Luận án Phát triển hệ thống phản hồi lực dùng lưu chất từ biến
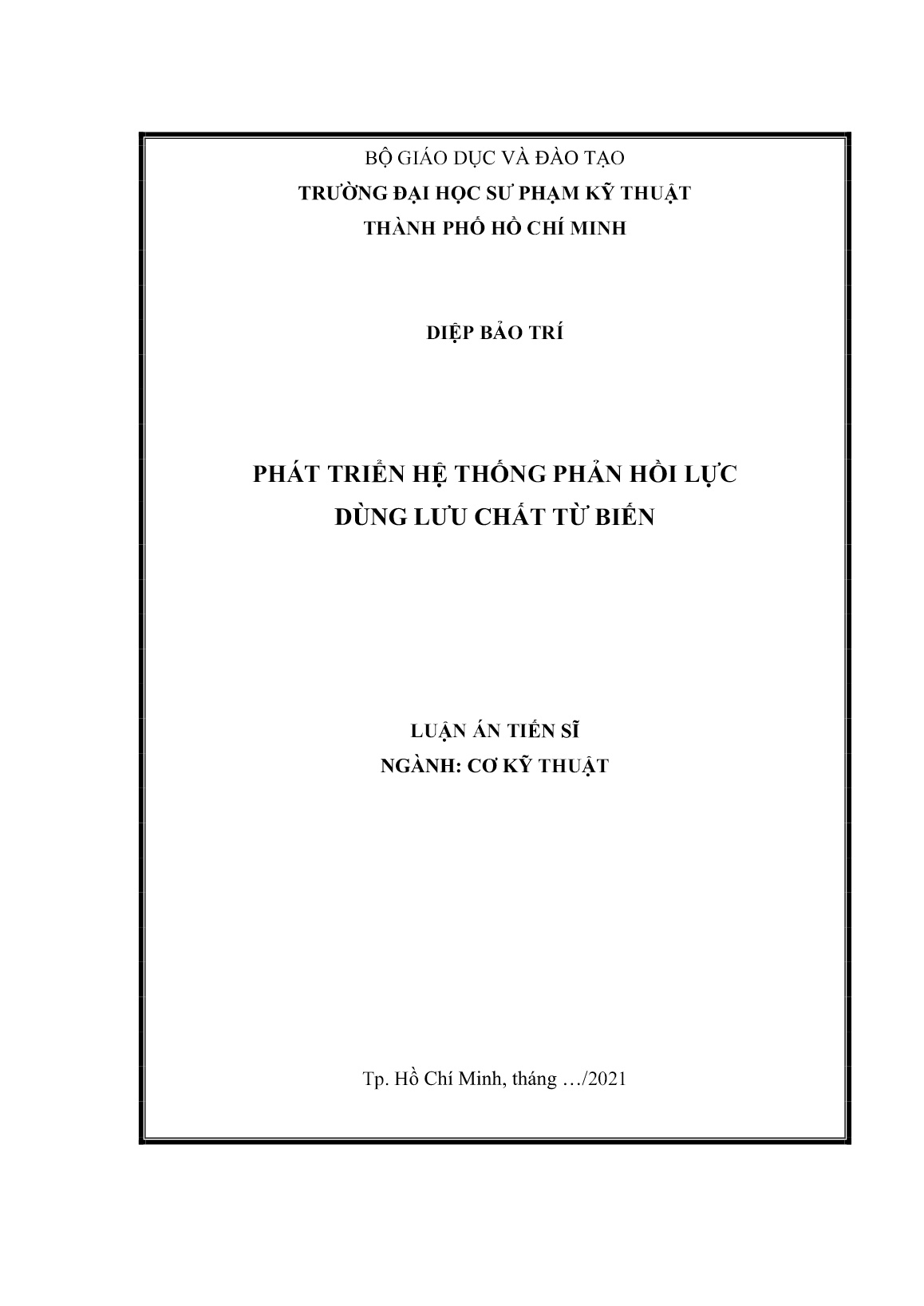
Trang 1
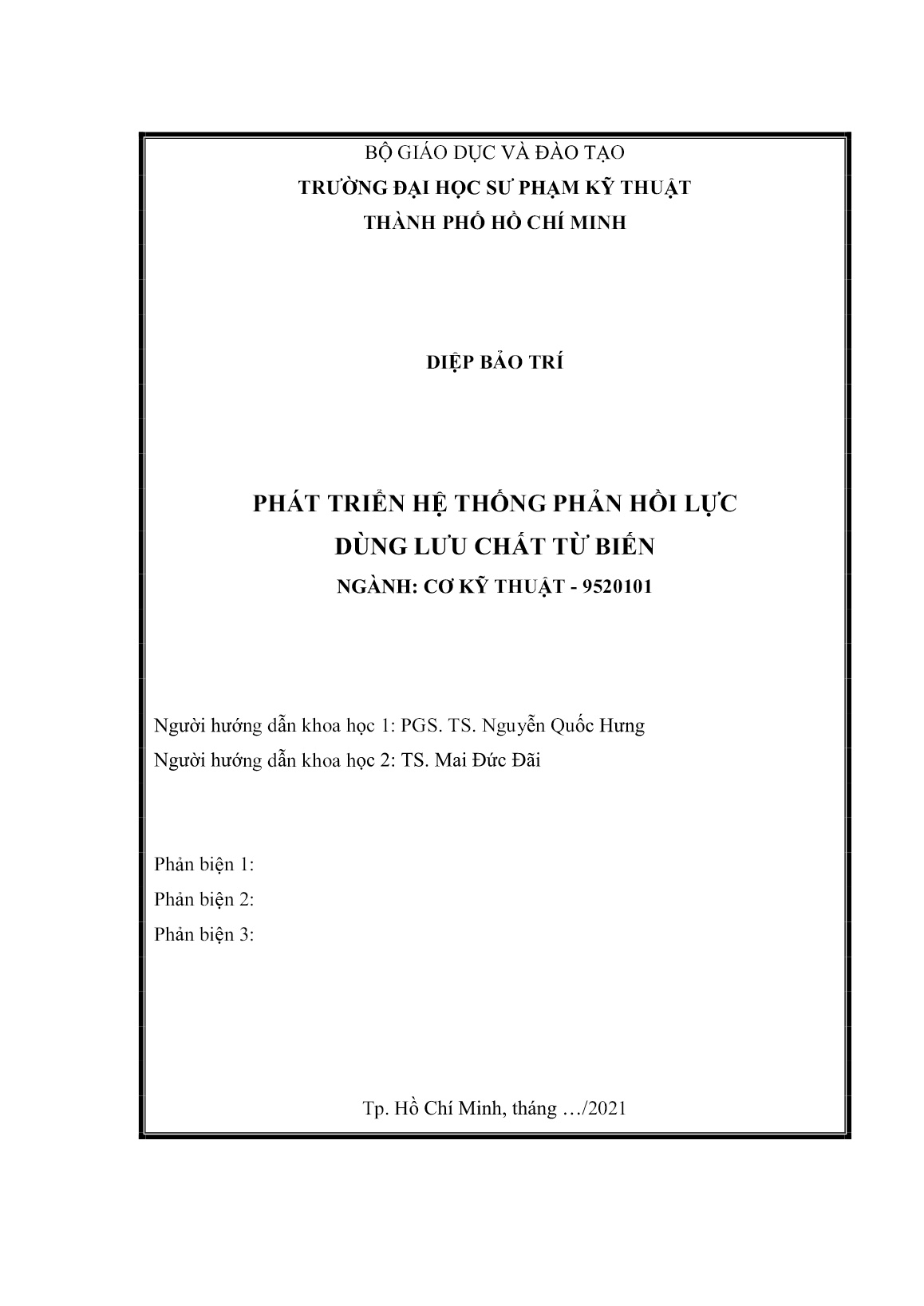
Trang 2
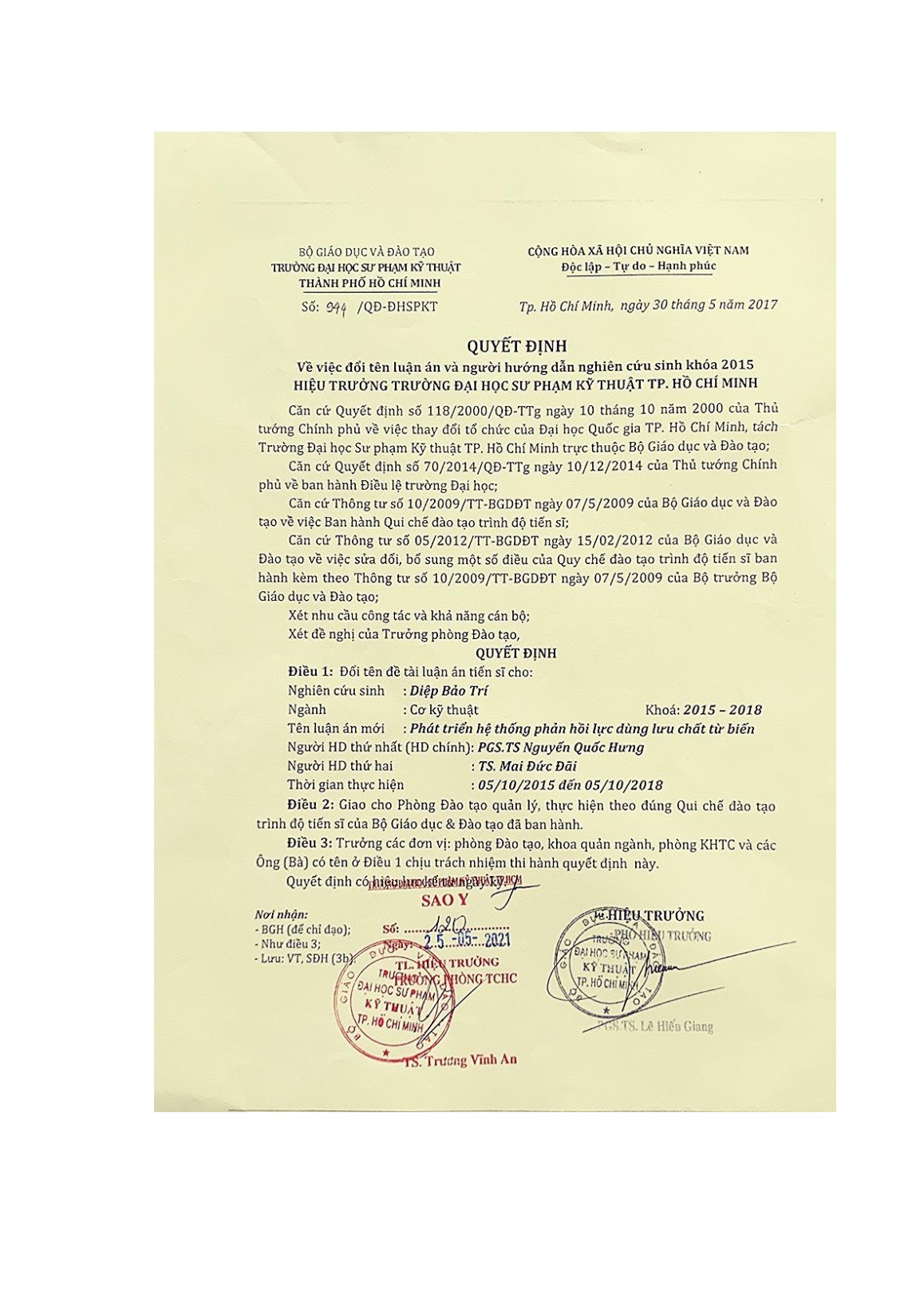
Trang 3
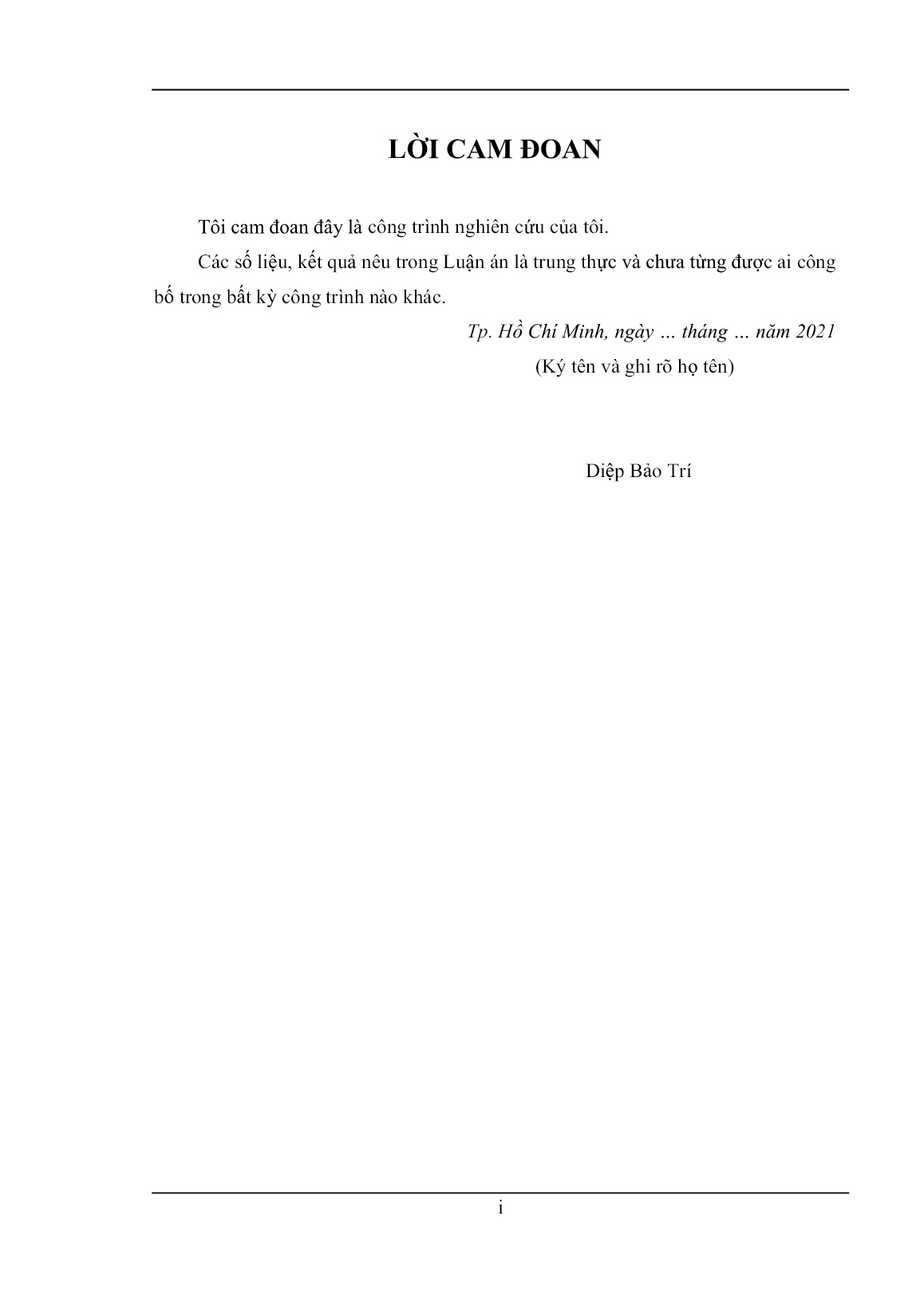
Trang 4
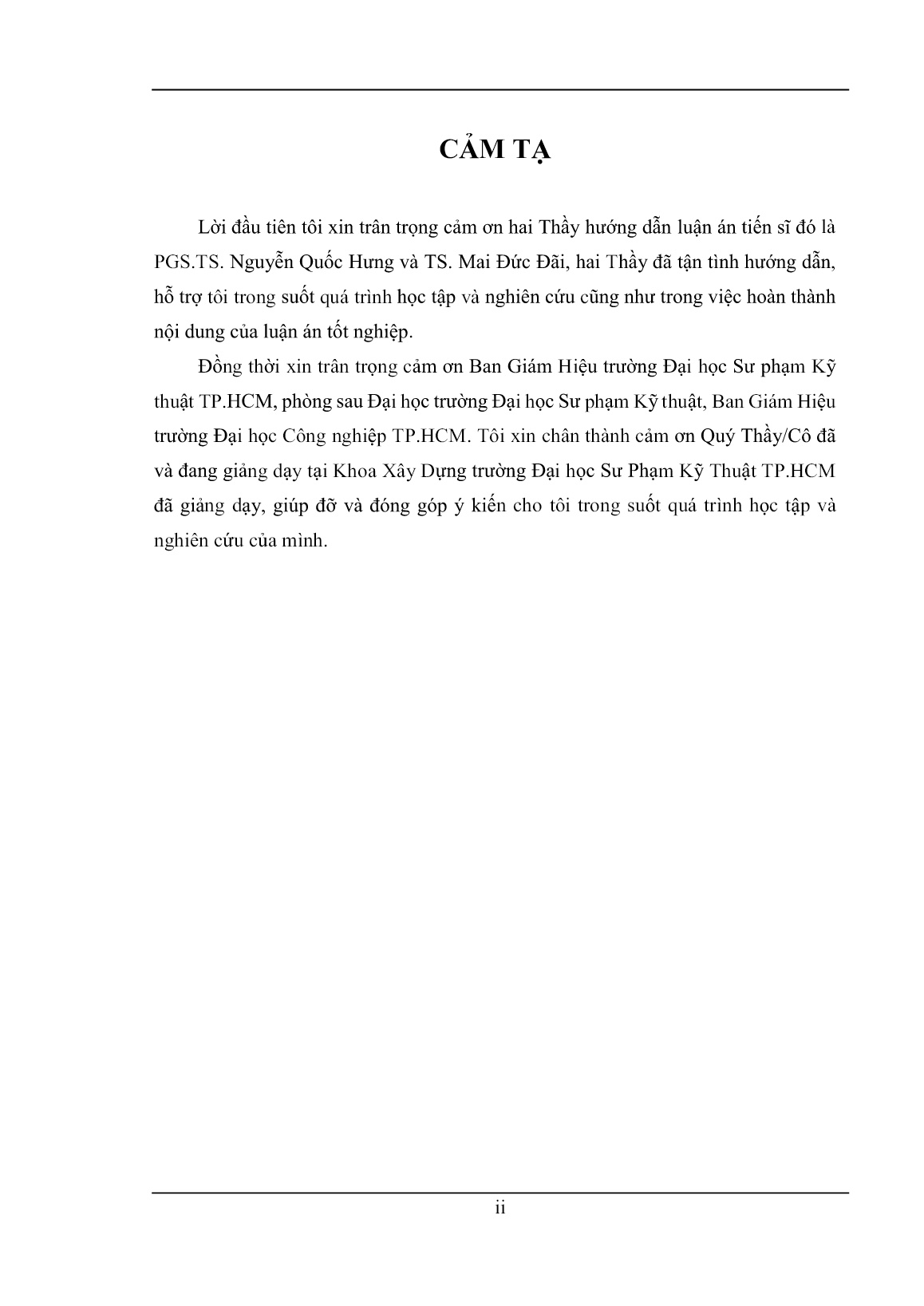
Trang 5
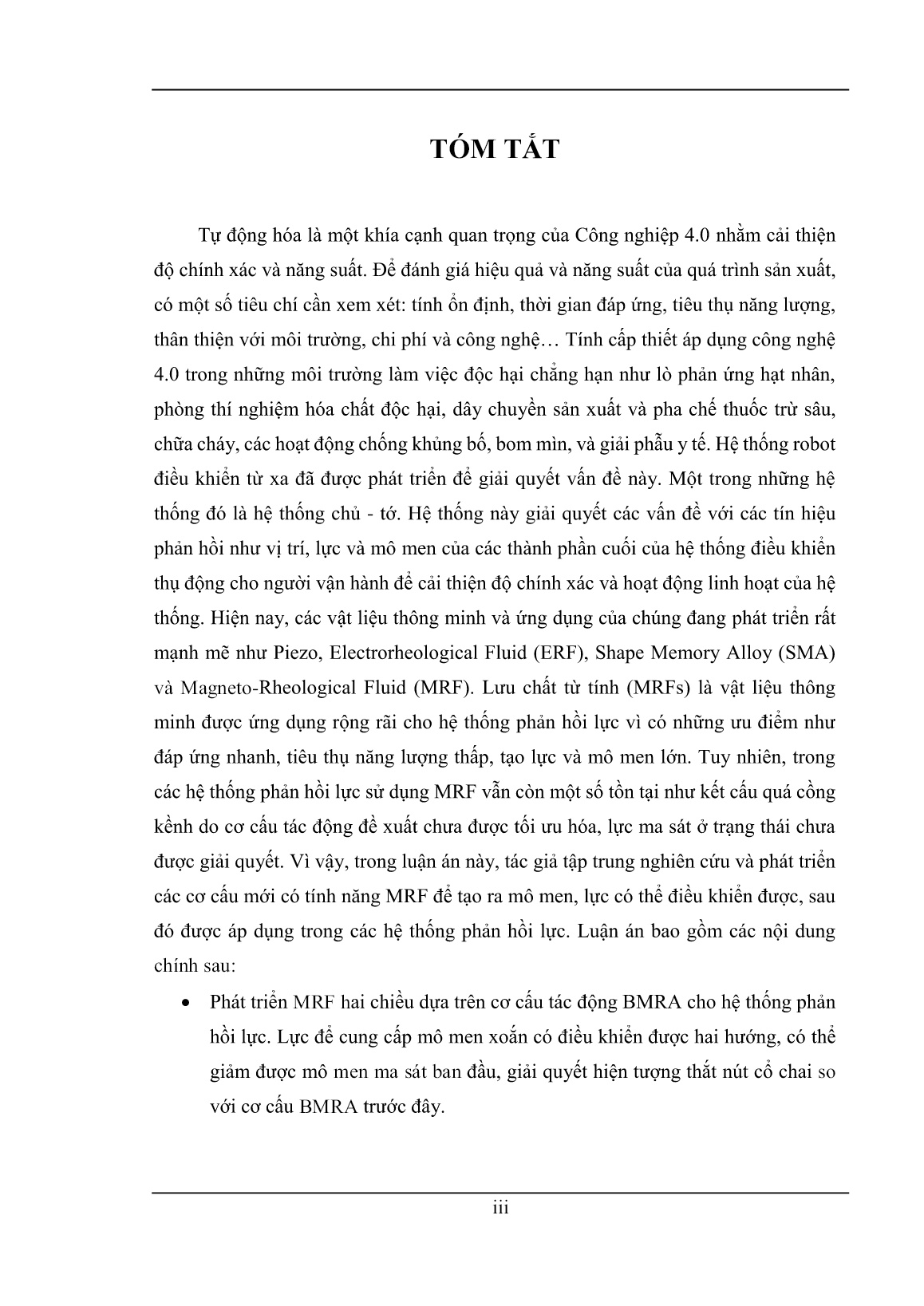
Trang 6
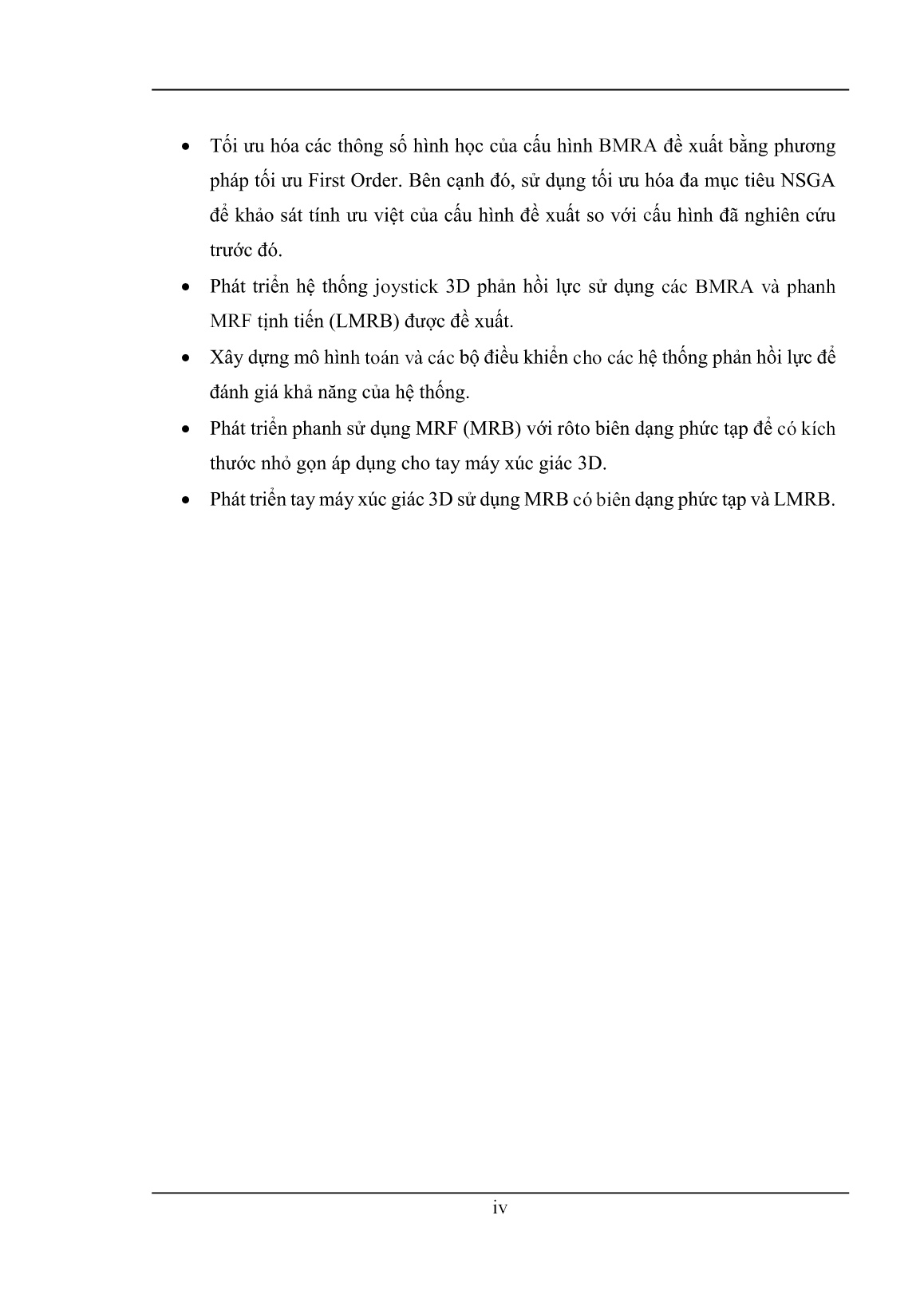
Trang 7
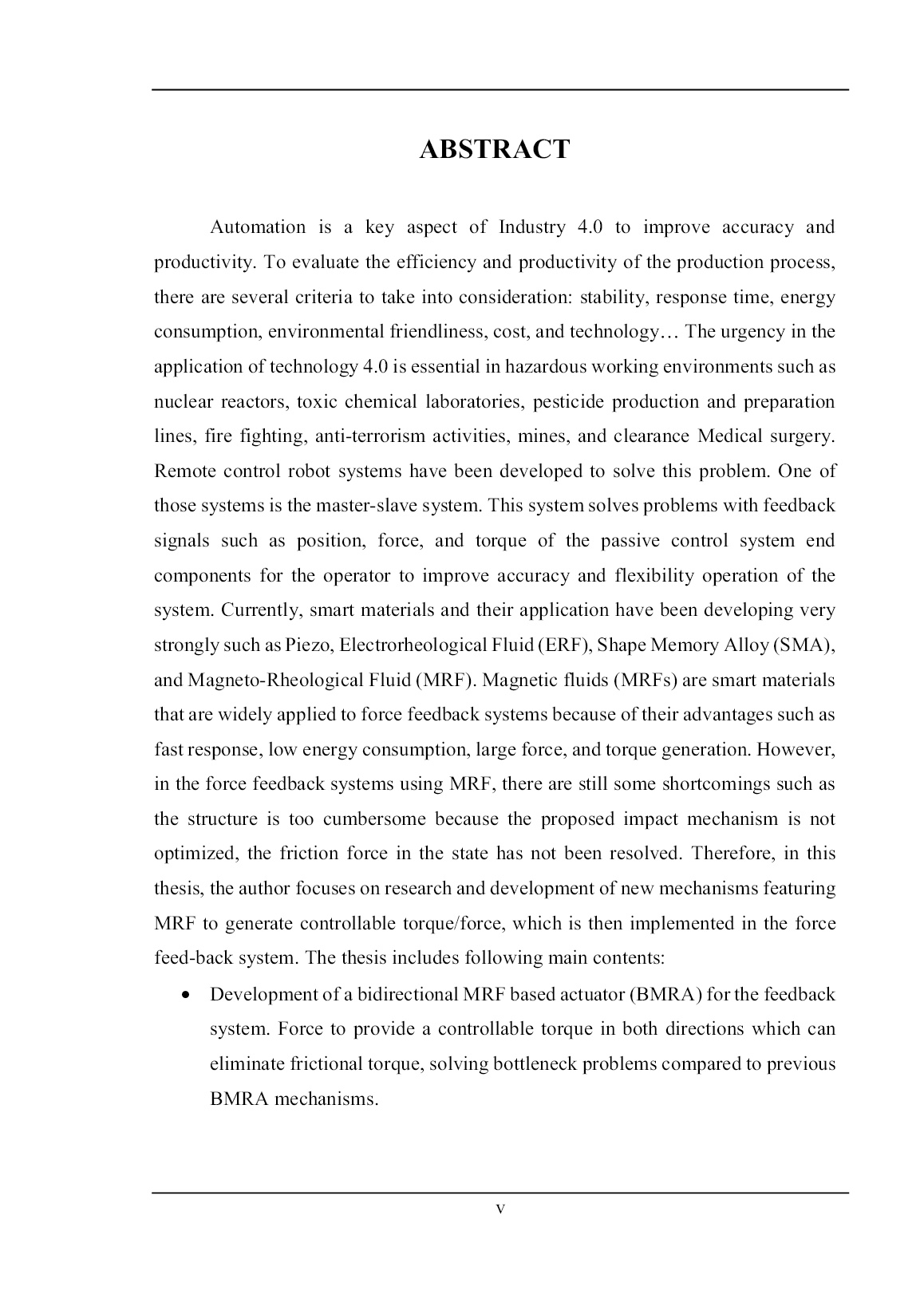
Trang 8
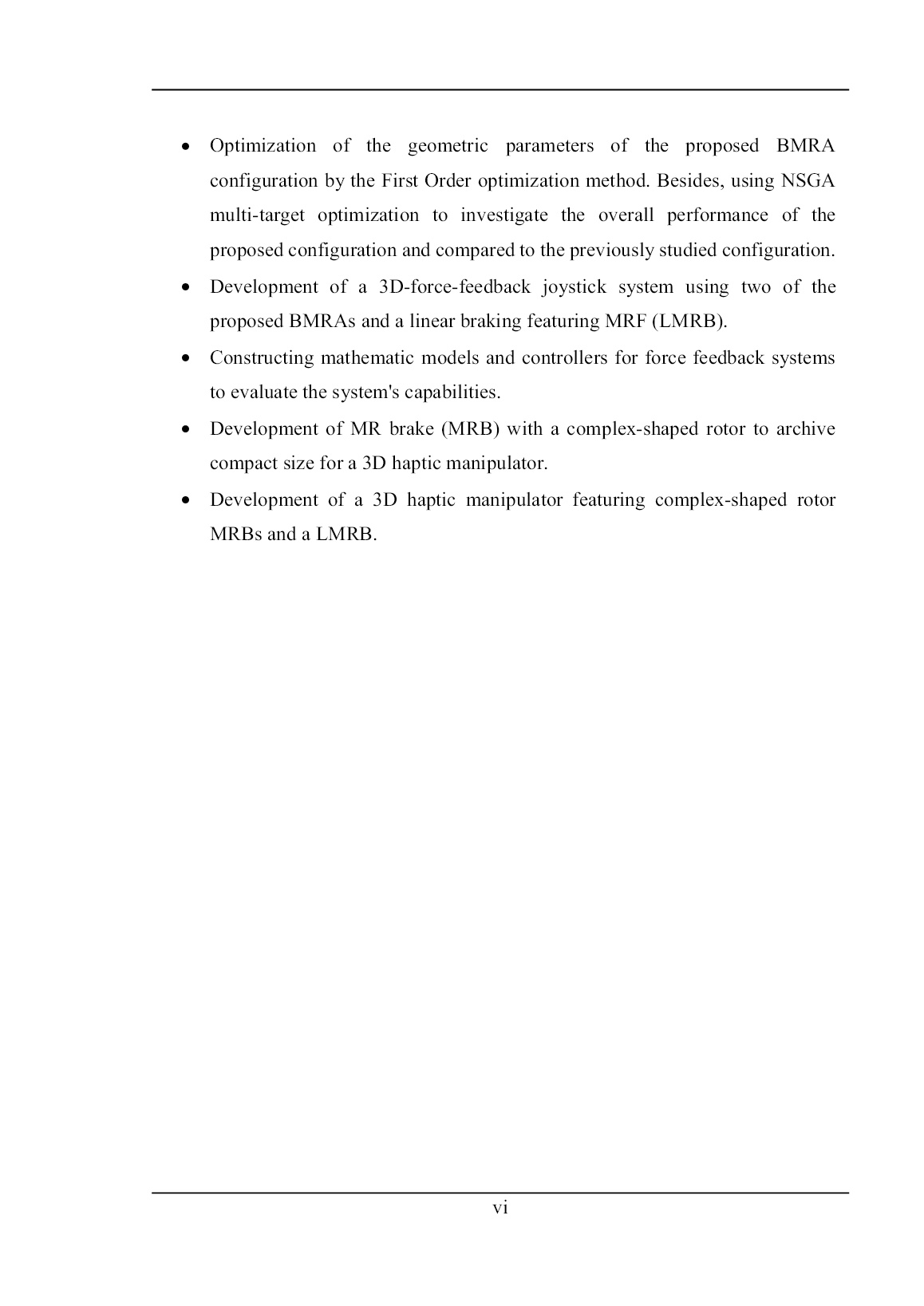
Trang 9
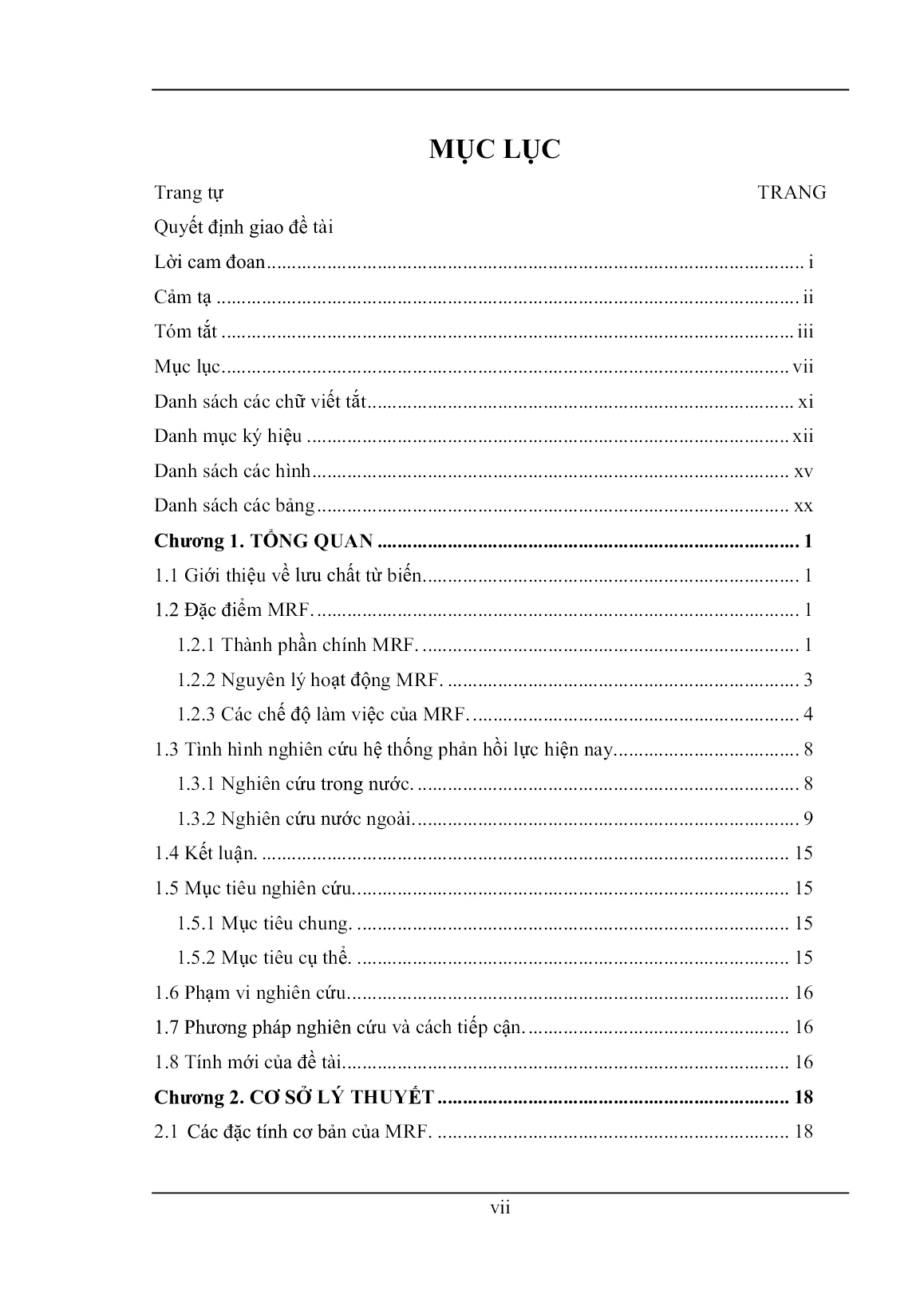
Trang 10
Tải về để xem bản đầy đủ
Bạn đang xem 10 trang mẫu của tài liệu "Luận án Phát triển hệ thống phản hồi lực dùng lưu chất từ biến", để tải tài liệu gốc về máy hãy click vào nút Download ở trên.
Tóm tắt nội dung tài liệu: Luận án Phát triển hệ thống phản hồi lực dùng lưu chất từ biến
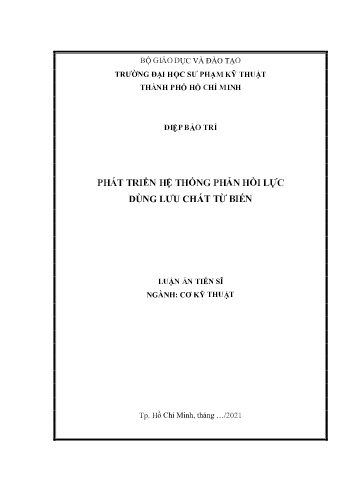
ều khiển chuyển đổi buộc hệ thống trượt trên mặt trượt. Xét một hệ thống phi tuyến SISO thứ tự n được mô tả như sau: 𝑥(𝑛) = 𝑓(𝑥, 𝑡) + 𝑏𝑢(𝑡) + 𝑑(𝑡) (2-51) 𝑥 = [𝑥 �̇� 𝑥(𝑛−1)] T (2-52) Ở đây b > 0, 𝑥 ∈ 𝐑𝑛, 𝑢 ∈ 𝐑, d(t) là nhiễu và các yếu tố không chắc chắn bên ngoài và được giả định |𝑑(𝑡)| ≤ 𝐷. Khi bỏ qua nhiễu và các yếu tố không chắc chắn bên ngoài, hệ được mô tả như sau: 𝑥(𝑛) = 𝑓(𝑥, 𝑡) + 𝑏𝑢(𝑡) (2-53) Vectơ sai số: 𝒆 = 𝒙d − 𝒙 = [𝑒 �̇� 𝑒 (𝑛−1)] T (2-54) Khi đó mặt trượt được xác định như sau: 𝑠(𝑥, 𝑡) = 𝑪𝒆 = 𝑐1 + 𝑐2�̇� + ⋯+ 𝑒 (𝑛−1) (2-55) Chương 2 46 Ở đây 𝑪 = [𝑐1 𝑐1 𝑐𝑛−1 1] là véc tơ 1𝑥𝑛. Chọn �̇� = 0, ta có: �̇�(𝑥, 𝑡) = 𝑐1�̇� + 𝑐2�̈� + ⋯+ 𝑒 𝑛 = 𝑐1�̇� + 𝑐2�̈� + ⋯+ 𝑐𝑛−1𝑒 𝑛−1 + 𝑥𝑑 (𝑛) − 𝑥(𝑛) = ∑ 𝑐𝑖𝑒 (𝑖) + 𝑥𝑑 (𝑛) − 𝑓(𝑥, 𝑡) − 𝑏𝑢(𝑡) = 0𝑛−1𝑖=1 (2-56) Luật điều khiển tương đương được thiết kế như sau: 𝑢𝑒𝑞 = 1 𝑏 (∑ 𝑐𝑖𝑒 (𝑖) + 𝑥d (𝑛)𝑛−1 𝑖=1 − 𝑓(𝑥, 𝑡)) (2-57) Để đáp ứng các điều kiện của điều khiển chế độ trượt 𝑠(𝑥, 𝑡). �̇�(𝑥, 𝑡) ≤ −𝜂|𝑠|, ≥ 0 thì ta chọn luật điều khiển chuyển đổi là: 𝑢sw = 1 𝑏 𝐾 sgn(𝑠) ( 2-58) Với K = D + Bộ điều khiển trượt bao gồm luật điều khiển tương đương và luật điều khiển chuyển đổi được biểu diễn như sau: 𝑢 = 𝑢𝑒𝑞 + 𝑢sw (2-59) Sự ổn của hệ thống: �̇�(𝑥, 𝑡) = ∑ 𝑐𝑖𝑒 (𝑖) + 𝑥d (𝑛)𝑛−1 𝑖=1 − 𝑓(𝑥, 𝑡) − 𝑏𝑢(𝑡) − 𝑑(𝑡) ( 2-60) Từ (2-59), (2-60) ta có: �̇�(𝑥, 𝑡) = ∑ 𝑐𝑖𝑒 (𝑖) + 𝑥d (𝑛) 𝑛−1 𝑖=1 − 𝑓(𝑥, 𝑡) − 𝑏 ( 1 𝑏 (∑ 𝑐𝑖𝑒 (𝑛) + 𝑥d (𝑛) − 𝑓(𝑥, 𝑡) 𝑛−1 𝑖=1 ) + 1 𝑏 𝐾 sgn(𝑠)) − 𝑑(𝑡) = −𝐾 sgn(𝑠) − 𝑑(𝑡) Do đó ta có: 𝑠�̇� = 𝑠(−𝐾 sgn(𝑠)) − 𝑠. 𝑑(𝑡) = −𝜂|𝑠| ≤ 0 (2-61) Hệ thống ổn định. 2.8.2.3 Bộ điều khiển SMC theo tham số cận trên. Xét một hệ phi tuyến bậc 2 như sau: �̈� = 𝑓(𝑥, �̇�) + ∆𝑓(, �̇�) + 𝑔(𝑥, �̇�)𝑢 + ∆𝑔(𝑥, �̇�)𝑢 + 𝑑0(𝑡) (2-62) Chương 2 47 Trong đó f và g là hàm phi tuyến đã biết, u và x là tín hiệu điều khiển đầu vào và sự đo lường đầu ra tương ứng (𝑢 ∈ 𝑅 và 𝑥 ∈ 𝑅), 𝑑0(𝑡) là nhiễu của hệ thống và với |𝑑(𝑥, 𝑥,̇ 𝑡)| ≤ 𝐷, D là hằng số dương. Giả sử: 𝑑(𝑥, �̇�, 𝑡) = ∆𝑓(𝑥, �̇�) + ∆𝑔(𝑥, �̇�)𝑢 + 𝑑0(𝑡), khi đó phương trình (2-62) được viết lại như sau: �̈� = 𝑓(𝑥, �̇�) + 𝑔(𝑥, �̇�)𝑢 + 𝑑(𝑥, �̇�, 𝑡) (2-63) Sai lệch tín hiệu mong muốn đầu vào và tín hiệu thực tế đầu ra được định nghĩa như sau: 𝑒 = 𝑥d − 𝑥. Mặt trượt được định nghĩa như sau: 𝑠 = �̇� + 𝑐𝑒 (2-64) Trong đó c thỏa điều kiện Hurwitz c > 0. Đạo hàm mặt trượt được xác định như sau: �̇� = �̈� + 𝑐�̇� = �̈�𝑑 − �̈� + 𝑐�̇� = �̈�𝑑 − 𝑓 − 𝑔𝑢 − 𝑑 + 𝑐�̇� Tín hiệu điều khiển được xác định như sau: 𝑢 = 1 𝑔 [−𝑓 + �̈�𝑑 + 𝑐�̇� + 𝜂sgn(𝑠)] (2-65) Sự ổn định của hệ thống được chứng minh như sau: Áp dụng hàm Lyapunov: 𝐿 = 1 2 𝑠2 Ta có: �̇� = 𝑠�̇� = 𝑠(�̈�𝑑 − 𝑓 − 𝑔𝑢 − 𝑑 + 𝑐�̇�) = 𝑠(�̈�𝑑 − 𝑓 − (−𝑓 + �̈�𝑑 + 𝑐�̇� + 𝜂sgn(𝑠)) − 𝑑 + 𝑐�̇�) = 𝑠(−𝑑 − 𝜂𝑠𝑔𝑛(𝑠)) = −𝑠𝑑 − 𝜂|𝑠| Nếu 𝜂 ≥ 𝐷 thì: �̇� = −𝑠𝑑 − 𝜂|𝑠| ≤ 0, hệ thống ổn định. Để hạn chế hiện tượng nhiễu (chattering), hàm bão hòa sat(s) được sử dụng thay vì sgn(s) trong phương trình (2-66) như sau: sat(𝑠) = { 1, 𝑠 > ∆ 𝑘𝑠, |𝑠| ≤ ∆, 𝑘 = 1/∆ −1, 𝑠 < −∆ (2-66) với là lớp biên (boundary layer) Chương 2 48 Ngoài việc sử dụng hàm bão hòa sat(s) thì hàm mũ và hàm lượng giác cũng được áp dụng như hàm sigmoid để giảm thiểu hiện tượng nhiễu của bộ điều khiển trượt Hình 2.12. Hình 2.12: Đồ thị hàm bão hòa. Chương 3 49 Chương 3 PHÁT TRIỂN CƠ CẤU HAI CHIỀU DÙNG MRF Các cơ cấu sử dụng MRF truyền thống đều bố trí cuộn dây phía trên mặt trụ của đĩa điều này sẽ hạn chế việc từ trường đi qua các vị trí cần thiết của phanh, đôi khi rơi vào hiện tượng “thắt nút chai” dẫn tới làm giảm hiệu suất của cơ cấu, kết cấu cồng kềnh làm tăng khối lượng của cơ cấu. Một vấn đề khác của hệ thống phản hồi lực là khi ở trạng ban đầu đều mong muốn lực bằng không. Nhược điểm của phanh MRF là khi không có dòng điện áp dụng thì khó kiểm soát được lực cũng như mô men đầu ra. Khi đó một lực phản hồi nhỏ lên hệ thống thì nó không thể phản ánh được điều này sẽ làm giảm tính năng của hệ thống phản hồi. Ngoài ra, đối với hệ thống phản hồi sử dụng phanh MRF, để cảm nhận được lực phản hồi thì người vận hành cần di chuyển hệ thống phản hồi. Do đó, lực phản hồi không được phản ánh cho người vận hành nếu hệ thống đứng yên. Để khắc phục nhược điểm này gần đây cơ cấu hai chiều dùng MRF (BMRA) đã được phát triển cho ứng dụng trong hệ thống phản hồi lực. 3.1 Cơ cấu hai chiều dùng MRF (BMRA). 3.1.1 Mô hình BMRA của Nguyen P. B [56]. Tác giả Nguyen P. B là người đầu tiên đề xuất cơ cấu hai chiều sử dụng MRF [56] (Hình 3.1). Do bố trí hai đĩa quay cùng tốc độ nhưng ngược chiều nên có thể khử được ma sát ban đầu của cơ cấu. Tuy nhiên BMRA của Nguyen P. B vẫn sử dụng kết cấu truyền thống đó là vị trí của cuộn dây vẫn bố trí phía trên mặt trụ của đĩa. Điều này sẽ hạn chế từ trường đi qua khe MRF, đôi khi rơi vào hiện tượng “thắt nút cổ chai”, dễ bão hoà từ dẫn tới hiệu suất của cơ cấu giảm. Hơn nữa việc tối ưu hoá hình học chưa được xem xét nên kết cấu BMRA còn khá lớn, mô men phản hồi không cao chỉ đạt 1.2 Nm. Chương 3 50 Hình 3.1: Cơ cấu hai chiều dùng BMRA_[56]. 3.1.2 Mô hình BMRA mới đề xuất. Để khắc phục một số tồn tại của mẫu BMRA_[56], và trên cơ sở của cơ cấu 2 chiều đã phát triển bởi [76], tác giả đã phát triển một cơ cấu BMRA mới với các cuộn dây được bố trí tại mỗi bên mặt đầu thân vỏ của BMRA. Điều này sẽ khắc phục được hiện tượng thắt nút chai cũng như bão hòa từ tại một số vị trí của BMRA, đồng thời tác giả có xét tới bài toán tối ưu hình học BMRA sao cho khối lượng của BMRA đề xuất nhỏ nhất và mô men đầu ra đạt theo yêu cầu cho trước. Tác giả đưa ra hai phương án cho BMRA của mình đó là: - Phương án 1: BMRA có một cuộn dây ở mỗi bên (BMRA1) (Hình 3.2) - Phương án 2: BMRA có hai cuộn dây ở mỗi bên (BMRA2) (Hình 3.3) Hình 3.2: Cấu hình BMRA1. Hình 3.3: Cấu hình BMRA2. Chương 3 51 3.1.2.1 Cấu tạo và nguyên lý hoạt động BMRA. Về cấu tạo của BMRA1, BMRA2 là giống nhau chỉ khác nhau về số lượng cuộn dây bố trí trên thân vỏ. Cụ thể là đối với BMRA1 chỉ bố trí 1 cuộn dây ở mỗi bên thân vỏ, còn BMRA2 thì được bố trí 2 cuộn dây mỗi bên. Vì vậy cấu tạo của chúng bao gồm: đĩa 1 và đĩa 2 lần lượt được lắp chặt trên trục vào 1 và trục vào 2, hai trục này được cố định bằng các ổ lăn và trên các trục có bố trí các phớt chặn không cho MRF rò rỉ ra ngoài. Đồng thời hai trục này được dẫn động bởi hệ bánh răng bên ngoài sao cho hai trục đầu vào quay cùng tốc độ và ngược chiều nhau. Khe hở giữa thân vỏ và các đĩa sẽ được điền đầy MRF. Các cuộn dây được bố trí mặt bên BMRA có một màng mỏng ngăn cho cuộn dây không tiếp xúc với MRF. Về nguyên lý hoạt động của BMRA: trục vào 1 và 2 sẽ được dẫn động bởi một động cơ AC servo thông qua một hệ thống truyền lực bên ngoài (hệ bánh răng côn) làm cả hai trục quay cùng tốc độ nhưng ngược chiều. Do hai đĩa được gắn cố định với hai trục tương ứng nên cũng được quay cùng tốc độ nhưng ngược chiều. Khi một dòng điện chỉ áp dụng vào cuộn dây 1 của BMRA1 thì một từ trường tương ứng được tạo ra xung quanh cuộn dây. Khi đó từ trường sẽ làm cho MRF trong khe MRF bên trái của đĩa 1 trở nên sệt lại ngay lập tức. Từ ma sát giữa đĩa 1 với MRF và MRF với thân vỏ BMRA sẽ tạo ra mô men ma sát đầu ra của BMRA (T1) thông qua trục đầu ra được gắng cố định trên thân vỏ BMRA quay cùng chiều với đĩa 1 (CW). Mô men đầu ra chủ yếu sinh ra đĩa 1, bên còn lại có mô men đi qua nhưng tương đối nhỏ. Độ lớn của mô men đầu ra của BMRA1 phụ thuộc vào dòng điện áp dụng cho cuộn dây 1. Tương tự cuộn dây của đĩa 2, khi dòng điện chỉ áp dụng vào cuộn dây 2 thì mô men ma sát đầu ra do đĩa 2 của BMRA1 (T2) được tạo ra thông qua trục ra của BMRA1 và trục ra quay cùng chiều quay với đĩa 2 (CCW). 3.1.2.2 Mô men ma sát đầu ra của các BMRA. Mô men ma sát BMRA1. Để tính mô men ma sát sinh ra trên hai đĩa của BMRA1, tác giả chia khe lưu chất thành 4 vùng để tính mô men đó là MRF1, MRF2, MRF3, MRF4 tương ứng với các bán kính Ri, Rci, Rco, Rd được thể hiện bởi Hình 3.4. Chương 3 52 Hình 3.4: Thông số hình học BMRA1. Mô men đầu ra của BMRA1 được tạo ra bởi ma sát của hai đĩa 1 và đĩa 2 và ma sát của các phớt với trục. Do hai đĩa quay ngược chiều, cùng tốc độ nên mô men đầu ra BMRA được tính như sau: 𝑻𝟎𝟏 = 𝑻𝟏 − 𝑻𝟐 + 𝑻𝒔𝟏 − 𝑻𝒔𝟐 (3-1) Trong đó: - 𝑻𝟎𝟏: mô men đầu ra của BMRA1. - 𝑻𝟏: mô men sinh ra giữa đĩa 1 (bên trái) và thân vỏ. - 𝑻𝟐: mô men sinh ra giữa đĩa 2 (bên phải) và thân vỏ. - 𝑻𝒔𝟏: mô men ma sát giữa các phớt và trục 1. - 𝑻𝒔𝟐: mô men ma sát giữa các phớt và trục 2. Mô men ma sát trên từng đĩa của BMRA1 được tính theo công thức (2-18), (2-19): 𝑻𝟏 = 𝜋𝜇𝑑11𝑅𝑐𝑖 4 2𝑡𝑔 [1 − ( 𝑅𝑖 𝑅𝑐𝑖 ) 4 ] |𝜔1| + 2𝜋𝜏𝑦𝑑11 3 (𝑅𝑐𝑖 3 − 𝑅𝑖 3) + 𝜋𝜇𝑑12𝑅𝑐𝑜 4 2𝑡𝑔 [1 − ( 𝑅𝑐𝑖 𝑅𝑐𝑜 ) 4 ] |𝜔1| + 2𝜋𝜏𝑦𝑑12 3 (𝑅𝑐𝑜 3 − 𝑅𝑐𝑖 3 ) + 𝜋𝜇𝑑13𝑅𝑑 4 2𝑡𝑔 [1 − ( 𝑅𝑐𝑜 𝑅𝑑 ) 4 ] |𝜔1| + 2𝜋𝜏𝑦𝑑13 3 (𝑅𝑑 3 − 𝑅𝑐𝑜 3 ) +2𝜋𝑅𝑑 2𝑡𝑑(𝜏𝑦𝑑14 + 𝜇𝑑14 |𝜔1|𝑅𝑑 𝑡𝑔 ) (3-2) Chương 3 53 𝑻𝟐 = 𝜋𝜇𝑑21𝑅𝑐𝑖 4 2𝑡𝑔 [1 − ( 𝑅𝑖 𝑅𝑐𝑖 ) 4 ] |𝜔2| + 2𝜋𝜏𝑦𝑑21 3 (𝑅𝑐𝑖 3 − 𝑅𝑖 3) + 𝜋𝜇𝑑22𝑅𝑐𝑜 4 2𝑡𝑔 [1 − ( 𝑅𝑐𝑖 𝑅𝑐𝑜 ) 4 ] |𝜔2| + 2𝜋𝜏𝑦𝑑22 3 (𝑅𝑐𝑜 3 − 𝑅𝑐𝑖 3 ) + 𝜋𝜇𝑑23𝑅𝑑 4 2𝑡𝑔 [1 − ( 𝑅𝑐𝑜 𝑅𝑑 ) 4 ] |𝜔2| + 2𝜋𝜏𝑦𝑑23 3 (𝑅𝑑 3 − 𝑅𝑐𝑜 3 ) +2𝜋𝑅𝑑 2𝑡𝑑(𝜏𝑦𝑑24 + 𝜇𝑑24 |𝜔2|𝑅𝑑 𝑡𝑔 ) (3-3) Với thông số lưu biến của MRF: - 𝜇𝑑11, 𝜇𝑑12, 𝜇𝑑13, 𝜇𝑑14: độ nhớt sau chảy dẻo của MRF tương ứng tại các vị trí MRF1, MRF2, MRF3, MRF4 của đĩa 1 - 𝜏𝑑11, 𝜏𝑑12, 𝜏𝑑13, 𝜏𝑑14: ứng suất chảy dẻo của MRF tương ứng tại các vị trí MRF1, MRF2, MRF3, MRF4 của đĩa 1 - 𝜇𝑑21, 𝜇𝑑22, 𝜇𝑑23, 𝜇𝑑24: độ nhớt sau chảy dẻo của MRF tương ứng tại các vị trí MRF1, MRF2, MRF3, MRF4 của đĩa 2 - 𝜏𝑑21, 𝜏𝑑22, 𝜏𝑑23, 𝜏𝑑24: ứng suất chảy dẻo của MRF tương ứng tại các vị trí MRF1, MRF2, MRF3, MRF4 của đĩa 2 Với thông số hình học của BMRA: - R là bán kính BMRA, Rd là bán kính đĩa, Rdi là bán kính mặt bích trục 1 - Rci là bán kính trong cuộn dây, Rco là bán kính ngoài cuộn dây - hc là chiều cao cuộn dây, t0 là bề dày mặt trụ, td bề dày đĩa - tg là bề dày khe MRF, th là bề dày thành đứng BMRA - tc1 là bề rộng cuộn dây BMRA1, tw là bề dày thành mỏng - Rs1 là bán kính trục 1, Rs2 là bán kính trục - Vận tốc góc của đĩa hai đĩa: 1, 1 Với 𝑇𝑠1 = 0,65(2𝑅𝑠1) 2𝜔1 1 3⁄ ; 𝑇𝑠2 = 0,65(2𝑅𝑠2) 2𝜔2 1 3⁄ theo công thức (2-24) Mô men ma sát của BMRA2. Trong thực tế với yêu cầu mô men lớn thì BMRA một cuộn dây khó đạt được. Vì vậy, tác giả khảo sát thêm trường hợp nhiều cuộn dây, cụ thể là 2 cuộn dây. Cấu hình đề xuất BMRA hai cuộn dây bên thân vỏ (BMRA2) thể hiện bởi Hình 3.5. Chương 3 54 Để tính mô men ma sát đầu ra của BMRA2, tác giả chia khe lưu chất thành 6 vùng lưu chất tính mô men đó là MRF1, MRF2, MRF3, MRF4, MRF5, MRF6 tương ứng với các bán kính Ri, Rci1, Rco1, Rci2, Rco2, Rd được thể hiện bởi Hình 3.5. Hình 3.5: Thông số hình học BMRA2. Mô men đầu ra của BMRA2 được tính như sau: 𝑻𝒐𝟐 = 𝑻𝐝𝟏 − 𝑻𝐝𝟐 + 𝑻𝒔𝟏 − 𝑻𝒔𝟐 (3-4) Trong đó: - 𝑻𝟎𝟐: mô men đầu ra của BMRA2 - 𝑻𝐝𝟏: mô men sinh ra giữa đĩa 1 (bên trái) và thân vỏ - 𝑻𝐝𝟐: mô men sinh ra giữa đĩa 2 (bên phải) và thân vỏ - 𝑻𝒔𝟏, 𝑻𝒔𝟐: được tính tương tự như BMRA1 Mô men sinh ra trên hai đĩa của BMRA2 được tính theo công thức (2-18), (2-19): 𝑻𝒅𝟏 = 𝜋𝜇11𝑅𝑐𝑖1 4 2𝑡𝑔 [1 − ( 𝑅𝑖 𝑅𝑐𝑖1 ) 4 ] |𝜔1| + 2𝜋𝜏𝑦11 3 (𝑅𝑐𝑖1 3 − 𝑅𝑖 3) + 𝜋𝜇12𝑅𝑐o1 4 2𝑡𝑔 [1 − ( 𝑅𝑐𝑖1 𝑅𝑐𝑜1 ) 4 ]|𝜔1| + 2𝜋𝜏𝑦12 3 (𝑅𝑐𝑜1 3 − 𝑅𝑐𝑖1 3 ) + 𝜋𝜇13𝑅𝑐𝑖2 4 2𝑡𝑔 [1 − ( 𝑅𝑐𝑜1 𝑅𝑐𝑖2 ) 4 ] |𝜔1| + 2𝜋𝜏𝑦13 3 (𝑅𝑐𝑖2 3 − 𝑅𝑐𝑜1 3 ) Chương 3 55 + 𝜋𝜇14𝑅𝑐o2 4 2𝑡𝑔 [1 − ( 𝑅𝑐𝑖2 𝑅𝑐𝑜2 ) 4 ]|𝜔1| + 2𝜋𝜏𝑦14 3 (𝑅𝑐𝑜2 3 − 𝑅𝑐𝑜1 3 ) + 𝜋𝜇15𝑅𝑑 4 2𝑡𝑔 [1 − ( 𝑅𝑐𝑜2 𝑅𝑑 ) 4 ] |𝜔1| + 2𝜋𝜏𝑦15 3 (𝑅𝑑 3 − 𝑅𝑐𝑜2 3 ) +2𝜋𝑅𝑑 2𝑡𝑑(𝜏𝑑16 + 𝜇16 |𝜔1|𝑅𝑑 𝑡𝑔 ) (3-5) 𝑻𝒅𝟐 = 𝜋𝜇21𝑅𝑐𝑖1 4 2𝑡𝑔 [1 − ( 𝑅𝑖 𝑅𝑐𝑖1 ) 4 ] |𝜔2| + 2𝜋𝜏𝑦21 3 (𝑅𝑐𝑖1 3 − 𝑅𝑖 3) + 𝜋𝜇22𝑅𝑐o1 4 2𝑡𝑔 [1 − ( 𝑅𝑐𝑖1 𝑅𝑐𝑜1 ) 4 ]|𝜔2| + 2𝜋𝜏𝑦22 3 (𝑅𝑐𝑜1 3 − 𝑅𝑐𝑖1 3 ) + 𝜋𝜇23𝑅𝑐𝑖2 4 2𝑡𝑔 [1 − ( 𝑅𝑐𝑜1 𝑅𝑐𝑖2 ) 4 ] |𝜔2| + 2𝜋𝜏𝑦23 3 (𝑅𝑐𝑖2 3 − 𝑅𝑐𝑜1 3 ) + 𝜋𝜇24𝑅𝑐o2 4 2𝑡𝑔 [1 − ( 𝑅𝑐𝑖2 𝑅𝑐𝑜2 ) 4 ]|𝜔2| + 2𝜋𝜏𝑦24 3 (𝑅𝑐𝑜2 3 − 𝑅𝑐𝑜1 3 ) + 𝜋𝜇25𝑅𝑑 4 2𝑡𝑔 [1 − ( 𝑅𝑐𝑜2 𝑅𝑑 ) 4 ] |𝜔2| + 2𝜋𝜏𝑦25 3 (𝑅𝑑 3 − 𝑅𝑐𝑜2 3 ) +2𝜋𝑅𝑑 2𝑡𝑑(𝜏𝑑26 + 𝜇26 |𝜔2|𝑅𝑑 𝑡𝑔 ) (3-6) 3.2 Thiết kế tối ưu cho các BMRA. Thiết kế tối ưu cho các BMRA là chúng ta đi tìm giá trị các kích thước hình học của BMRA sao cho khối lượng của các BMRA (mb) là nhỏ nhất với mô men đầu ra của các BMRA (Tb) được ràng buộc bằng hoặc lớn hơn giá trị yêu cầu (giá trị yêu cầu được đưa ra tùy thuộc vào từng ứng dụng cụ thể). Từ đó ta có các yếu tố ban đầu cho bài toán tối ưu hóa bao gồm: Hàm mục tiêu: khối lượng của BMRA (mb) là nhỏ nhất. 𝑚𝑏 = 𝑉𝑑1𝜌𝑑1 + 𝑉𝑑2𝜌𝑑2 + 𝑉ℎ𝜌ℎ + 𝑉𝑠1𝜌𝑠1 + 𝑉𝑠2𝜌𝑠2 + 𝑉𝑀𝑅𝐹𝜌𝑀𝑅𝐹 + 𝑉𝑐𝜌𝑐 (3-7) Trong đó: - Vd1, Vd2, Vh, Vs1, Vs2, VMRF, Vc là thể tích của các bộ phận cấu tạo nên BMRA tương ứng đó là thể tích của đĩa 1, đĩa 2, vỏ, trục 1, trục 2, MRF và cuộn đây. - Khối lượng riêng tương ứng đó là d1, d2, h, s1, s2, MRF, c Biến thiết kế: tất các thông số hình học chủ yếu của BMRA. Chương 3 56 Điều kiện ràng buộc: mô men đầu ra của BMRA Tb 5 Nm. Vật liệu áp dụng phải là vật liệu từ tính nên tác giả sử dụng thép hợp kim C45, áp dụng cho thân vỏ, đĩa của BMRA. Hơn nữa, vật liệu C45 thông dụng trên thị trường, chi phí phù hợp. Vật liệu Inox 304 áp dụng cho các trục đầu vào và ra của BMRA để lưu chất xung quanh phớt không bị cứng lại khi kích hoạt từ trường ở BMRA. MRF sử dụng là MRF-132DG. Đây là lưu chất có từ tính trung bình, tính đáp ứng tốt. Bảng 3.1: Vật liệu và khối lượng riêng các chi tiết của BMRA. Trong quá trình tính toán tối ưu thì các kích thước hình học quan trọng của BMRA1 và BMRA2 như chiều cao của cuộn dây (hc của BMRA1 và hc1, hc2 của BMRA2), chiều rộng của cuộn dây (wc), bán kính ngoài đĩa (Rd), bán kính trong của đĩa (Rdi), vị trí của các cuộn dây trên vỏ (Rci đối với BMRA1 và Rci1, Rci2 đối với BMRA2), độ dày của đĩa (td), bề dày của vỏ hình trụ (t0), bề dày bên ngoài của vỏ (th) được chọn làm biến thiết kế. Tuy nhiên, kích thước khe hở nhỏ làm tăng mô men BMRA ở trạng thái dòng điện không áp dụng, sẽ làm giảm hiệu suất của cơ cấu, năng lượng tiêu tán cao, sinh nhiệt cao và nhanh mòn, ngoài ra kích thước khe hở nhỏ sẽ gây khó khăn trong chế tạo. Vì vậy, kích thước khe MRF không được chọn làm biến thiết kế trong tối ưu hóa mà được xác định theo kinh nghiệm và được chọn tg = 0,8 mm. Đối với độ dày thành mỏng của vỏ ở vị trí cuộn dây (tw) nên càng nhỏ càng tốt để hạn chế từ thông đi qua nhưng buộc từ thông đi qua các ống MRF, tw cũng không nên chọn quá nhỏ vì dẫn tới khó khăn trong chế tạo và độ cứng của kết cấu không đảm bảo. Vì vậy, độ dày của Bộ phận Vật liệu Khối lượng riêng (Kg.m-3) Trục Inox 304 7900 Đĩa và vỏ Thép C45 7850 Cuộn dây Đồng (24 gage) 8900 MRF MRF-132DG 2400 Chương 3 57 thành mỏng cũng không được coi là biến thiết kế mà được xác định theo kinh nghiệm và chọn tw = 0,6 mm. 3.2.1 Tối ưu hoá một mục tiêu cho BMRA. Trong các phương pháp tối ưu cục bộ thì phương pháp First Orders hội tụ nhanh. Hơn nữa, phương pháp này được tích hợp trong công cụ tối ưu của phần mềm thương mại ANSYS, nên có thể sử dụng dễ dàng và tính toán nhanh hơn và không cần tương tác giữa các phần mềm. Tuy nhiên, các giá trị ban đầu của biến thiết kế phải chọn tương đối chính xác (phụ thuộc vào kinh nghiệm). Một số thuật toán tối ưu hóa đạo hàm bậc nhất điển hình là phương pháp độ dốc, độ dốc liên hợp được áp dụng trong nghiên cứu này thể hiện bởi Hình 3.6. Trong phần mềm ANSYS có hỗ trợ về vấn đề thiết kế tối ưu bằng công cụ tối ưu tích hợp. Vì thế, trong hầu hết các trường hợp, bài toán tối ưu của các cơ cấu dùng MRF có thể được giải quyết trực tiếp bằng phần mềm ANSYS mà không cần phải thông qua bất kỳ phần mềm lập trình nào khác. Trước hết giá trị ban đầu của các biến thiết kế (Design Variable - DV) được chọn từ ban đầu. Thời gian tính toán tối ưu phụ thuộc đáng kể vào giá trị được chọn ban đầu. Do đó, giá trị ban đầu của các biến thiết kế nên được tính toán dựa trên tính toán sơ bộ hoặc dựa trên kinh nghiệm thực tế. Sau đó, một tập phân tích để giải quyết mạch từ và tính toán đặc tính hiệu suất của các thiết bị như năng lượng điều khiển, hằng số thời gian cảm ứng, giảm áp suất, lực, mô men phanh. Trong ANSYS, tập tin phân tích được xây dựng bằng ngôn ngữ thiết kế tham số (APDL). Cần lưu ý rằng tập tin phân tích này được tạo từ mô hình giao diện người dùng đồ họa (GUI) của ANSYS. Trong tập tin phân tích, các biến thiết kế phải được sử dụng làm biến tượng trưng và giá trị ban đầu được gán cho chúng. Để tính toán các đặc tính hiệu suất của cơ cấu thì cần tính toán mật độ từ thông trên toàn bộ thể tích hoạt động của MRF. Mật độ từ thông (B) và cường độ từ trường (H) không phải là hằng số dọc theo ống MRF. Mật độ từ thông và cường độ từ trường trung bình trên ống MRF được tính bằng cách tích phân mật độ từ thông dọc theo đường dẫn được xác định trước, sau đó chia cho chiều dài đường dẫn. Chương 3 58 Hình 3.6: Lưu đồ tối ưu hóa bằng phương pháp First Order. Để tính hằng số thời gian quy nạp trước tiên từ thông được xác định như sau: Φ = 2𝜋. 𝑅𝑑 ∫ 𝐵(𝑠). 𝑑𝑠𝐿𝑝 (3-8) Trong đó B(s) là mật độ từ thông tại mỗi điểm nút trên đường dẫn, s là một biến giả của tích phân. Việc tích phân được thực hiện dọc theo chiều dài đường dẫn Lp. Đáng chú ý là kích thước hình học của các cơ cấu MRF thay đổi trong quá trình tối ưu hóa, do đó kích thước chia lưới của mô hình phần tử hữu hạn phải được chỉ định bởi số lượng phần tử trên mỗi dòng thay vì kích thước phần tử. Chương 3 59 Công cụ tối ưu hóa ANSYS sẽ chuyển đổi vấn đề tối ưu hóa bị ràng buộc thành vấn đề không bị ràng buộc thông qua hàm Penalty (hàm phạt), đó là hàm mục tiêu không thứ nguyên, không ràng buộc. Hàm Penalty được xây dựng từ các giá trị khởi tạo ban đầu của các biến thiết kế, sau đó chạy tập tin phân tích ta có được giá trị khởi tạo của các đặc tính hoạt động của cơ cấu như năng lượng điều khiển, hằng số thời gian điện cảm, lực/mô men của BMRA. Với công cụ tối ưu của ANSYS, sau đó sẽ chuyển đổi các bài toán tối ưu bị ràng buộc thành không ràng buộc thông qua hàm Penalty. Hàm mục tiêu tương đương không ràng buộc có phương trình: 𝑄(𝑥, 𝑞) = 𝑂𝐵𝐽 𝑂𝐵𝐽0 + ∑ 𝑃𝑥 𝑛 𝑖=1 (𝑥𝑖) + 𝑞 ∑ 𝑃𝑔 𝑚 𝑖=1 (𝑔𝑖) (3-9) Trong đó: - OBJ0 là giá trị hàm mục tiêu tham chiếu được xác định từ giá trị của các biến thiết kế ban đầu, q là tham số bề mặt kiểm soát thỏa mãn ràng buộc; - Px là hàm phạt Penalty bên ngoài áp dụng cho biến thiết kế x; - Pg là hàm phạt Penalty nội bộ áp dụng cho biến trạng thái g. Đối với vòng lặp ban đầu (j=0), hướng tìm kiếm của biến thiết kế là độ dốc âm của hàm mục tiêu không ràng buộc. Khi đó vectơ chỉ phương được tính như sau: 𝑑(0) = −∇𝑄(𝑥(0), 1) (3-10) Các giá trị của DV trong lần lặp tiếp theo (j+1) được lấy từ phương trình sau: 𝑥(𝑗+1) = 𝑥(𝑗) + 𝑠𝑗𝑑 (𝑗) (3-11) Trong đó tham số tìm kiếm 𝑠𝑗 được tính bằng cách sử dụng kết hợp giải thuật Golden-Section với kỹ thuật
File đính kèm:
luan_an_phat_trien_he_thong_phan_hoi_luc_dung_luu_chat_tu_bi.pdf
Trang thong tin LA tieng Viet Diep Bao Tri.docx
Trang thong tin LA tieng Anh Diep Bao Tri.docx
Tom tat luan an tieng Viet Diep Bao tri.pdf
Tom tat luan an tieng Anh Diep Bao tri.pdf