Luận án Nghiên cứu thiết kế tối ưu động cơ servo không đồng bộ 3 pha rotor lồng sóc
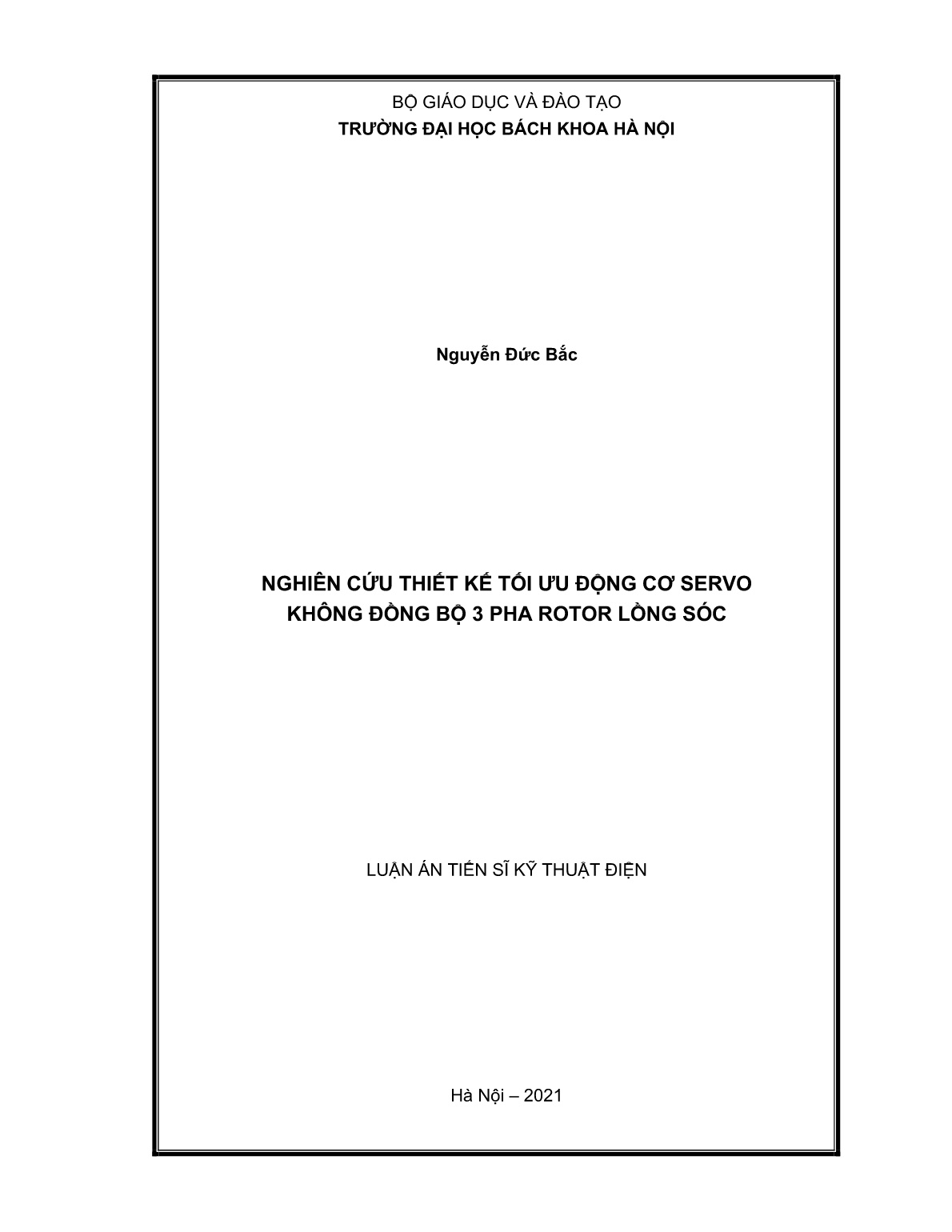
Trang 1
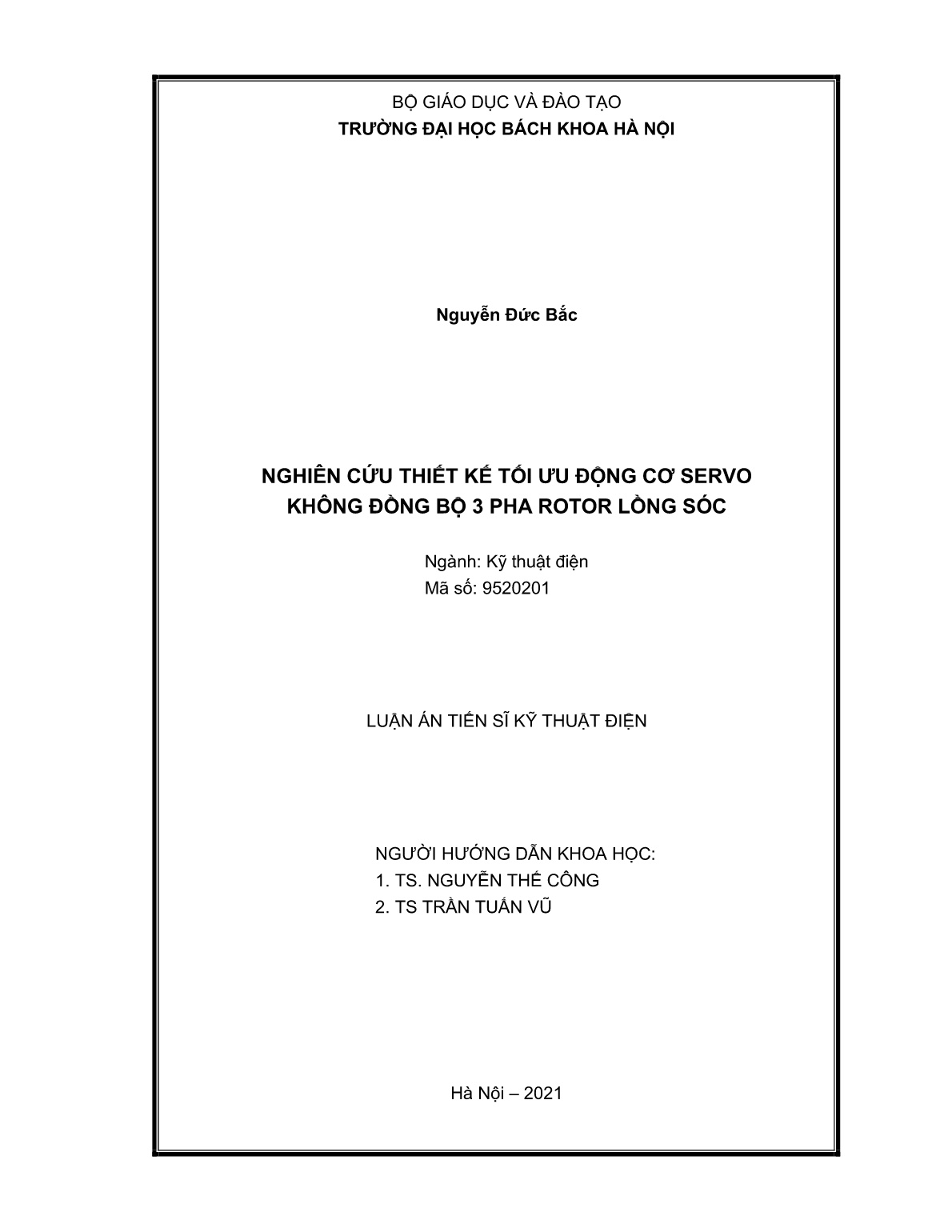
Trang 2
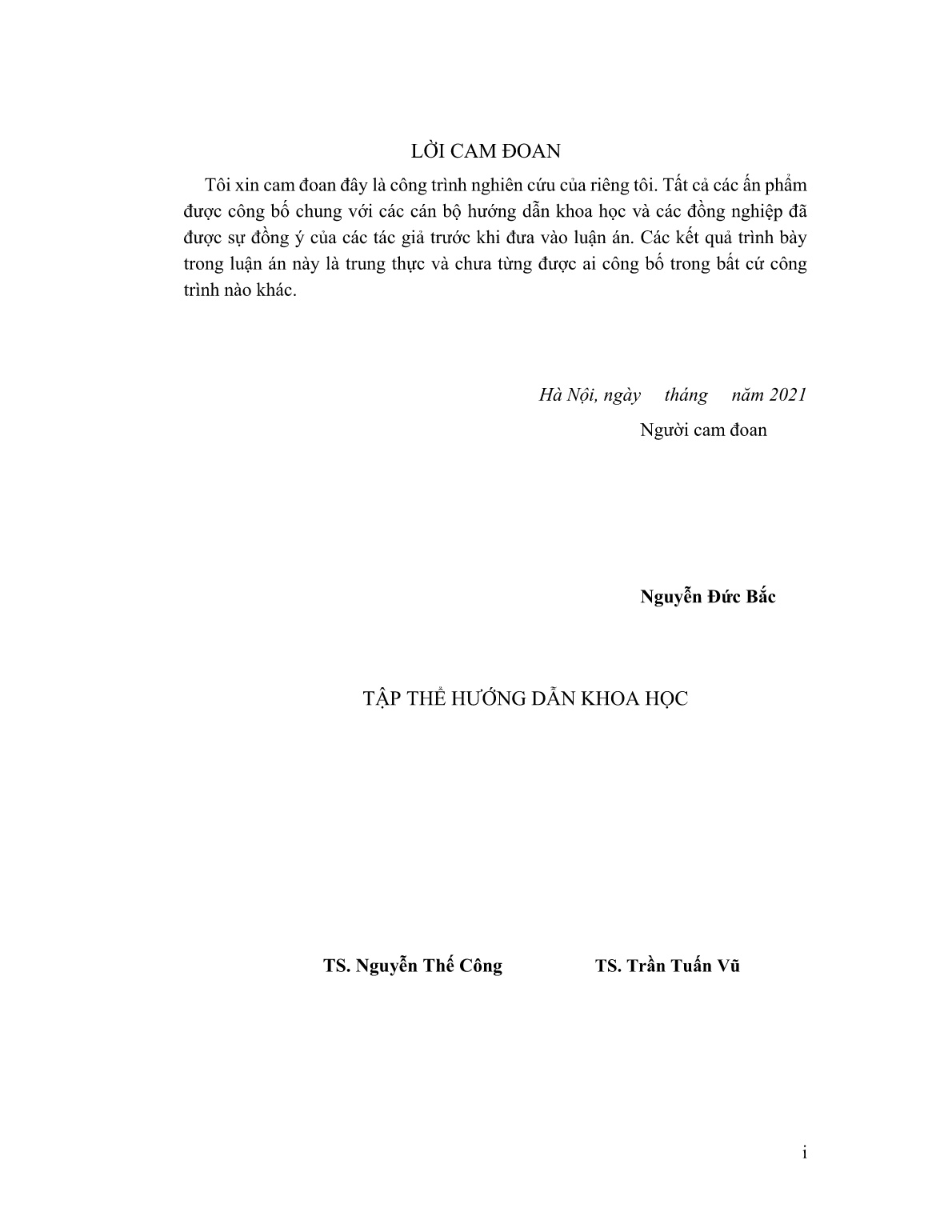
Trang 3
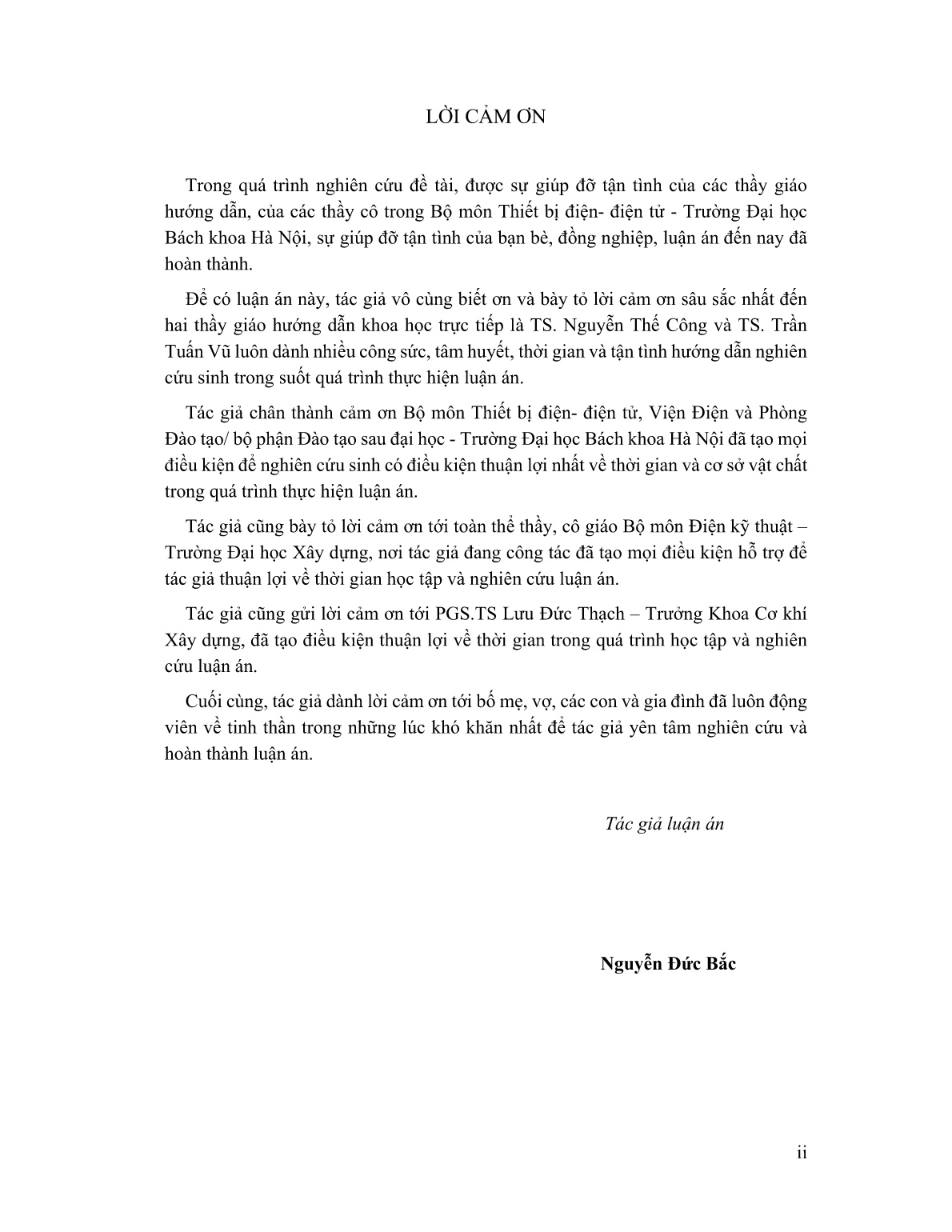
Trang 4
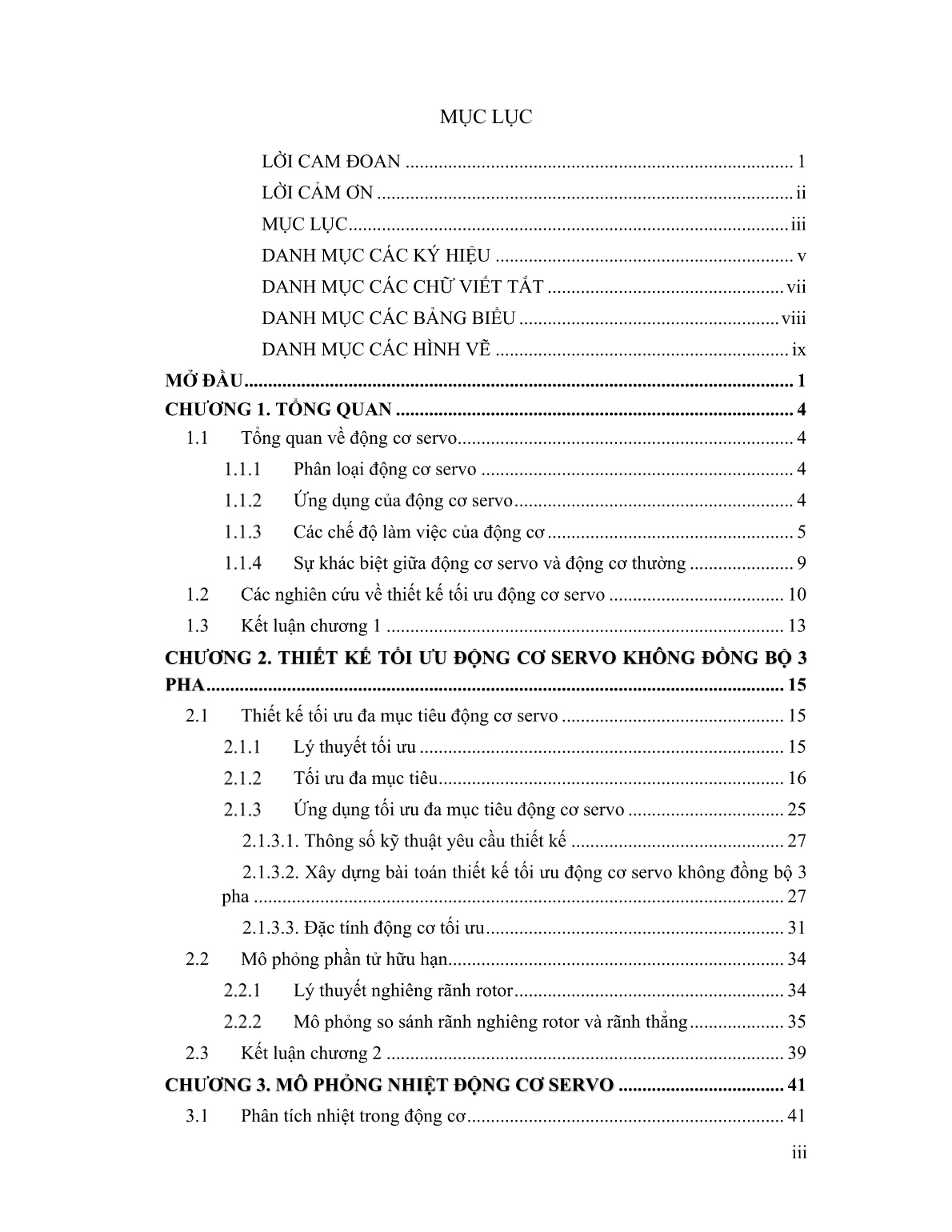
Trang 5
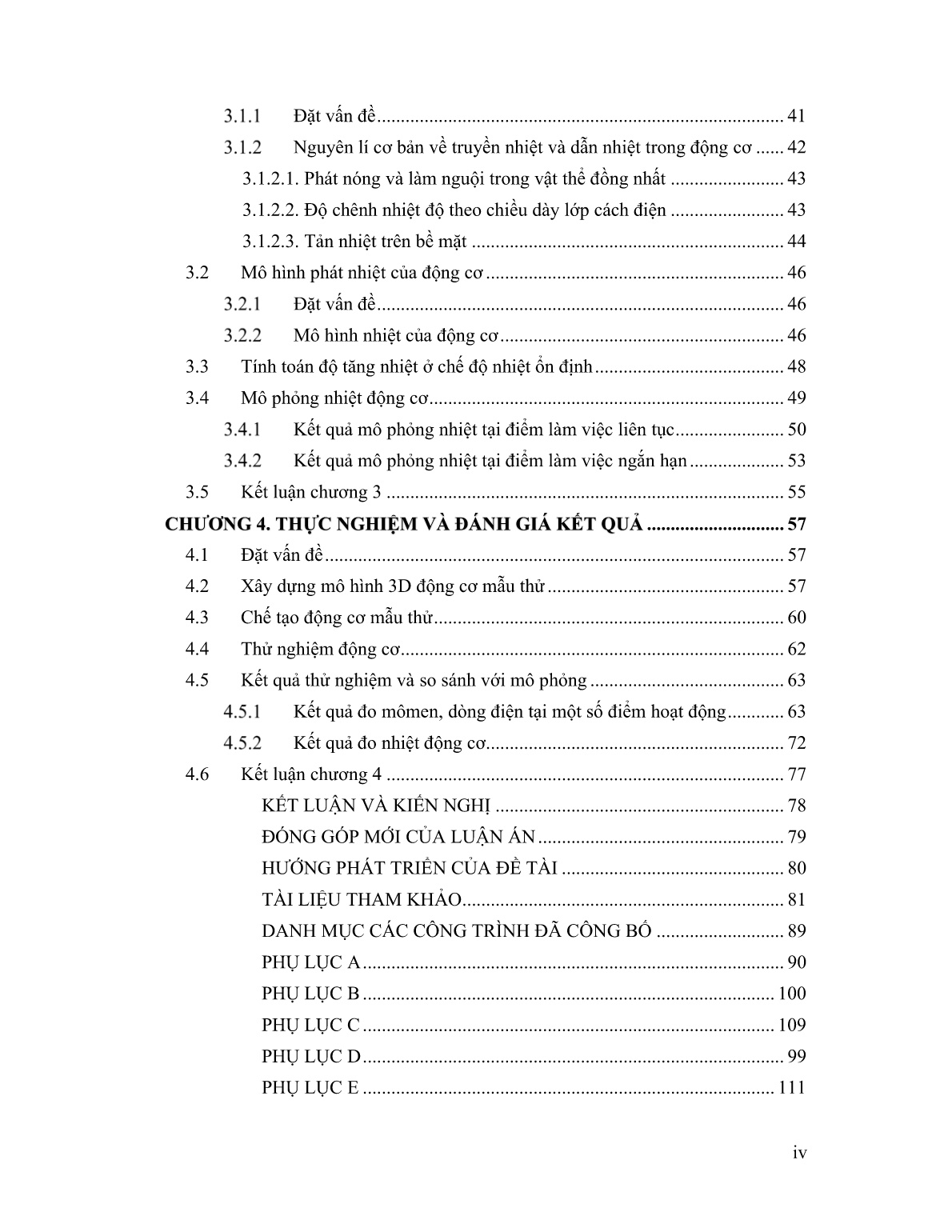
Trang 6
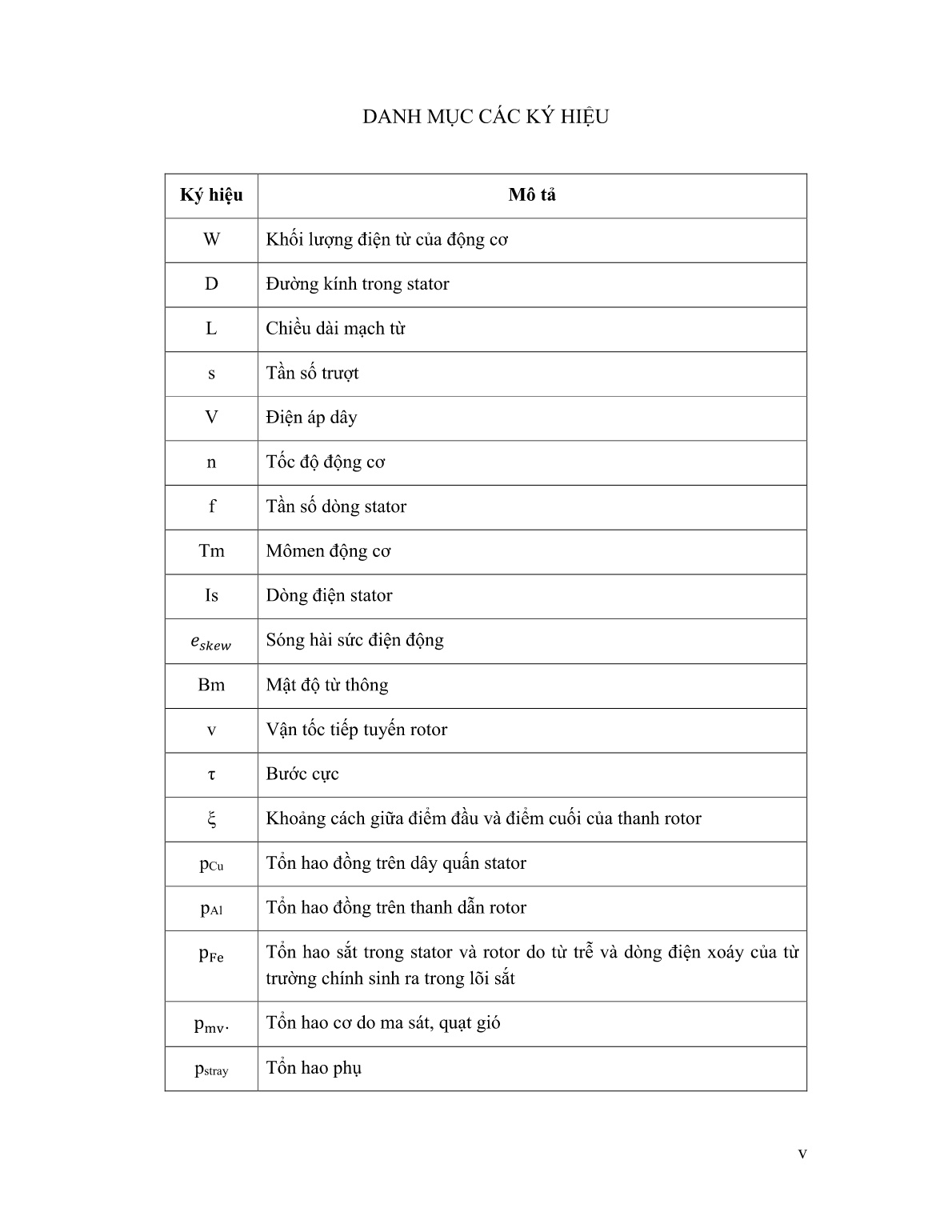
Trang 7
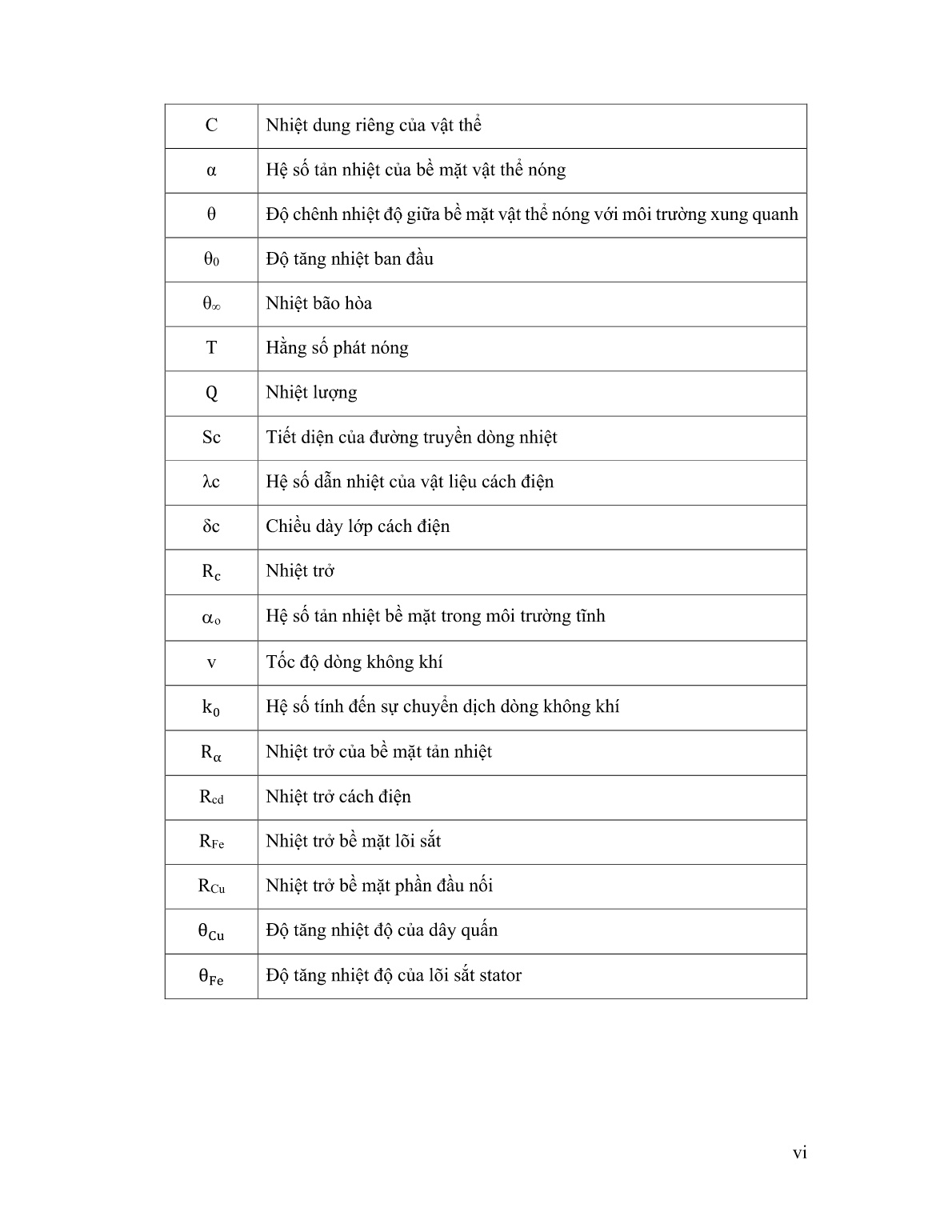
Trang 8
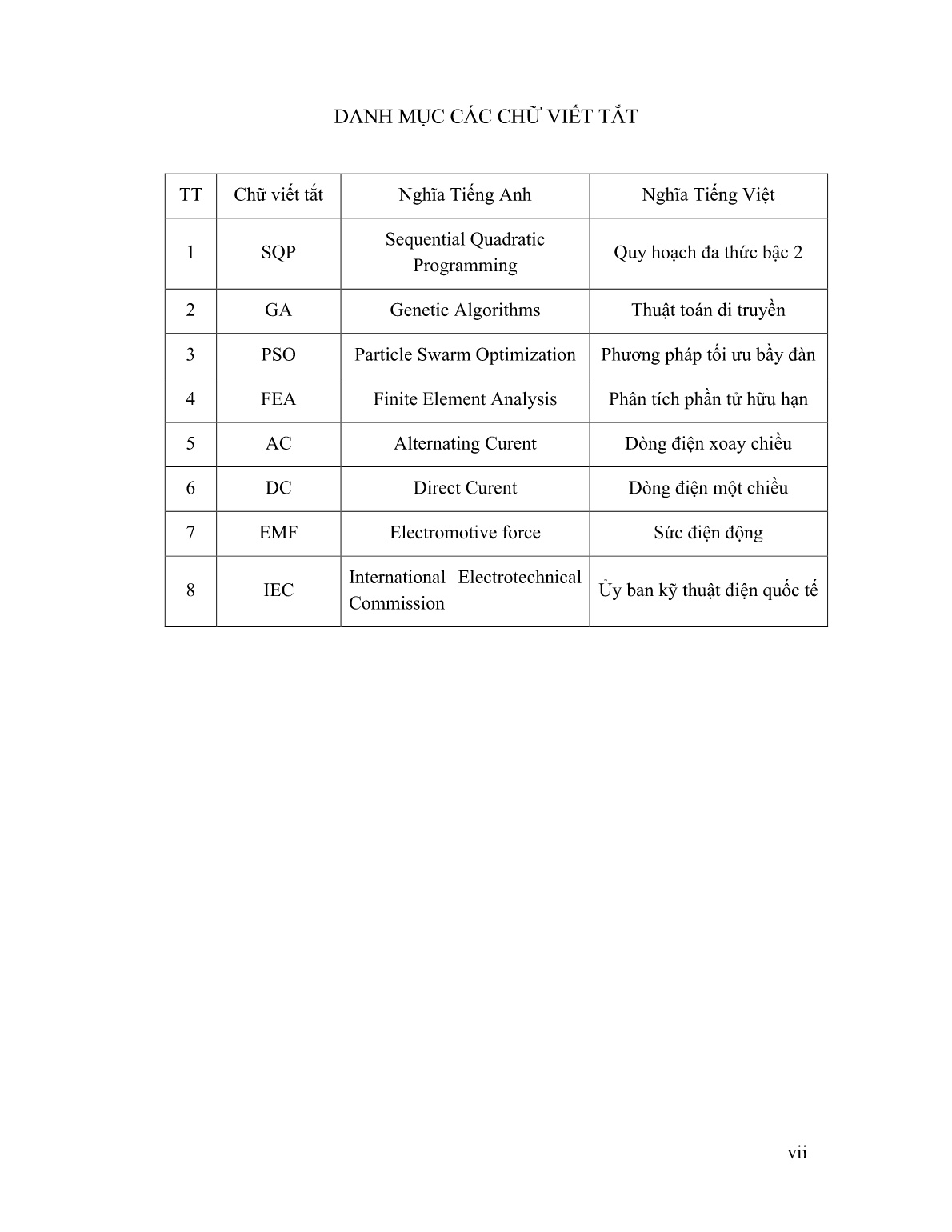
Trang 9
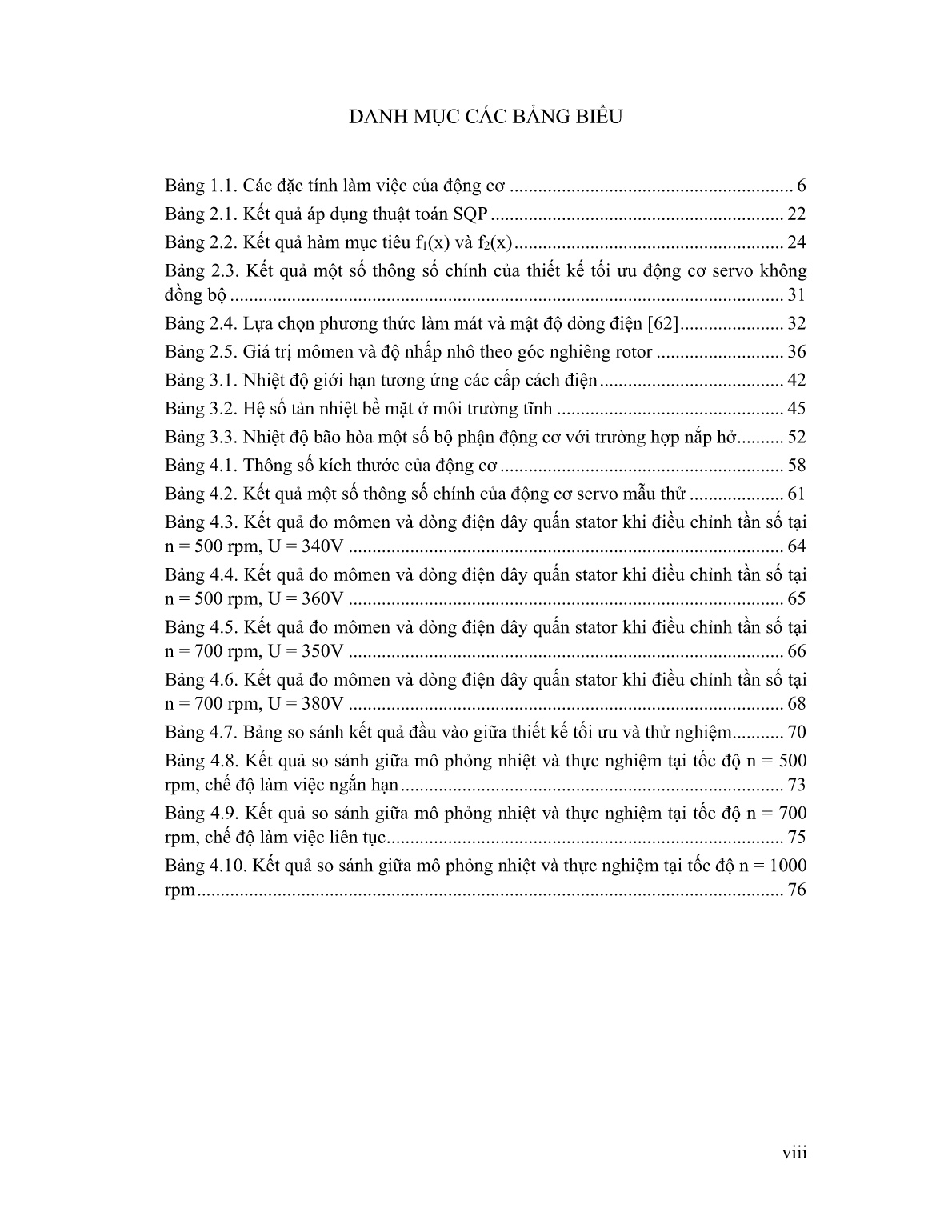
Trang 10
Tải về để xem bản đầy đủ
Bạn đang xem 10 trang mẫu của tài liệu "Luận án Nghiên cứu thiết kế tối ưu động cơ servo không đồng bộ 3 pha rotor lồng sóc", để tải tài liệu gốc về máy hãy click vào nút Download ở trên.
Tóm tắt nội dung tài liệu: Luận án Nghiên cứu thiết kế tối ưu động cơ servo không đồng bộ 3 pha rotor lồng sóc
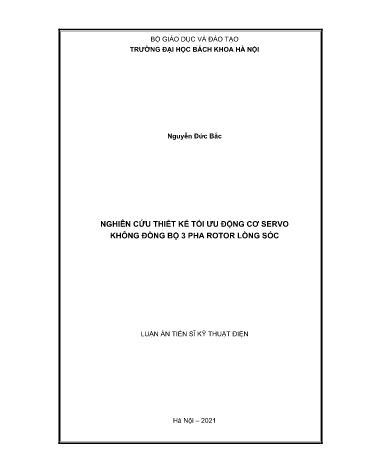
en tại 500 rpm Mômen Ia Ib Ic -10 -8 -6 -4 -2 0 2 4 6 8 10 0 2 4 6 8 10 12 14 16 18 100 110 120 130 140 150 160 170 180 190 D ò ng đ iệ n (A ) M ôm en ( N .m ) Thời gian (ms) Mô phỏng FEA 2D, mômen tại 500 rpm Mômen Ia Ib Ic 38 Tương tự, khi so sánh kết quả mô phỏng FEA 2D của mômen tại n = 3500rpm. Kết quả mômen trung bình thu được là 0,4 N.m, dao động mômen 0,056 N.m khi rãnh nghiêng (Hình 2.19) so với 0,43 N.m (cùng dòng điện) và dao động mômen cực đại là 0,125 N.m khi rãnh thẳng (Hình 2.20). Dao động mômen giảm 55% với giá trị mômen trung bình giảm 7%. Hình 2.19. Kết quả mô phỏng mômen cực đại tại 3500 rpm, rotor rãnh nghiêng Hình 2.20. Kết quả mô phỏng mômen cực đại tại 3500 rpm, rotor rãnh thẳng 39 Tiến hành mô phỏng FEA tại một số điểm hoạt động (tốc độ) khác nhau. So sánh với thiết kế tối ưu, kết quả được thể hiện như trong Hình 2.21. Các kết quả mô phỏng FEA ở chế độ cực đại và liên tục khi so sánh với kết quả thiết kế tối ưu, sai số nhỏ hơn 10%. Hình 2.21. So sánh mô phỏng FEA và thiết kế tối ưu 2.3 Kết luận chương 2 Nội dung chương 2 đã trình bày một phương pháp mới thiết kế tối ưu động cơ sử dụng các thuật toán trên cơ sở tối ưu các thông số kết cấu, điều khiển, ứng dụng cho động cơ servo không đồng bộ 3 pha rotor lồng sóc. Phương pháp thiết kế sử dụng thuật toán tối ưu hóa, nhằm giảm các vòng lặp chế tạo mẫu thử tốn kém về chi phí và thời gian của phương pháp thiết kế máy điện “truyền thống”. Dựa trên phân bổ Pareto đưa ra phương án lựa chọn tốt nhất giữa khối lượng điện từ và mômen cực đại sau khi đánh giá mô hình bằng thuật toán ɛ-constraint kết hợp thuật toán quy hoạch đa thức bậc 2 (SQP) trong Matlab. Một thiết kế tối ưu được lựa chọn trên đặc tính phân bố Pareto với khối lượng điện từ là 9,52 kg, mômen cực đại đạt được là 15 N.m. Một thiết kế khác có thể làm tăng mômen cực đại nhưng với khối lượng lớn hơn. Đặc tính mômen – tốc độ của động cơ servo không đồng bộ được xây dựng với các điểm hoạt 40 động tối ưu của chế độ làm việc liên tục và chế độ cực đại. Thiết kế rotor rãnh nghiêng được so sánh với rotor rãnh thẳng nhờ phân tích mô phỏng FEA. Góc nghiêng tối ưu lựa chọn cho thiết kế động cơ là 7,50C (tương ứng góc nghiêng 1 rãnh). Mô phỏng FEA tại một số điểm hoạt động khác nhau (tốc độ khác nhau) để kiểm nghiệm mô hình thiết kế tối ưu. Kết quả sai số giữa hai mô hình thấp hơn 10%. Các kết quả chương 2 được công bố trong bài báo số [3], [5]. 41 CHƯƠNG 3. MÔ PHỎNG NHIỆT ĐỘNG CƠ SERVO 3.1 Phân tích nhiệt trong động cơ Đặt vấn đề Khi động cơ làm việc sẽ sinh ra tổn hao, biến thành nhiệt năng và làm nóng các bộ phận của động cơ, làm giảm độ tin cậy và tuổi thọ cách điện. Tổn hao càng lớn thì hiệu suất động cơ càng thấp. Khi trạng thái nhiệt trong động cơ ổn định thì toàn bộ nhiệt lượng thoát ra môi trường xung quanh nhờ sự chênh lệch nhiệt giữa các bộ phận của động cơ và môi trường bên ngoài. Tổn hao trong động cơ không đồng bộ gồm các loại sau: - Tổn hao đồng trên dây quấn stator pCu - Tổn hao đồng trên thanh dẫn rotor pAl - Tổn hao sắt trong stator và rotor do từ trễ và dòng điện xoáy của từ trường chính sinh ra trong lõi sắt p . - Tổn hao cơ do ma sát, quạt gió p . - Tổn hao phụ pstray. Tản nhiệt trong động cơ thông qua hai hình thức: truyền nhiệt trong vật rắn và tản nhiệt nhờ bức xạ, đối lưu [70],[71]. Giải quyết bài toán tản nhiệt cho động cơ là vấn đề quan trọng khi thiết kế. Quá trình tính toán nhiệt liên quan chặt chẽ đến việc làm nguội và xác định độ tăng nhiệt θ cho phép giữa dây quấn động cơ và môi trường bên ngoài. Vật liệu cách điện là một trong những vật liệu chủ yếu dùng trong ngành chế tạo máy điên. Khi thiết kế, lựa chọn vật liệu cách điện là một khâu rất quan trọng vì phải đảm bảo máy làm việc tốt với tuổi thọ nhất định, đồng thời giá thành của máy lại không cao [72]–[74]. Khi chọn vật liệu cách điện cần chú ý đến những vấn đề sau: - Vật liệu cách điện phải có độ bền cao, chịu tác dụng cơ học tốt, chịu nhiệt và dẫn nhiệt tốt lại ít thấm nước. - Phải chọn vật liệu cách điện có tính cách điện cao để đảm bảo thời gian làm việc của máy trong điều kiện làm việc bình thường, đồng thời đảm bảo giá thành của máy không cao. - Một trong những yếu tố cơ bản nhất là làm giảm tuổi thọ của vật liệu cách điện (cũng là tuổi thọ của máy) là nhiệt độ. Nếu nhiệt độ vượt quá nhiệt độ cho phép 42 thì chất điện môi, độ bền cơ học của vật liệu giảm đi nhiều, dẫn đến sự già hóa nhanh chóng chất cách điện. Hiện nay, theo nhiệt độ cho phép của vật liệu (nhiệt độ mà vật liệu cách điện làm việc tốt ở điều kiện làm việc bình thường), Ủy ban kỹ thuật điện quốt tế (IEC) - tương ứng với Tiêu chuẩn Việt Nam TCVN 8086:2009 đã chia vật liệu cách điện thành các cấp như Bảng 3.1: Bảng 3.1. Nhiệt độ giới hạn tương ứng các cấp cách điện Cấp cách điện Nhiệt độ giới hạn của dây quấn (°C) Cấp Y 90 Cấp A 105 Cấp E 120 Cấp B 130 Cấp F 155 Cấp H 180 Cấp C >180 Tuỳ theo yêu cầu thực tế trong sử dụng động cơ servo, môi trường làm việcmà các nhà thiết kế sẽ lựa chọn cấp cách điện phù hợp, phụ thuộc vào lựa chọn vật liệu cách điện, tính toán phát nóng và làm mát. Nguyên lí cơ bản về truyền nhiệt và dẫn nhiệt trong động cơ Nguồn nhiệt chủ yếu trong động cơ là tổn hao trong dây quấn và lõi sắt. Nếu cần đi sâu vào quá trình nhiệt độ trong dây quấn và lõi sắt thì phải nghiên cứu sự dẫn nhiệt và truyền nhiệt theo nhiều chiều. Nhưng vì thực tế, việc tính toán nhiệt chỉ cho những kết quả gần đúng cho nên để đơn giản việc tính toán, giả thiết rằng dây quấn, lõi sắt stator, thanh dẫn rotor là những khối có tính dẫn nhiệt rất lớn, nghĩa là những khối đẳng nhiệt [61],[75]. 43 3.1.2.1. Phát nóng và làm nguội trong vật thể đồng nhất Gọi Q là nhiệt lượng phát ra trong một đơn vị thời gian do tổng tổn hao P sinh ra trong một vật thể đồng chất. Trong quá trình đốt nóng, một phần nhiệt lượng Q làm tăng nhiệt độ vật thể, một phần khác tản ra môi trường xung quanh qua mặt ngoài vật thể. Nếu nhiệt lượng Q không đổi, cân bằng năng lượng trong khoảng thời gian dt có dạng: Qdt = Cdθ + αSθdt (3.1) Trong đó: Cdθ: nhiệt lượng đốt nóng vật thể αSθdt: nhiệt lượng khuếch tán ra môi trường xung quanh C: nhiệt dung riêng của vật thể (J/°C) α: hệ số tản nhiệt của bề mặt vật thể nóng θ: độ chênh nhiệt độ giữa bề mặt vật thể nóng với môi trường xung quanh Khi đã đốt nóng vật thể đến mức độ nào đó thì nhiệt độ của vật thể đạt bão hòa (θ =θ∞ = const). Khi đó phương trình (3.1) trở thành: Qdt = αSθ (3.2) Độ tăng nhiệt do đốt nóng là: θ = θ + (θ − θ ) 1 − e ⁄ (3.3) Trong đó: θ0: độ tăng nhiệt ban đầu T là hằng số phát nóng (thời gian cần thiết để vật thể phát nóng đến nhiệt độ ổn định). 3.1.2.2. Độ chênh nhiệt độ theo chiều dày lớp cách điện Nhiệt lượng Q truyền qua chiều dày lớp cách điện trong một đơn vị thời gian được biễu diễn như công thức: 44 Q = θ S λ δ (3.4) Trong đó: θc: độ chênh nhiệt độ Sc: tiết diện của đường truyền dòng nhiệt, λc: hệ số dẫn nhiệt của vật liệu cách điện δc: chiều dày lớp cách điện (chiều dài đường truyền dòng nhiệt) → θ = Q S δ λ = QR (3.5) Với Rc là nhiệt trở. R = 1 λ δ S (3.6) Biểu thức trên tương tự như định luật Ohm trong mạch điện với sự tương ứng giữa θ với U; Q với I và Rc với R. Khi cách điện có nhiều lớp thì nhiệt trở tổng bằng tổng nhiệt trở các lớp: R = R + R +. . . +R (3.7) Và nhiệt dẫn tổng của nhiều lớp cách điện: λ = δ δ λ + δ λ +. . . + δ λ (3.8) Trong đó: δ1, δ2, , δn: chiều dày từng lớp cách điện. λ1, λ2, , λn: hệ số dẫn nhiệt của từng lớp cách điện tương ứng. 3.1.2.3. Tản nhiệt trên bề mặt Quá trình tản nhiệt trên bề mặt một vật thể đang nóng (có nhiệt độ cao hơn nhiệt độ môi trường) được thực hiện bằng bức xạ nhiệt và đối lưu. Nhiệt lượng Q bức xạ ra môi trường phụ thuộc vào tính chất của bề mặt bức xạ (đánh bóng, thô, sơn) và 45 tỷ lệ với nhiệt độ tuyệt đối của bề mặt. Trong trường hợp đối lưu, nhiệt lượng Q tách ra khỏi bề mặt phụ thuộc chủ yếu vào tốc độ khí thổi qua bề mặt. Nhiệt lượng Q tản ra trên bề mặt vật thể nóng do bức xạ và đối lưu được xác định theo công thức: Q = αS θ (3.9) Trong đó: θ = θ − θ : độ chênh nhiệt của bề mặt nóng so với môi trường θ, θ0: Nhiệt độ bề mặt vật thể nóng và nhiệt độ môi trường Q: Nhiệt lượng phát ra trong một giây (W) α: Hệ số tản nhiệt trung bình bề mặt bức xạ và đối lưu, phụ thuộc vào bề mặt tản nhiệt, tốc độ không khí và độ chênh nhiệt θα. Khi tốc độ không khí trên bề mặt tản nhiệt nằm trong khoảng v = 15 ÷ 25 m/s, hệ số tản nhiệt bề mặt được xác định theo công thức sau: α = α (1 + k v) (3.10) Trong đó: o: Hệ số tản nhiệt bề mặt trong môi trường tĩnh (Theo Bảng 3.2) v: Tốc độ dòng không khí. k : hệ số tính đến sự chuyển dịch dòng không khí. ở bề mặt rotor k = 0,1; ở bề mặt phần đầu nối dây quấn stator, k = 0,05 – 0,07. Bảng 3.2. Hệ số tản nhiệt bề mặt ở môi trường tĩnh Tính chất bề mặt o; W/°C.cm2 Mặt gang, thép có trát phủ chỗ gồ ghề và sơn (vỏ và nắp, gối trục của máy) 1,42.10-3 Mặt gang, thép không trát phủ, có sơn 1,67.10-3 Mặt đồng có phủ sơn 1,33.103 46 Độ chênh nhiệt giữa bề mặt tản nhiệt với môi trường: θ = Q αS = q 1 α (3.11) Trong đó q = Q/S là dòng nhiệt qua đơn vị bề mặt tản nhiệt. Nhiệt trở của bề mặt tản nhiệt được xác định: R = θ Q = 1 αS (3.12) 3.2 Mô hình phát nhiệt của động cơ Đặt vấn đề Từ trước đến nay, việc phân tích nhiệt trong động cơ ít nhận được sự quan tâm hơn so với phân tích điện từ [76]. Minh chứng cho điều đó thể hiện trong số lượng các ấn phẩm liên quan được công bố. Quá trình nhiệt và điện từ liên quan và ảnh hưởng lẫn nhau. Dựa vào quá trình mô phỏng nhiệt [77],[78], có thể tối ưu hóa sản phẩm khi biết giới hạn ngưỡng nhiệt độ vật liệu các thành phần trong động cơ. Phân tích nhiệt trong động cơ điện [79]–[83] có thể chia thành hai loại cơ bản, phương pháp phân tích mạch và phương pháp số: - Phương pháp phân tích mạch [84]–[86] có ưu điểm tính toán nhanh, tuy nhiên đòi hỏi phải xác định được chính xác mô hình mạch các đường truyền nhiệt chính. Ở dạng cơ bản, việc phân tích mạng truyền nhiệt bao gồm dẫn nhiệt, đối lưu và bức xạ của các bộ phận trong động cơ. - Phương pháp số [87] cho phép có thể mô hình hóa bất cứ bộ phận nào, tuy nhiên đòi hỏi việc thiết lập mô hình phức tạp và thời gian tính toán kéo dài. Mô hình nhiệt của động cơ Do có sự tương đồng giữa các mô hình mạch điện và mạch nhiệt nên sự truyền nhiệt trong động cơ có thể được biểu diễn dưới dạng một mô hình mạch, trong đó các nhiệt trở tương ứng với điện trở, dòng nhiệt tương ứng với dòng điện và độ chênh nhiệt tương ứng với điện áp [88]–[90]. Mô hình nhiệt của động cơ [91]–[93] được xây dựng dựa trên các hướng chính của dòng nhiệt trong động cơ không đồng bộ như trong Hình 3.1. 47 Hình 3.1. Hướng truyền nhiệt trong động cơ [88] Trong đó: 1. Thanh dẫn rotor 6. Vỏ 2. Dây quấn stator 7. Không khí đầu dây sau 3. Lõi sắt stator 8. Không khí đầu dây trước 4. Đầu dây stator sau 9. Nắp trước 5. Đầu dây stator trước 10. Nắp sau Các hướng của dòng nhiệt : - Dòng nhiệt từ các thanh dẫn rotor truyền qua khe hở không khí, cuộn dây stator đến lõi sắt stator rồi cuối cùng đến môi trường xung quanh qua vỏ bằng đối lưu. - Dòng nhiệt từ đầu cuộn dây stator và các thanh dẫn rotor hướng về phía không khí ở nắp và đến môi trường xung quanh qua nắp bằng đối lưu. Mô hình nhiệt của động cơ [94],[95] chứa các thành phần sau: - Nguồn nhiệt: được sinh ra trong động cơ do các tổn hao trong lõi thép, trong dây quấn (bỏ qua tổn hao do ma sát trên trục) 48 - Nhiệt trở: kết nối giữa hai nút lân cận, điện trở nhiệt cản trở sự truyền nhiệt từ thành phần này qua thành phần khác, phụ thuộc vào kích thước hình học và tính chất vật liệu. - Nhiệt dung: phụ thuộc vào đặc tính của vật liệu. Hình 3.2 cho thấy mô hình mạng nhiệt được xây dựng. Đây là sơ đồ được sử dụng để phân tích nhiệt ở trạng thái ổn định. Phần nhiệt bức xạ (ký hiệu bằng chữ R) và đối lưu (ký hiệu bằng nhiệt dung C) ra ngoài môi trường. Các giá trị nhiệt trở trong mô hình được tính từ các dữ liệu như kích thước động cơ và vật liệu. Công suất nhiệt được kết nối với các nút trong sơ đồ. Mỗi giá trị dung nhiệt được tính từ công suất nhiệt và trọng lượng riêng của các thành phần trong động cơ. Hình 3.2. Mô hình nhiệt động cơ 3.3 Tính toán độ tăng nhiệt ở chế độ nhiệt ổn định Việc tính toán và lựa chọn phương thức làm mát [96]–[99] ảnh hưởng rất lớn đến nhiệt độ của động cơ, vì vậy từ việc tính nhiệt và chọn kết cấu làm mát cho động cơ phải được tiến hành song song và qua lại với nhau để đảm bảo nhiệt độ làm việc của máy. 49 Động cơ có hai nguồn nhiệt chủ yếu là tổn hao đồng của dây quấn stator và tổn hao sắt của lõi sắt stator (Trong phần này trình bày độ tăng nhiệt của dây quấn stator và lõi sắt stator). Để đơn giản hóa, coi dây quấn và lõi sắt là những khối đồng nhất thì dòng nhiệt của dây quấn đi ra môi trường xung quanh theo hai đường: - Qua cách điện rãnh vào lõi sắt rồi tản ra bề mặt lõi sắt với nhiệt trở cách điện Rcd và nhiệt trở bề mặt lõi sắt RFe - Từ phần đầu nối dây quấn với nhiệt trở bề mặt phần đầu nối RCu ra môi trường. Độ tăng nhiệt độ của dây quấn được xác định: θ = [Q (1 + R /R ) + Q ]R 1 + (R R ⁄ ) + (R R ⁄ ) (3.13) Độ tăng nhiệt độ của lõi sắt stator: θ = Q R + θ 1 + R /R (3.14) 3.4 Mô phỏng nhiệt động cơ Motor-CAD là phần mềm mô phỏng quá trình phát nhiệt trong khi hoạt động của các loại động cơ, dựa trên phân tích mạch tập trung. Dựa trên kết quả phân tích nhiệt, giúp tối ưu trong quá trình thiết kế tản nhiệt cho động cơ. Phương pháp phân tích mạch tập trung có lợi thế hơn về tốc độ tính toán so với các phương pháp số. Mô hình nhiệt được phân tích tương tự như mô hình mạch điện với việc tính toán các điện trở nhiệt, đối lưu và bức xạ cho các bộ phận khác nhau của kết cấu động cơ. Khả năng tính toán và cho ra kết quả gần như tức thì cho phép Motor-CAD thực hiện dễ dàng các phương án thay đổi khác nhau [100]–[102]. Các nút được tự động đặt tại các điểm quan trọng trên mặt cắt của động cơ, được liên kết bởi các điện trở dẫn nhiệt, đối lưu và bức xạ. Nguồn nhiệt phát ra từ các tổn hao trong dây quấn stator, thanh dẫn rotor, mạch từ, cơ. Tính toán và giải quyết vấn đề tản nhiệt cho động cơ là một việc rất quan trọng. Thiết kế nhiệt phải đảm bảo nhiệt độ dây quấn không được vượt quá giới hạn của lớp cách điện được chọn. Khi thay đổi các cấu trúc và phương thức làm mát khác nhau đối với động cơ, nhiệt độ các bộ phận trong động cơ sẽ thay đổi. Dựa trên các kết quả 50 phân tích nhiệt và giới hạn ngưỡng nhiệt độ của cấp cách điện, có thể lựa chọn kết cấu làm mát tối ưu cho động cơ [103]. Kết quả mô phỏng nhiệt tại điểm làm việc liên tục *) Trường hợp nắp động cơ kín Hình 3.3 biểu diễn nhiệt độ theo thời gian của một số bộ phận trong động cơ servo không đồng bộ ở chế độ làm việc liên tục, làm mát tự nhiên tại tốc độ n=500rpm, mômen đạt được của động cơ M = 4,8 N.m. Nhiệt độ môi trường là 400C, sau khoảng thời gian 3,8h nhiệt độ động cơ đạt bão hòa. Hình 3.3. Nhiệt độ động cơ theo thời gian, chế độ làm việc liên tục, làm mát tự nhiên Mặt cắt nhiệt của động cơ (Hình 3.4, Hình 3.5) thể hiện các giá trị nhiệt điển hình tại một số bộ phận trong động cơ như vỏ, dây quấn, ổ bi ở chế độ làm việc liên tục tại tốc độ n=500 rpm. Kết quả phân tích nhiệt cho thấy, nhiệt độ của dây quấn stator là 154,80C, mạch từ stator là 149,60C, thanh dẫn lồng sóc là 1770C, nhiệt độ vỏ là 143,80C và ổ bi là 144,30C. Các thông số trong mô hình nhiệt của động cơ thiết kế được lựa chọn cấp cách điện (nhiệt) là cấp F. Qua phân tích kết quả nhận được trong trường hợp nắp kín chúng ta nhận thấy nhiệt độ trên dây quấn stator và rotor ở ngưỡng và vượt quá điều kiện cho phép của cấp F (<1550C). Để thoả mãn điều kiện cấp F, tiếp tục thực hiện mô phỏng với nắp hở để kiểm tra và có kết luận lựa chọn kết cấu nắp khi làm mát tự nhiên. 51 Hình 3.4. Mặt cắt nhiệt dọc trục của động cơ, làm mát tự nhiên, chế độ liên tục Hình 3.5. Mặt cắt nhiệt ngang trục của động cơ, làm mát tự nhiên, chế độ liên tục *) Khi thiết kế hở nắp động cơ Khi thiết kế nắp hở cho động cơ, nhiệt độ trong động cơ sẽ giảm (diện tích phần nắp hở lựa chọn là 10%). Hình 3.6 biểu diễn nhiệt độ theo thời gian của một số bộ phận trong động cơ ở chế độ làm việc liên tục, làm mát tự nhiên tại tốc độ n=500rpm khi thiết kế hở nắp, sau khoảng thời gian 3,3h nhiệt độ động cơ đạt bão hòa. 52 Hình 3.6. Nhiệt độ động cơ theo thời gian, chế độ làm việc liên tục, làm mát tự nhiên với thiết kế hở nắp Mặt cắt nhiệt của động cơ (Hình 3.7) thể hiện các giá trị nhiệt điển hình tại một số bộ phận trong động cơ như vỏ, dây quấn, ở chế độ làm việc liên tục tại tốc độ n=500 rpm khi thiết kế nắp hở. Hình 3.7. Mặt cắt nhiệt ngang trục của động cơ, làm mát tự nhiên, chế độ liên tục với thiết kế hở nắp. Kết quả chi tiết thể hiện các giá trị nhiệt điển hình tại một số bộ phận trong động cơ như trong Bảng 3.3. Bảng 3.3. Nhiệt độ bão hòa một số bộ phận động cơ với trường hợp nắp hở Nhiệt độ bão hòa (0C) Dq stator Stator Lồng sóc Rotor Trục Vỏ 94,1 90,5 106,4 105,7 104,4 87,1 53 Kết quả phân tích nhiệt cho thấy, nhiệt độ bão hòa của dây quấn stator là 940C, giảm 39% so với thiết kế nắp kín. Trong trường hợp này, thời gian để động cơ đạt nhiệt độ bão hòa nhanh hơn (3,3h so với 3,8h với nắp kín). Phân tích kết quả nhận được trong trường hợp nắp hở chúng ta nhận thấy nhiệt độ các bộ phận trong động cơ đều thỏa mãn điều kiện cho phép của cấp F (<1550C). Chính vì vậy tác giả lựa chọn kết cấu nắp hở, làm mát tự nhiên để chế tạo mẫu thử. Kết quả mô phỏng nhiệt tại điểm làm việc ngắn hạn *) Trường hợp nắp động cơ kín Hình 3.8 thể hiện độ nhiệt độ theo thời gian của một số bộ phận chính của động cơ tại n = 500 rpm, mômen cực đại Mmax = 15 N.m, chế độ làm việc ngắn hạn. Khoảng thời gian nhiệt độ dây quấn động cơ đạt đến giới hạn ngưỡng nhiệt độ cho phép của cấp cách điện F với chế độ làm mát tự nhiên là 900s. Hình 3.8. Nhiệt độ động cơ theo thời gian, chế độ làm việc ngắn hạn, làm mát tự nhiên Trong Hình 3.8 thể hiện khoảng thời gian làm việc ngắn hạn của động cơ cho đến khi động cơ đạt nhiệt độ giới hạn ngưỡng tới hạn cho phép (cấp cách điện F cho dây quấn và chọn ngưỡng nhiệt độ cực đại của các bộ phận khác như lồng sóc hay rotor là 2200C). Sử dụng phương pháp làm mát tự nhiên, động cơ có thể làm việc trong khoảng thời gian 900s, để nhiệt độ dây quấn đạt 155,60C và nhiệt độ tại điểm cao nhất của động cơ ở thanh dẫn lồng sóc là 207,50C. Mặt cắt nhiệt của động cơ (Hình 3.9, Hình 3.10) thể hiện các giá trị nhiệt điển hình tại một số bộ phận trong động cơ như vỏ, dây quấn, ổ bi ở chế độ làm việc ngắn hạn tại tốc độ n=500 rpm. 54 Hình 3.9. Mặt cắt nhiệt dọc trục của động cơ, làm mát tự nhiên, chế độ ngắn hạn Hình 3.10. Mặt cắt nhiệt ngang trục của động cơ, làm mát tự nhiên, chế độ ngắn hạn *) Khi thiết kế hở nắp động cơ Hình 3.11 thể hiện độ nhiệt độ theo thời gian của một số bộ phận chính của động cơ tại n = 500 rpm, làm mát tự nhiên, chế độ làm việc ngắn hạn khi thiết kế nắp hở. Khoảng thời gian nhiệt độ dây quấn động cơ đạt đến giới hạn ngưỡng nhiệt độ cho phép của cấp cách điện F trong trường hợp này là 990s, thời gian làm việc ngắn hạn của động cơ tăng lên 10% (so với 900s trong trường hợp nắp kín). Khi đó nhiệt độ dây quấn đạt 152,50C và nhiệt độ tại điểm cao nhất của động cơ ở thanh dẫn lồng sóc là 212,70C (Hình 3.12). 55 Hình 3.11. Nhiệt độ động cơ theo thời gian, chế độ
File đính kèm:
luan_an_nghien_cuu_thiet_ke_toi_uu_dong_co_servo_khong_dong.pdf
Thông tin bằng tiếng Anh.pdf
Thông tin bằng tiếng Việt.pdf
Tóm tắt luận án.pdf
Trích yếu luận án.pdf