Luận án Nghiên cứu tổ hợp vật liệu sơn chịu nhiệt trên cơ sở nhựa silicon và định hướng sử dụng
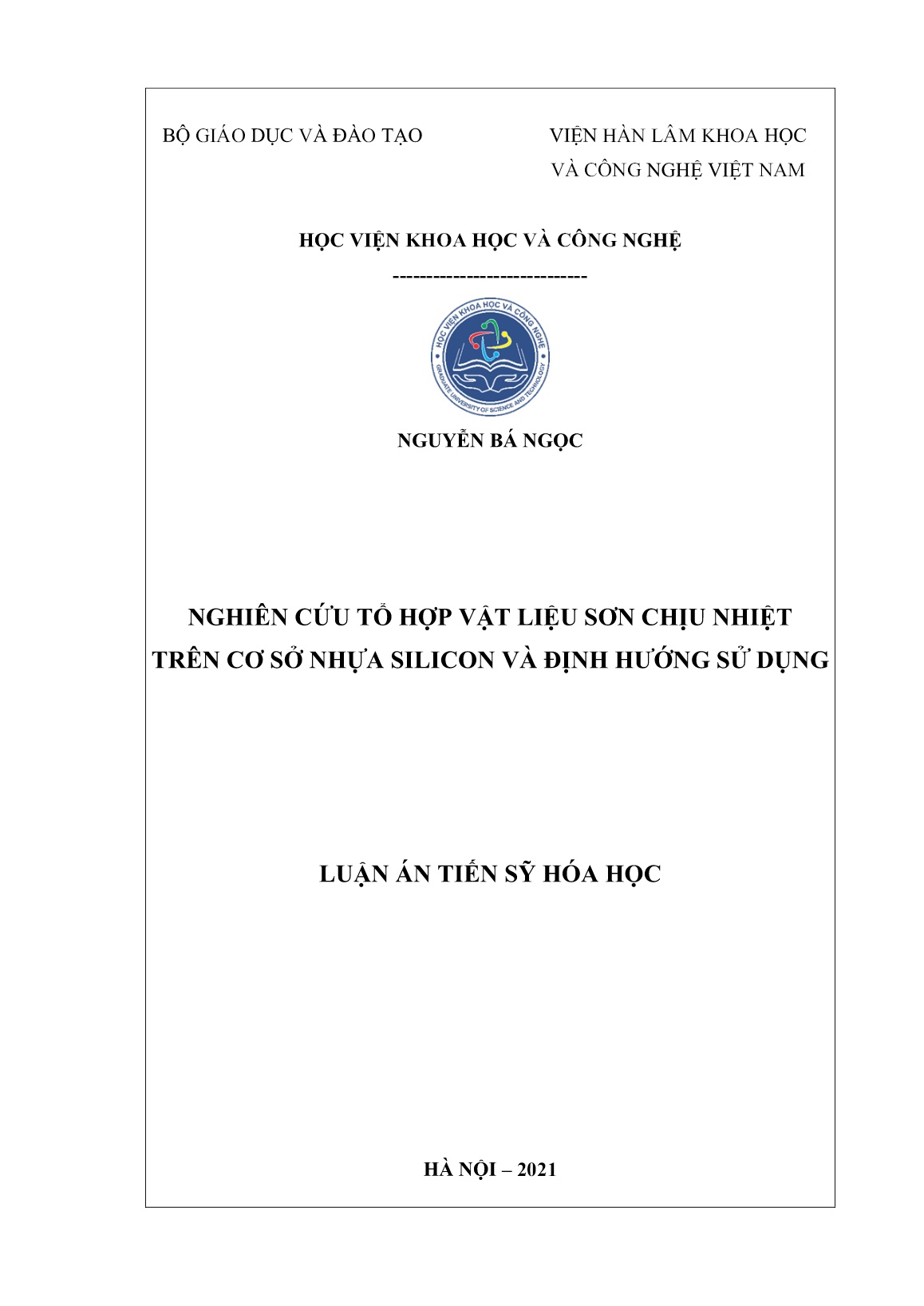
Trang 1
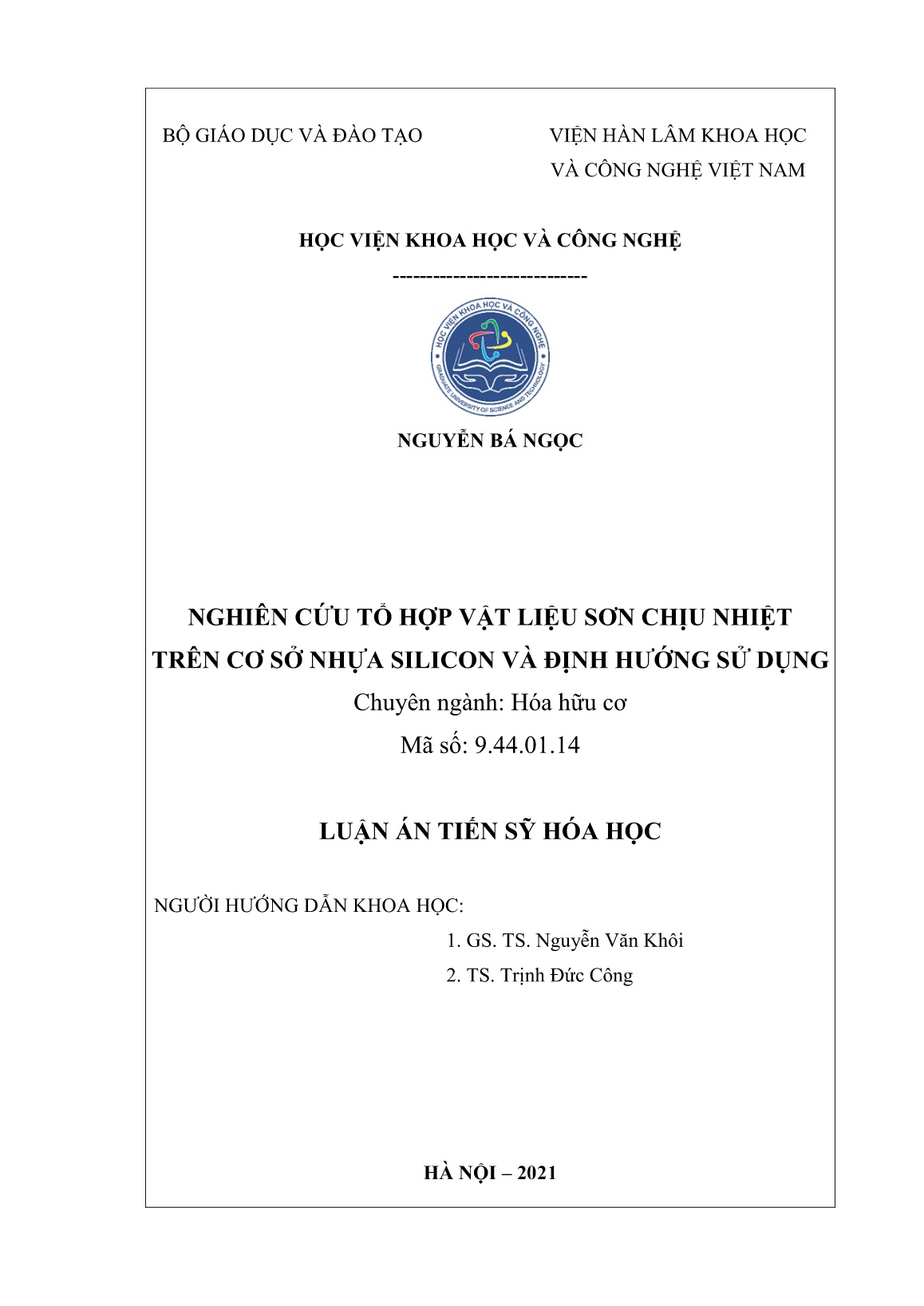
Trang 2
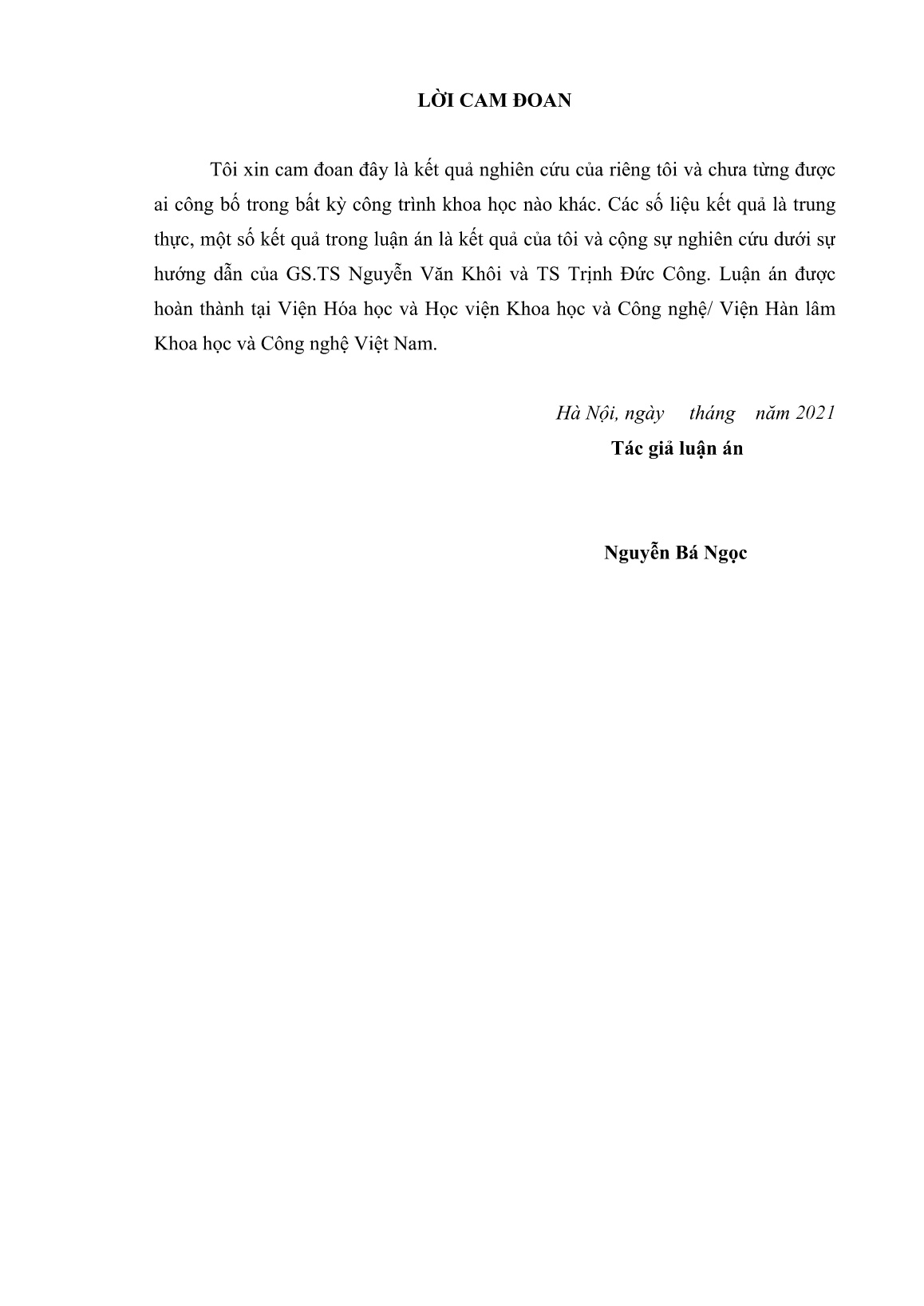
Trang 3
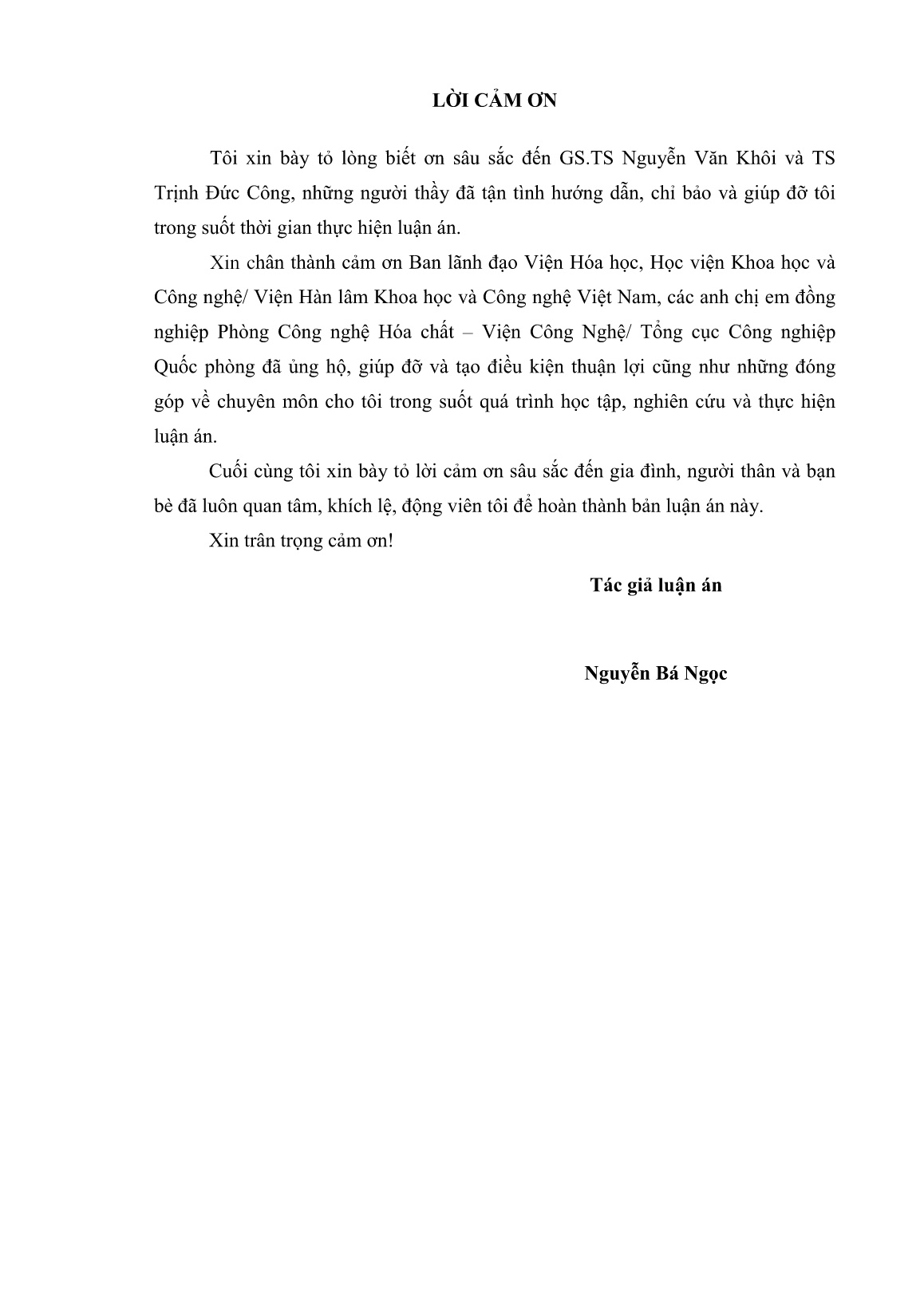
Trang 4
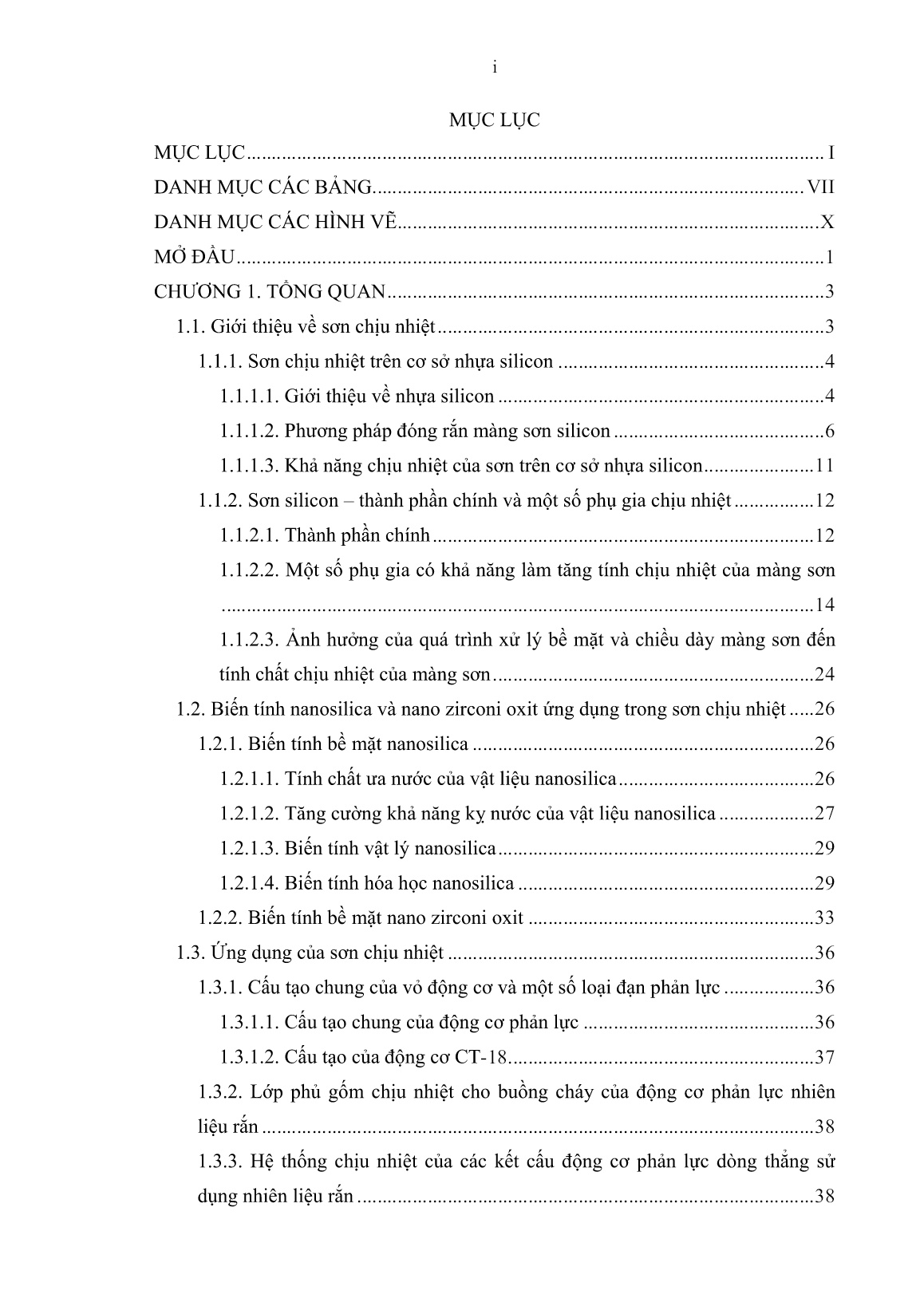
Trang 5
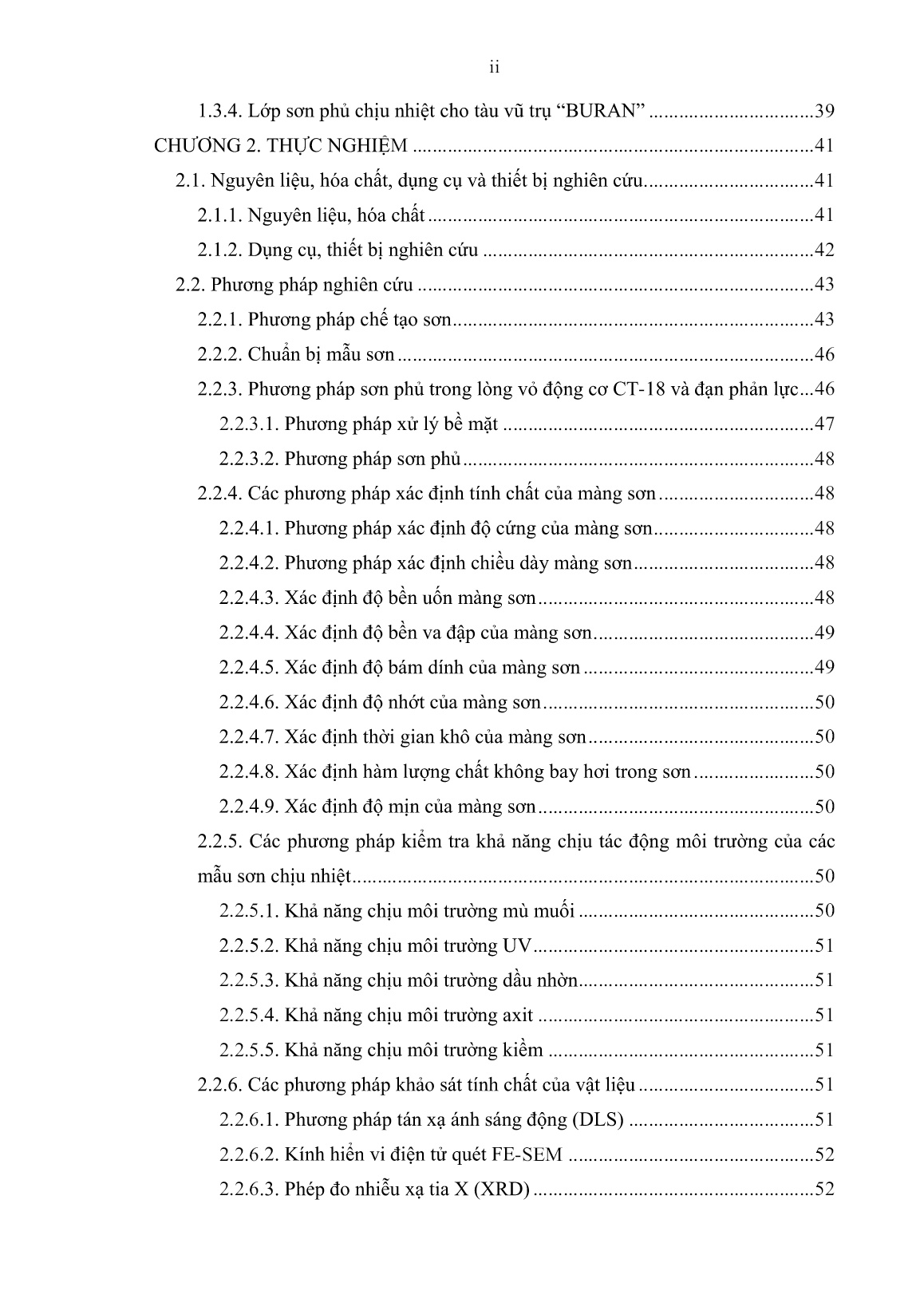
Trang 6
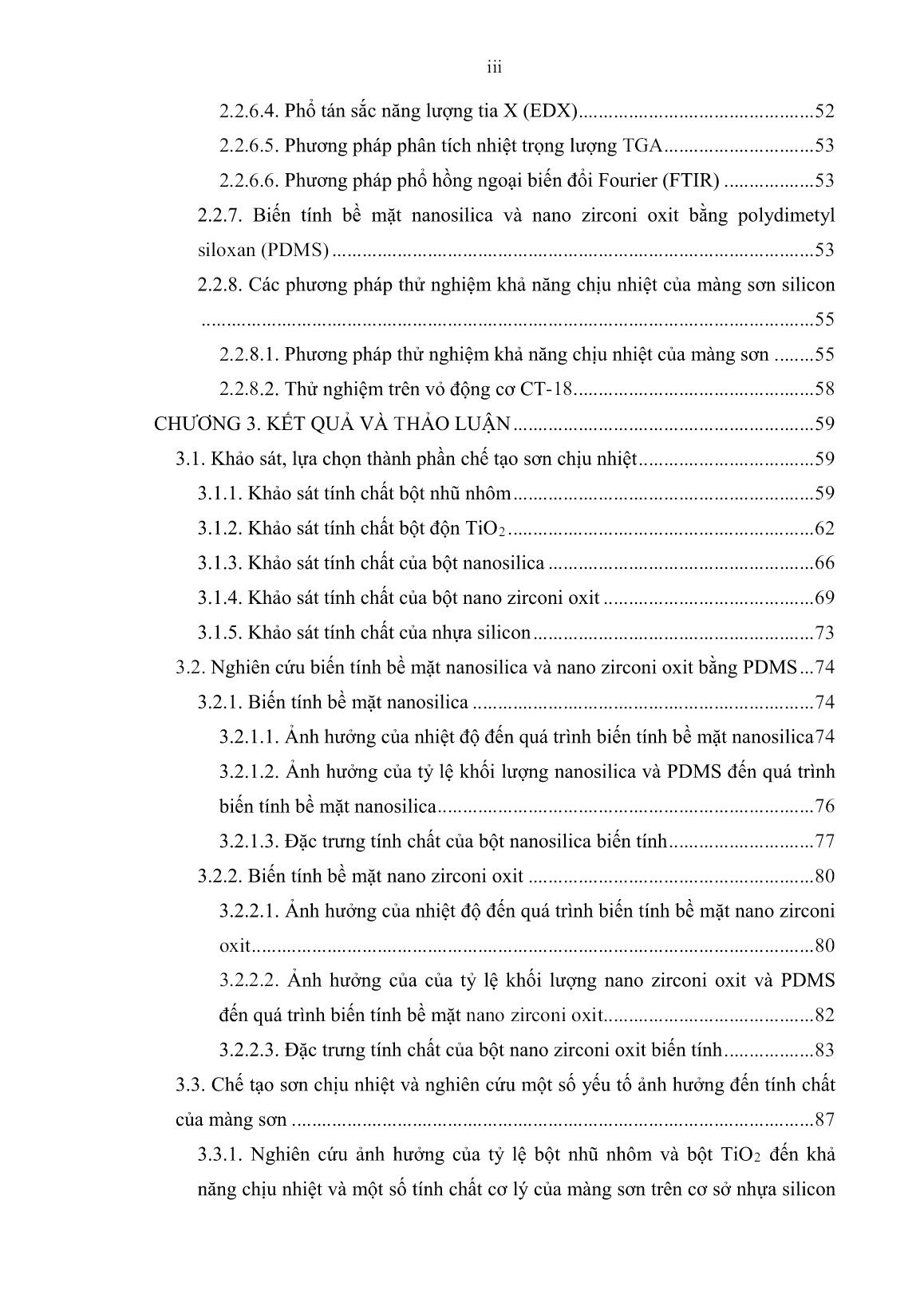
Trang 7
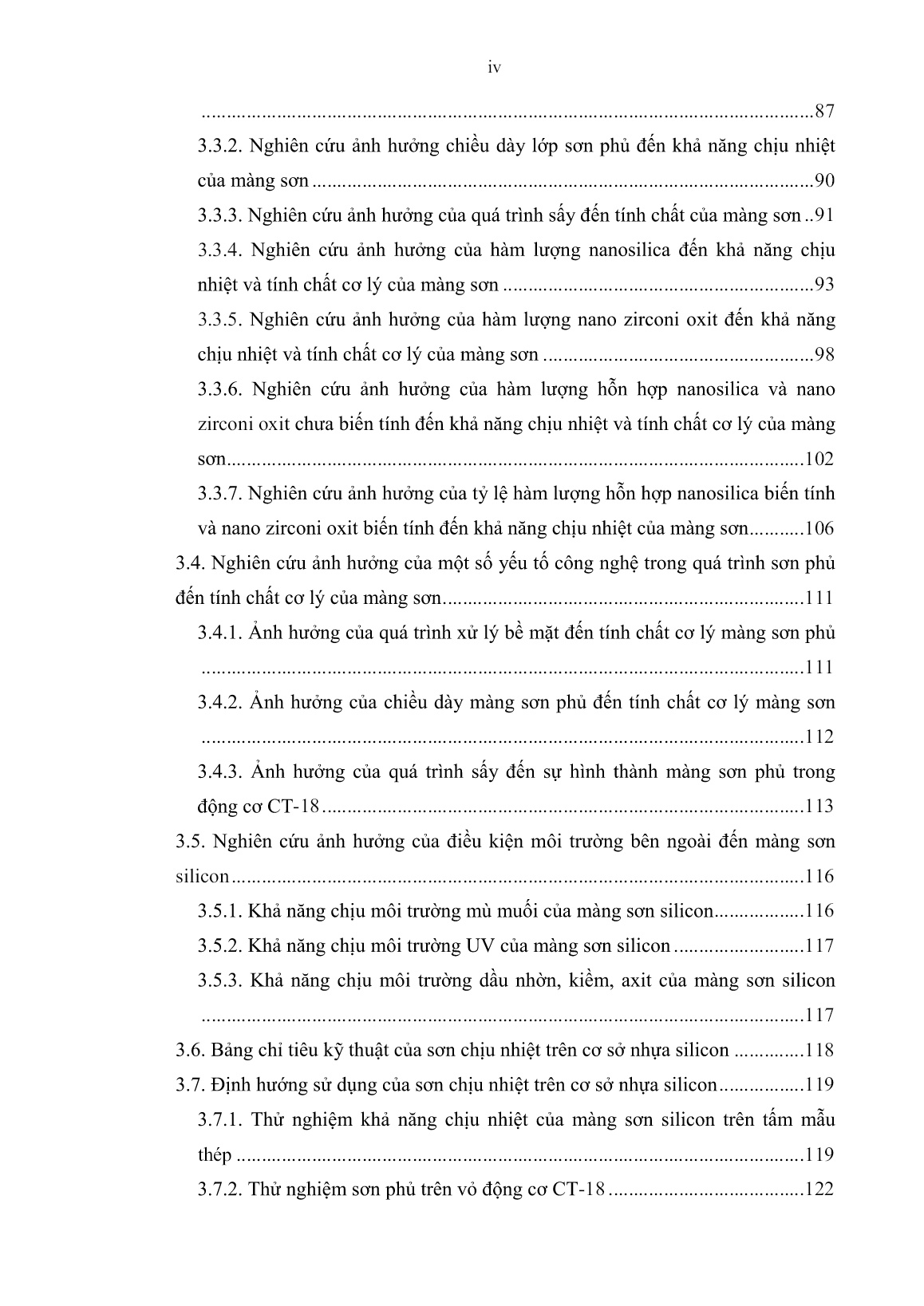
Trang 8
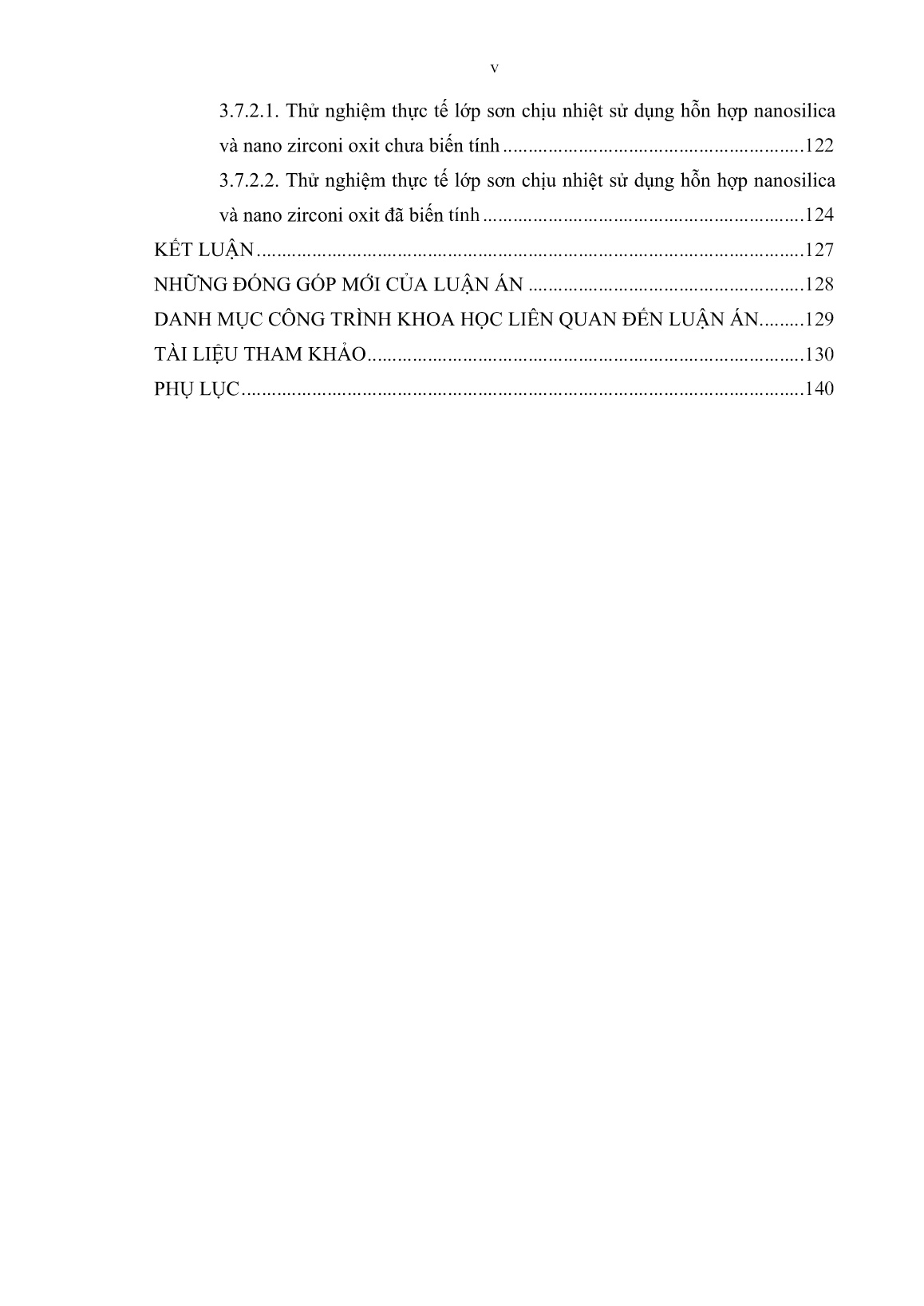
Trang 9
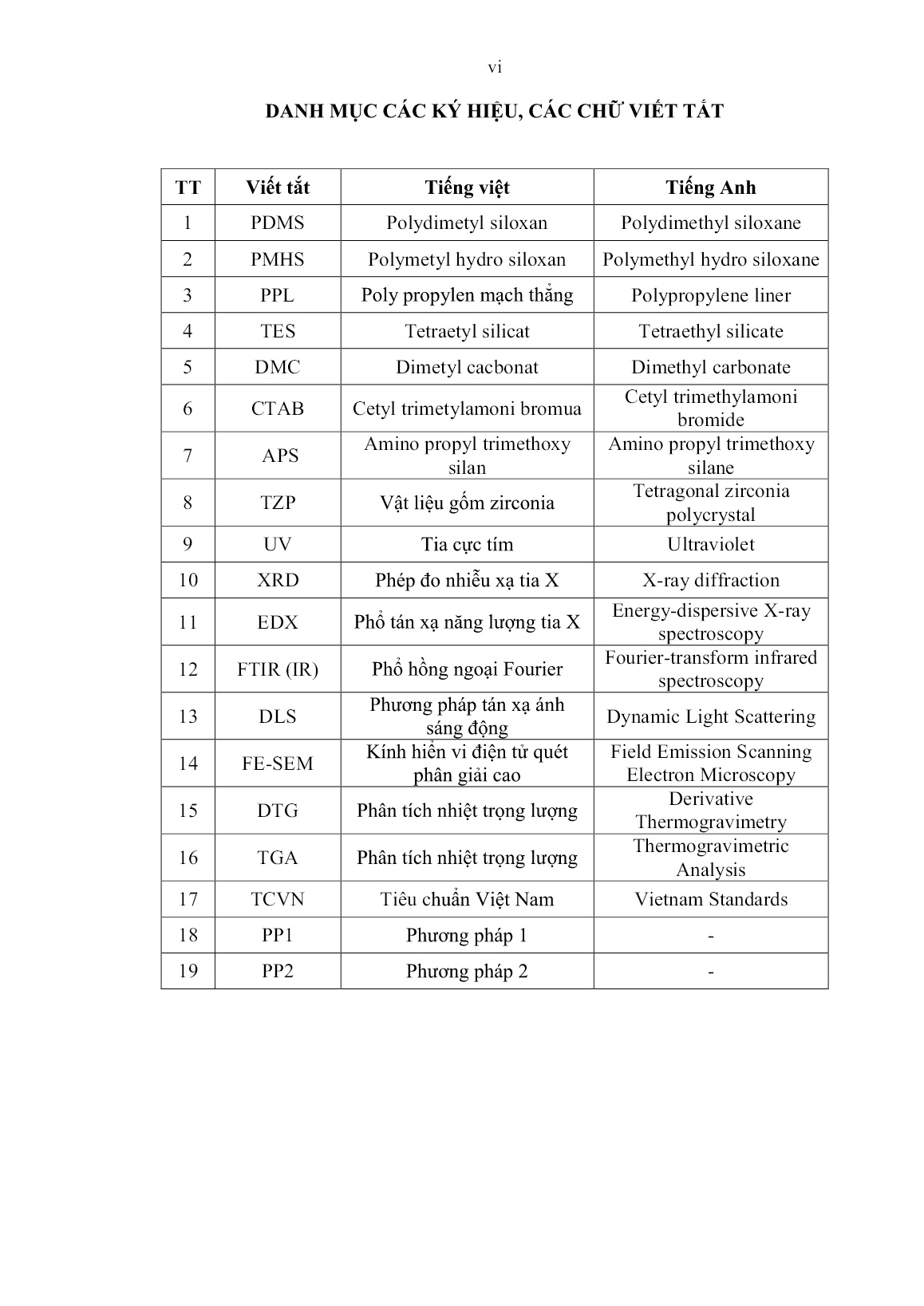
Trang 10
Tải về để xem bản đầy đủ
Bạn đang xem 10 trang mẫu của tài liệu "Luận án Nghiên cứu tổ hợp vật liệu sơn chịu nhiệt trên cơ sở nhựa silicon và định hướng sử dụng", để tải tài liệu gốc về máy hãy click vào nút Download ở trên.
Tóm tắt nội dung tài liệu: Luận án Nghiên cứu tổ hợp vật liệu sơn chịu nhiệt trên cơ sở nhựa silicon và định hướng sử dụng
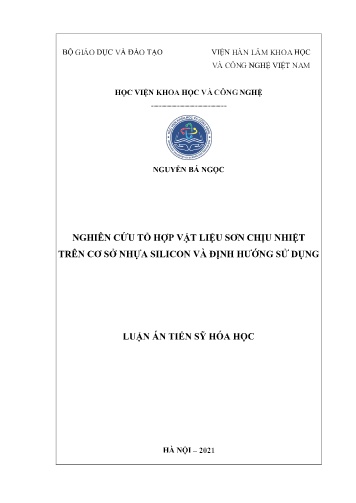
n Nghiền mịn Định lượng nguyên liệu Trộn, ngâm ủ Chất tạo màng Bột màu Phụ gia Dung môi 45 ra khỏi nhau. Độ mịn của dung dịch sơn phụ thuộc vào quá trình nghiền, nếu thời gian (hoặc số lượt) nghiền chưa đủ, các hạt bột màu, pha rắn khác vẫn bị kết tụ vào với nhau, khi đó sơn không đạt được độ mịn và màu sắc mong muốn. Nghiền mịn là công đoạn quan trọng quyết định nhiều đến chất lượng của sơn. Trong công đoạn này cần nghiên cứu lựa chọn thiết bị nghiền và chế độ nghiền phù hợp để sản phẩm sơn đạt độ mịn theo yêu cầu. Các thiết bị thông dụng là máy nghiền hạt ngọc, máy nghiền bi thùng, máy cán nhiều trục (hiện nay ít dùng) và các loại máy khác. Tùy theo yêu cầu kỹ thuật của từng loại sơn, người ta lựa chọn sử dụng máy nghiền tương ứng cho hiệu quả. Thời gian nghiền tùy chủng loại sơn và thiết bị nghiền. Sau khi nghiền đạt độ mịn, chuyển sang bể pha chỉnh. * Pha chỉnh Hỗn hợp sau khi nghiền xong, được đưa vào bể pha chỉnh khuấy đều bằng máy khuấy đĩa. Sau đó tiếp tục bổ sung chất tạo màng, dung môi, chất pha loãng (việc điều chỉnh màu sắc của sơn được thực hiện trước trong phòng thí nghiệm khi chế thử mẻ nhỏ để thiết lập được đơn pha chế) để đảm bảo chất lượng cuối cùng của màng sơn. Công đoạn này thường thực hiện với việc khuấy trộn trong 6 giờ. Điều chỉnh độ nhớt của sơn cho phù hợp theo yêu cầu kỹ thuật của sản phẩm. Sau đó lấy mẫu sơn đi kiểm tra chất lượng. * Lọc Sau khi pha chỉnh, sơn được lọc bằng lưới 100 lỗ/mm2 để loại hết các hạt thô hoặc bụi bẩn ở trong sơn, sau đó chuyển sơn sang công đoạn kiểm tra. * Kiểm tra chất lượng sản phẩm Sơn được lấy mẫu để kiểm tra các chỉ tiêu kỹ thuật của sơn theo tiêu chuẩn hay điều kiện kỹ thuật. Khi đạt, chuyển sang công đoạn đóng hộp – ghi nhãn. * Đóng hộp - ghi nhãn Đóng hộp theo tiêu chuẩn Việt Nam và theo yêu cầu của người sử dụng. Các hộp chứa phải sạch, không bụi, rỉ và phải đủ độ vững chắc để bảo đảm trong quá trình bảo quản cũng như vận chuyển. Ghi nhãn theo yêu cầu của TCVN 2090-1993 – Sơn: Phương pháp lấy mẫu, bao gói, ghi nhãn, vận chuyển và bảo quản. * Bảo quản, vận chuyển Mỗi loại sơn cần được bảo quản, vận chuyển ở điều kiện nhất định. Các yêu cầu về điều kiện bảo quản, vận chuyển cần theo tuân thủ tiêu chuẩn hay điều kiện 46 kỹ thuật cho loại sơn đó, tuân thủ TCVN 2090-1993 Sơn. Phương pháp lấy mẫu, bao gói, ghi nhãn, vận chuyển và bảo quản. Chỉ dẫn cụ thể cần được ghi trên nhãn ở thùng vận chuyển. Nhìn chung, các loại sơn cần được bảo quản trong các kho thoáng, có mái che. Nhiệt độ bảo quản phù hợp với từng loại sơn. Tuỳ loại thùng chứa sơn mà các thùng có thể xếp trên giá, xếp chồng. Kho không được chứa các axit, kiềm, các chất oxy hoá, cách xa các nguồn nhiệt. Kho phải có hệ thống phòng cháy, chữa cháy theo đúng tiêu chuẩn, có nội quy xuất, nhập, được theo dõi, bảo vệ chặt chẽ. 2.2.2. Chuẩn bị mẫu sơn Trước khi phun chuẩn bị tấm mẫu thử, mẫu sơn được khuấy trộn bằng cơ học để tránh hiện tượng lắng, cho hỗn hợp trở nên đồng nhất. Sau đó sơn được gia công để tạo mẫu (theo tiêu chuẩn TCVN 2090:2007) trên các tấm thép theo tiêu chuẩn TCVN 5670:2007. Hình 2.5. Sơ đồ quy trình công nghệ sơn phủ tấm mẫu thử nghiệm Các tấm mẫu trước khi sơn phủ được làm sạch bề mặt bằng giấy ráp và rửa lại bằng dung môi trước khi tiến hành sơn phủ. Quá trình sơn phủ có thể được tiến hành nhiều lớp để đạt được chiều dày nhất định, chiều dày mỗi lớp sơn phủ từ 25 đến 50 µm. Các lớp sơn phủ sau phải thực hiện sau khi lớp sơn phủ trước khô se bề mặt, mỗi lần sơn phủ cách nhau ít nhất không nhỏ hơn 30 phút. Sau khi sơn phủ xong, các mẫu sơn được để khô tự nhiên ở điều kiện nhiệt độ phòng trong từ 6 đến 8 giờ trước khi được đem đi sấy. Sau khi sấy, các mẫu sơn được lấy ra và để ổn định ở nhiệt độ phòng ít nhất 24 giờ trước khi tiến hành các thử nghiệm tiếp theo. 2.2.3. Phương pháp sơn phủ trong lòng vỏ động cơ CT-18 và đạn phản lực Phương pháp sơn phủ trong lòng vỏ động cơ CT-18 và đạn phản lực, được 47 tiến hành qua các bước sau: 2.2.3.1. Phương pháp xử lý bề mặt * Phương pháp tẩy sạch bề mặt Công đoạn làm sạch bề mặt rất cần thiết trong công nghệ xử lý bề mặt đối với các chi tiết vỏ động cơ CT-18 và đạn phản lực, phương pháp làm sạch bằng hóa học là phù hợp. Các chi tiết được đưa vào bể tẩy dầu mỡ, dung dịch tẩy dầu mỡ là dung dịch kiềm nóng sau đó đưa sang tẩy bằng axit và được rửa sạch bằng nước thường. * Phương pháp phốt phát hóa bề mặt - Đối với các chi tiết bằng thép trước khi sơn phải đưa qua công đoạn này. Công nghệ phốt phát hóa ở nhiệt độ thường là phù hợp với công nghệ sơn phủ. Chế độ phốt phát hóa ở nhiệt độ thường như sau: + Dung dịch làm việc ở nhiệt độ phòng; + Thời gian phốt phát hoá từ 15 - 25 phút. Các chi tiết phốt phát hóa qua các bước sau: + Làm sạch bề mặt chi tiết; + Phốt phát hóa bề mặt chi tiết; + Rửa bằng nước nóng; + Sấy khô ở nhiệt độ 180oC; + Để nguội tự nhiên; + Các chi tiết sau khi phốt phát hóa xong phải được phun sơn sau thời gian không quá 13 giờ; - Đối với các chi tiết bằng nhôm trước khi sơn cần anốt hóa qua các bước sau: + Làm sạch bề mặt chi tiết bằng dung dịch tẩy dầu mỡ; + Rửa bằng nước nóng; + Anốt hóa chi tiết trong dung dịch axit sunfuric ở nhiệt độ 15 - 25oC, thời gian 30 - 40 phút; + Rửa bằng nước nóng; + Nhuộm mầu trong dung dịch bicrômat kali ở nhiệt độ 80 - 90oC, thời gian 5 - 10 phút; + Rửa bằng nước nóng, thời gian 3 - 5 phút; 48 + Sấy khô ở nhiệt độ 100oC; + Để nguội tự nhiên. 2.2.3.2. Phương pháp sơn phủ Qua thực tế quá trình phun phủ động cơ, nhận thấy công nghệ phun phủ là phù hợp để sơn phủ lòng vỏ động cơ CT-18 và vỏ đạn phản lực. Công nghệ này có tính năng ưu việt sau: - Bề mặt màng sơn đều, bóng đẹp; - Chiều dày màng sơn có thể điều chỉnh theo mong muốn. Công nghệ sơn phun phụ thuộc vào các yếu tố độ nhớt của sơn, áp lực phun, kích thước vòi phun và điều kiện trong quá trình thi công lớp sơn phủ. 2.2.4. Các phương pháp xác định tính chất của màng sơn 2.2.4.1. Phương pháp xác định độ cứng của màng sơn Độ cứng màng sơn được xác định theo tiêu chuẩn Việt Nam TCVN 2098:2007: Sơn: Phương pháp xác định độ cứng của màng. 2.2.4.2. Phương pháp xác định chiều dày màng sơn Độ dày của màng sơn được xác định theo tiêu chuẩn TCVN 9760:2013 (ISO 2808:2007) về Sơn và vecni – Xác định độ dày màng. Hình 2.6. Thiết bị SE 1000FN hãng Sheen (Anh) 2.2.4.3. Xác định độ bền uốn màng sơn Độ bền uốn màng sơn được xác định theo tiêu chuẩn Việt Nam TCVN 2099- 2013: Sơn và vecni: Phép thử uốn (trục hình trụ). 49 Hình 2.7. Thiết bị đo độ bền uốn màng sơn Ref. 801 hãng Sheen 2.2.4.4. Xác định độ bền va đập của màng sơn Độ bền va đập của màng sơn được xác định theo tiêu chuẩn Việt Nam TCVN 2100-2 : 2013: Sơn và vecni - Phép thử biến dạng nhanh (độ bền va đập). Hình 2.8. Thiết bị đo độ bền va đập màng sơn 2.2.4.5. Xác định độ bám dính của màng sơn Hình 2.9. Thiết bị đo độ bám dính kẻ ô màng sơn Độ bám dính của màng sơn được xác định theo tiêu chuẩn Việt Nam TCVN 50 2097:2015: Sơn và vecni – Phép thử cắt ô. 2.2.4.6. Xác định độ nhớt của màng sơn Độ nhớt của màng sơn được xác định theo tiêu chuẩn Việt Nam TCVN 2092:2013: Sơn và vecni – Xác định thời gian chảy bằng phễu chảy. 2.2.4.7. Xác định thời gian khô của màng sơn Thời gian khô của màng sơn được xác định theo tiêu chuẩn Việt Nam TCVN 2096:2015: Sơn và vecni – Phương pháp xác định độ khô và thời gian khô. 2.2.4.8. Xác định hàm lượng chất không bay hơi trong sơn Hàm lượng chất không bay hơi trong sơn được xác định theo tiêu chuẩn Việt Nam TCVN 10519:2019: Sơn, vecni và chất dẻo – Xác định hàm lượng chất không bay hơi. 2.2.4.9. Xác định độ mịn của màng sơn Độ mịn của màng sơn được xác định theo tiêu chuẩn Việt Nam TCVN 2091:2015: Sơn và vecni – Xác định độ nghiền mịn. 2.2.5. Các phương pháp kiểm tra khả năng chịu tác động môi trường của các mẫu sơn chịu nhiệt Khả năng chịu môi trường hóa chất được thử nghiệm tại Trung tâm Đo lường/ Viện Công nghệ/ Tổng cục Công nghiệp quốc phòng. Các mẫu sơn sau khi được thử nghiệm khả năng chịu sốc nhiệt, tiếp tục được thử nghiệm khả năng chịu môi trường hóa chất như mù muối, UV, dầu nhờn (castrol Activ), môi trường axit và môi trường kiềm. Sau thời gian thử nghiệm, các mẫu được kiểm tra đánh giá lại bề mặt. Mẫu thử nghiệm đạt yêu cầu về khả năng chịu tác động của môi trường khi bề mặt mẫu trước và sau khi thử nghiệm không có sự thay đổi. 2.2.5.1. Khả năng chịu môi trường mù muối Khả năng chịu mù muối của mẫu sơn chịu nhiệt được kiểm tra theo TCVN 7699 – 2 - 52 : 2007: sơn và lớp phủ bảo vệ kim loại – Phương pháp thử mù muối. Thử nghiệm được tiến hành trong tủ khí hậu ATLAS UV/CON Model UC- 327-2. 51 Hình 2.10. Tủ khí hậu ATLAS UV/CON Model UC-327-2 2.2.5.2. Khả năng chịu môi trường UV Khả năng chịu UV của mẫu sơn chịu nhiệt được kiểm tra theo TCVN 9277 : 2012: Sơn và vecni – Phương pháp thử thời tiết nhân tạo – Thử nghiệm dưới đèn huỳnh quang tử ngoại và nước. 2.2.5.3. Khả năng chịu môi trường dầu nhờn Khả năng chịu môi trường dầu nhờn của mẫu sơn chịu nhiệt được kiểm tra theo TCVN 10517-3:2014: Sơn và vecni – Xác định độ bền với chất lỏng – Phần 3: Phương pháp sử dụng môi trường hấp phụ. 2.2.5.4. Khả năng chịu môi trường axit Khả năng chịu môi trường axit của mẫu sơn chịu nhiệt được kiểm tra theo TCVN 10517-3:2014: Sơn và vecni – Xác định độ bền với chất lỏng – Phần 3: Phương pháp sử dụng môi trường hấp phụ. 2.2.5.5. Khả năng chịu môi trường kiềm Khả năng chịu môi trường kiềm của mẫu sơn chịu nhiệt được kiểm tra theo TCVN 10517-3:2014: Sơn và vecni – Xác định độ bền với chất lỏng – Phần 3: Phương pháp sử dụng môi trường hấp phụ. 2.2.6. Các phương pháp khảo sát tính chất của vật liệu 2.2.6.1. Phương pháp tán xạ ánh sáng động (DLS) Phương pháp tán xạ ánh sáng động là phương pháp phân tích chỉ ra sự phân bố đường kính hạt của mẫu đo và phân bố kích thước cỡ hạt của mẫu. Đây là phương pháp phân tích hiện đại, đáng tin cậy trong quá trình nghiên cứu kích thước 52 của các vật liệu. Các nghiên cứu trong luận án được khảo sát trên trên máy HORIBA Laser Scattering Particle Size Distribution Analyzer LA-950 tại phòng thí nghiệm Viện Hóa học - Vật liệu/ Viện Khoa học và Công nghệ quân sự. 2.2.6.2. Kính hiển vi điện tử quét FE-SEM Kính hiển vi điện tử quét FE-SEM có thể tạo ra ảnh với độ phân giải cao của bề mặt mẫu vật bằng cách sử dụng một chùm điện tử (chùm các electron) hẹp quét trên bề mặt mẫu. Việc tạo ảnh của mẫu vật được thực hiện thông qua việc ghi nhận và phân tích các bức xạ phát ra từ tương tác của chùm điện tử với bề mặt mẫu vật. Phương pháp này cho thông tin về hình thái học của vật chất. Các mẫu được chụp ảnh trên máy Field Emission Scaning Electron Microscope S – 4800 tại Viện Khoa học – Vật liệu/ Viện Hàn lâm Khoa học và Công nghệ Việt Nam. 2.2.6.3. Phép đo nhiễu xạ tia X (XRD) Phép đo nhiễu xạ tia X (XRD) là phương pháp được sử dụng rộng rãi nhất để xác định cấu trúc tinh thể, bằng cách sử dụng một chùm tia X song song hẹp, đơn sắc, chiếu vào mẫu. Phương pháp nhiễu xạ bột rất dễ thực hiện và cho phép xác định thành phần pha, tỷ phần pha, cấu trúc tinh thể (các tham số mạng tinh thể),... Các mẫu được đo XRD dưới dạng bột. Giản đồ XRD của các mẫu nghiên cứu được ghi trên máy D8 Advance - Bruker của Đức tại Viện Hóa học – Vật liệu/ Viện Khoa học và Công nghệ Quân sự. 2.2.6.4. Phổ tán sắc năng lượng tia X (EDX) Phổ tán sắc năng lượng tia X, hay phổ tán sắc năng lượng là kỹ thuật phân tích thành phần hóa học của vật rắn dựa vào việc ghi lại phổ tia X phát ra từ vật rắn, do tương tác với các bức xạ (mà chủ yếu là chùm điện tử có năng lượng cao trong các kính hiển vi điện tử). Phương pháp này thường được gọi là EDX. Kỹ thuật EDX chủ yếu được thực hiện trong các kính hiển vi điện tử, ở đó ảnh vi cấu trúc vật rắn được ghi lại thông qua việc sử dụng chùm điện tử có năng lượng cao tương tác với vật rắn. Sử dụng phương pháp này để xác định thành phần nguyên tố có trong mẫu. Phổ EDX được đo trên máy Oxford Instruments (Anh) tại Viện Kỹ thuật Nhiệt đới/ Viện Hàn lâm Khoa học và Công nghệ Việt Nam. 53 2.2.6.5. Phương pháp phân tích nhiệt trọng lượng TGA Phân tích nhiệt trọng lượng TGA là phương pháp dựa trên cơ sở xác định khối lượng của mẫu vật liệu bị mất đi hoặc tăng lên trong quá trình chuyển pha như một hàm của nhiệt độ. Phép đo phân tích nhiệt trọng lượng TGA nhằm xác định khối lượng bị mất đi trong quá trình chuyển pha, khối lượng bị mất theo thời gian và theo nhiệt độ do quá trình khử nước hoặc phân hủy. Các phép đo phân tích nhiệt được thực hiện trên máy phân tích DTG-60H – SHIMADZU tại phòng thí nghiệm của Khoa Hóa lý – Đại học Sư phạm Hà Nội và thiết bị TGA - TG209F1, xuất xứ NETZSCH - Đức tại Viện Kỹ thuật Nhiệt đới/ Viện Hàn lâm Khoa học và Công nghệ Việt Nam. 2.2.6.6. Phương pháp phổ hồng ngoại biến đổi Fourier (FTIR) Phổ hồng ngoại sử dụng trong luận án để xác định thông tin về nhóm chức, liên kết trong phân tử dựa vào sự dao động của các liên kết khi chiếu một chùm ánh sáng đơn sắc có bước sóng nằm trong vùng hồng ngoại qua mẫu phân tích. Phổ IR của các mẫu nghiên cứu được ghi trên máy chụp phổ hồng ngoại Nicolet 6700 FT-IR tại phòng thí nghiệm Viện kỹ thuật nhiệt đới/ Viện Hàn lâm Khoa học và Công nghệ Việt Nam. Phổ được ghi trong vùng bước sóng từ 400- 4000 cm-1. 2.2.7. Biến tính bề mặt nanosilica và nano zirconi oxit bằng polydimetyl siloxan (PDMS) Quá trình biến tính bề mặt các hạt nano (nanosilica hoặc nano zirconi oxit) được tiến hành trong thiết bị phản ứng thủy nhiệt autoclave có lõi PPL thể tích lõi 100ml. Đầu tiên cân chính xác một lượng bột nano oxit (nanosilica hoặc nano zirconi oxit) vào bình cầu thủy tinh, sau đó bổ sung thêm 5 gam polydimetyl siloxan (PDMS) và 15 gam methanol (MeOH) sao cho tỉ lệ khối lượng giữa bột nano/PDMS là 1:0,25; 1:0,5; 1:0,75 và 1:1. Hỗn hợp sau được khuấy trộn bằng máy khuấy đũa Eurostar 20 cánh khuấy teflon với tốc độ 4000 vòng/phút trong 30 phút để hỗn hợp được đồng nhất. Sau đó, hỗn hợp được bổ sung thêm 7,5 g dimetyl cacbonat (DMC) và 0,05g KOH và được khuấy ở tốc độ 4000 vòng/phút trong 30 phút. Tiếp theo, hỗn hợp trong bình cầu thủy tinh được rung siêu âm bằng thiết bị Skymen JP-040 ở tần số 40 kHz ở trong 30 phút (tiến hành rung siêu âm 10 phút 54 sau đó nghỉ 10 phút). Hỗn hợp sau đó được chuyển sang lõi phản ứng PPL của thiết bị phản ứng thủy nhiệt autoclave. Toàn bộ thiết bị phản ứng được đặt trong tủ sấy và được gia nhiệt đến nhiệt độ phản ứng 150oC, 200oC và 250oC. Tốc độ gia nhiệt của tủ sấy 2-3oC/phút. Thời gian phản ứng được thực hiện trong 02 giờ tính từ lúc tủ sấy đạt nhiệt độ phản ứng. Kết thúc quá trình phản ứng tắt tủ sấy và làm nguội bình phản ứng tự nhiên trong tủ sấy. Sản phẩm sau khi được lấy ra khỏi thiết bị phản ứng được rửa (sau đó ly tâm, lọc) bằng n-hexan 3 lần để loại bỏ hoàn toàn thành phần dư. Hỗn hợp sau đó được sấy ở nhiệt độ 80oC trong 12 giờ để loại bỏ hết thành phần dung môi và thu được bột nano đã biến tính bề mặt. Tiếp đó bột nano oxit đã biến tính bề mặt được bảo quản trong túi PE bịt kín. Cơ chế phản ứng của quá trình biến tính bề mặt. Bước 1. Phản ứng depolyme của PDMS dưới tác dụng của DMC và xúc tác KOH tạo thành các oligome của PDMS với các nhóm methoxy ở đầu mạch. H3C Si CH3 O CH3 Si CH3 CH3 O Si CH3 CH3 O Si CH3 CH3 CH3 x y + H3C Si CH3 O CH3 Si CH3 CH3 O CH3 x H3C O Si CH3 CH3 O Si CH3 CH3 CH3 y KOH - CO2 C O O O CH3 CH3 Bước 2. Sự hấp phụ hóa học của oligome PDMS có các nhóm methoxy đầu mạch lên bề mặt oxit kim loại. Oxit kim loai OH H3C O Si CH3 CH3 O Si CH3 CH3 CH3 y + Oxit kim loai O Si CH3 CH3 O Si CH3 CH3 CH3 y + H3C OH Oxit kim loai Quá trình biến tính bề mặt các hạt nano bằng PDMS được trình bày ở hình 2.11. 55 Hình 2.11. Sơ đồ quá trình biến tính bề mặt nanosilica hoặc nano zirconi oxit bằng PDMS 2.2.8. Các phương pháp thử nghiệm khả năng chịu nhiệt của màng sơn silicon 2.2.8.1. Phương pháp thử nghiệm khả năng chịu nhiệt của màng sơn * Thử nghiệm khả năng chịu nhiệt của màng sơn bằng lò nung Căn cứ vào các điều kiện thực tế trong quá trình hoạt động của động cơ CT- 18 là 20-25 giây, tiến hành đánh giá khả năng chịu nhiệt của màng sơn bằng thử nghiệm trong điều kiện như sau: Các thử nghiệm khả năng chịu sốc nhiệt được tiến hành trong lò nung nhiệt độ cao, Nabertherm tại Viện Công nghệ/ Tổng cục Công nghiệp Quốc phòng. Khi nhiệt độ lò nung đạt được nhiệt độ thử nghiệm 600oC, 700oC, 800oC, 900oC, 1.000oC, 1.050oC và 1.100oC, tiến hành đưa các mẫu thử vào DMC MeOH Bột nano oxit PDMS KOH Khuấy trộn sơ bộ Thiết bị phản ứng Autoclave Tủ sấy Làm nguội Rửa, ly tâm, lọc Sấy, bảo quản 56 lò nung trong thời gian 25 giây để tiến hành thử nghiệm đánh giá. Thời gian thử nghiệm được tính từ lúc bắt đầu đưa mẫu thử vào trong lò đến khi lấy mẫu thử ra khỏi lò. Sau thời gian thử nghiệm 25 giây, tiến hành lấy mẫu thử ra khỏi lò nung, để nguội tự nhiên và tiến hành đánh giá sự thay đổi bề mặt (sự bong tróc, phồng rộp, nứt vỡ) của các lớp màng sơn trên các tấm mẫu thử. Đánh giá bề mặt của mẫu thử bằng mắt thường, mẫu thử được đánh giá là đạt yêu cầu khi bề mặt mẫu không bị nứt, phồng rộp, không bị phá hủy và không xuất hiện bột, phấn trên bề mặt mẫu. Hình 2.12. Lò nung Nabertherm 1300oC * Thử nghiệm khả năng chịu nhiệt của màng sơn bằng đèn khò axetylen Khả năng chịu nhiệt của tấm mẫu đã sơn phủ được thử nghiệm theo tiêu chuẩn ASTM-E285-08, sử dụng đèn khò ôxi - axetylen cố định phụt trực tiếp vào bề mặt trước hoặc sau của tấm mẫu đã sơn phủ. Nhiệt độ tối đa của ngọn lửa đèn khò ôxi - axetylen có thể đạt đến trên 3000ºC khi tỷ lệ O2/C2H2 là 1/1,2; tốc độ dòng phụt rất lớn, hoàn toàn thích hợp dùng để thử nghiệm khả năng bảo vệ nhiệt, chịu nhiệt của tấm mẫu đã sơn phủ. Tiến hành thử nghiệm thực tế khả năng chịu nhiệt của tấm mẫu đã sơn phủ sử dụng đèn khò ôxi - axetylen. Khả năng cách nhiệt của tấm mẫu đã sơn phủ được xác định dựa trên giản đồ hiển thị nhiệt độ mặt sau của mẫu thử theo thời gian tính từ thời điểm ngọn lửa của đèn khò ôxi - axetylen tác động vào mặt trước của mẫu thử. Các thông số trong quá trình thử nghiệm cần xác định như: - Tỷ lệ O2/C2H2 ; 57 - Nhiệt độ ngọn lửa đo bằng thiết bị đo nhiệt độ từ xa hồng ngoại OS524E- SC; - Tốc độ dòng khí cháy khi chưa xảy ra quá trình cháy. Các tấm mẫu đã sơn phủ được gá lắp trên giá thử nghiệm đo nhiệt độ. Sử dụng đèn khò ôxi - axetylen cố định, phụt trực tiếp vào bề mặt trước của tấm mẫu đã sơn phủ, khoảng cách từ đầu đèn khò đến tấm mẫu 10-20 cm. Tiến hành đo nhiệt độ ngọn lửa đèn khò bằng thiết bị đo nhiệt độ hồng ngoại cầm tay OS524E-SC (hình 2.13) đồng thời đo nhiệt độ trực tiếp tại vị trí ngọn lửa sau mẫu thử. Xác định sự thay đổi nhiệt độ tại vị trí sau vị trí tiếp xúc trực tiếp với ngọn lửa theo thời gian thử nghiệm 20-25 giây. Hình 2.13. Nhiệt kế hồng ngoại cầm tay nhiệt độ cao OS524E-SC Sơ đồ phương pháp thử nghiệm được trình bày trên hình 2.14. Hình 2.14. Sơ đồ thử nghiệm khả năng chịu nhiệt của tấm mẫu đã sơn phủ sử dụng đèn khò ôxi - axetylen theo tiêu chuẩn ASTM-E285-08 58 2.2.8.2. Thử nghiệm trên vỏ động cơ CT-18 Sau khi đã tiến hành các thử nghiệm ở quy mô phòng thí nghiệm và mô phỏng điều kiện thực tế, lớp sơn phủ chịu nhiệt được áp dụng trong động cơ CT-18 và thử nghiệm thực tế. Hình 2.15. Lớp sơn phủ trong lòng vỏ động cơ CT-18 Mẫu sơn phủ được sơn vào vỏ động cơ CT-18 cả bên trong và bên ngoài lớp vỏ. Đặc biệt là phần động cơ hành trình, lớp sơn phủ được phun với chiều dày từ 200 đến 400 µm ở bên trong lòng động cơ và từ 50 đến 100 µm ở bên ngoài vỏ động cơ. Lớp sơn sau khi được sơn p
File đính kèm:
luan_an_nghien_cuu_to_hop_vat_lieu_son_chiu_nhiet_tren_co_so.pdf
Đóng góp mới của luận án.doc
NEW CONTRIBUTION - Ngọc.doc
Tóm tắt luận án tiếng anh.pdf
Tom tat luận án.pdf
Trang thông tin đóng góp mới.pdf
Trích yếu luận án.pdf