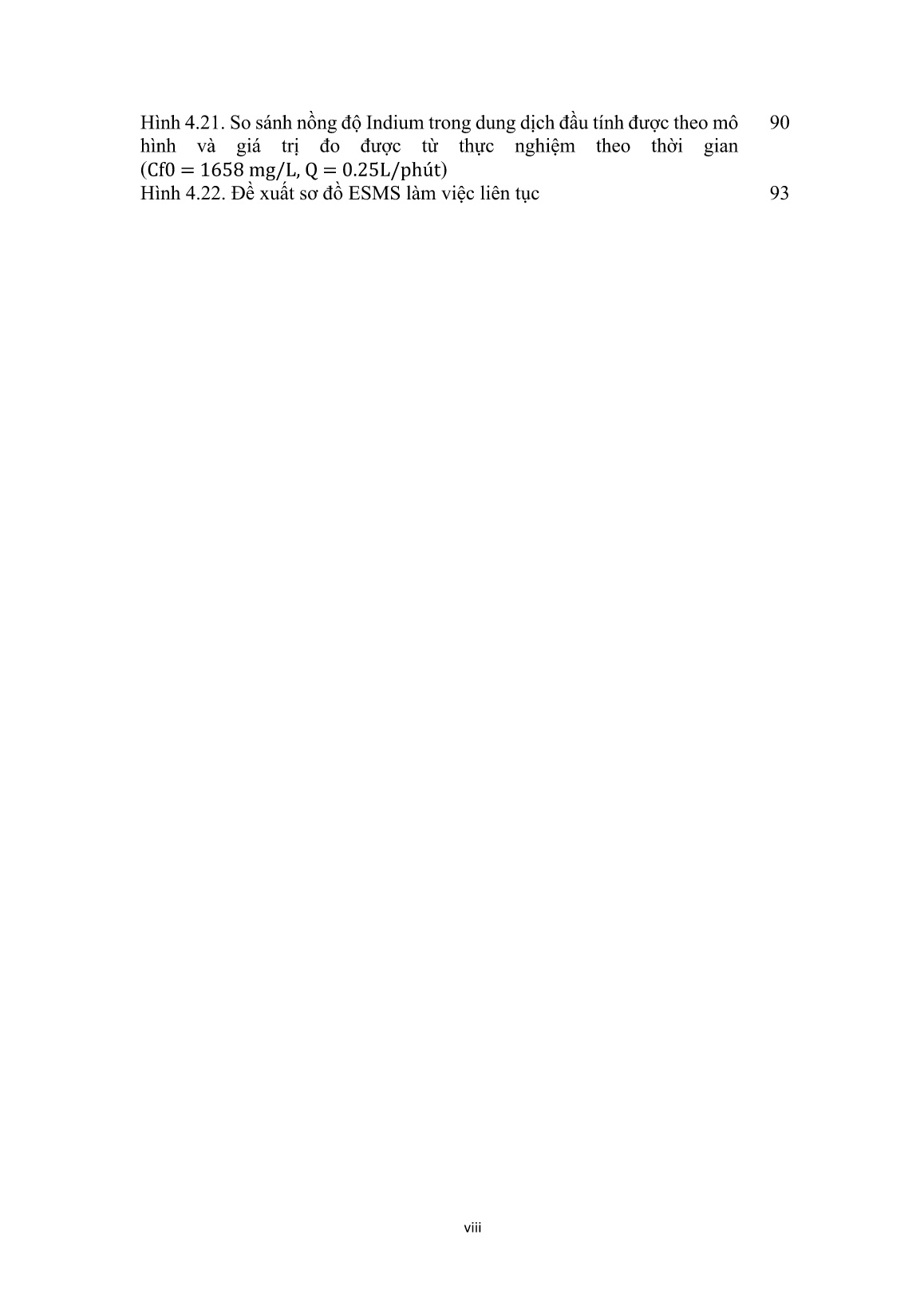
Trang 8
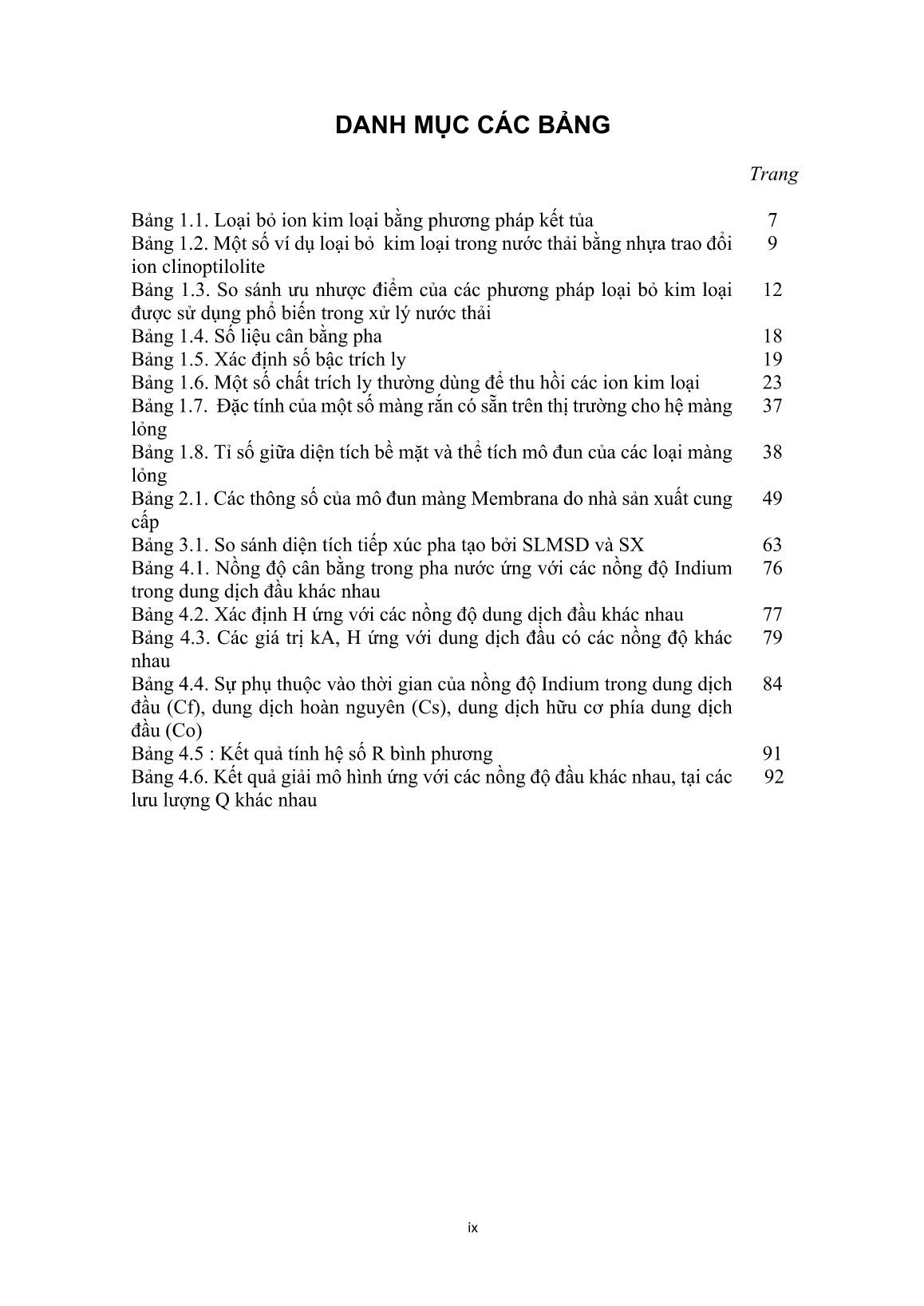
Trang 9
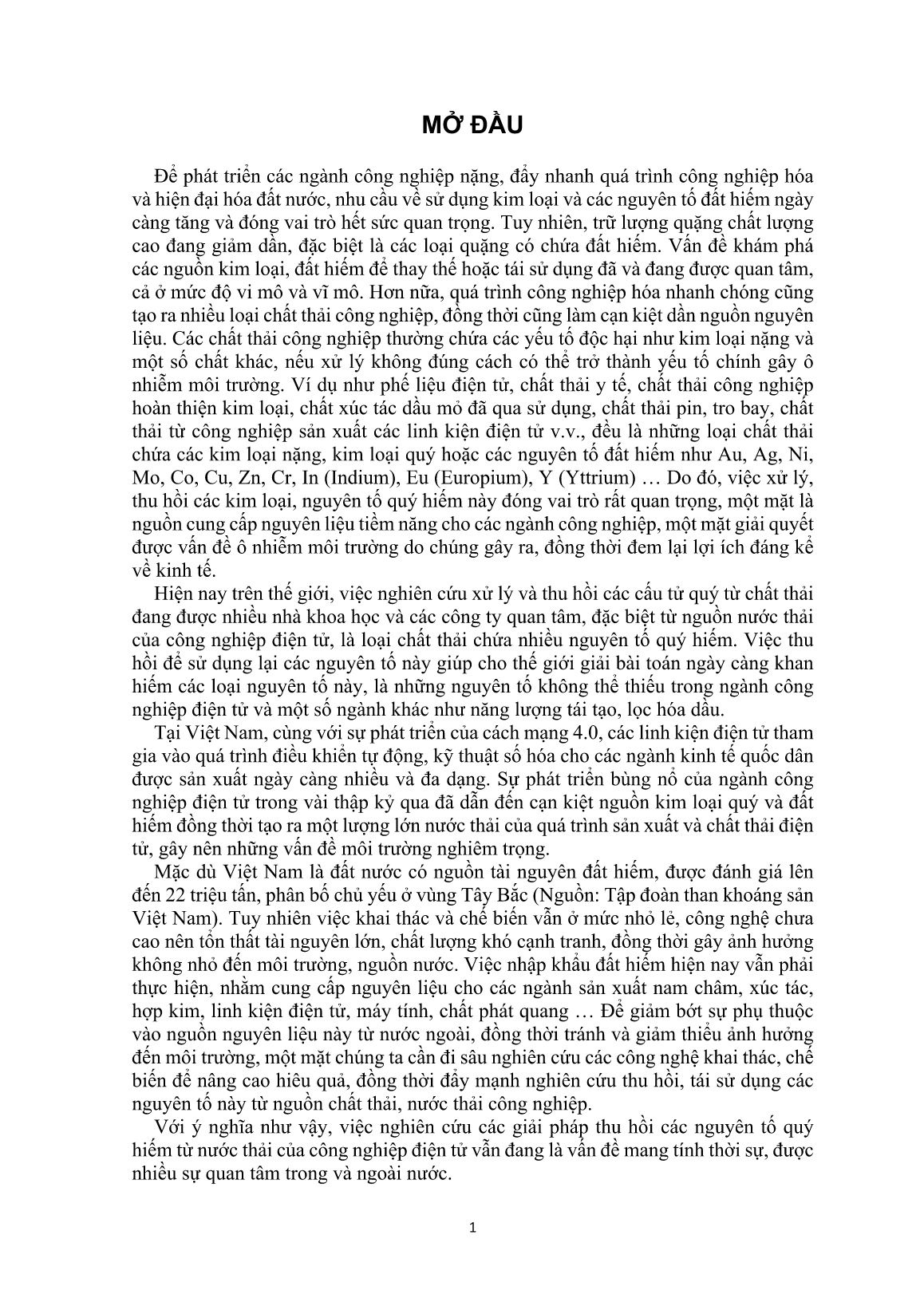
Trang 10
Tải về để xem bản đầy đủ
Bạn đang xem 10 trang mẫu của tài liệu "Luận án Nghiên cứu quá trình trích ly với sự hỗ trợ của màng ứng dụng thu hồi indium từ dung dịch thải của công nghiệp điện tử", để tải tài liệu gốc về máy hãy click vào nút Download ở trên.
Tóm tắt nội dung tài liệu: Luận án Nghiên cứu quá trình trích ly với sự hỗ trợ của màng ứng dụng thu hồi indium từ dung dịch thải của công nghiệp điện tử
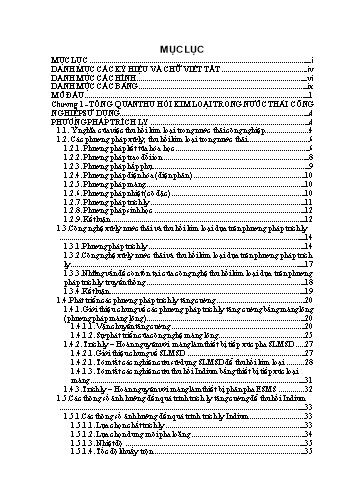
nhược điểm như sau: Ưu điểm: Phân riêng bằng màng cho phép thu được pha dầu không bị lẫn nước. Diện tích tiếp xúc pha lớn được tạo ra nhờ khuấy trộn. Dòng qua màng là dòng đối lưu nên tốc độ hoàn nguyên lớn hơn so với SLMSD (dòng khuếch tán). Hệ thiết bị gọn gàng so với công nghệ trích ly truyền thống. Không yêu cầu diện tích màng lớn như đối với công nghệ SLMSD. Nhược điểm: Chi phí đầu tư có thể cao hơn so với công nghệ trích ly truyền thống do chi phí màng vẫn còn cao. Cả hai phương án đề xuất ở trên đều dựa trên quá trình trích ly, do đó, để tiến hành nghiên cứu, đánh giá hiệu quả thu hồi kim loại ở các phương án này, cần có những thông số cơ bản như loại dung môi trích ly, dung môi pha loãng và dung dịch hoàn nguyên dựa trên những kết quả nghiên cứu trích ly đã có. Ngoài ra, các thông số ảnh hưởng đến sự vận chuyển qua màng cũng cần được quan tâm. Vì thế trong mục tiếp theo, ảnh hưởng của các thông số cơ bản đối với quá trình trích ly thông thường sẽ được đưa ra, từ đó lựa chọn các điều kiện thích hợp để thực hiện các nghiên cứu khảo sát trong các chương tiếp theo. 1.5. Các thông số ảnh hưởng đến quá trình trích ly tăng cường để thu hồi Indium Vì quá trình trích ly tăng cường là sự kết hợp giữa quá trình trích ly và quá trình khuếch tán qua màng kỵ nước, nên các thông số ảnh hưởng lên quá trình này bao gồm các thông số ảnh hưởng đến quá trình trích ly và các thông số ảnh hưởng đến vận chuyển qua màng. 1.5.1. Các thông số ảnh hưởng đến quá trình trích ly Indium Các thông số ảnh hưởng đến quá trình trích ly Indium đã được nghiên cứu rộng rãi và được tổng hợp lại dưới đây. 1.5.1.1. Lựa chọn chất trích ly Quá trình trích ly kim loại có thể đạt được bằng các cách khác nhau với 3 loại chất trích ly: loại axit, loại bazơ và solvat hóa. Do nước thải của quá trình khắc axit có pH<7, chất trích ly loại axit thường được sử dụng. Tiêu chí lựa chọn chất trích ly đã được trình bày ở mục 1.4.1. Để trích ly Indium, rất nhiều dung môi trích ly đã được sử dụng như: bis(2,4,4-trimethylpentyl) phosphinic acid Cyanex (272, 923), bis (2-ethylhexyl) phosphoric acid (D2EHPA), 2-ethyl hexyl phosphinic acid mono(2-ethyl hexyl) ether (PC88A), tributyl phosphate(TBP), hỗn hợp của D2EHPA và TBP [7]. Trong đó, D2EHPA là một trong những chất phổ biến nhất để trích ly Indium do có hệ số phân bố cao, độ bền cao, độ chọn lọc cao và độ tan trong nước nhỏ [5, 11]. Hơn nữa, D2EHPA còn có khả năng trích ly chọn lọc Indium ra khỏi các ion kim loại hóa trị III thường gặp trong dung dịch thực có chứa Indium như Bi3+, Fe3+, La3+, Ga3+, As3+ [5, 11]. Cơ chế trích ly ở đây là trao đổi ion và có thể tạo các phức Indium – polyme (Sato 1992) [23] theo phương trình phản ứng: 2Inaq3++5HR2org⇌In2R10H4org+6Haq+ (1. 1) Với HR2org là ký hiệu của D2EHPA do hợp chất này ở dạng dimer trong dung dịch. Cấu tạo hóa học của D2EHPA (C16H35O4P) được thể hiện trong hình 1.18. Hình 1.18 Cấu tạo hóa học của D2EHPA 1.5.1.2. Lựa chọn dung môi pha loãng Trong các dung môi sẵn có trên thị trường, kerosene là một dung môi pha loãng phổ biến vẫn được dùng trong trích ly Indium [5] do thỏa mãn các tiêu chí đã đưa ra ở mục 1.4.1 như: độ nhớt thấp (khoảng 1.5cSt), khối lượng riêng thấp (khối lượng riêng tương đối ở 150C là 0,8÷<1), không tan trong nước, dễ hòa tan các dung môi trích ly, giá thành thấp,...Tuy nhiên, dung môi này gây mùi khó chịu có thể ảnh hưởng đến sức khỏe khi làm việc trong thời gian dài. Do vậy, Isopar-L với các tính chất tương tự [73] nhưng không gây mùi khó chịu được dùng để thay thế dầu hỏa làm dung môi pha loãng trong một số nghiên cứu gần đây [51] [74] [79] [80]. 1.5.1.3. Nhiệt độ Phản ứng trích ly của Indium (III) bởi D2EHPA trong môi trường axit là phản ứng tỏa nhiệt nên hệ số phân bố của Indium (III) giảm khi nhiệt độ tăng [23] và khoảng nhiệt độ tối ưu là 20 đến 250C. Hơn nữa, sự tăng nhiệt độ khiến cho khả năng hòa tan giữa các pha cao hơn, dẫn đến sự tạo thành lớp nhũ tương ở các bề mặt tiếp xúc pha, làm giảm hiệu quả trích ly. Vì thế, các thí nghiệm trích ly Indium thường được tiến hành ở nhiệt độ phòng (25oC). 1.5.1.4. Tốc độ khuấy trộn Tốc độ khuấy trộn càng lớn, kích thước giọt nhũ tương càng nhỏ nên diện tích tiếp xúc A càng lớn dẫn đến quá trình chuyển khối diễn ra nhanh hơn. Trong quá trình trích ly thông thường, việc làm giảm kích thước nhũ tương khiến cho quá trình lắng khó khăn hơn. 1.5.1.5. pH của dung dịch đầu Khi pH càng tăng tức [H+] càng giảm khiến hệ số phân bố càng tăng. Vì thế, quá trình trích ly cũng diễn ra nhanh hơn. Khoảng pH được khảo sát thường là từ 0,5 đến 3 [75]. Do ở pH thấp (nhỏ hơn 0,5), hiệu suất trích ly quá thấp (khoảng 40%); ở pH lớn hơn 3, Indium có thể bị kết tủa. Theo Feng Chi Yen (2016) [11], khoảng pH tối ưu cho trích ly Indium là 1,3 đến 2,3. Trong khi đó Chou et al. [5] lại đề nghị khoảng pH thích hợp là 1 – 1,5. Còn theo Lupi [75], pH thích hợp là 1,5. Sự khác nhau này có thể do điều kiện thí nghiệm khác nhau. Do khoảng pH khá hẹp và khá thấp nên hiệu suất trích ly thay đổi không đáng kể [11]. 1.5.1.6. Loại dung dịch hoàn nguyên và nồng độ Với dung dịch axit HCl lớn hơn hoặc bằng 1M, Indium có thể được hoàn nguyên chọn lọc [5] [8] [11] theo PTPƯ sau: In2R10H4org+6Haq+⇌2Inaq3++5HR2org (1. 2) Đối với quá trình trích ly tăng cường nhằm thu hồi Indium, cơ chế chuyển khối ở đây là cơ chế chuyển khối tăng cường ghép cặp – ngược chiều nên cần duy trì gradient nồng độ H+ giữa phía dung dịch hoàn nguyên và dung dịch đầu càng lớn càng tốt để tách Indium triệt để ra khỏi dung dịch đầu. Do đó, HCl thường được chọn ở nồng độ 5M [70]. 1.5.1.7. Sự có mặt của Axit Oxalic (OA) Các nghiên cứu cho đến nay chưa đề cập đến thu hồi Indium từ các dung dịch có chứa axit oxalic mà chủ yếu vẫn tập trung vào các dung dịch thu được sau hòa tách hoặc dung dịch khắc axit truyền thống [5]. Điều này có thể được giải thích do gần đây dung dịch khắc axit mới (chứa OA) mới được đưa vào sử dụng trong công nghiệp sản xuất LCD [75]. Sự có mặt OA có thể sẽ làm giảm hiệu quả trích ly do sự tạo phức của Indium với OA theo các PTPU sau: H2C2O4⇌H++HC2O4- K1=5.9.10-2 (1. 3) HC2O4-⇌H++C2O42- K2=6.4.10-5 (1. 4) In3++HC2O4-⇌In(HC2O4)2+ β1=103,08 (1. 5) In3++C2O42-⇌In(C2O4)+ β1=105,3 (1. 6) In3++2C2O42-⇌In(C2O4)2- β1=1010,52 (1. 7) In3++3C2O42-⇌In(C2O4)33- β1=1014,7 (1. 8) 1.5.2.Các thông số ảnh hưởng đến vận chuyển qua màng 1.5.2.1. Chọn màng Trong công nghệ SLMSD, màng rắn hỗ trợ (gọi tắt là màng) đóng vai trò giữ màng lỏng trong mao quản. Khả năng trích ly phụ thuộc chủ yếu vào pha màng lỏng (dung môi trích ly). Tuy nhiên độ bền của màng lỏng và độ bền cơ học của hệ phụ thuộc vào cấu trúc màng (rắn), bao gồm: độ xốp, hình dạng, kích thước mao quản, độ ngoằn nghèo của mao quản. Do màng đóng vai trò tạo bề mặt tiếp xúc giữa pha nước và pha hữu cơ và chỉ cho phép dung môi hữu cơ đi qua do đó màng cần thỏa mãn các yêu cầu chủ yếu sau: Diện tích bề mặt riêng lớn (để tăng năng suất chuyển khối) Có tính kỵ nước (để chỉ cho pha hữu cơ đi qua) Màng mỏng để đạt được dòng khuếch tán qua màng lớn (nhưng vẫn phải đủ dày để đảm bảo độ bền cơ học). Do đó, màng bất đối xứng thường được sử dụng. Vật liệu màng: Màng hỗ trợ có thể làm từ vật liệu polymer hoặc vô cơ. Về lý thuyết, màng sử dụng có thể ưa nước hoặc kỵ nước, đồng thể hoặc dị thể, đối xứng hoặc bất đối xứng trong cấu trúc, trung hòa, mang điện dương hay điện âm. Nó có thể được chế tạo từ nhiều vật liệu hoặc có cấu trúc khác nhau. Tuy nhiên các dung môi nước thường dễ bay hơi, không đảm bảo độ bền của màng nên các dung môi hữu cơ thường được sử dụng để tạo pha màng. Do đó, vật liệu chế tạo màng thường là vật liệu kỵ nước để có thể giữ được các dung môi hữu cơ trong các mao quản của màng nhờ lực mao quản. Đồng thời, vật liệu chế tạo màng hỗ trợ yêu cầu có tính bền nhiệt và bền hóa học trong dung dịch đầu, dung dịch hoàn nguyên và dung dịch hữu cơ. Đối với quá trình màng lỏng, các màng được sử dụng nhiều nhất bao gồm: Polytetrafluoroethylene (PTFE), polypropylene (PP), polysulphones (PS) (bảng 1.7). Màng PP thường thấy trên thị trường của hãng Celgard. Trong đó, màng Celgard – 2400 và Celgard – 2500 với các thông số đặc trưng được đưa ra gần đây đã được ứng dụng nhiều để thu hồi kim loại trong các quá trình thủy luyện. Màng PP ở dạng ống được sản xuất bằng phương pháp chuyển pha. Các màng PS cũng được điều chế bằng phương pháp chuyển pha trong đó PS được hòa tan trong dung môi để tạo thành dung dịch. Dung dịch này sau đó được phủ lên các sợi rỗng. Sau đó, dung môi được loại bỏ bằng cách cho bay hơi. Màng thu được là bất đối xứng và có các mao quản rất nhỏ bên trong các sợi này. Bảng 1.7 Đặc tính của một số màng rắn có sẵn trên thị trường cho hệ màng lỏng (nguồn: [36]) Tên thương mại Vật liệu Nhà sản xuất Độ dày (µm) Độ xốp (%) Kích thước pore (µm) Celgard 2400 PP Celanese 25 38 0,02 Celgard 2500 PP Celanese 25 45 0,04 Accurel PP Enka 100 64 0,10 Accurel PP Enka 150 70 0,20 hoặc 0,40 Accurel PP Enka 160 75 0,20 Accurel 1E-PP PP Enka 75 73 0,1 – 0,3 Accurel BS7C PP Armak 50 48 - Duragard 2500 PP Plolyplastic 25 45 0,04 FP - DCH PTFE Flow Lab. 150 80 0,45 FHLP PTFE Milipore 60 85 0,50 FP - 045 PTFE Sumimoto 80 73 0,45 Millipore PTFE Milipore 125 68 10 Goretex PTFE Gore 60 78 0,20 Fluoropore FG PTFE Milipore 60/115 70 0,20 Fluoropore FP-200 PTFE Milipore 100 83 2,0 Fluoropore FP-045 PTFE Milipore 80 75 0,45 Fluoropore FP-010 PTFE Milipore 60 55 0,1 Nucelopore Polycarbonate Nucelopore Corp. 10 12 0,4 Mô đun màng: được sử dụng để giữ lớp polyme xốp chứa pha lỏng. Yêu cầu đối với mô đun màng: bền cơ học, diện tích bề mặt trên một đơn vị thể tích lớn, không cho dung dịch đầu và dung dịch hoàn nguyên đi qua. Có 3 loại mô đun thỏa mãn các yêu cầu trên (hình 1.19), bao gồm: Mô đun màng phẳng (a) Mô đun màng sợi rỗng (b) Mô đun màng cuốn (c) Trong đó, hai loại mô đun đầu tiên được sử dụng phổ biến nhất. (a) (b) (c) Hình 1.19 Các loại mô đun màng SLM Trong các loại mô đun ở trên, mô đun màng phẳng có thiết kế đơn giản nhất, có thể được sử dụng để thực hiện các nghiên cứu trong phòng thí nghiệm nhưng rất khó chuyển lên quy mô công nghiệp. Trong khi đó, mô đun màng sợi rỗng có diện tích bề mặt riêng lớn (Bảng 1.8), độ dày màng nhỏ nên tốc độ chuyển khối cao [36, 75], do đó được ứng dụng rộng rãi trong công nghệ màng lỏng. Theo Elhassado và Do [78], khi A/V tăng 2 lần, thời gian vận hành giảm 2 lần. Ở quy mô nhỏ (quy mô thí nghiệm), mô đun màng sợi rỗng loại kỵ nước Liqui-Cell của Membrana với diện tích màng 1,4 m2 (đường kính: 6,35 cm; chiều cao: 20,3 cm) được sử dụng rộng rãi nhất nên cũng được chọn sử dụng trong nghiên cứu này. Bảng 1.8 Tỉ số giữa diện tích bề mặt và thể tích mô đun của các loại màng lỏng (nguồn: [76]) Loại mô đun màng ELM HFSLM FSSLM Màng ống A/V, m2/m3 1000 – 3000 1000 100 – 200 50 1.5.2.2. Chế độ thủy động ở phía dung dịch đầu và phía dung dịch hoàn nguyên Trong các mô đun màng sợi rỗng, dung dịch đầu thường được cho tuần hoàn trong các sợi rỗng. Tốc độ tuần hoàn phía dung dịch đầu càng lớn, độ dày lớp biên càng giảm nên vận tốc khuếch tán qua lớp biên càng lớn dẫn đến hệ số chuyển khối chung càng lớn. Đối với mô đun ở trên, lưu lượng tuần hoàn thích hợp phía dung dịch đầu là 1 L/phút [79]. Tốc độ tuần hoàn phía dung dịch hoàn nguyên ít ảnh hưởng đến hệ số chuyển khối chung hơn nên thường được chọn theo tốc độ tuần hoàn phía dung dịch đầu [79]. Đối với mô đun ở trên, lưu lượng tuần hoàn thích hợp phía dung dịch hoàn nguyên được chọn là 1 L/phút. 1.5.2.3. Áp suất tới hạn giữa hai phía của màng Chênh lệch áp suất qua màng có được là do sự tuần hoàn các pha dung dịch đầu và dung dịch hoàn nguyên ở hai phía của màng. Khi chênh lệch này vượt quá một giá trị tới hạn nhất định, pha màng lỏng (dung dịch hữu cơ) sẽ bị đẩy ra khỏi các mao quan của màng rắn. Áp suất qua màng nhỏ nhất Pc cần để đẩy pha hữu cơ ra khỏi các mao quản có đường kính lớn nhất có thể được tính theo phương trình Laplace [36] : Pc=2γ.cosθr Với: Pc: áp suất, N/m2 γ: sức căng bề mặt giữa pha nước (dung dịch đầu hoặc dung dịch hoàn nguyên) và pha hữu cơ, N/m θ: góc tiếp xúc giữa mao quản màng và màng lỏng r: bán kính mao quản, m Công thức trên đúng với trường hợp các mao quản hình trụ, song song. Đối với các mô đun màng sợi rỗng trên thị trường, các mao quản có cấu hình bất đối xứng hơn nhiều. Do đó, thực tế áp suất qua màng lớn hơn nhiều so với giá trị tính ở trên. Điều đó cho thấy sự chênh lệch áp suất qua màng không phải là nguyên nhân chính gây ra tổn thất dung môi đẫn đến giảm độ bền của màng lỏng. Nguyên nhân chủ yếu ở đây là do tác dụng của lực ma sát ở hai bên của màng 1.6. Kết luận Sau khi tổng quan thu hồi kim loại quý hiếm từ nước thải nhận thấy trích ly là phương pháp được ứng dụng phổ biến nhất để thu hồi Indium từ nước thải hay dịch hòa tách chất thải điện tử. Do đó công nghệ xử lý nước thải và thu hồi kim loại dựa trên phương pháp trích ly đã được lựa chọn để thu hồi Indium từ dung dịch thải của quá trình khắc axit trong công nghiệp sản xuất LCD. Phương pháp trích ly truyền thống vận hành từng bậc, do đó thường yêu cầu trích ly nhiều bậc, hoàn nguyên nhiều bậc dẫn đến hệ thống thiết bị cồng kềnh, lượng dung môi tiêu tốn lớn. Để giảm kích thước thiết bị cũng như lượng dung môi tiêu tốn, hai phương án trích ly tăng cường đã được đưa ra trong đó quá trình hoàn nguyên được thực hiện đồng thời với quá trình trích ly: Trích ly – Hoàn nguyên trong đó màng đóng vai trò tạo bề mặt tiếp xúc SLMSD. Đây là phương pháp hiện đã và đang được nghiên cứu. Trích ly – Hoàn nguyên trong đó màng đóng vai trò thiết bị phân riêng pha ESMS. Đây là phương pháp mới, sẽ được phát triển một cách hệ thống trong luận án này. Tiến hành tổng quan các nghiên cứu xử lý nước thải và thu hồi kim loại nhận thấy: SLMSD cho phép đạt được nồng độ ion kim loại trong nước thải sau khi xử lý nhỏ hơn 1 mg/L đồng thời cho phép nâng cao nồng độ ion kim loại trong dung dịch hoàn nguyên nhờ điều chỉnh tỉ lệ thể tích giữa nước thải đi vào và dung dịch hoàn nguyên với độ ổn định của màng lỏng cao nên rất được quan tâm nghiên cứu nhằm ứng dụng trong công nghiệp, đặc biệt trong công nghiệp điện tử. Đã có những nghiên cứu bước đầu đánh giá khả năng thu hồi Indium từ các môi trường axit vô cơ như HCl, HNO3, H2SO4 bằng SLMSD với kết quả tốt. Khi nghiên cứu thu hồi Indium từ màn hình LCD thải bằng công nghệ SLMSD, 94% Indium được loại bỏ khỏi dung dịch đầu trong khoảng 20 phút. Tuy nhiên, hiện chưa ghi nhận bất cứ nghiên cứu nào liên quan đến thu hồi Indium từ dung dịch chứa axit oxalic. Lý do vì các dung dịch khắc axit truyền thống thường sử dụng axit vô cơ hoặc hỗn hợp các axit vô cơ. Mãi đến gần đây, các axit hữu cơ như axit oxalic mới được đưa vào sử dụng. Cần lưu ý rằng: axit oxalic có khả năng cạnh tranh với D2EHPA để tạo phức với Indium, do đó sự có mặt của axit oxalic có thể giảm tốc độ phản ứng trích ly đáng kể và khiến cho quá trình trích ly trở nên khó khăn hơn nhiều. Hiện chưa ghi nhận bất cứ nghiên cứu nào đề cập đến công nghệ ESMS Với mục đích phát triển phương pháp trích ly tăng cường mới đồng thời đánh giá so sánh hiệu quả của phương pháp mới so với các phương pháp hiện có ở cùng điều kiện, đánh giá ảnh hưởng của các thông số lên quá trình trích ly tăng cường bao gồm các thông số ảnh hưởng đến quá trình trích ly và các thông số ảnh hưởng đến vận chuyển qua màng đã được thực hiện dựa trên các nghiên cứu đã có. Từ đó, các thông số cơ bản cho quá trình trích ly tăng cường nhằm thu hồi Indium được lựa chọn như sau: (i) Dung môi trích ly: D2EHPA 0,08M pha loãng trong Isopar-L (chọn nồng độ dung môi trích ly tương đối thấp) (ii) Nhiệt độ: nhiệt độ phòng (250C) (iii) pH dung dịch đầu: 1 (là giá trị pH đặc trưng của nước thải của quá trình khắc axit) (iv) Dung dịch hoàn nguyên: HCl 5M (nồng độ H+ - ion vận chuyển ngược chiều với In3+ - phía dung dịch hoàn nguyên rất lớn để duy trì động lực quá trình vận chuyển In3+ qua màng). (v) Nồng độ axit oxalic trong dung dịch đầu: 2% khối lượng (là nồng độ đặc trưng trong nước thải của quá trình khắc axit). (vi) Màng: mô đun màng sợi rỗng Liqui – Cel của Membrana (vật liệu màng: PP, màng kỵ nước, diện tích màng: 1,4 m2) (viii) Lưu lượng tuần hoàn phía dung dịch đầu: 1 L/phút (ix) Lưu lượng tuần hoàn phía dung dịch hoàn nguyên: 1 L/phút Chương 2. ĐỐI TƯỢNG VÀ PHƯƠNG PHÁP NGHIÊN CỨU 2.1. Đối tượng nghiên cứu Nhu cầu thu hồi Indium từ nước thải của quá trình khắc axit trong công nghiệp LCD là rất lớn và hết sức có ý nghĩa trong việc cân bằng giữa cung và cầu, đáp ứng yêu cầu xử lý nước thải và tạo ra giá trị kinh tế cao. Nhằm đánh giá hiệu quả của phương pháp trích ly tăng cường, đối tượng nghiên cứu được chọn ở đây là dung dịch mô phỏng nước thải của quá trình khắc axit trong công nghệ sản xuất màn hình LCD với thành phần như sau: nồng độ Indium là 200mg/L, nồng độ OA là 2% khối lượng, pH dung dịch bằng 1. 2.2. Phương pháp nghiên cứu 2.2.1. Phương pháp thực nghiệm 2.2.1.1. Phương pháp trích ly gián đoạn 360 ml dung dịch đầu chứa In3+ và 540 ml dung môi trích ly chứa D2EHPA hòa tan trong Isopar-L được trộn lẫn và khuấy đều. Sau mỗi khoảng thời gian nhất định, 3ml mẫu được lấy bằng pipet, sau đó ly tâm để phân riêng pha nước và pha hữu cơ. Nồng độ Indium trong pha nước được đo bằng máy quang phổ hấp thụ nguyên tử (Perkin Elmer AAnalyst-200). Tất cả các thí nghiệm được thực hiện ở cùng tốc độ khuấy (540 rpm) ở tại nhiệt độ phòng (250C±1). Thời gian tiến hành thí nghiệm là 60 – 150 phút. 2.2.1.2. Phương pháp trích ly tăng cường SLMSD Để khảo sát hiệu quả thu hồi Indium bằng phương pháp trích ly tăng cường trong đó màng đóng vai trò tạo bề mặt tiếp xúc, sơ đồ thí nghiệm SLMSD đã được lắp đặt. Sau đó, hiệu quả thu hồi Indium ứng với các nồng độ D2EHPA khác nhau đã được khảo sát. Tốc độ chuyển khối của SLMSD với quá trình trích ly truyền thống đã được so sánh và được tìm cách giải thích một cách có hệ thống nguyên nhân gây ra sự thay đổi tốc độ chuyển khối đó. Sơ đồ một hệ thống SLMSD (hình 2.1) bao gồm: 1 – Thùng chứa dung dịch đầu 2 – Bơm dung dịch đầu 3 – Mô đun màng sợi rỗng 4 – Thùng chứa dung dịch hoàn nguyên phân tán trong pha hữu cơ 5- Bơm dung dịch hoàn nguyên – dung dịch hữu cơ Hình 2.1 Sơ đồ hệ thống SLMSD Hình 2.1 thể hiện sơ đồ hệ thống SLMSD. Dung dịch đầu chứa In3+ được tuần hoàn trong các sợi rỗng (phía ống) của mô đun màng 3 bằng bơm dung dịch đầu 2; dung dịch hoàn nguyên (axit HCl 5M) được phân tán trong dung môi trích ly (D2EHPA trong Isopar-L) và sau đó được tuần hoàn ở phía vỏ của mô đun màng bằng bơm dung dịch hoàn nguyên 5. Dung dịch đầu vào và dung môi trích ly tiếp xúc ở bề mặt màng kỵ nước để tạo phức giữa In3+ và D2EHPA theo PTPU 1.1. Phức tạo thành sau đó được khuếch tán qua các mao quản màng tới thùng hoàn nguyên 4 và phản ứng với HCl ở bề mặt tiếp xúc giữa dung dịch hữu cơ và dung dịch hoàn nguyên theo PTPU 1.2. D2EHPA được tái sinh quay lại bề mặt màng – dung dịch đầu để tiếp tục phản ứng với In3+ (hình 2.2). Hình 2.2 Quá trình chuyển khối qua màng Trong sơ đồ này, dung dịch đầu chỉ tiếp xúc dung môi trích ly tại bề mặt màng do tính kỵ nước của màng ngăn cản dung dịch đầu đi qua các mao quản màng. Ở phía dung dịch đầu, ion kim loại Me+ (ở đây là In3+) được khuếch tán qua lớp biên. Sau đó ion kim loại phản ứng với D2EHPA tạo phức. Phức tạo thành được khuếch tán qua màng sang phía dung dịch hoàn nguyên. Tại bề mặt tiếp xúc hai pha phía dung dịch hoàn nguyên, phức phản ứng với axit mạnh tạo muối và giải phóng D2EHPA tự do. Ở đây có hai dòng vật chất di chuyển ngược chiều nhau: dòng Me+ di chuyển từ phía dung dịch đầu sang phía dung dịch hoàn nguyên; dòng H+ di chuyển theo chiều ngược lại tạo nên hiệu ứng ghép cặp. Chừng nào còn duy trì được chênh lệch nồng độ H+ giữa dung dịch hoàn nguyên và dung dịch đầu thì ion kim loại còn có thể vận chuyển sang phía dung dịch hoàn nguyên. Vì phản ứng trích ly ở đây tạo ra H+ nên pH phía dung dịch đầu sẽ giảm. Dùng micropipet để bổ sung NaOH 50% vào thùng chứa dung dịch đầu nhằm giữ pH phía dung dịch đầu không đổi, đồng thời chọn pH của dung dịch
File đính kèm:
luan_an_nghien_cuu_qua_trinh_trich_ly_voi_su_ho_tro_cua_mang.docx
1. Trang bia LA.docx
1. Trang bia LA.pdf
2. Trang phụ bìa LA.docx
2. Trang phụ bìa LA.pdf
3. LỜI CAM ĐOAN.docx
3. LỜI CAM ĐOAN.pdf
4. LỜI CẢM ƠN.docx
4. LỜI CẢM ƠN.pdf
5. LA_DTTNgan_Final 201221_V3.pdf
Bìa tóm tắt LA.docx
Bìa tóm tắt LA.pdf
Tóm tắt LA_201221_V1.docx
Tóm tắt LA_201221_V1.pdf
Trích yếu LA.doc
Trích yếu LA.pdf
TT đưa lên mạng TA_TV.doc
TT đưa lên mạng TA_TV.pdf