Luận án Nghiên cứu ứng dụng sơn phủ bảo vệ chống ăn mòn cho cốt thép trong bê tông vùng biển Việt Nam
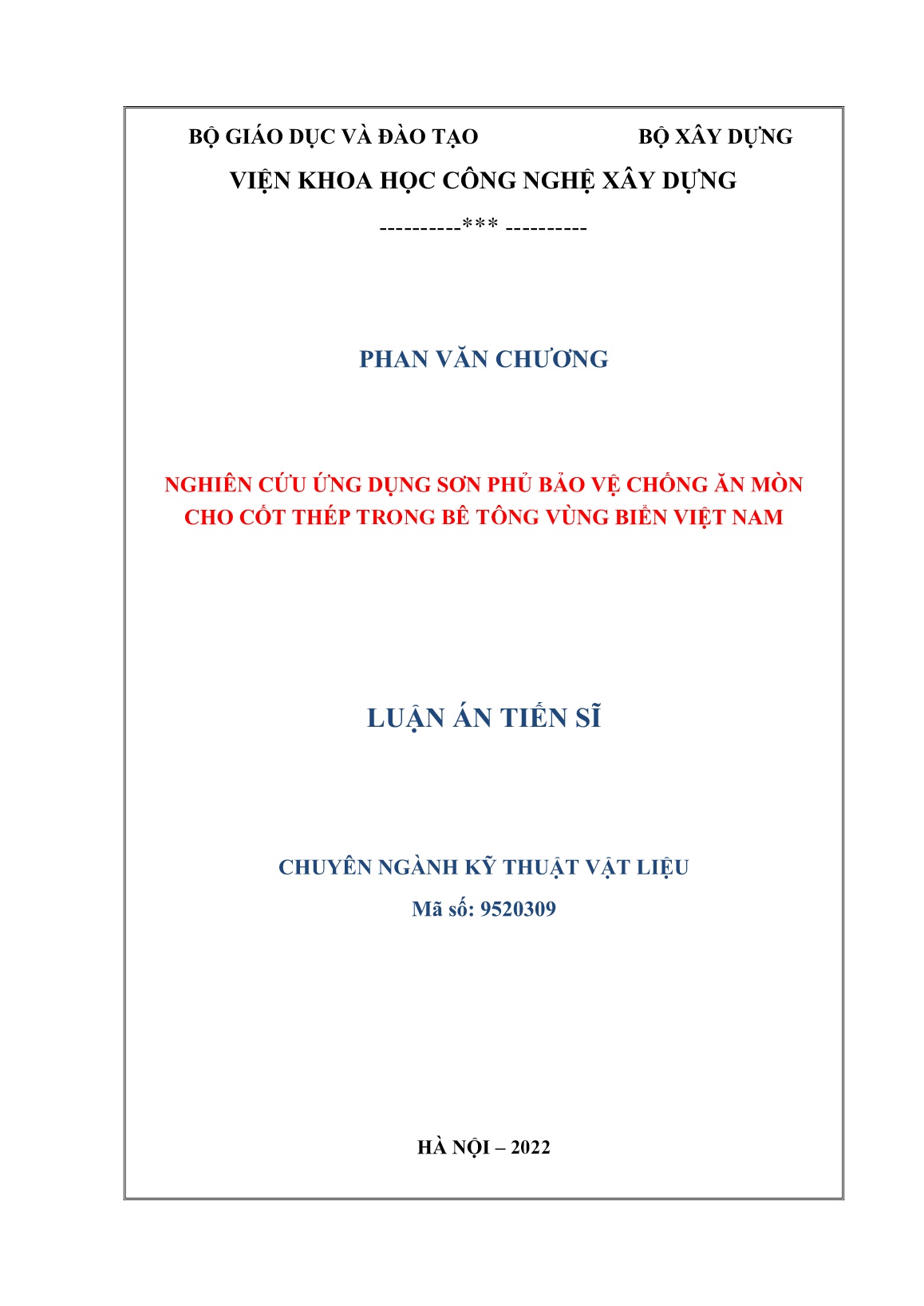
Trang 1
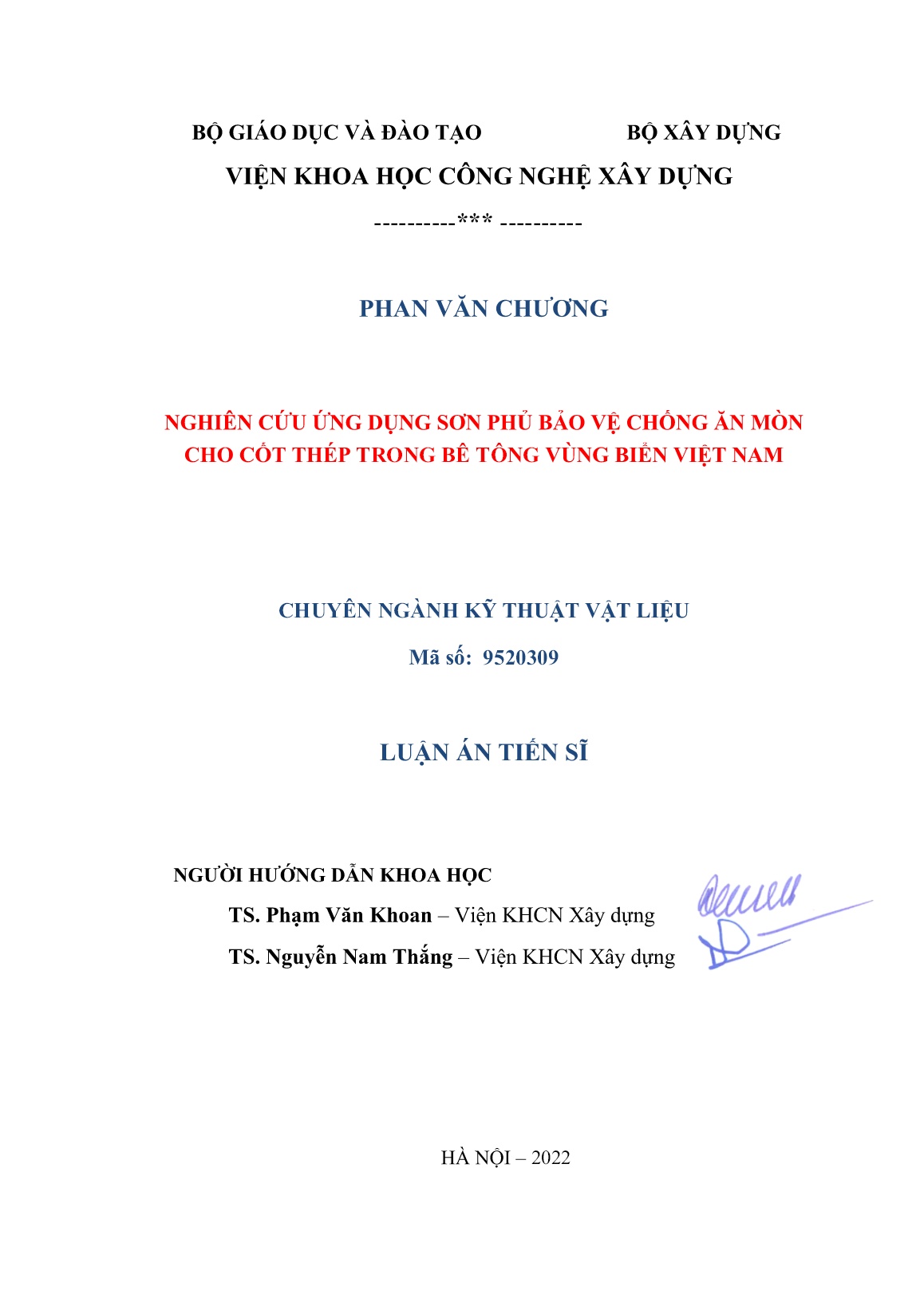
Trang 2
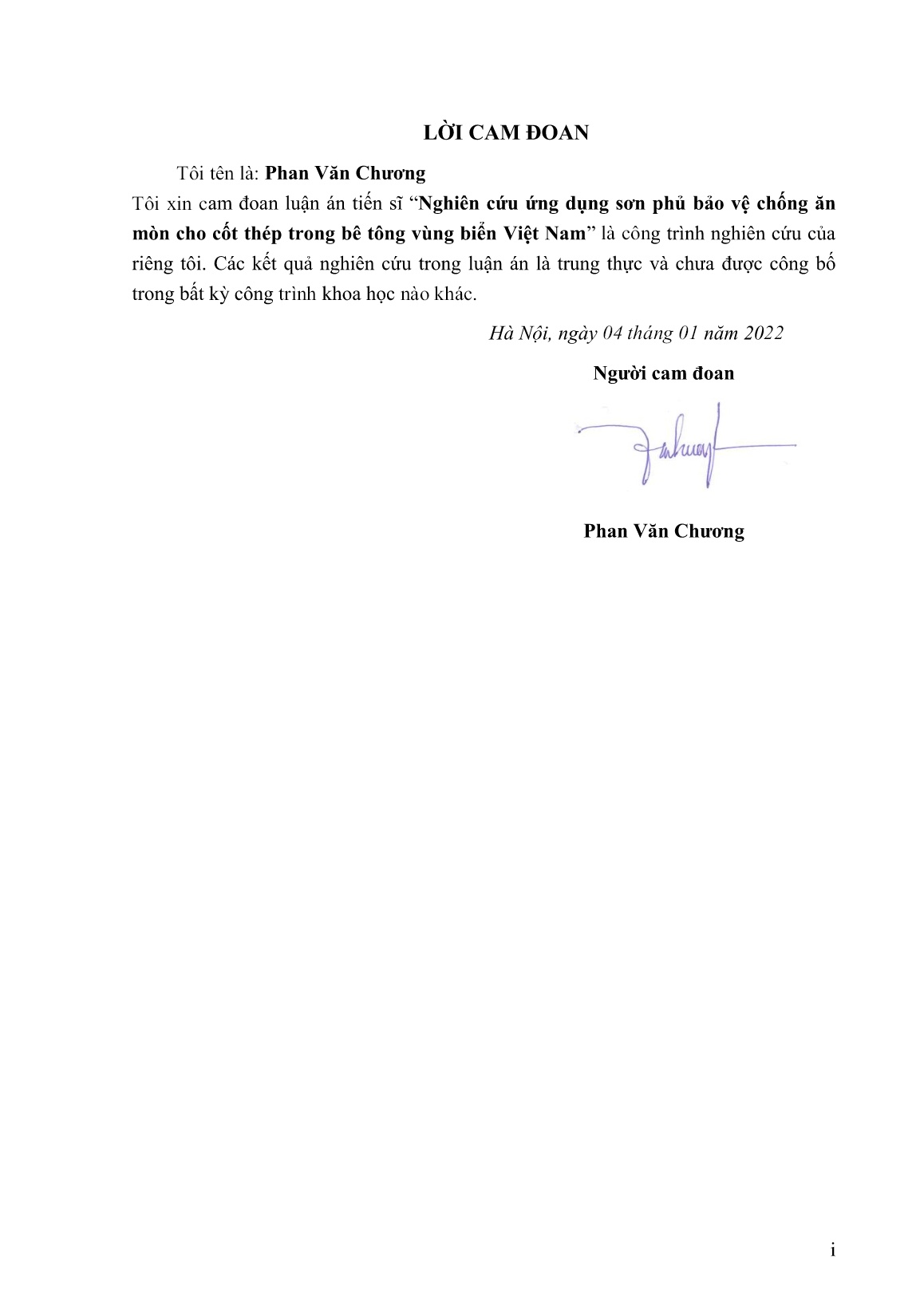
Trang 3
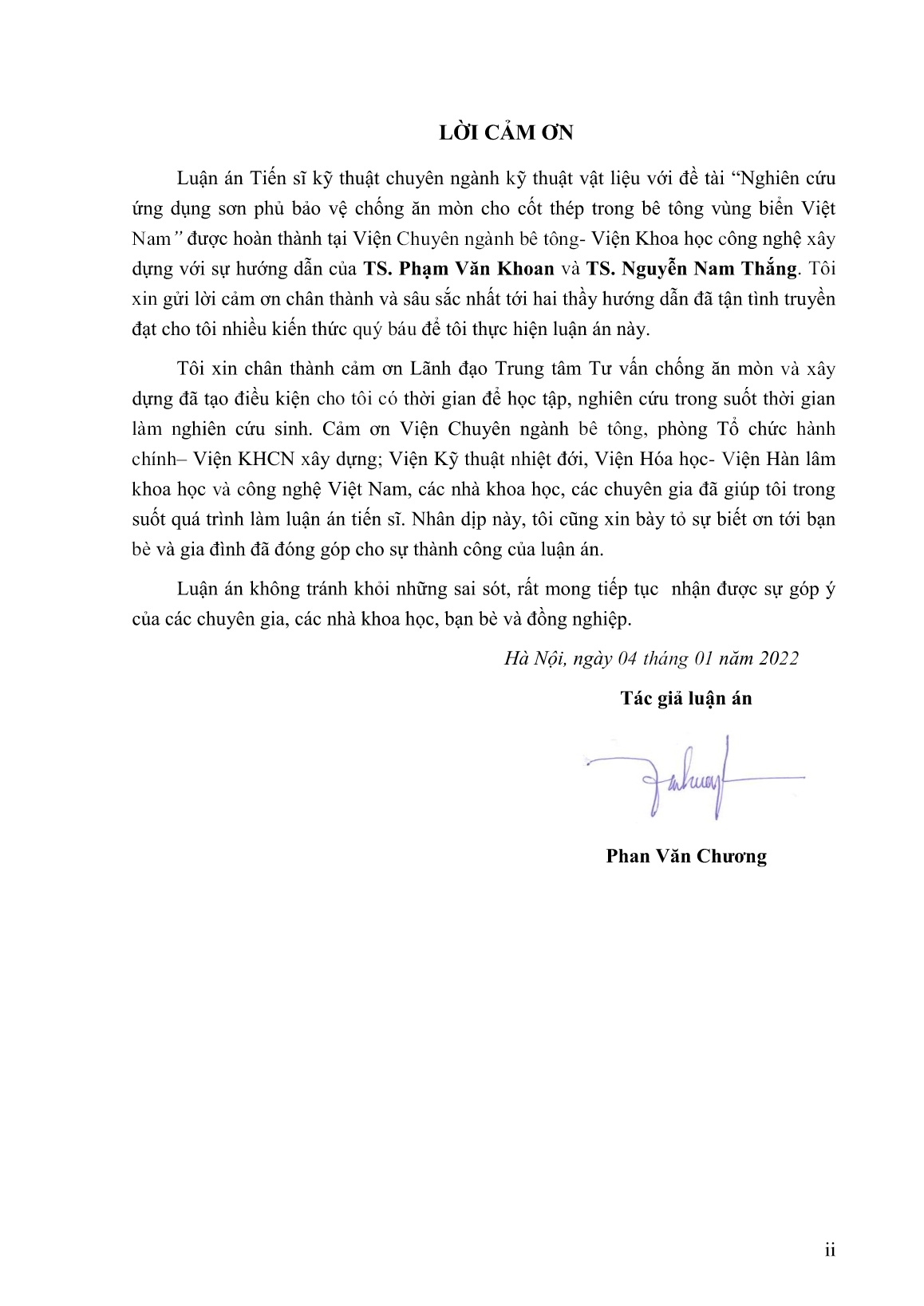
Trang 4

Trang 5
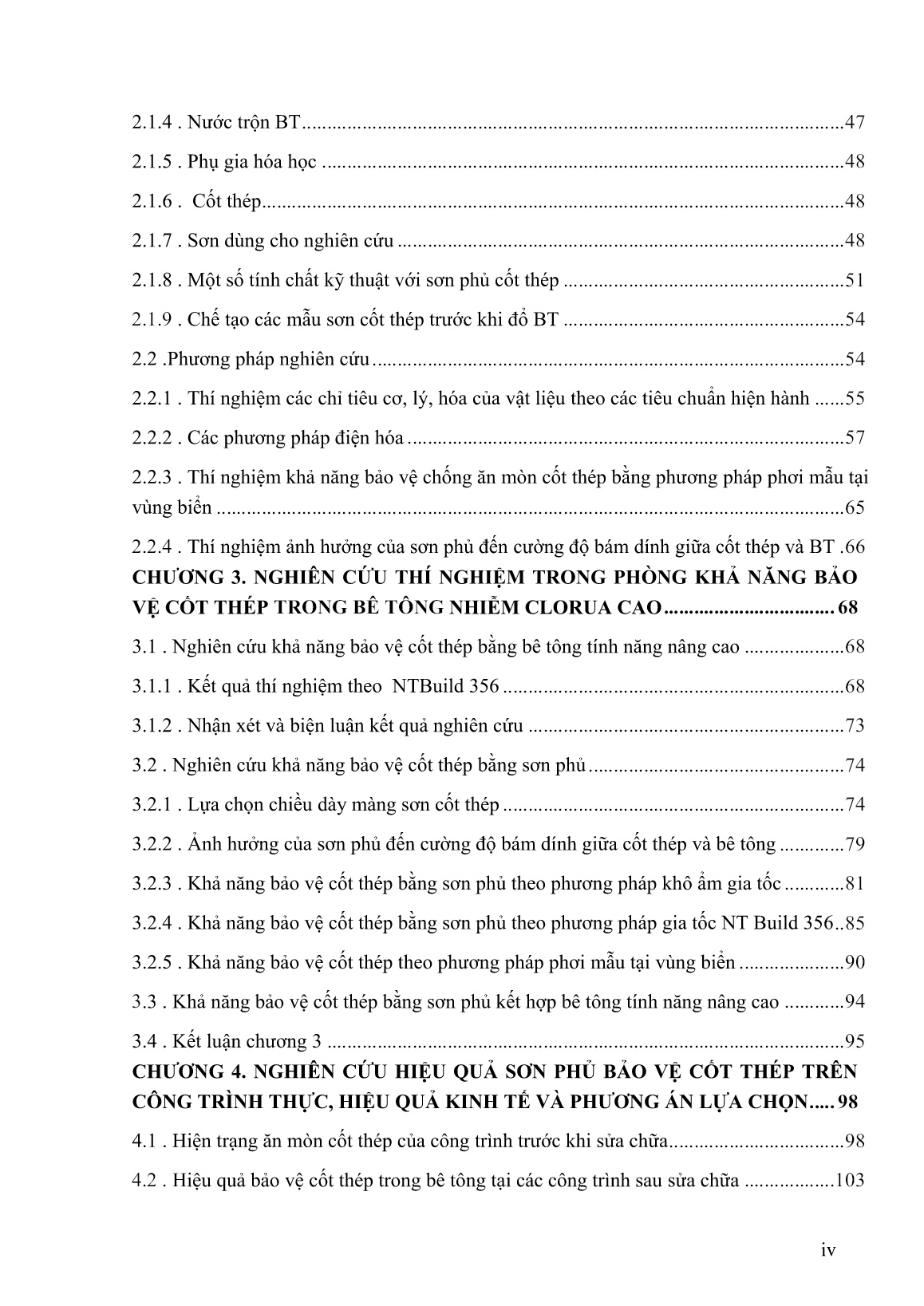
Trang 6
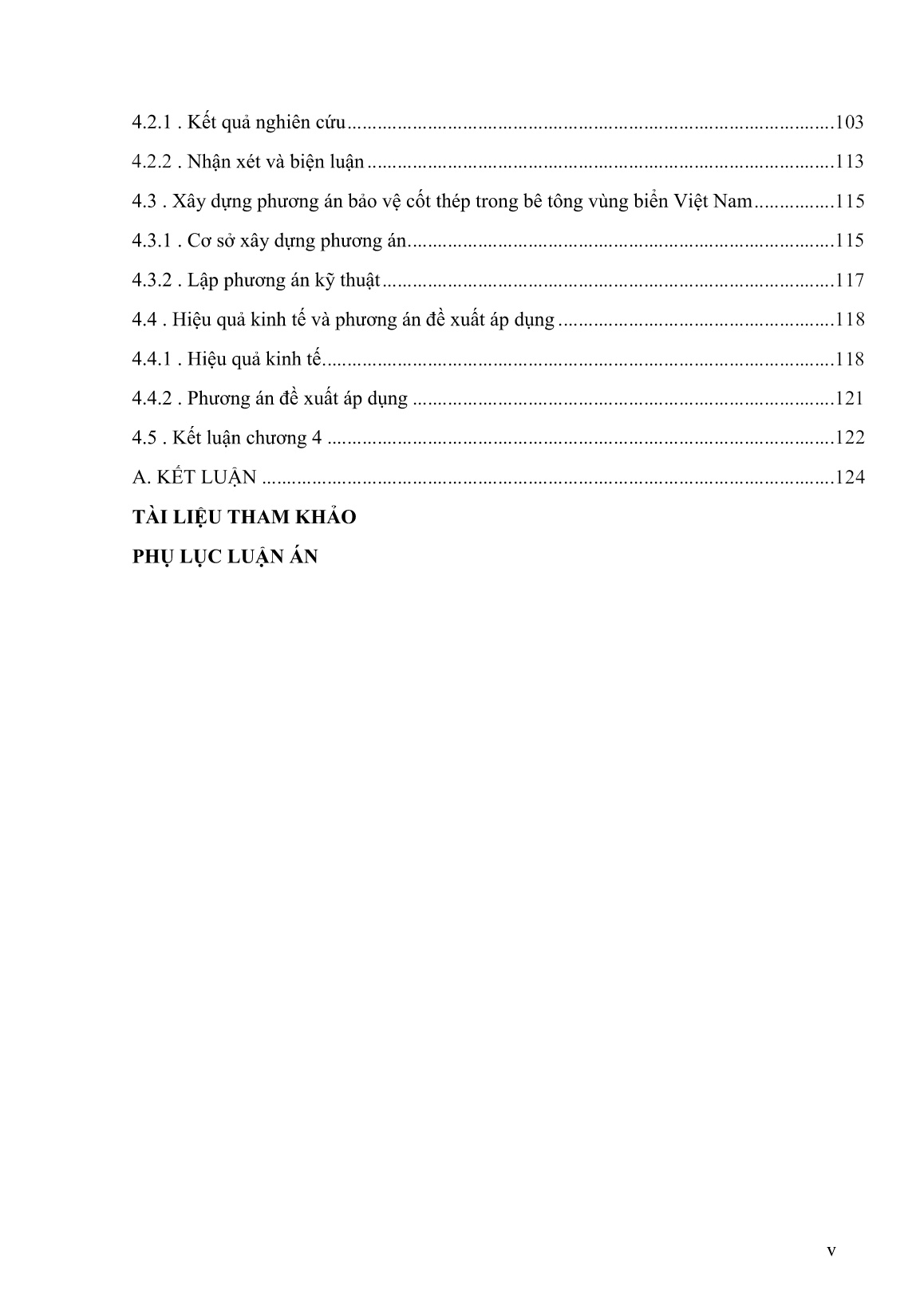
Trang 7
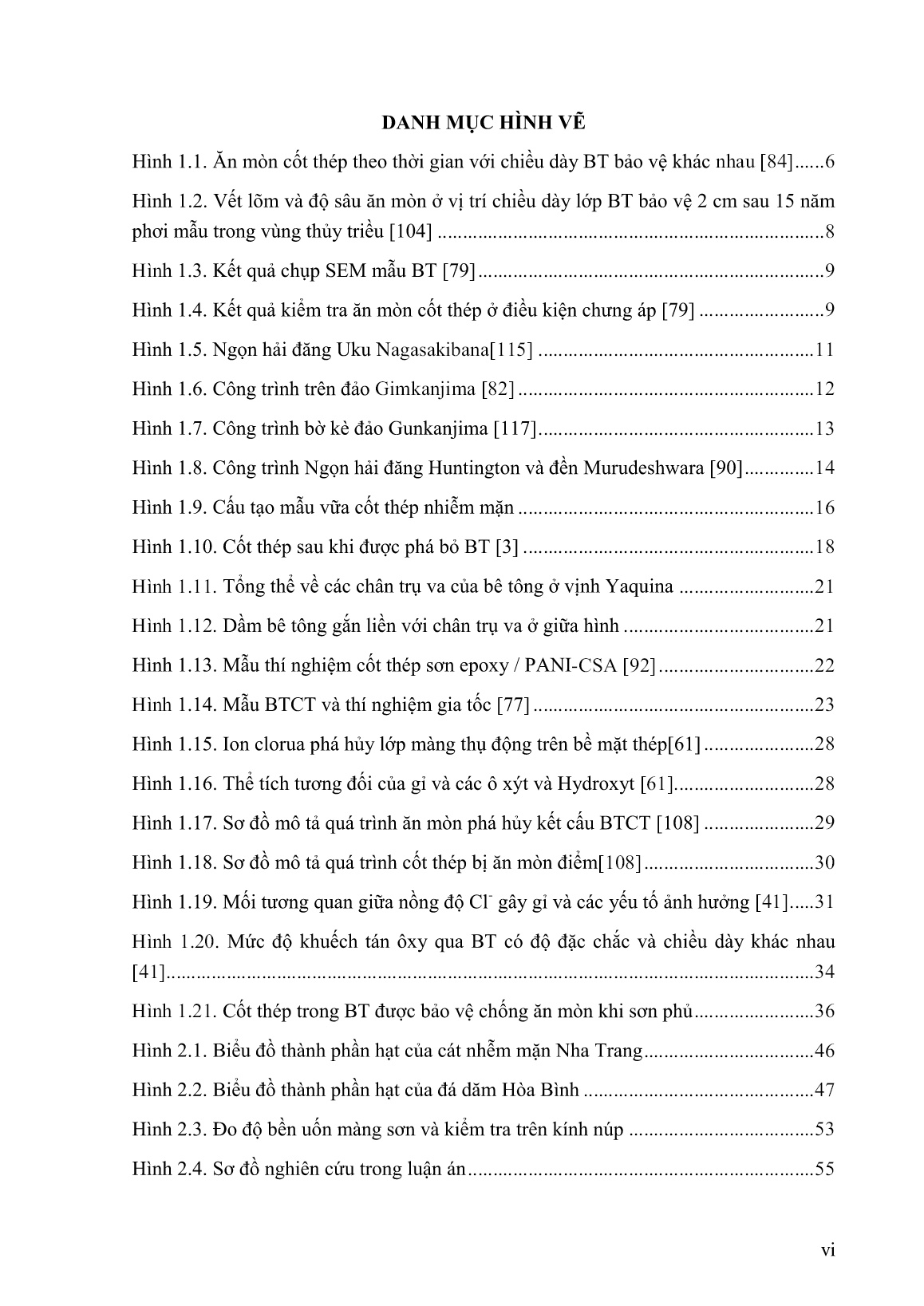
Trang 8
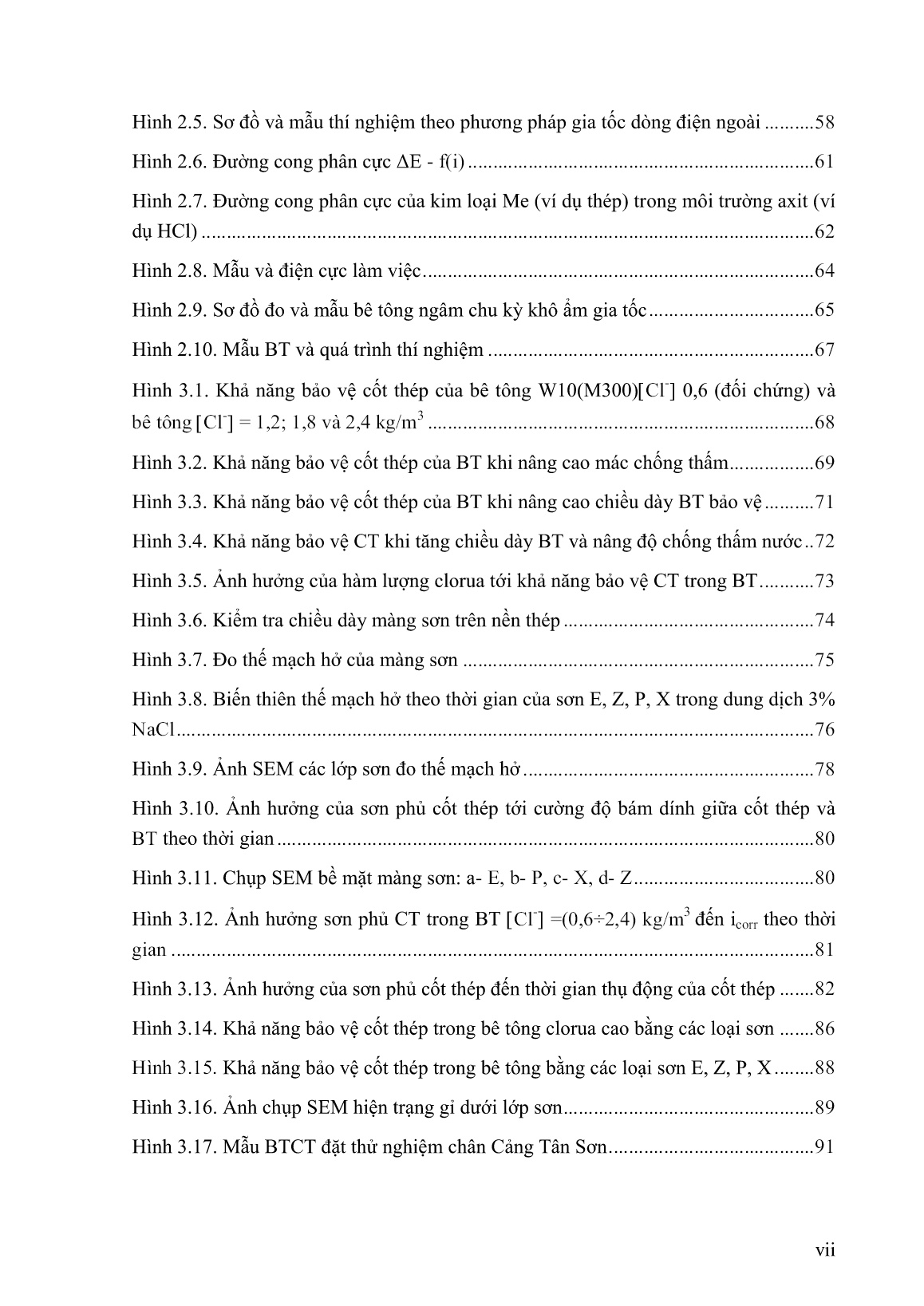
Trang 9
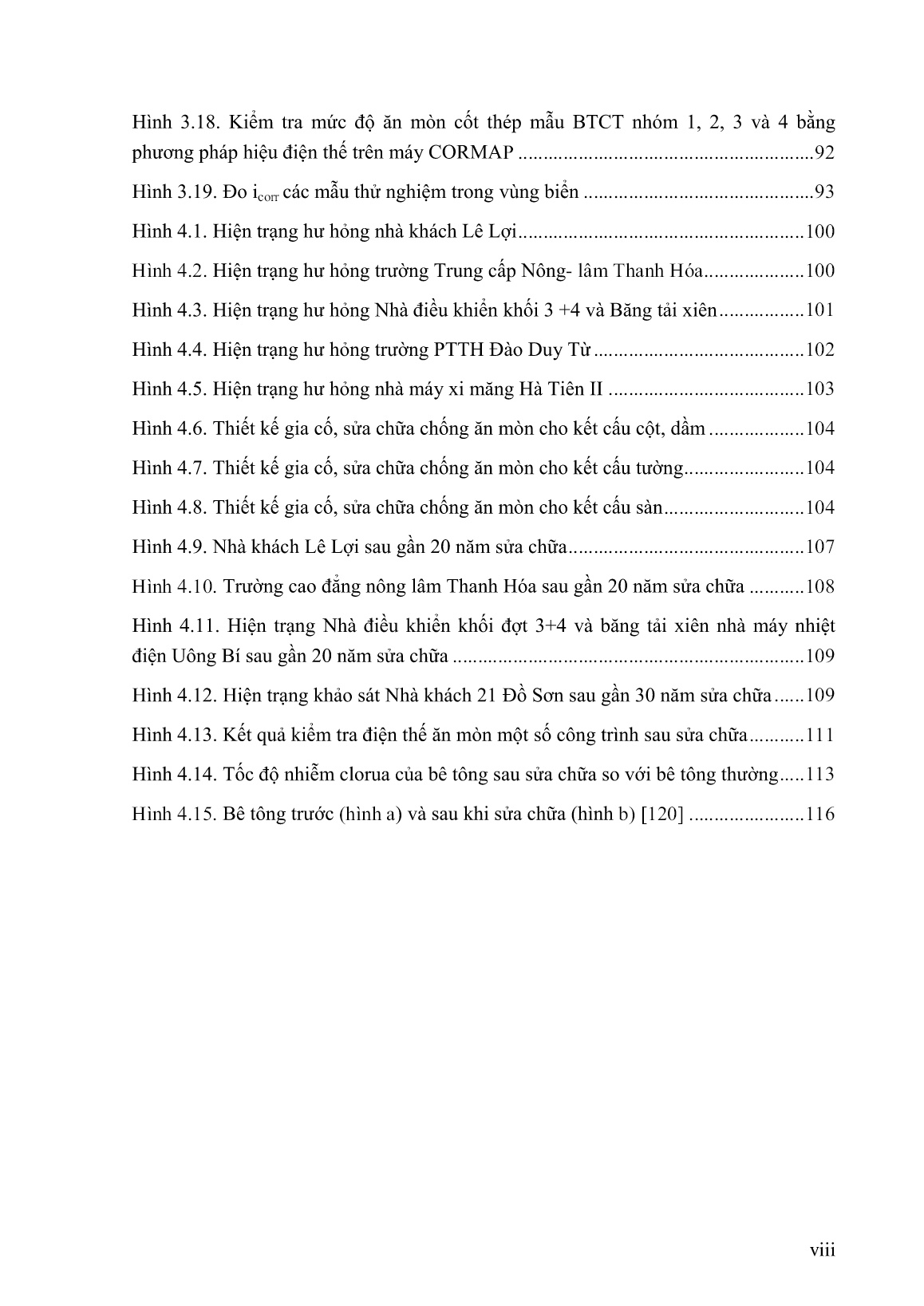
Trang 10
Tải về để xem bản đầy đủ
Bạn đang xem 10 trang mẫu của tài liệu "Luận án Nghiên cứu ứng dụng sơn phủ bảo vệ chống ăn mòn cho cốt thép trong bê tông vùng biển Việt Nam", để tải tài liệu gốc về máy hãy click vào nút Download ở trên.
Tóm tắt nội dung tài liệu: Luận án Nghiên cứu ứng dụng sơn phủ bảo vệ chống ăn mòn cho cốt thép trong bê tông vùng biển Việt Nam
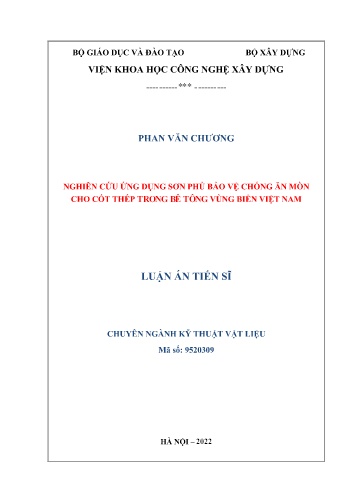
ông bay hơi % 65,55 TCVN 9014:2011 - Sơn Xi măng- polyme AC-05 : Thành phần A dạng bột, màu đỏ nhạt (gồm xi măng, bột mịn và chất ức chế ăn mòn cốt thép); thành phần B dạng lỏng, màu trắng sữa (latex acrylic butadien). Loại sơn này Trung tâm tư vấn chống ăn mòn và xây dựng của Viện KHCNXD đã sử dụng để sửa chữa các công trình bê tông cốt thép vùng biển và tại các nhà máy hóa chất công nghiệp. Tổng trọng lượng bộ 18 kg (thành phần A: 13 kg/bao, thành phần B: 5 Kg/can). Thông số kỹ thuật sản xuất trong Bảng 2.10, kết quả thử nghiệm trong Bảng 2.11. 50 Bảng 2.10. Thông số kỹ thuật sơn AC-05 Chỉ tiêu Thông số kỹ thuật Thời gian làm việc 1h ở nhiệt độ 20oC, ½ h ở nhiệt độ 30oC Thời gian khô hoàn toàn (24÷36) giờ Thời gian thi công ở 250C (30÷60) phút Bảng 2.11. Kết quả thử nghiệm sơn xi măng- polyme TT Chỉ tiêu thử Đơn vị Kết quả Phƣơng pháp thử 1 Thời gian khô hoàn toàn h, min 30h, 50 min TCVN 2096- 4:2015 2 Cường độ bám dính trên nền thép MPa 1,6 TCVN 9349:2012 - Sơn gốc Polyurethane: sản phẩm Cleanthane của ATEK. Sơn gồm có 2 thành phần: sơn gồm polyols hoặc polyester polyols; chất đóng rắn là polyisocyanate tỷ lệ trộn sơn và chất đóng rắn theo tỷ lệ 15,5 : 3,5 theo khối lượng. Thông số kỹ thuật chính của sơn theo công bố của nhà sản xuất trong Bảng 2.12, kết quả thí nghiệm một số tính chất của sơn trong Bảng 2.13. Bảng 2.12. Thông số kỹ thuật sơn polyurethane Chỉ tiêu Thông số kỹ thuật Tỉ trọng 1,15 kg/lít Hàm lượng chất khô ≥ 65% Cường độ chịu kéo ASTM D412 >1,5 MPa Độ bền mù muối > 720 giờ Chịu mài mòn < 60 mg Chịu va đập, chịu mài mòn, chống ăn mòn, khả năng chịu hoá chất và muối biển Đáp ứng tốt Thời gian khô hoàn toàn 18÷24 giờ Bảng 2.13. Kết quả thí nghiệm sơn polyurethane TT Chỉ tiêu thử Đơn vị Kết quả Phƣơng pháp thử 1 Ổn định trong thùng chứa - Khi khuấy trộn sơn trở nên đồng nhất không bị vón cục TCVN 9014:2011 2 Thời gian khô bề mặt h, min 1 h 58 min TCVN 2096- 4:2015 3 Độ bền va đập kG.cm 60 TCVN 2100- 2:2013 51 TT Chỉ tiêu thử Đơn vị Kết quả Phƣơng pháp thử 4 Hàm lượng chất không bay hơi % 70,31 TCVN 9014:2011 - Sơn epoxy giàu kẽm: Là sơn epoxy giàu kẽm một thành phần Master Emaco 8100AP. Được khuyến nghị sử dụng làm lớp phủ cho cốt thép trong bê tông, nơi có môi trường clorua tấn công. Chịu va đập, chịu mài mòn, bám dính tốt với cốt thép, chống ăn mòn cốt thép trên nguyên lý anot hy sinh. Hàm lượng Zn trong màng sơn khô >90%. Khả năng chịu hoá chất và môi trường kiềm cao. Tỷ trọng: 2,2 kg/lít ở 25 o C. Nhiệt độ khi sơn từ (10÷40) oC. Thời gian khô hoàn toàn: 12÷24 giờ. Độ nhớt động lực học 1,072 mPa.s ở 25oC. Thành phần hóa theo công bố của nhà sản xuất trong Bảng 2.14, kết quả thí nghiệm một số tính chất trong Bảng 2.15. Bảng 2.14.Thành phần hóa học của epoxy giàu kẽm Tên hóa học Hàm lƣợng, % 1-metoxypropan-2-ol 10÷ 15 cyclohexanone 0,3 ÷1 2-metoxypropyl axetat 0 ÷0,2 ZnO 3÷ 7 Zn 50÷70 Bảng 2.15. Kết quả thí nghiệm sơn epoxy giàu kẽm TT Chỉ tiêu thử Đơn vị Kết quả Phƣơng pháp thử 1 Ổn định trong thùng chứa - Khi khuấy trộn sơn trở nên đồng nhất, không bị vón cục TCVN 9012:2011 2 Thời gian khô bề mặt h, min 0 h 40 min TCVN 2096-4:2015 3 Độ bền va đập kG.cm 55 TCVN 2100-2:2013 4 Hàm lượng kẽm % 93,65 TCVN 9012:2011 2.1.8 . Một số tính chất kỹ thuật với sơn phủ cốt thép 2.1.8.1 . Lực bám dính của màng sơn vào nền thép Lực bám dính của màng sơn vào bề mặt nền cần bảo vệ là tính chất quan trọng của sơn, liên quan chặt chẽ đến chất lượng bảo vệ của màng sơn trước các yếu tố xâm thực (màng sơn càng bám chặt vào nền càng khó bị phồng rộp, bong tróc). Phương 52 pháp thí nghiệm theo tiêu chuẩn TCVN 9349:2012. Sơn thí nghiệm gồm 04 loại sơn trên nền thép đã được làm sạch, kết quả trong Bảng 2.16. Bảng 2.16. Kết quả lực bám dính của sơn vào nền thép Loại sơn Lực bám dính, N/mm2 Mẫu 1 Mẫu 2 Mẫu 3 Trung bình Xi măng- polyme 1,67 1,56 1,58 1,60 Polyurethane 3,81 3,67 3,54 3,67 Epoxy 4,32 4,13 3,81 4,09 Epoxy giàu kẽm 4,24 4,06 4,12 4,14 Kết quả cho thấy lực bám dính trên nền thép của sơn P, E và Z cao hơn so với sơn X, trong đó sơn Z có lực bám dính cao nhất so với các sơn còn lại. 2.1.8.2 . Độ bền hóa chất Độ bền hóa chất đối với sơn cốt thép trong BT chủ yếu là khả năng chịu kiềm, khả năng chịu nước muối. Hiện nay mới có yêu cầy kỹ thuật của sơn E theo TCVN 9014: 2011, phạm vi áp dụng tiêu chuẩn này cho sơn E là kết cấu thép và các kết cấu kim loại chịu tác động của môi trường khí quyển biển. Yêu cầu kỹ thuật TCVN 9013:2011 của sơn P cho kết cấu thép, chưa có yêu cầu kỹ thuật cho sơn X và Z. Điều kiện thử nghiệm khả năng chịu kiềm của sơn E là ngâm mẫu trong 168 giờ (7 ngày), chịu nước muối là 240 giờ (10 ngày). Độ bền kiềm và acid của P là 168 giờ (7 ngày) trong khi tiêu chuẩn ASTM A934 có yêu cầu về sơn cốt thép và được coi là đạt yêu cầu về độ bền hóa chất nếu sau 45 ngày ngâm trong dung dịch NaOH 3M, CaCl2 và nước cất không thấy bất kỳ dấu hiệu hư hỏng nào của màng sơn. Đối chiếu hai tiêu chuẩn thì ASTM A934 quy định dài ngày hơn và khắc nghiệt hơn. Do vậy áp dụng phương pháp thử một số chỉ tiêu và thời gian ngâm mẫu của ASTM A934 đối với 4 loại sơn Z, E, P và sơn X có kết hợp với thử độ chịu acid H2SO4 50 g/l. Tiến hành quét 04 loại sơn lên tấm thép kích thước 50 mm x 100 mm x 2 mm với chiều dày lớp phủ khoảng 100 µm, mỗi loại 3 tấm và tiến hành ngâm 2 tấm trong các dung dịch trên, 1 tấm giữ lại để so sánh. Kết quả thử nghiệm trong Bảng 2.17 cho thấy cả bốn loại sơn đều đạt yêu cầu theo tiêu chuẩn nói trên. 53 Bảng 2.17. Kết quả thử nghiệm độ bền hóa chất của màng sơn Tên chỉ tiêu Epoxy Xi măng- polyme Polyurethane Epoxy giàu kẽm Dung dịch NaOH 3M Không hỏng Không hỏng Không hỏng Không hỏng Dung dịch CaCl2 Không hỏng Không hỏng Không hỏng Không hỏng Nước cất Không hỏng Không hỏng Không hỏng Không hỏng H2SO4 50g/l Không hỏng Không hỏng Không hỏng Không hỏng 2.1.8.3 . Độ bền uốn của các loại sơn Thí nghiệm độ bền uốn thể hiện sự làm việc đồng thời của cốt thép khi sơn và BT, khi kết cấu chịu tác động của tải trọng bị nứt thì sơn có còn khả năng bảo vệ cốt thép khỏi tác động ăn mòn nữa không. Nếu sơn không bị rạn hay nứt, mặc dù BT bị nứt thì vẫn đảm bảo được tính chất bảo vệ cốt thép khi có sự xâm nhập của tác nhân ăn mòn bên ngoài. Thí nghiệm độ bền uốn theo TCVN 2099:2007 như Hình 2.3. Hình 2.3. Đo độ bền uốn màng sơn và kiểm tra trên kính núp Bảng 2.18. Kết quả đo độ bền uốn của các màng sơn Trục Loại sơn Φ 1 Φ 2 Φ 3 Φ 4 Polyurethane Đạt Đạt Đạt Đạt Xi măng - polyme Có hiện tượng rạn Có hiện tượng rạn Đạt Đạt Epoxy Đạt Đạt Đạt Đạt Epoxy giàu kẽm Đạt Đạt Đạt Đạt Các kết quả thí nghiệm trong Bảng 2.18 cho thấy, việc sử dụng các loại sơn khác nhau có độ bền uốn đạt qua trục Φ 3. Sơn polyurethane cho kết cấu thép theo TCVN 54 9013: 2011 có yêu cầu độ bền uốn chịu được uốn cong 2 mm, nếu áp dụng tiêu chuẩn này thì sơn Polyurethane đạt độ bền uốn. 2.1.9 . Chế tạo các mẫu sơn cốt thép trƣớc khi đổ BT Sơn phủ cốt thép dùng trong nghiên cứu bao gồm sơn X, P, E hai thành phần và Z một thành phần. Nhiệt độ môi trường khi sơn cốt thép nên từ (10÷35) oC và độ ẩm tương đối không được vượt quá 85%. Sơn và chất pha loãng trong quá trình bảo quản, chế tạo mẫu và bảo dưỡng không bị nhiễm axit, kiềm và các tác nhân hóa học khác, không để gần lửa và được bảo vệ tránh ánh nắng mặt trời. Dùng giấy ráp để tẩy các gỉ sét, sau đó , làm sạch bụi bằng khí nén và vải lau sao cho bề mặt cốt thép đạt mức Sa 2 theo ISO 8501-1. Dùng vải tẩm dung môi (xăng, cồn) để tẩy sạch các vết bụi bẩn bám trên bề mặt thép. Cốt thép được ngâm xăng trong quá trình bảo quản để tránh gỉ trở lại. Sơn hai thành phần (X, P, E) được chuẩn bị theo tỷ lệ khuyến cáo của nhà sản xuất và khuấy đều trước và sau khi trộn. Sơn Z một thành phần được khuấy đều trước khi sơn. Tiến hành nhúng cốt thép vào sơn đã chuẩn bị, mỗi lần nhúng cách nhau 60 phút, kết hợp quét, lăn để độ dày lớp phủ đồng đều. Kiểm tra khuyết tật màng sơn (bao gồm bong tróc, lỗ) và bịt kín các khuyết tật. Khi xuất hiện các kết tủa trắng trên bề mặt của sơn phủ epoxy giàu kẽm, làm sạch để loại bỏ các kết tủa trước khi sơn lại. Kiểm tra chiều dày màng sơn khô theo tiêu chuẩn TCVN 9760:2013 sau 7 ngày để khô hoàn toàn trong điều kiện tự nhiên. Khi chiều dày đạt yêu cầu, cốt thép được tiến hành đổ bê tông ngay sau đó. 2.2 . Phƣơng pháp nghiên cứu Phương pháp nghiên cứu trong luận án là kết hợp kết quả thí nghiệm trong phòng với kết quả nghiên cứu trên các công trình thực. Kết quả trong phòng cho phép so sánh hiệu quả bảo vệ cốt thép của các giải pháp bảo vệ cốt thép. Kết quả nghiên cứu trên công trình thực dùng để minh chứng, định lượng thời gian bảo vệ cốt thép của giải pháp nghiên cứu trong phòng và đề xuất lựa chọn các phương án đạt hiệu quả kinh tế - kỹ thuật để đưa vào áp dụng trong thực tế. Sơ đồ nghiên cứu của luận án như Hình 2.4, theo đó, nghiên cứu được tiến hành song song trong phòng thí nghiệm và trên các công trình đã ứng dụng. Kết quả phòng thi nghiệm dùng để so sánh khả năng bảo vệ cốt thép của các giải pháp áp dụng. Kết quả trên công trình ứng dụng để minh chứng cho 55 các phương án phòng thí nghiệm và lượng hóa chỉ tiêu về độ bền và mức tái nhiễm clorua trong môi trường biển Việt Nam. Hình 2.4. Sơ đồ nghiên cứu trong luận án Dưới đây là một số tiêu chuẩn chính thí nghiệm phục vụ nghiên cứu trong phòng và trên công trình. 2.2.1 . Thí nghiệm các chỉ tiêu cơ, lý, hóa của vật liệu theo các tiêu chuẩn hiện hành Các chỉ tiêu chính về cơ, lý, hóa của vật liệu được liệt kê trong Bảng 2.19. 56 Bảng 2.19. Các tiêu chuẩn thử nghiệm dùng trong nghiên cứu TT Tên tiêu chuẩn Tên tiêu chuẩn áp dụng 1 Xi măng. Phương pháp thử. Xác định độ dẻo tiêu chuẩn, thời gian đông kết, độ ổn định thể tích. TCVN 6017:2015 2 Xi măng. Phương pháp xác định độ bền uốn và nén TCVN 6016:1995 3 Xi măng. Phương pháp xác định độ mịn của bột xi măng TCVN 4030: 2003 4 Cốt liệu cho BT và vữa- Phương pháp thử xác định thành phần hạt TCVN 7572-2:2006 5 Cốt liệu cho BT và vữa- Phương pháp thử xác định khối lượng riêng, khối lượng thể tích, độ hút nước TCVN 7572-4 :2006 6 Cốt liệu cho BT và vữa- Phương pháp thử xác định khối lượng thể tích xốp và độ hổng TCVN 7572-6 :2006 7 Cốt liệu cho BT và vữa- Phương pháp thử xác định độ ẩm TCVN 7572-7 :2006 8 Cốt liệu cho BT và vữa- Phương pháp thử xác định hàm lượng clorua TCVN 7572-15 :2006 9 Phụ gia hóa học cho BT TCVN 8826: 2011 10 Chất lượng nước- xác định độ pH TCVN 6492:2011 11 Chất lượng nước- xác định chỉ số pemanganat TCVN 6186:1996 12 Chất lượng nước- xác định clorua- chuẩn độ bạc nitrat với chỉ thi cromat (phương pháp mở) TCVN 6194:1996 13 Chất lượng nước- xác định sunfat- phương pháp trọng lượng sử dụng bariclorua TCVN 6200:1996 14 Sơn và vecni - Phép thử biến dạng nhanh (Độ bền va đập) - Phần 2: Phép thử tải trọng rơi, mũi ấn có diện tích nhỏ TCVN 2100-2:2013 15 Sơn và vecni - Phép thử uốn (trục hình trụ) TCVN 2099:2007 16 Bê tông cốt thép - Kiểm tra khả năng cốt thép bị ăn mòn - Phương pháp điện thế TCVN 9348:2012 17 Bê tông nặng - Phương pháp xác định độ chống thấm nước TCVN 3116:1993 18 Concrete, repairing materials and protective coating: Embedded steel method, chloride permeability NT Build 356 19 Standard Specification for Epoxy-Coated Steel Reinforcing Bars ASTM A775/A775M– 01 57 TT Tên tiêu chuẩn Tên tiêu chuẩn áp dụng 20 Standard Specification for Epoxy-Coated Prefabricated Steel Reinforcing Bars ASTM A934/A934M-01 21 Standard Test Method for Conducting Potentiodynamic Polarization Resistance Measurements ASTM G59/97 22 Một số tiêu chuẩn thử nghiệm khác 2.2.2 . Các phƣơng pháp điện hóa 2.2.2.1 . Thí nghiệm khả năng chống ăn mòn cho cốt thép bằng phƣơng pháp gia tốc theo tiêu chuẩn NT Build 356 Phương pháp gia tốc theo tiêu chuẩn NT Build 356 [12, 42] của Hội thử nghiệm Bắc Âu NORDTEST đã được nhiều tác giả sử dụng để nghiên cứu ăn mòn cốt thép trong BT [14, 15, 29, 30, 57, 86, 103, 110-112]. Phương pháp gia tốc bằng dòng điện một chiều dựa trên bản chất ăn mòn cốt thép trong BT là quá trình điện hoá nên có thể sử dụng dòng điện làm tăng khuếch tán Cl - vào trong BT làm tăng mạnh mẽ tốc độ phản ứng ăn mòn, đây là phương pháp gia tốc có hiệu quả để đánh giá khả năng chống ăn mòn cho BTCT [59, 96]. Khi áp một dòng điện có thế không đổi vào hệ trong môi trường có ion Cl-, hai tác nhân clorua và dòng điện tác động đồng thời vào hệ dẫn đến quá trình ăn mòn sẽ xảy ra nhanh hơn gấp nhiều lần khi không có điện áp vào hệ. Tại thời điểm ban đầu, lớp BT còn khả năng bảo vệ nên cường độ dòng điện nhỏ, khi hàm lượng Cl- trong BT và trong dung dịch dịch chuyển đến cốt thép tăng, độ dẫn điện tăng lên nên cường độ dòng điện tăng theo. Sự gia tăng về cường độ dòng điện đến đột biến cho thấy bắt đầu ăn mòn và nứt bê tông được nhìn thấy sau đó [49],[77]. 58 Hình 2.5. Sơ đồ và mẫu thí nghiệm theo phƣơng pháp gia tốc dòng điện ngoài Sơ đồ và mẫu thí nghiệm xem Hình 2.5. Các mẫu BTCT bắt đầu được thí nghiệm gia tốc khi đủ tuổi 28 ngày, mẫu được ngâm trong dung dịch NaCl 3% sao cho luôn giữ mực nước cách đỉnh mẫu là 3cm, cốt thép được nối với cực dương của nguồn điện một chiều có điện thế không đổi 5V, cực âm nối với một điện cực khác bằng thép không gỉ cùng nhúng trong dung dịch. Dưới tác động của dòng điện, tốc độ khuyếch tán ion Cl- vào cốt thép tăng nhanh và quá trình ăn mòn cốt thép tăng tốc mạnh, tạo gỉ gây nứt mẫu. Cường độ dòng điện được đo liên tục sau từng 24h đồng thời quan sát trạng thái bề mặt của mẫu. Tại thời điểm cường độ dòng điện tăng đột biến thường xuất hiện trạng thái nứt mẫu kèm theo gỉ thép tiết ra mặt ngoài theo chiều dọc của thanh thép. Khả năng bảo vệ cốt thép của bê tông hoặc sơn cốt thép kết hợp bê tông càng cao thì khoảng thời gian tính từ khi thí nghiệm đến khi cường độ dòng điện tăng đột biến, cốt thép gỉ phá vỡ mẫu càng tăng. Khoảng thời gian này được quy ước trong luận án là “khả năng bảo vệ cốt thép”. Chuẩn bị các tổ mẫu (gồm 3 viên mẫu/tổ) theo nội dung nghiên cứu như sau: - Bê tông có độ chống thấm W10 (M300), W12 (M400), W16 (M500) hình trụ đường kính 70 mm, cao 200 mm, chiều dày lớp BT bảo vệ cốt thép là 30 mm, cốt thép CT3 có đường kính 10 mm. Hàm lượng clorua trong mỗi mẫu là 0,6; 1,2 ; 1,8 và 2,4 kg/m 3 BT. 59 - Bê tông có độ chống thấm W10 (M300) hình trụ đường kính 110 mm, 150 mm, cao 200 mm, chiều dày lớp BT bảo vệ cốt thép là 50 mm, 70 mm cốt thép CT3 có đường kính 10 mm. Hàm lượng clorua trong mỗi mẫu có chiều dày BT bảo vệ khác nhau là 0,6; 1,2 ; 1,8 và 2,4 kg/m 3 BT. - Bê tông có độ chống thấm W12 (M400), W16 (M500) hình trụ đường kính 110 mm, 150 mm, cao 200 mm, chiều dày lớp BT bảo vệ cốt thép là 50 mm, 70 mm cốt thép CT3 có đường kính 10 mm. Các mẫu BT có hàm lượng clorua là 2,4 kg/m3BT. - Bê tông có độ chống thấm W10 (M300) hình trụ đường kính 70 mm, cao 200 mm, chiều dày lớp BT bảo vệ cốt thép là 30 mm, cốt thép CT3 có đường kính 10 mm. Các mẫu BT có hàm lượng clorua là 0,6; 1,2 ; 1,8 và 2,4 kg/m3BT. Cốt thép được sơn phủ 4 loại sơn: Z, E, P, X bằng cách nhúng và sơn quét kết hợp, chiều dày của mỗi loại sơn theo thứ tự (175±18) µm, (175±18) µm, (150±15) µm, (1500±150) µm. Các mẫu thí nghiệm theo phương pháp NT Build 356 được tổng hợp trong Bảng 2.20. Bảng 2.20. Ký hiệu mẫu thí nghiệm gia tốc NT Build 356 STT Bê tông Ký hiệu mẫu [Cl - ], kg/m 3 ∆, mm Ghi chú 1 M300, W10 M30.3.0.6 0,6 30 Tăng [Cl-] 2 M30.3.1.2 1,2 30 3 M30.3.1.8 1,8 30 4 M30.3.2.4 2,4 30 5 M400, W12 M40.3.0.6 0,6 30 Tăng W 6 M40.3.1.2 1,2 30 7 M40.3.1.8 1,8 30 8 M40.3.2.4 2,4 30 9 M500, W16 M50.3.0.6 0,6 30 Tăng W 10 M50.3.1.2 1,2 30 11 M50.3.1.8 1,8 30 12 M50.3.2.4 2,4 30 13 M300, W10 M30.5.0.6 0,6 50 Tăng ∆ 14 M30.5.1.2 1,2 50 15 M30.5.1.8 1,8 50 16 M30.5.2.4 2,4 50 17 M300, W10 M30.7.0.6 0,6 70 Tăng ∆ 18 M30.7.1.2 1,2 70 19 M30.7.1.8 1,8 70 20 M30.7.2.4 2,4 70 21 M400, W12 M40.5.2.4 2,4 50 Tăng W+∆ 22 M40.7.2.4 2,4 70 60 STT Bê tông Ký hiệu mẫu [Cl - ], kg/m 3 ∆, mm Ghi chú 23 M500, W16 M50.5.2.4 2,4 50 Tăng W+∆ 24 M50.7.2.4 2,4 70 25 M300, W10 M30.3.0.6.X 0,6 30 Sơn X 26 M30.3.1.2.X 1,2 30 27 M30.3.1.8.X 1,8 30 28 M30.3.2.4.X 2,4 30 29 M300, W10 M30.3.0.6.P 0,6 30 Sơn P 30 M30.3.1.2.P 1,2 30 31 M30.3.1.8.P 1,8 30 32 M30.3.2.4.P 2,4 30 33 M300, W10 M30.3.0.6.E 0,6 30 Sơn E 34 M30.3.1.2.E 1,2 30 35 M30.3.1.8.E 1,8 30 36 M30.3.2.4.E 2,4 30 37 M300, W10 M30.3.0.6.Z 0,6 30 Sơn Z 38 M30.3.1.2.Z 1,2 30 39 M30.3.1.8.Z 1,8 30 40 M30.3.2.4.Z 2,4 30 Cấp phối, cường độ chịu nén và độ chống thấm nước của BT được thể hiện trong Bảng 2.21. Bảng 2.21. Cấp phối, cƣờng độ chịu nén, mác chống thấm nƣớc của BT có hàm lƣợng clorua khác nhau STT Mác BT Thành phần vật liệu trong 1m3 BT [Cl - ], kg/m 3 BT R28, MPa Cấp chống thấm Xi măng, kg Cát , kg Đá , kg Nƣớc, lít Phụ gia siêu dẻo, lít 1 M300 348 725 1165 185 3,83 0,6 33,2 W10 2 348 725 1165 185 3,83 1,2 33,9 W10 3 348 725 1165 185 3,83 1,8 34,4 W10 4 348 725 1165 185 3,83 2,4 34,8 W10 5 M400 429 678 1147 183 4,72 0,6 43,2 W12 6 429 678 1147 183 4,72 1,2 44,8 W12 7 429 678 1147 183 4,72 1,8 45,5 W12 8 429 678 1147 183 4,72 2,4 46,1 W12 9 M500 507 634 1130 181 5,58 0,6 52,1 W16 10 507 634 1130 181 5,58 1,2 53,6 W16 61 STT Mác BT Thành phần vật liệu trong 1m3 BT [Cl - ], kg/m 3 BT R28, MPa Cấp chống thấm Xi măng, kg Cát , kg Đá , kg Nƣớc, lít Phụ gia siêu dẻo, lít 11 507 634 1130 181 5,58 1,8 55,2 W16 12 507 634 1130 181 5,58 2,4 55,7 W16 Hàm lượng clorua trong bê tông với các mức 0,6; 1,2 ; 1,8 và 2,4 kg/m3BT được chuẩn bị như sau: - Chuẩn bị cát sạch từ cát nhiễm mặn: Lượng cát sạch được tạo ra bằng cách sục rửa nước sạch vào cát nhiễm mặn cho đến khi hàm lượng clorua đạt giá trị 0 ppm (kiểm tra nhanh bằng thiết bị đo độ mặn) hoặc phân tích hóa học theo tiêu chuẩn TCVN 7572-15: 2006. Cát này sẽ được dùng để phối trộn với cát nhiễm mặn ban đầu. - Trộn cát nhiễm mặn và cát sạch (đã rửa) theo các tỷ lệ khác nhau để đạt hàm lượng clorua là 0,6; 1,2 ; 1,8 và 2,4 kg/m3BT; sau đó dùng cát đã phối trộn có hàm lượng clorua khác nhau để đổ bê tông. Xác định clorua trong bê tông theo theo tiêu chuẩn TCVN 7572-15: 2006. 2.2.2.2 . Thí nghiệm khả năng xảy ra ăn mòn cốt thép bằng phƣơng pháp điện trở phân cực Phương pháp đo điện trở phân cực còn được gọi là phương pháp phân cực tuyến tính. Phương pháp này do Stern Geary đề ra năm 1956 và đã được phát triển, áp dụng tính tốc độ ăn mòn cho nhiều hệ ăn mòn có kết quả rất tốt. Hình 2.6. Đƣờng cong phân cực ΔE - f(i) Trên đường phân cực E - f(i) (Hình 2.6) áp dụng cho hệ ăn mòn có hai phản ứng: 62 Phản ứng xảy ra trên anot, kim loại Me bị hoà tan: Me – ze → Me2+ và trên catot xảy ra phản ứng: zH++ ze → 2 z H2 Tại khoảng thế phân cực ΔE rất nhỏ so với Ecorr, ΔE = ±10 mV, sự phụ thuộc của ΔE vào mật độ dòng (thí nghiệm với điện cực có diện tích 1 cm2) là tuyến tính: RP=[ di Ed )( ]Ecor= corI B (2.1) Mặt khác giá trị B được tính theo công thức: B= ).(3,2 . MeH MeH bb bb (2.2) Trong đó: bH - là hệ số độ dốc đoạn thẳng Tafel đối với quá trình catot thoát khí hiđro thay đổi giá trị từ 0,06 V ÷ ∞; bMe - là hệ số độ dốc đoạn thẳng Tafel đối với quá trình anot hoà tan kim loại thay đổi từ 0,06 ÷ 0,12 V. Từ (2.2) ta có: icorr= PR B (2.3) Vậy muốn xác định tốc độ ăn mòn k
File đính kèm:
luan_an_nghien_cuu_ung_dung_son_phu_bao_ve_chong_an_mon_cho.pdf
2. Tóm tắt LA V- Phan Văn Chương.pdf
3. Tóm tắt E- Phan văn chương.pdf
4. Đóng góp mới-V-phan văn Chương.pdf
5. Đóng góp mới-E-phan văn Chương.pdf
6. Trích yếu luận án-NCS. Phan Văn Chương.pdf